Коленчатый вал фиксируется от осевого смещения: Осевая фиксация коленчатого вала — Энциклопедия по машиностроению XXL
Осевая фиксация коленчатого вала — Энциклопедия по машиностроению XXL
Противовесы служат для разгрузки коренных подшипников от вредного действия центробежных сил. Для подвода смазки от коренных шеек к шатунным просверлены каналы. Коренными шейками коленчатый вал устанавливается в постели картера и крепится крышками. Осевая фиксация коленчатых валов обеспечивается упорными подшипниками. [c.15]Осевая фиксация коленчатого вала производится упорными полукольцами 21 (рис. 2.7), установленными в торцах гнезда подшипника 3-й коренной шейки в блоке. Осевой зазор в этом соединении равен 0,054,..0,306 мм. [c.38]
Вкладыши коренных и шатунных подшипников — стальные с тонкослойной заливкой из свинцовистой бронзы. Упорный подшипник имеет четыре бронзовых полукольца для фиксации коленчатого вала от перемещений в осевом направлении.

Рис. 4.12. Способы фиксации осевого перемещения коленчатого вала |
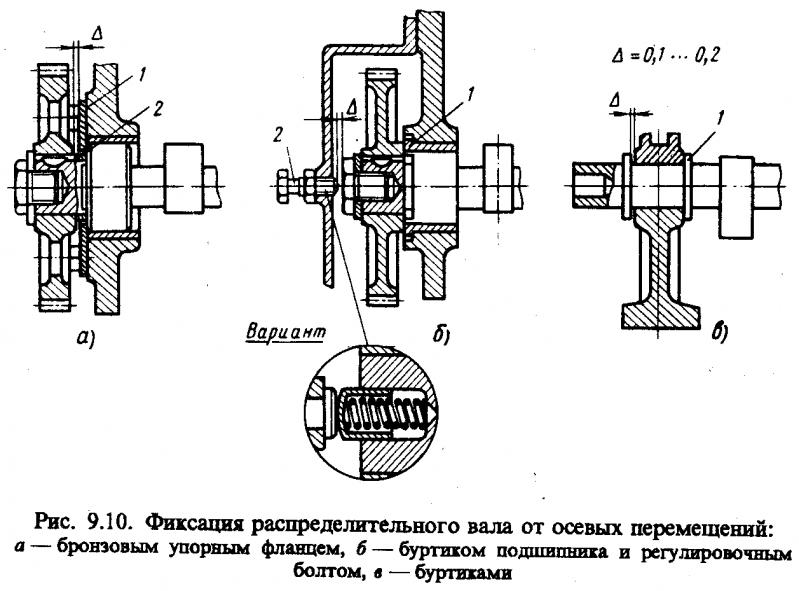
По конструкции валы можно разделить на прямолинейные, коленчатые и гибкие (рис. 10.1). Широко применяют прямолинейные валы ступенчатой конструкции. Такая форма вала удобна при монтаже, так как позволяет установить деталь с натягом без повреждения соседних участков и обеспечить ее осевую фиксацию. Уступы валов могут воспринимать значительные осевые нагрузки. Однако в местах сопряжения участков разного диаметра возникает концентрация напряжений, что снижает прочность вала. [c.147]
Распределительные валы. Распределительный вал (рис. 157) предназначен для передачи движения клапанам от коленчатого вала. Он выполняется обычно за одно целое с кулачками и элементами привода некоторых агрегатов двигателя (бензонасосов, топливных и масляных насосов, прерывателей-распределителей и т. д.). Распределительный вал устанавливается, как правило, в стале-баббитовых или алюминиевых подшипниках, число которых большей частью равно числу коренных подшипников коленчатого вала.
Для фиксации вала от осевого смещения в выточках заднего коренного подшипника установлены четыре бронзовых полукольца 15. В заднем торце коленчатого вала выточено гнездо для шарикового подшипника первичного вала коробки передач. Коленчатый вал в сборе с маховиком подвергается динамической балансировке. [c.23]
Задний конец коленчатого вала в торцевой части имеет два отверстия для запрессовки штифтов фиксации маховика, одно осевое отверстие для опорного подшипника первичного вала коробки передач, а также резьбовые отверстия для болтов крепления маховика.
[c.41]
Распределительный вал сделан полым внутри него проходит уравновешивающий вал 18, установленный в распределительном валу на двух опорах и приводимый во вращение от шестерни 9 коленчатого вала.На концах уравновешивающего вала закреплены противовесы 19 и 29. Для фиксации распределительного и уравновешивающего валов в осевом направлении служит упорный штифт 17 с пружиной.
Основным вопросом конструкции ведущей шестерни, соединенной с коленчатым валом, является система ее осевой фиксации. [c.327]
В другом варианте ведущая шестерня связана с коленчатым валом посредством осевых или торцевых шлиц и имеет возможность перемещаться по валу в осевом направлении, сохраняя постоянство зазора в зацеплении. Центрируется она или на хвостовике вала или в задней части картера. Осевая фиксация и передача осевого усилия ведущей шестерни осуществляются шариковыми подшипниками или подпятниками, расположенными в задней крышке картера.
[c.327]
Классификация. По геометрической форме валы делятся на прямые, коленчатые и гибкие . По конструк-пин прямые валы и оси делятся на гладкие и ступенчатые (рис. 3.136). Гладкие, т. е. валы одного номинального диаметра, по всей длине обеспечивают хорошее центрование насаживаемых деталей и имеют повышенные прочность и жесткость из-за отсутствия проточек, являющихся концентраторами напряжений для получения требуемых посадок участки вала отличаются допусками на диаметр и шероховатостью поверхности. Для сборки насаживаемых на валы деталей необходимы специальные приспособления. Ступенчатые валы и оси имеют более широкое распространение. Они обеспечивают удобную сборку (разборку) и фиксацию насаживаемых деталей от осевого смещения. Кроме того, уступы на валах воспринимают осевую нагрузку. [c.400]
Осевая фиксация коленчатого вала осуществляется средним коренным подшипником,, вследствие чего вал может свободно удлиняться в обе стороны. Двигатель не имеет вставных, цилиндровых гильз. Если износ цилиндров достигает максимально допустимого предела, необходимо подвергнуть блок расшлифовкг и установить поршни соответственно увеличенного диаметра. Поршни имеют лишь по одному маслосъемному кольцу, расположенному выше поршневого пальца. Система смазки обычная, циркуляционная, под давлением. Масляный насос шестеренного типа, горизонтальный, с приводом от шестерни на распределительном валу. Впускные и выпускные клапаны, как у всех дизелей, верхние, подвесные. Привод клапанов нормальный, при помощи толкателей, штанг толкателей и коромысла. Головка цилиндра общая на все четыре цилиндра. Для регулирования топливоподачи применяется описанный выше пневматический регулятор. 3
Каждый ряд цилиндров закрыт общей головкой 7, также отлитой из алюминиевого силава. В камере, расноложенной между обеими секциями блока, проходят штанги толкателей. Камера закрыта сверху крышкой, в которой отлиты впускные трубопроводы. Конструкции поршней 6 с кольцами, поршневых пальцев и шатунов 10 в основном аналогичны конструкции одноименных деталей двигателя автомобиля М-21 Волга . В картере двигателя на пяти подшипршках установлен отлитый из специального чугуна коленчатый вал 2 с полыми шейками, имеющий четыре кривошипа с противовесами. В шатунных шейках вала имеются грязеуловители. Нижние головки шатунов, цилиндров, расположенных в общей поперечной плоскости, посажены на одну общую шатунную шейку коленчатого вала. Вкладыши коренных и шатунных нодшипников тонкостенные, сталебаббитовые, трехслойные, с металлокерамическим подслоем (60% меди и 40% никеля), что значительно повышает срок службы вкладышей. Осевая фиксация коленчатого вала осуществляется упорными кольцами в переднем коренном подшипнике. Снизу к блок-картеру присоединен стальной штампованный поддон 1.
[c.87]
В некоторых рядных двигателях со скользящими коренными опорами, как, например, Испано 12-№г, осевая фиксация коленчатого вала осуществляется торцовыми поверхностями вкладыша переднего коренного подшипника.

В случае выполнения шестерен редуктора с шевронным зубом, как, например, в двигателях Кертис-Конкверор, АМ-34, осевая фиксация коленчатого вала обеспечивается упорным подшипником вала редуктора. [c.174]
Осевой зазор коленчатого вала замеряют после установки распределительной шестерни. В двигателях ГАЗ-51, М-20 и ЗИЛ-120 шестерни напрессовывают ijp упора в стальную упорную шайбу коленчатого вала, а у двигателя Москвич -400 и Москвич -402 до упора в торец передней шейки с меткой для установки газораспределения наружу. Замеренный осевой зазор между торцом передней шайбы упорного подшипника и торцом сопряженной с ней детали (стальной упорной шайбы у двигателя ГАЗ и шестерни у двигателя ЗИЛ-120) допускается в пределах 0,075—0,175 мм у двигателей ГАЗ и 0,05—0,23 мм у двигателей ЗИЛ-120.
Ввиду возможных деформаций картера все похшинники коленчатого валз1 должны иметь специальные зазоры, величина которых устанавливается с уче-том длины и температуры картера. Заедание коленчатого вала в подшипниках приводит к их выплавлению. Один из крайних коренных подшипников-должен обеспечивать фиксацию коленчатого вала от осевых перемещений с этой целью в направлении действия усилия при выключении сцепления иногда устанавливается упорный шарикоподшипник.
Стальной распределительный вал 9 установлен на пяти опорах в картере в середине блока у основания цилиндров. Подшипники вала выполнены в виде тонкостенных сталебаббитовых втулок. Осевая фиксация распределительного вала осуществляется упорным фланцем. Распределительный вал приводится от коленчатого вала шестеренчатой передачей. Шестерни закрыты литой алюминиевой крышкой. Впускные каналы у каждой головки расположены с внутренней стороны, и к ним присоединяется общий трубопровод.
[c.87]
Снизу к блоку болтами крепятся подвески коренных подшипников коленчатого вала. На торцах выносного и смежного с ним подшипников имеются упорные кольца для фиксации вала в осевом направлетти. [c.136]
Коленчатый вал нуждается в фиксации от осевых перемещений, возникающих вследствие его температурных расширений и возможных осевых усилий от косозубых шестерен. Осевая фиксация осуществляется специальным устройством — одного из коренных подшипников (чаще всего передним) через упорную стальную шайбу установленную впереди подшипника, и два сталебаббитовых кольца 9 и IO, установленных по обеим сторонам подшипника (стальной стороной к подшипнику). Известны конструкции валов, в которых фиксирующей является средняя или крайняя задняя шейка вала. Величина осевого зазора составляет 0,075—0,2 мм.
[c.44]
Остов дизеля — это стальной сварной У-образпый блок цилиндров, развал меледу которыми равен 45°. Снизу к блоку крепятся подвески для крепления подшипников коленчатого вала. Вкладыши подшипников тонкостенные из свинцовистой бронзы фиксируются от проворота усиками и штифтами. Для фиксации вала в осевом направлении на торцах девятой подвески установлены на винтах упорные кольца из бронзы, залитой баббитом. [c.24]
Предварительная обработка отверстий под втулки противовесов в задней части коленчатого вала заключается в сверлении, раззенковывании и развертывании. Эти операции выполняются на радиально-сверлильных или на вертикально-сверлильных станках (фиг. 130). Деталь устанавливается по внутренней плоскости, по осевому отверстию в коренной шейке и по установочному отверстию в шеке. Для фиксации служат пальцы 2 и 3. При обработке отверстий [c.163]
Цилиндрические полые толкатели 11 изготовлены из стали с торцовой рабочей поверхностью, наплавленной отбеленным чугуном. Толкатели установлены в каналах прилива блока и выходят в камеру, закрытую снаружи двумя крышками 10. Стальной расиределительный вал 12 установлен в перегородках блок-картера на пяти опорах со сталебаббитовыми тонкостенными втулками. На валу, кроме кулачков, имеются шестерня привода масляного насоса и распределителя и эксцентрик привода бензонасоса. Кулачки имеют конусную поверхность. Рабочие поверхности распределительного вала закалены. Осевая фиксация вала осуш ествляется упорным фланцем. На переднем конце вала закреплена на чугунной ступице текстолитовая шестерня 19, зацепляющаяся с шестерней 16 коленчатого вала.
[c.87]
Па переднем конце вала на шпонке гайкой закреплена чугунная шестерня 21, зацепляющаяся с шестерней коленчатого вала. Осевая фиксация вала осуя1,ествляется упорным фланцем 22. [c.98]
Каналы впускных клапанов 3 (фиг. 69) выведены к внутретшей стороне головок и соединяются с впускным трубопроводом 1, а каналы выпускных клапанов 15 выведены к наружной стороне головок, где к ним крепятся выпускные трубопроводы. Правый трубопровод имеет клапан-термостат 12 подогрева горючей смеси. Распределительный вал 13 изготовлон из чугуна и установлен посередине блок-картера у основания цилиндров на пяти опорах, снабженных тонкостенными сталебаббитовылш втулками. На переднем конце вала закреплена звездочка 29, соединяемая бесшумной цепью со звездочкой 24 коленчатого вала. Осевая фиксация вала осуществляется упорным фланцем. Цепная передача закрыта крышкой 26.
[c.106]
В редукторном двигателе коленчатый вал разгружен от силы тяги, однако осевая фиксация его необходима в этом случае от случайных сил, хотя бы непостоянных по времени и незначительных по величине. В двигателе Нэпир Х1-А эта фиксация выполнена задним опорным роликовым подшипником (фиг. 64). [c.173]
Длина коренных подшипников обычно меньше длины шейки вала, чем обеспечивается торцовый зазор для расширения коленчатого вала. Упорный коренной подшипник устанавливается с минимальным зазором для предупреждения осевого перемещения вала. Его лучше размещать на крайней коренной шейке с той стороны, на которой отбирается от двигателя мощность. Вкладыши упорного подшипника имеют торцовые упорные поверхности. Стопорный штифт для фиксации вкладышей установлен в крышке, а не в опоре подшипника, с тем чтобы был возможен демонтаж обоих вкладышей. При тонком слое заливки вкладышей пригонка шабровкой их недопустима. Внутреннюю поверхность вкладышей (баббитовый слой) обрабатывают алмазной расточкой. Толщина вкладыша после расточки в середине должна быть на 0,1—0,13 мм больше, чем у торцов. Изготовленные таким образом вкладыши имеют квазиэллипти-ческий вид.
[c.191]
Фиксация распределительного вала от осевых перемещений
В процессе вращения распределительного вала возникают осевые усилия, которые передаются на упорные фланцы либо винты. Распределительный вал двигателя (ЗМЗ-53, ЯМЗ, ЗИЛ-130, А-01, Д-240, СМД-60) фиксируется от осевых перемещений посредством упорных фланцев. В дизельном двигателе Д-240 [рис. 1, а)] упорная шайба (1) зажата между опорной шейкой вала и ступицей приводной шестерни (11). Осевое перемещение шайбы (4), а следовательно, и распределительного вала, ограничивается торцом втулки (10) с одной стороны, и упорным фланцем (6), который прикреплён к стенке блок-картера (посредством винтов (5)), с другой стороны.
Рис. 1. Способы фиксации осевого перемещения распределительного вала.
а) – Фиксация распределительного вала дизельного двигателя Д-240 посредством упорного фланца;
б) – Фиксация распределительного вала дизельного двигателя СМД-14 посредством упорного винта;
1) – Упорная шайба;
2) – Болт;
3) – Замковая шайба;
4) – Шайба;
5) – Винт;
6) – Упорный фланец;
7) – Шпонка;
8) – Распределительный вал;
9) – Блок-картер;
10) – Втулка;
11) – Шестерня распределительного вала;
12) – Крышка;
13) – Подпятник;
14) – Контргайка;
15) – Регулировочный винт.
В дизельном двигателе СМД-14 осевое перемещение распределительного вала ограничивается упорным винтом (15) [рис. 1, б)], который завёрнут в резьбовое отверстие передней крышки (12) распределительных шестерён. Вал при этом упирается фланцем в бурт втулки (10) с одной стороны, тогда как с другой стороны его перемещение ограничивает винт (15), который упирается в подпятник (13).
Осевые усилия в разъёмных подшипниках могут восприниматься специальными буртиками, которые выполнены на распределительном валу и упираются в торцы упорного подшипника (М-2140, ВАЗ).
17*
Похожие материалы:
Тест по дисциплине «Устройство, ТО и ремонт АТ»
Вариант 1
Тема: «Классификация и общее устройство автомобилей»
1. Какое понятие отсутствует в общей классификации автомобилей:
а) транспортные;
б) специальные;
в) рыночные;
г) специализированные.
2. Какая группа механизмов входит в устройство автомобиля:
а) ремиссия;
б) абсмиссия;
в) трансмиссия;
г) форсмиссия.
3. Что на автомобиле является источником механической энергии:
а) кузов;
б) двигатель;
в) шасси;
г) аккумуляторная батарея;
4. Расшифруйте и опишите модель автомобиля КамАЗ-53201:
___________________________________________________________
___________________________________________________________
___________________________________________________________
___________________________________________________________
___________________________________________________________
5. Расшифруйте и опишите колёсную формулу 8х6:
___________________________________________________________
___________________________________________________________
___________________________________________________________
Тема: «Классификация двигателей. Механизмы и системы двигателя внутреннего сгорания. Основные понятия»
1. В каких двигателях внутреннего сгорания происходит образование рабочей смеси внутри его цилиндров:
а) карбюраторных;
б) инжекторных;
в) дизельных;
г) газовых.
2. Какой механизм преобразует возвратно-поступательное движение поршня во вращательное движение коленчатого вала:
а) кривошипно-шатунный;
б) карбюраторный;
в) инжекторный;
г) газораспределительный;
3. Какой такт в работе четырёхтактного двигателя внутреннего сгорания изображён на (рис.1):
а) Рабочий ход
б) Впуск
в) Выпуск
г) Сжатие
Рисунок 1
4. Перечислите по порядку название тактов в работе четырёхтактного двигателя:
а) Нет правильного ответа.
б) Выпуск, сжатие, впуск, рабочий ход.
в) Рабочий ход, впуск, сжатие, выпуск.
г) Впуск, сжатие, рабочий ход, выпуск.
5. Что такое ВМТ:
а) комплекс последовательных периодически повторяющихся процессов (впуск, сжатие, сгорание, расширение и выпуск), в результате которых энергия топлива преобразуется в механическую работу.
б) положение поршня в цилиндре, при котором расстояние от него до оси коленчатого вала двигателя наименьшее.
в) положение поршня в цилиндре, при котором расстояние от него до оси коленчатого вала двигателя наибольшее.
г) это сумма рабочих объемов всех его цилиндров, выраженная в литрах.
6. Что такое литраж двигателя:
а) часть рабочего цикла, происходящая за время движения поршня от одной мертвой точки до другой
б) положение поршня в цилиндре, при котором расстояние от него до оси коленчатого вала двигателя наименьшее.
в) положение поршня в цилиндре, при котором расстояние от него до оси коленчатого вала двигателя наибольшее.
г) это сумма рабочих объемов всех его цилиндров, выраженная в литрах.
Тема: «Кривошипно-шатунный механизм»
Как называется деталь соединяющая поршень с шатуном?
Стопорное кольцо
Вкладыш
Поршневой палец
Коленчатый вал
Как называется деталь к которой крепятся шатуны?
Стопорное кольцо
Вкладыш
Поршневой палец
Коленчатый вал
Как называется верхняя часть поршня?
Юбка
Бобышка
Днище
Крышка
Какая часть шатуна разъемная?
Нижняя головка шатуна
Верхняя головка шатуна
Шейка
Никакая
Какая деталь КШМ совершает возвратно-поступательное движение?
Поршень
Шатун
Коленчатый вал
Маховик
Какая деталь КШМ совершает вращательное движение?
Поршень
Шатун
Поршневой палец
Коленчатый вал
Какая деталь не относится к КШМ?
Коленчатый вал
Поршневой палец
Клапан
Шатун
Какая деталь КШМ сделана из алюминиевого сплава?
Стопорное кольцо
Коленчатый вал
Поршневой палец
Поршень
Какая деталь отсутствует в поршне?
Юбка
Днище
Грязевая камера
Бабышка
Какой из поршней, одной марки двигателя, имеет наибольший диаметр?
Номинальный
Первого ремонта
Второго ремонта
Третьего ремонта
Тема: «Газораспределительный механизм»
Для чего предназначен газораспределительный механизм дизельного двигателя?
Для подачи топлива
Для подачи воздуха
Для впуска воздуха и выпуска отработанных газов
Для распределения газов по цилиндрам двигателя
Какая из деталей больше всего нагревается при работе двигателя?
Штанга
Выпускной клапан
Впускной клапан
Распределительный вал
Какая деталь закрывает клапана?
Штанга
Коромысло
Распределительный вал
Пружины
Какая деталь отсутствует в газораспределительном механизме?
Шатун
Штанга
Распределительный вал
Толкатель
Какая деталь поднимает штангу?
Распределительный вал
Толкатель
Клапан
Пружина
Тепловой зазор появляется на:
Перегретом двигателе
Холодном двигателе
Прогретом двигателе
Заглушенном двигателе
С какой скоростью вращается распределительный вал?
В два раза быстрее коленчатого вала
В два раза медленнее коленчатого вала
Со скоростью вращения коленчатого вала
В четыре раза быстрее коленчатого вала
Какая деталь закрепляет клапан в сборе с пружинами?
Тарелка
Шплинт
Сухарики
Стопорное кольцо
В каком положении должен находиться поршень при регулировке клапанов?
В ВМТ в конце такта сжатия
В НМТ в конце такта сжатия
В ВМТ в конце такта выпуска
В ВМТ в конце такта впуска
Как называется часть распределительного вала поднимающая толкатель?
Шейка
Хвостовик
Рычаг
Кулачек
Вариант 2
Тема: «Классификация и общее устройство автомобилей»
1. Трансмиссия – это …
а) механизмы тормозной системы автомобиля;
б) механизмы рулевого управления автомобиля;
в) агрегат, вырабатывающий электроэнергию на автомобиле;
г) блок механизмов, которые передают крутящий момент, от коленчатого вала двигателя к ведущим колёсам автомобиля.
2. Какие агрегаты не входит в состав шасси автомобиля:
а) трансмиссия; г) механизмы управления;
б) ходовая часть; д) грузовая платформа;
в) двигатель; е) топливный насос.
3. Что не является основной частью автомобиля:
а) шасси;
б) ходовая часть;
в) двигатель;
г) кузов;
д) грузовая платформа;
4. Расшифруйте и опишите модель автомобиля ВАЗ-21099:
___________________________________________________________
___________________________________________________________
___________________________________________________________
___________________________________________________________
___________________________________________________________
5. Расшифруйте и опишите колёсную формулу 6х6:
___________________________________________________________
___________________________________________________________
___________________________________________________________
Тема: «Классификация двигателей. Механизмы и системы двигателя внутреннего сгорания. Основные понятия»
1. Как правильно называется объём, высвобождаемый при движении поршня в цилиндре от верхней мёртвой точки к нижней мёртвой точке:
а) полный;
б) рабочий;
в) камеры сгорания;
г) картера.
2. С помощью какой системы в двигателе внутреннего сгорания идёт трансформация тока низкого напряжения в ток высокого напряжения:
а) системы питания;
б) системы охлаждения;
в) системы смазки;
г) системы отопления;
д) системы зажигания;
3. Перечислите по порядку название тактов в работе четырёхтактного двигателя (рис. 1).
а) Нет правильного ответа.
б) Выпуск, сжатие, впуск, рабочий ход.
в) Рабочий ход, впуск, сжатие, выпуск.
г) Впуск, сжатие, рабочий ход, выпуск.
Рисунок 1
4. Дать определение понятию «степень сжатия»:
а) отношение полного объема цилиндра к объему камеры сжатия, показывающее, во сколько раз полный объем цилиндра больше объема камеры сжатия;
б) комплекс последовательных периодически повторяющихся процессов (впуск, сжатие, сгорание, расширение и выпуск), в результате которых энергия топлива преобразуется в механическую работу.
в) положение поршня в цилиндре, при котором расстояние от него до оси коленчатого вала двигателя наименьшее
г) это сумма рабочих объемов всех его цилиндров, выраженная в литрах.
5. Дать определение понятию «такт»:
а) отношение полного объема цилиндра к объему камеры сжатия, показывающее, во сколько раз полный объем цилиндра больше объема камеры сжатия;
б) комплекс последовательных периодически повторяющихся процессов (впуск, сжатие, сгорание, расширение и выпуск), в результате которых энергия топлива преобразуется в механическую работу.
в) часть рабочего цикла, происходящая за время движения поршня от одной мертвой точки до другой
г) это сумма рабочих объемов всех его цилиндров, выраженная в литрах.
6. Что такое рабочий цикл двигателя:
а) комплекс последовательных периодически повторяющихся процессов (впуск, сжатие, сгорание, расширение и выпуск), в результате которых энергия топлива преобразуется в механическую работу.
б) положение поршня в цилиндре, при котором расстояние от него до оси коленчатого вала двигателя наименьшее.
в) положение поршня в цилиндре, при котором расстояние от него до оси коленчатого вала двигателя наибольшее.
г) это сумма рабочих объемов всех его цилиндров, выраженная в литрах.
Тема: «Кривошипно-шатунный механизм»
Материал изготовления блоков цилиндров
чугун
алюминий
сталь
железо
Базовой деталью КШМ и всего двигателя является
маховик
коленвал
блок цилиндров
поршни
шатуны
К подвижным деталям КШМ относятся
шатуны е) бугеля
поршни ж) вкладыши
блок цилиндров з) поршневые кольца
клапана и) маховик
коленвал к) сухари
К неподвижным деталям КШМ относятся
а) шатуны е) бугеля
б) поршни ж) вкладыши
в) блок цилиндров з) поршневые кольца
г) клапана и) маховик
д) коленвал к) сухари
Прорези на юбке поршня предназначены для …
снижения нагрева
уменьшения массы поршня
увеличения прочности поршня
компенсации теплового расширения
отвода масла со стенок цилиндров
Материал вкладышей
сплав стали и алюминия
сплав меди и свинца
бронза
Маслосъёмные кольца служат для …
упрочнения поршня г) снятия излишек масла со стенок цилиндра
уплотнения цилиндра д) снижения детонации
уменьшения массы е) поршня снижения масла на угар
С помощью чего коленвал фиксируется от осевого смещения?
стопорной шайбой
вкладышами
упорными полукольцами
упорными шарикоподшипниками
В каком положении должен находиться поршень при регулировке клапанов?
В ВМТ в конце такта сжатия
В НМТ в конце такта сжатия
В ВМТ в конце такта выпуска
В ВМТ в конце такта впуска
Какая деталь не входит в шатунно-поршневую группу?
Шейка
Поршневой палец
Поршень
Кулачек
Тема: «Газораспределительный механизм»
1. Какую функцию в двигателе выполняет ГРМ:
а) приготавливает горючую смесь из паров топлива и воздуха;
б) отводит лишнее тепло от деталей двигателя;
в) своевременно впускает в цилиндры двигателя горючую смесь (воздух) и выпускает отработавшие газы;
г) подаёт смазку к трущимся поверхностям деталей двигателя.
2. Правильное соотношение вращения газораспределительной шестерни и шестерни коленчатого вала:
а) 1 : 1; б) 1 : 2; в) 1 : 3; г) 1 : 4.
3. Штанга передаёт усилие:
а) от газораспределительного вала к толкателю;
б) от толкателей к коромыслам;
в) от толкателей к клапану;
г) от клапана к газораспределительной шестерне.
4. Из какого материала выполнена направляющая втулка клапанов:
а) асбеста; б) алюминиевая бронза; в) чугуна; г) металлокерамики.
5. Фазы газораспределения – это…
а) скорость, с которой выхлопные газы выходят из глушителя;
б) количество вредных веществ в выхлопных газах;
в) моменты открытия и закрытия клапанов относительно мёртвых точек, выраженные в градусах поворота коленчатого вала;
г) скорость открытия и закрытия клапанов относительно мёртвых точек
6. Внешними признаками неисправности ГРМ двигателя являются:
а) уменьшение компрессии и хлопки во впускном и выпускном трубопроводах;
б) падение мощности двигателя и металлические стуки;
в) все перечисленные факторы.
7. Плохое прилегание клапана к седлу возможно вследствие:
а) коробления головок клапанов;
б) заедания стержня клапана в направляющей втулке;
в) отсутствия зазора между стержнем клапана и коромыслом;
г) всех перечисленных факторов;
8. Регулировка теплового зазора в клапанах производится для:
а) обеспечения плотной посадки клапана в седле;
б) обеспечения плотной посадки клапана в направляющей втулке;
в) обеспечения плотного прилегания клапана к коромыслу;
г) обеспечения бесшумной работы газораспределительной шестерни.
9. Какая деталь закрепляет клапан в сборе с пружинами?
а) Тарелка
б) Шплинт
в) Сухарики
г) Стопорное кольцо
10. В каком положении должен находиться поршень при регулировке клапанов?
а) В ВМТ в конце такта сжатия
б) В НМТ в конце такта сжатия
в) В ВМТ в конце такта выпуска
г) В ВМТ в конце такта впуска
Вариант 3
Тема: «Классификация и общее устройство автомобилей»
1. Какие системы относятся к механизмам управления автомобилем:
а) система питания;
б) тормозная система;
в) система зажигания;
г) система рулевого управления.
2. Шасси – это…
а) система, объединяющая в себе механизмы, которые передают энергию двигателя к ведущим колесам;
б) устройство, преобразующее какой-либо вид энергии в механическую работу;
в) часть автомобиля или другого транспортного средства, предназначенная для размещения пассажиров и груза;
3. Какой агрегат отсутствует в ходовой части:
а) Колеса; г) КПП;
б) Мост; д) Главная передача;
в) Кузов; е) Подвеска.
4. Расшифруйте и опишите модель автомобиля ЛиАЗ-5256:
___________________________________________________________
___________________________________________________________
___________________________________________________________
___________________________________________________________
___________________________________________________________
5. Расшифруйте и опишите колёсную формулу 6х4:
___________________________________________________________
___________________________________________________________
___________________________________________________________
Тема: «Классификация двигателей. Механизмы и системы двигателя внутреннего сгорания. Основные понятия»
1. Назовите механизмы двигателя:
а) пуска; д) корреляции;
б) смазки; е) газораспределения;
в) питания; ж) кривошипно-шатунный.
г) охлаждения;
2. Степень сжатия бензиновых ДВС составляет:
а) 8-12; б) 14-18; в) 16-20; г) 6-10;
3. Укажите количество тактов ДВС в современных автомобилях:
а) два б) четыре в) шесть г) восемь
4. Дать определение понятию «полный объем цилиндра»:
а) отношение полного объема цилиндра к объему камеры сжатия, показывающее, во сколько раз полный объем цилиндра больше объема камеры сжатия;
б) комплекс последовательных периодически повторяющихся процессов (впуск, сжатие, сгорание, расширение и выпуск), в результате которых энергия топлива преобразуется в механическую работу.
в) сумма объема камеры сжатия и рабочего объема цилиндра, т. е. пространство над поршнем, когда он находится в н. м. т.
г) это сумма рабочих объемов всех его цилиндров, выраженная в литрах.
5. Дать определение понятию «нижняя мертвая точка»:
а) отношение полного объема цилиндра к объему камеры сжатия, показывающее, во сколько раз полный объем цилиндра больше объема камеры сжатия;
б) положение поршня в цилиндре, при котором расстояние от него до оси коленчатого вала двигателя наименьшее.
в) часть рабочего цикла, происходящая за время движения поршня от одной мертвой точки до другой
г) это сумма рабочих объемов всех его цилиндров, выраженная в литрах.
6. Какое количество основных систем и механизмов имеет двигатель?
а) 2 механизма и 2 системы;
б) 4 механизма и 2 системы;
в) 2 механизма и 5 систем;
г) 4 механизма и 4 системы
Тема: «Кривошипно-шатунный механизм»
1. Какие из перечисленных деталей жестко крепятся к коленчатому валу?
а) Храповик
б) Шатун
в) Маховик
г) Шкив
2. Какие кольца установлены ближе к днищу поршня?
а) Компрессорные
б) Маслосъемные.
в) Компрессионные или маслосъемные в зависимости от конструктивных особенностей поршня
г) Отражатели
3. В чем состоит назначение КШМ?
а) Сжатие смеси в цилиндрах двигателя
б) Преобразование возвратно-поступательного движения
в) Передача усилия
г) Соединение деталей двигателя
4. Какая деталь КШМ сделана из алюминиевого сплава?
а) Стопорное кольцо
б) Коленчатый вал
в) Поршневой палец
г) Поршень
5. Какая деталь отсутствует в поршне?
а) Юбка
б) Днище
в) Грязевая камера
г) Бабышка
6. Какой из поршней, одной марки двигателя, имеет наибольший диаметр?
а) Номинальный
б) Первого ремонта
в) Второго ремонта
г) Третьего ремонта
7. Маслосъёмные кольца служат для …
а) упрочнения поршня г) снятия излишек масла со стенок цилиндра
б) уплотнения цилиндра д) снижения детонации
в) уменьшения массы поршня е) снижения масла на угар
8. С помощью чего коленвал фиксируется от осевого смещения?
а) стопорной шайбой
б) вкладышами
в) упорными полукольцами
г) упорными шарикоподшипниками
9. Какая деталь не входит в шатунно-поршневую группу?
а) Шейка
б) Поршневой палец
в) Поршень
г) Кулачек
10. Какой технологической операции из перечисленных, подвергают коленчатый вал в сборе с маховиком?
а) взвешиванию для определения центра тяжести
б) окраске и лакировке для уменьшения коррозии
в) статической и динамической балансировке
г) проводят все операции, указанные в пунктах а) и б)
Тема: «Газораспределительный механизм»
1. Какие типы газораспределительных механизмов получили наибольшее распространение на автомобильных двигателях?
а) золотниковые
б) клапанные
в) оба типа механизмов
2. Какой ГРМ имеет меньшее количество деталей?
а) с нижним расположением клапанов
б) с верхним расположением клапанов
в) имеют одинаковое количество деталей.
3. Каким способом осуществляется привод газораспределительного механизма?
а) зубчатыми колесами
б) цепным или зубчатым ремнем
в) в зависимости от типа и модели двигателя способом, указанным в пункте а) или б).
4. Для чего предназначен толкатель ГРМ?
а) для передачи усилия от распределительного вала
б) для передачи усилия от поршня
в) для поворота клапана вокруг своей оси.
5. В каком ответе перечислены только детали ГРМ?
а) распределительный вал, штанга толкателя, коромысло, поршневой палец, клапан выпускной
б) толкатель, седло клапана, сухари, тарелка пружины клапана, направляющая толкателя
в) направляющая втулка клапана, ось коромысел, головка цилиндров, пружина клапана.
6. Как крепится тарелка пружины клапана к стержню клапана?
а) установочным штифтом
б) при помощи резьбы
в) контактной сваркой
г) сухариками.
7. Сколько опорных шеек имеет распределительный вал двигателя?
а) в 2 раза меньше коренных шеек коленвала;
б) в 2 раза меньше шатунных шеек коленвала;
в) такое же количество как и шатунных шеек коленвала;
г) такое же количество как и коренных шеек коленвала.
8. Как отличить впускной клапан от выпускного одного двигателя?
а) по длине стержня клапана
б) по диаметру тарелки клапана
в) по маркировке.
9. Какой клапан при работе двигателя нагревается до более высокой температуры?
а) впускной
б) выпускной
в) клапана одного цилиндра нагреваются до одинаковой температуры.
10. Какие детали ГРМ заставляют клапана открываться и закрываться?
а) открывает и закрывает распределительный вал
б) открывает кулачек распредвала, закрывает пружина
в) открывает пружина, закрывает кулачек распредвала.
Вариант 4
Тема: «Классификация и общее устройство автомобилей»
1. Что на автомобиле является источником механической энергии:
а) кузов;
б) двигатель;
в) шасси;
г) аккумуляторная батарея;
2. Какие преимущества имеет V- образный двигатель перед рядным?
а) компактность и увеличенная жесткость коленвала;
б) уменьшение высоты двигателя;
в) увеличение длины и ширины двигателя;
г) нет преимуществ.
3. Какие автомобили относятся к легковым?
а) автомобили длиной менее 5 метров;
б) автомобили с двигателем менее 1,8 литров;
в) пассажирские автомобили вместимостью не более 8 человек;
г) автомобили массой не более 2 тонн
4. Расшифруйте и опишите модель автомобиля ПАЗ-32053:
___________________________________________________________
___________________________________________________________
___________________________________________________________
___________________________________________________________
___________________________________________________________
5. Расшифруйте и опишите колёсную формулу 4х2:
___________________________________________________________
___________________________________________________________
___________________________________________________________
Тема: «Классификация двигателей. Механизмы и системы двигателя внутреннего сгорания. Основные понятия»
1. За сколько оборотов коленчатого вала совершается рабочий цикл в четырехтактном двигателе:
а) За 1 оборот (360o)
б) За 2 оборота (720°)
в) За 4 оборота (1440°)
2. Назовите системы двигателя:
а) пуска; г) охлаждения;
б) смазки; д) газораспределения;
в) питания; е) кривошипно-шатунный.
3. Из какого материала изготавливают блок цилиндров:
а) серый чугун;
б) углеродистая сталь;
в) легированная сталь;
г) алюминиевый сплав.
д) высокопрочная легированная сталь.
4. Дать определение понятию «полный объем цилиндра»:
а) отношение полного объема цилиндра к объему камеры сжатия, показывающее, во сколько раз полный объем цилиндра больше объема камеры сжатия;
б) комплекс последовательных периодически повторяющихся процессов (впуск, сжатие, сгорание, расширение и выпуск), в результате которых энергия топлива преобразуется в механическую работу.
в) сумма объема камеры сгорания и рабочего объема цилиндра, т. е. пространство над поршнем, когда он находится в н. м. т.
г) это сумма рабочих объемов всех его цилиндров, выраженная в литрах.
5. Дать определение понятию «нижняя мертвая точка»:
а) отношение полного объема цилиндра к объему камеры сжатия, показывающее, во сколько раз полный объем цилиндра больше объема камеры сжатия;
б) положение поршня в цилиндре, при котором расстояние от него до оси коленчатого вала двигателя наименьшее.
в) часть рабочего цикла, происходящая за время движения поршня от одной мертвой точки до другой
г) это сумма рабочих объемов всех его цилиндров, выраженная в литрах.
6. Поршень движется от НМТ к ВМТ, открыт выпускной клапан. Какой такт происходит в цилиндре двигателя?
а) Впуск;
б) Сжатие;
в) Рабочий ход;
г) Выпуск.
Тема: «Кривошипно-шатунный механизм»
1. Назовите геометрические параметры КШМ:
а) ход поршня; д) ширина двигателя;
б) рабочий объем; е) объем камеры сгорания;
в) степень сжатия; ж) полный объем цилиндра.
г) длина двигателя;
2. Сколько шатунов крепится на 1 шатунной шейке коленвала 8-ми цилиндрового V-образного двигателя?
а) один б) два в) четыре г) восемь
3. Рядный четырехцилиндровый двигатель имеет коленвал на котором……
а) 4 коренных и 4 шатунных шеек
б) 5 коренных и 4 шатунных шеек
в) 4 коренных и 5 шатунных шеек
г) 5 коренных и 5 шатунных шеек.
4. По назначению поршневые кольца делятся на ……
а) уплотнительные и маслосъемные
б) компрессионные и уплотнительные
в) компрессионные и маслосъемные.
г) уплотнительные и стопорные
5. Каким способом фиксируется поршневой палец в поршне?
а) стопорными кольцами
б) стопорными штифтами
в) установочными болтами
6. Какая деталь КШМ обеспечивает требуемую форму камеры сгорания, герметичность внутрицилиндрового пространства и передает силу давления газов на шатун?
а) гильза цилиндра
б) головка цилиндра
в) поршень
7. Что является направляющей для поршня при его перемещениях в двигателе?
а) блок-картер
б) гильза цилиндра
в) коленвал
8. Какую гильзу называют «мокрой»?
а) гильза, внутренняя поверхность которой смазывается маслом
б) гильза, наружная поверхность которой омывается охлаждающей жидкостью
в) гильза, которая охлаждается воздухом.
9. Какой технологической операции из перечисленных, подвергают коленчатый вал в сборе с маховиком?
а) взвешиванию для определения центра тяжести
б) окраске и лакировке для уменьшения коррозии
в) статической и динамической балансировке
г) проводят все операции, указанные в пунктах а) и б)
10. Какая часть шатуна разъемная?
а) Нижняя головка шатуна
б) Верхняя головка шатуна
в) Шейка
г) Никакая
Тема: «Газораспределительный механизм»
1. Какова частота вращения распределительного вала по сравнению с коленчатым валом на четырехтактном двигателе?
а) вращается в 2 раза быстрее коленвала
б) вращается с такой же скоростью как коленвал
в) вращается в 2 раза медленнее коленвала
г) вращается независимо от коленвала.
2. Штанга передает усилие от толкателя к коромыслу. Может ли конструкция ГРМ обходиться без штанг?
а) не могут, так как такой механизм не сможет работать
б) может, в ГРМ с нижним расположением клапанов
в) могут в ГРМ с верхним расположением клапанов и распределительного вала.
3. Какие детали входят в клапанный узел ГРМ?
а) впускной клапан, седло клапана, пружина клапана, направляющая втулка клапана, компрессионное кольцо
б) впускной клапан, тарелка пружины клапана, маслосъемное кольцо, сухари, механизм вращения клапана
в) впускные и выпускные клапана, опорная шайба пружины клапана, седло клапана, сухари.
4. Каким термином называют моменты открытия и закрытия клапанов относительно мертвых точек, выражая в градусах поворота коленчатого вала?
а) перекрытием клапанов
б) фазами газораспределения
в) порядком работы цилиндров.
г) угол опережения зажигания
5. В какой последовательности передается усилие в приводе клапанов?
а) распредвал, толкатель, штанга толкателя, регулировочный винт, коромысло, клапан
б) распредвал, толкатель, регулировочный винт, штанга толкателя, коромысло, клапан
в) распредвал, толкатель, штанга толкателя, клапан, коромысло, регулировочный винт.
6. Что обеспечивает герметичность сопряжений клапан-седло клапана?
а) их шлифовка и притирка по месту пастами
б) подгонка по месту с применением уплотнителей
в) установка самоподжимных манжет.
7. Для чего предназначен газораспределительный механизм дизельного двигателя?
а) Для подачи топлива
б) Для подачи воздуха
в) Для впуска воздуха и выпуска отработанных газов
г) Для распределения газов по цилиндрам двигателя
8. Какая из деталей больше всего нагревается при работе двигателя?
а) Штанга
б) Выпускной клапан
в) Впускной клапан
г) Распределительный вал
9. Фазы газораспределения – это…
а) скорость, с которой выхлопные газы выходят из глушителя;
б) количество вредных веществ в выхлопных газах;
в) моменты открытия и закрытия клапанов относительно мёртвых точек, выраженные в градусах поворота коленчатого вала;
г) скорость открытия и закрытия клапанов относительно мёртвых точек
10. Внешними признаками неисправности ГРМ двигателя являются:
а) уменьшение компрессии и хлопки во впускном и выпускном трубопроводах;
б) падение мощности двигателя и металлические стуки;
в) все перечисленные факторы.
Коренные подшипники
Надежность работы вкладышей коленчатого вала в значительной степени определяет надежность и моторесурс дизеля и зависит от правильного подбора конструктивных параметров вкладышей, материала и условий смазывания, жесткости коленчатого вала, блока н постелей под вкладыши и от многих других факторов.
Вкладыши коренных подшипников бывают толстостенные (у дизелей типа Д100) и тонкостенные (у дизелей типов Д49, 11Д45, ПД1М и др.). Толстостенные вкладыши постепенно уступили место в современных быстроходных дизелях тонкостенным. Тонкостенные вкладыши, имеющие меньшие размеры и массу, более экономичны для серийного производства и позволяют обеспечить взаимозаменяемость при сборке и ремонте без пришабровки и пригонки. Благодаря постановке тонкостенных вкладышей в постели подшипника с некоторым натягом достигается необходимая плотность их прилегания к полостям, что плохо обеспечивается при толстостенных вкладышах.
Коренные вкладыши дизелей 10Д100 (рис. 61) выполнены из бронзы и залиты слоем свинцовистого баббита БК 2 толщиной 0,5-0,7 мм. Толщина новых вкладышей 19 мм. Необходимость применения толстостенных вкладышей вызвана тем, что постели под вкладыши верхнего коленчатого вала в средней части сужены (чтобы можно было вынуть цилиндровые втулки из блока) и это значительно уменьшает опорную поверхность вкладышей. В этих условиях только толстостенные вкладыши обеспечивают необходимую жесткость опоры. Стремясь к унификации, вкладыши нижнего вала выполняют также толстостенными.
В зависимости от нагрузки, воспринимаемой вкладышами, их делят на рабочие и нерабочие. Основную нагрузку от давления газов и сил инерции несут рабочие вкладыши (рис. 61, а, б), расположенные в крышках подшипников нижнего и верхнего валов. Нерабочие вкладыши (рис. 61, в), уложенные в постели блока, выполнены одинаковыми для нижнего и верхнего подшипников. Они в середине имеют отверстие и канавку по всей полуокружности внутренней поверхности. Отверстие и канавка служат для подвода масла от масляного канала коленчатого вала. Эти вкладыши называют канавочными.
Рабочие вкладыши выполнены бес-канавочными. Для нижнего и верхнего подшипников они неодинаковы. Рабочие вкладыши подшипников верхнего вала (см. рис. 61, б) по наружной поверхности имеют канавку, сообщающуюся по концам с внутренней поверхностью двумя отверстиями. Масло из маслоподводящего канала в крышке подшипника поступает сверху в канавку вкладыша и далее по отверстиям в маслозахватывающие карманы, откуда увлекается вращающимся валом на шейку подшипника.
Карманы у торцов вкладышей выполнены с плавным переходом поверхности для обеспечения «масляного клина» при вращении шейки.
Рабочие вкладыши подшипников нижнего вала смазываются маслом, попадающим в их карманы по канавке от верхних канавочных вкладышей. Отсутствие канавки у рабочего вкладыша подшипника создает более благоприятную эпюру давления масла в смазочном слое. Известно, что для хорошей работы подшипников скольжения необходимо жидкостное трение, обеспечиваемое масляным слоем определенной толщины. Для обеспечения жидкостного трения необходимо, чтобы в несущей части масляного слоя как в поперечном, так и в продольном направлениях развивались такие гидродинамические давления, при которых результирующая сила обеспечивала бы поднятие вала относительно подшипника (рис. 62) на вполне определенный минимальный размер, зависящий от высоты неровностей поверхностей вала и подшипника и от деформаций.
Наличие смазочных канавок или неблагоприятное расположение смазочных поверхностей может значительно уменьшить несущую способность подшипника за счет уменьшения давления внутри масляного слоя. Наглядно это показано на рнс. 62, бив. При бесканавочных вкладышах максимальное давление внутри масляного слоя значительно выше, чем при канавочных вкладышах. Вкладыши подшипников по толщине изготовляют по градационным размерам с интервалом между градациями 0,25 мм. Всего градаций семь. Толщина вкладыша нулевого градационного размера 19 мм.
Вкладыши от проворота и осевого смещения фиксируют штифтами. Одиннадцатые подшипники (см. рис. 61, г) нижнего и верхнего валов являются упорными. Онн отличаются от опорных наличием по торцам нерабочих вкладышей буртов, которыми вкладыши охватывают опоры подшипников. К буртам по отверстиям и канавкам подводится масло.
Коренные подшипники коленчатого вала дизеля 2А-5Д49 имеют тонкостенные стальные вкладыши, залитые тонким слоем свинцовистой бронзы, на которую лужением нанесен прирабо-точный слой свинцовистого сплава. Верхний вкладыш на внутренней поверхности имеет канавку, которая через отверстия сообщается с маслопод-водящей канавкой в стойке блока цилиндров. Нижний вкладыш бескана-вочный, около стыка имеет карманы для захвата и равномерного распределения масла по трущимся поверхностям подшипника. Вкладыши устанавливают в опорах с натягом, обеспечиваемым за счет выступания одного торца нижнего и верхнего вкладышей над плоскостью разъема подшипника на 0,22-0,26 мм. При затяжке болтов подшипника за счет натяга обеспечивается плотное прилегание вкладышей к постелям. Дополнительное положение вкладышей фиксируется штифтом, запрессованным в подвеску блока. Упорный подшипник состоит из сталь-
Рис. 62. Эпюры гидродинамического давления в масляном слое подшипника:
о в поперечном сечении; 6 — в продольном сечении бесканавочного вкладыша: в н продольном сечении канавомного вктадьииа
Рис. 63. Коренные подшипники коленчатого вала дизеля ПД1М:
1 — опора вкладыша; 2 вкладыши опорных подшипников; — крышка; 4 — шпилька крепления крышки: 5 — вкладыш опорно упорного подшипника; а — отверстие подвода масла; б — холодильник; в — канавка кольцевая: г — отверстие; д — выступ ()ямок)
ных полуколец, прикрепленных винтами к девятой стойке и подвеске блока. Опорная поверхность полуколец покрыта тонким слоем бронзы.
Коренные подшипники дизеля ПДІМ (рис. 63) состоят из двух одинаковых бронзовых канавочных вкладышей 2, крышки <?, установленной на шпильках 4 на раме дизеля, и трубки, подводящей масло к отверстию а подшипника. Вкладыши установлены с натягом 0,26 мм, удерживающим их от проворачивания. От осевого смещения вкладыши фиксируются выступами д, входящими в пазы постелей рамы и крышек. По толщине вкладыши изготавливают по десяти градационным размерам. Толщина вкладыша нулевого градационного размера 7,5 мм, а десятого 10 мм. Толщина баббитовой заливки вкладышей 0,75 мм.
Вкладыши подшипников отличаются по ширине. У четвертого она
Рис. 64. Валоповоротный механизм равна 179 мм, у седьмого — 208 мм, а у остальных — 146 мм. Вкладыши седьмого подшипника б имеют бурты, которые ограничивают перемещение вала в подшипнике. Рабочие поверхности буртов также залиты баббитом. Крышки подшипников пригоняют к горизонтальным и вертикальным плоскостям опор блока по краске. Плотная посадка крышки в опоре разгружает шпильки 4 от срезывающих и изгибающих усилий.
Дизель-генераторные муфты и ва-лоповоротные механизмы. Для связи коленчатого вала дизеля с валом якоря генератора применяют полужесткие муфты. Для дизелей типов Д100 и Д49 муфты принципиально одинаковы. Они состоят из двух дисков 5, 6 (см. рис. 58), один из которых присоединен болтами к фланцу коленчатого вала, а второй — к фланцу вала якоря генератора. Между дисками установлен пакет тонких стальных пла-тин 4, притянутый болтами через сухари 3 к ведущему и ведомому дискам. Центрирование муфты осуществляется направляющими кольцами 7, установленными на ведущем фланце и выточке вала якоря. Благодаря зазорам в отверстиях между сухарями и дисками возможно некоторое проскальзывание ведущего диска относительно ведомого при особо резких перегрузках, предупреждающее поломки коленчатого вала.
Ведущий диск на наружной цилиндрической поверхности имеет зубья для червяка валоповоротного механизма. Валоповоротный механизм (рис. 64) служит для медленного проворачивания коленчатого вала при ремонте и регулировках дизеля. Он состоит из кронштейна 2, установленного на оси неподвижного кронштейна 1 и имеющего возможность поворачиваться на ней для ввода в зацепление червяка 4 с ведущим диском дизель-генераторной муфты. Вал 5 червяка установлен на бронзовых втулках. Кронштейн 2 застопорен штырем 6 и от произвольного включения удерживается пружинами.
В отключенном положении кронштейн с валом и червяком устанавливается в верхнее положение рукояткой 7 и стопорится штырем 6″. Конец штыря 6″ нажимает кнопку блокировочного переключателя 3 цепи пусковой системы дизеля, замыкает его контакты, обеспечивая возможность пуска дизеля. В рабочем положении штырь не замыкает контакты переключателя, цепь разомкнута и дизель не может быть пущен. Введя червяк 4 в зацепление с зубчатым диском муфты и фиксируя тем же штырем 6 кронштейн 2, проворачивают коленчатый вал ключом, установленным на шестигранную головку вала 5.
У дизеля ПД1М для проворачивания коленчатого вала на нем имеется специальный диск с отверстиями по наружному поясу для монтажного лома (см. рис. 60, поз. 1).
Вертикальная передача дизеля 10Д100. Вертикальная передача (рис. 65) служит для передачи вращающего момента от верхнего коленчатого вала к нижнему. Эта передача осуществляется с помощью двух пар конических шестерен со спиральными зубьями, двух вертикальных валов 1 и 12, на концах которых с помощью шпонок закреплены малые шестерни 2 и 13, и торсионного вала 10. Валы 1 и 12 вращаются в подшипниках нижнего 1) и верхнего 4 корпусов. Между роликовыми 3 и радиально-упорными шариковыми 6″ подшипниками верхнего и нижнего валов установлены распорные втулки 5. Роликовые подшипники стопорятся в корпусе разрезными пружинными кольцами. Наружные кольца шарикоподшипников зажимаются фланцами корпусов. Между внутренними и наружными кольцами шарикоподшипников установлены регулировочные и проставочные кольца.
Для регулирования зазора между зубьями конических шестерен под фланцы крепления корпусов 4 н И к блоку дизеля ставят стальные прокладки. Для этой же цели прокладки установлены между фланцами коленчатых валов и большими шестернями.
Нижний вертикальный вал 12 выполнен полым для прохода торсионного вала 10, который своим нижним концом соединен с ним шлицами.
Рис 65. Вертикальная передача дизеля 1 ОД 100:
12 — нижний и верхний вертикальные валы; 2, 13 — конические шестерни; 3 — роликоподшипники; 4, И — корпуса; 5 — распорные втулки; 6 — шарикоподшипники; 7,3 — полумуфты; 9 — шлицевая втулка; 10 — торсионный вал
Верхним концом торсионный вал соединен со шлицевой втулкой 9, которая соединяется также шлицами с полумуфтой 8. Полумуфта 8 болтами присоединена к полумуфте 7, насаженной на конусный хвостик вертикального вала.
К шарикоподшипникам нижнего вертикального вала масло подается через угловой штуцер, ввернутый во фланец корпуса. Роликовый подшипник 3 смазывается маслом, стекающим из шариковых подшипников. Нижняя пара шестерен смазывается струями масла, подводимого по трубопроводу из нижнего масляного коллектора дизеля. Верхняя пара шестерен смазывается также струями масла, подводимого из верхнего масляного коллектора. По каналам в корпусе 4 масло поступает к роликовому подшипнику 3 и далее, стекая, смазывает шариковые подшипники 6″.
⇐ | Коленчатые валы | | Тепловозы: Механическое оборудование: Устройство и ремонт | | Общие понятия о крутильных колебаниях коленчатого вала дизеля. Антивибраторы | ⇒
Описание и работа механизмов и систем двигателей
ОПИСАНИЕ И РАБОТА МЕХАНИЗМОВ И СИСТЕМ ДВИГАТЕЛЕЙБЛОК ЦИЛИНДРОВ является основной корпусной деталью двигателя и представляет собой отливку из чугуна. Блок цилиндров двигателя составляют два ряда полублоков под гильзы цилиндров, расположенных V-образно под углом 90° один к другому и представляющих одно целое с верхней частью картера. Левый ряд расточек под гильзы смещен относительно правого вперед (к вентилятору) на 29,5 мм, что обусловлено установкой двух шатунов на каждую шатунную шейку коленчатого вала.
В каждом ряду имеется по четыре цилиндра, выходящие на верхние обработанные плоскости, которые служат привалочными поверхностями для головок цилиндров. Прива-лочные поверхности отличаются высокой плоскостностью и параллельностью оси расточек под подшипники коленчатого вала.
Каждый цилиндр имеет два соосных цилиндрических отверстия, выполненных в верхнем и нижнем поясках блока, по которым центрируются гильза цилиндра, и выточки в верхнем поясе, образующие кольцевые площадки под бурты гильз. Чтобы обеспечить правильную посадку гильзы в цилиндре, параметры плоскостности и перпендикулярности упорной площадки под бурт гильзы к общей оси центрирующих расточек должны быть выполнены с высокой точностью. На нижнем пояске выполнены две канавки под уплотнительные кольца, которые предотвращают попадание охлаждающей жидкости из полости охлаждения блока в полость масляного картера двигателя.
Бобышки болтов крепления головок цилиндров выполнены в виде приливов к поперечным стенкам, образующим рубашку охлаждения, равномерно распределены вокруг каждого цилиндра.
Поперечные перегородки в нижней части блока цилиндров заканчиваются толстостенными арками, образующими коренные опоры коленчатого вала, к обработанным площадкам которых крепятся крышки коренных подшипников.
Картерная часть блока связана с крышками коренных подшипников коренными и стяжными болтами. Крышка пятой коренной опоры центрируется в продольном направлении по двум вертикальным штифтам, обеспечивая точность совпадения расточек под упорные полукольца коленчатого вала на блоке и на крышках.
Порядок затяжки болтов крепления крышек коренных опор приведен в таблице 14 (см. раздел «Ремонт двигателя»).
Расточка блока цилиндров под вкладыши коренных подшипников производится в сборе с крышками, поэтому крышки коренных подшипников не взаимозаменяемы и устанавливаются в строго определенном положении. На каждой крышке нанесен порядковый номер опоры, нумерация опор начинается с переднего торца блока.
В картерной части развала блока цилиндров в виде бобышек выполнены направляющие толкателей клапанов. Ближе к заднему торцу выполнена перепускная труба полости охлаждения, между четвертым и восьмым цилиндрами, для улучшения циркуляции охлаждающей жидкости. Одновременно она придает блоку еще и дополнительную жесткость. Параллельно оси расточек под подшипники коленчатого вала выполнены расточки под втулки распределительного вала увеличенной размерности.
С целью увеличения циркуляционного запаса масла на двигатель устанавливается масляный насос увеличенной производительности. Поэтому диаметры масляных каналов в блоке цилиндров существенно увеличены. В нижней части цилиндров отлиты заодно с блоком бобышки под форсунки охлаждения поршней.
Для установки на блок фильтра с теплообменником на правой стороне увеличены площадка и выполнены два дополнительных крепежных отверстия, а также сливное отверстие из фильтра. Блоки цилиндров под рядную и V-образную топливную аппаратуру не взаимозаменяемы!
ГИЛЬЗЫ ЦИЛИНДРОВ (см. рисунок 22 — Установка гильзы и форсунки охлаждения поршня)»мокрого» типа, легкосъемные, имеют маркировку 740.51-1002021 на конусной поверхности в нижней части,нанесенную ударным способом. Установка гильз с другой маркировкой недопустима, т.к. это приведет к ускоренному износу гильз и поршневых колец.
В соединении гильза-блок цилиндров полость охлаждения уплотнена резиновыми кольцами круглого сечения. В верхней части установлено кольцо в проточке гильзы, в нижней части — два кольца в расточки блока.
Рисунок 22 — Установка гильзы и форсунки охлаждения поршня: 1 — трубка форсунки; 2 — корпус форсунки; 3 — корпус клапана; 4, 6 — уплотнительные кольца; 5 — гильза
Гильза цилиндра изготавливается из серого специального чугуна, без упрочняющей термообработки. Микрорельеф на зеркале гильзы представляет собой редкую сетку впадин и площадок под углом к оси гильзы. При работе двигателя масло удерживается во впадинах, что улучшает прирабатываемость деталей цилиндропоршневой группы.
При сборке двигателя на нерабочем выступе торца гильзы наносится номер цилиндра и индекс варианта исполнения поршня.
ПРИВОД АГРЕГАТОВ (см. одноименный рисунок 23)осуществляется прямозубыми зубчатыми колесами и служит для привода механизма газораспределения, ТНВД, компрессора и насоса гидроусилителя рулевого управления автобуса. Зубчатые колеса устанавливаются на двигатель в строго определенном положении по метке «0»на зубчатом колесе привода распределительного вала, метке «Е»на зубчатом колесе привода ТНВД и рискам,выбитым на зубчатых колесах. Механизм газораспределения приводится в действие от ведущего зубчатого колеса (с модулем зуба 4,5 мм), закрепленного на хвостовике коленчатого вала, через блок промежуточных зубчатых колес, которые вращаются на двух рядах роликов 3, разделённых промежуточной втулкой 4 и расположенных на оси 1, закреплённой на заднем торце блока цилиндров. На хвостовик распределительного вала напрессовано зубчатое колесо 16 (с модулем зуба 3 мм), угловое расположение которого относительно кулачков вала определяется шпонкой. Зубчатое колесо 15 привода ТНВД установлено на вал 13 привода ТНВД с натягом и ориентируется шпонкой 14.
Привод ТНВД осуществляется от колеса 15, находящегося в зацеплении с колесом 16 привода распределительного вала. Вращение от вала к ТНВД передается через ведущую и ведомую полумуфты с упругими пластинами, которые компенсируют несоосность установки валов ТНВД и зубчатых колес. С колесом привода ТНВД находятся в зацеплении зубчатые колеса компрессора и насоса гидроусилителя рулевого управления.
К заднему торцу блока цилиндров крепится картер агрегатов. В верхней части картера агрегатов есть расточки, в которые устанавливаются компрессор и насос гидроусилителя рулевого управления. По бокам картера агрегатов выполнены бобышки с отверстиями для слива масла из турбокомпрессоров и отверстием под указатель уровня масла.
В верхней части картера агрегатов и картера маховика слева выполнен прилив, предназначенный для установки коробки отбора мощности (КОМ). В случае отсутствия КОМ внутренние поверхности прилива не обрабатываются.
Привод агрегатов закрыт картером маховика, закреплённым к заднему торцу блока цилиндров через картер агрегатов.
При необходимости отбора мощности от двигателя, может быть установлен картер маховика с люком для установки коробки отбора мощности.
Рисунок 23 -Привод агрегатов: 1 — болт крепления роликового подшипника; 2 — промежуточное зубчатое колесо; 3 — болт; 4, 16 — шайбы; 5 — манжета; 6 — корпус заднего подшипника; 7 — прокладка; 8 — вал колеса привода ТНВД; 9, 19 — шпонки; 10, 12, 18 — подшипники; 11 — зубчатое колесо привода ТНВД; 13 — вал распределительный в сборе с зубчатым колесом; 15 — ось с фланцем; 18 — болт крепления оси ведущего колеса; 20 — ведущее зубчатое колесо привода распределительного вала; 21, 22 — кольца упорные; 23 — ведущее зубчатое колесо коленчатого вала
На картере маховика справа предусмотрено место под фиксатор маховика, применяемый для установки угла опережения впрыскивания топлива и регулирования тепловых зазоров в механизме газораспределения.
Ручка фиксатора при работе двигателя должна находиться в верхнем положении. В нижнее положение ее переводят при регулировочных работах, в этом случае фиксатор находится в зацеплении с маховиком (см. рисунок 24 — Положения ручки фиксатора маховика).В верхней части картера маховика выполнена расточка, в которую устанавливается корпус заднего подшипника вала привода ТНВД. Внизу в левой части картера имеется расточка, в которую устанавливается стартер. В середине картера выполнена расточка под манжету коленчатого вала.
Рисунок 24 — Положения ручки фиксатора маховика: а) — при эксплуатации; б) — при регулировке в зацеплении с маховиком
КОЛЕНЧАТЫЙ ВАЛ (см. рисунок 25)изготовлен из высококачественной стали с упрочнением методом карбонитрирования или азотирования.
Валы имеют пять коренных и четыре шатунных шейки, связанные щеками и сопряженные с ними переходными галтелями.
Для равномерного чередования рабочих ходов расположение шатунных шеек коленчатого вала выполнено под углом 90°. На шатунные шейки устанавливаются по два шатуна: один для правого и один для левого рядов цилиндров (см. рисунок 28 — Поршень с кольцами в сборе с шатуном).
Подвод масла к шатунным шейкам производится через отверстия 5 в коренных и отверстия 4 в шатунных шейках (см. рисунок 25 — Коленчатый вал).
Рисунок 25 — Коленчатый вал: 1 — противовес коленчатого вала передний; 2 — шпонка; 3 — шестерня привода масляного насоса; 4 — отверстие подвода масла к шатунным шейкам; 5 — отверстие подвода масла в коренных шейках
Для уравновешивания сил инерции и уменьшения вибраций коленчатый вал имеет шесть противовесов, отштампованных заодно со щеками коленчатого вала. Кроме основных противовесов имеется дополнительный съемный противовес 1, напрессованный на вал, его угловое расположение относительно коленчатого вала определяется шпонкой 3.
На двигателях с электронной системой управления с топливной аппаратурой фирмы «BOSCH» съемный противовес 1 имеет зубчатый обод, предназначенный для работы индуктивного датчика, установленного в передней крышке блока цилиндров. На двигателях с рядным ТНВД имеется восемь пазов.
Для обеспечения требуемого дисбаланса, на маховике выполнена выборка 15 (см. рисунок 26 — Установка полуколец, вкладышей подшипников, манжеты и маховика коленчатого вала).
От осевых перемещений коленчатый вал зафиксирован двумя верхними 7 и нижними 10 полукольцами, установленными в проточках задней коренной опоры блока цилиндров, так, что сторона с канавками прилегает к упорным торцам вала.
Уплотнение коленчатого вала осуществляется резиновой манжетой 12 безпружинной конструкции с уплотнительным элементом из PTFE (модифицированный фторопласт) с дополнительным уплотняющим элементом — пыльником 13. Манжета размещена в картере 2 маховика.
На хвостовике коленчатого вала выполнена шейка 20, по которой центрируется шестерня 3 (с модулем зуба 4,5 мм) привода газораспределительного механизма и маховик 1.
На носок коленчатого вала напрессована шестерня 3 (см. рисунок 25 — Коленчатый вал)привода масляного насоса.
На торце хвостовика коленчатого вала выполнено десять резьбовых отверстий М16х1,5-6Н для крепления шестерни коленчатого вала и маховика, на торце носка — восемь резьбовых отверстий М12х1,25-6Н для крепления гасителя крутильных колебаний (см. рисунок 29 — Установка гасителя крутильных колебаний, фланца отбора мощности и шкива).
Номинальные диаметры шеек коленчатого вала:
— коренных — (95±0,015) мм;
— шатунных — (80±0,015) мм.
Коленчатые валы имеют маркировку 740.50-1005020, выполненную в поковке на третьем противовесе. Установка валов с другой маркировкой недопустима из-за значительных отличий от коленчатых валов других моделей двигателей.
ВКЛАДЫШИ КОРЕННЫХ И ШАТУННЫХ ПОДШИПНИКОВ (см. рисунок 26 -Установка полуколец, вкладышей подшипников, манжеты и маховика коленчатого вала и рисунок 28 — Поршень с кольцами в сборе с шатуном) изготовлены из стальной ленты, покрытой слоями свинцовистой бронзы, свинцовооловянистого сплава и олова.
Верхние 8 (см. рисунок 26 — Установка полуколец, вкладышей подшипников, манжеты и маховика коленчатого вала) и нижние 9 вкладыши коренных подшипников невзаимозаменяемые. В верхнем вкладыше имеется отверстие для подвода масла и канавка для его распределения.
Вкладыши 9 (см. рисунок 28 — Поршень с кольцами в сборе с шатуном) нижней головки шатуна взаимозаменяемы. От проворачивания и бокового смещения вкладыши фиксируются выступами (усами), входящими в пазы, предусмотренные в постелях блока и шатуне, а также крышках подшипников.
Рисунок 26 — Установка полуколец, вкладышей подшипников, манжеты и маховика коленчатого вала: 1 — маховик; 2 — картер маховика; 3 — шестерня привода газораспределительного механизма; 4 — установочный штифт маховика; 5 — блок цилиндров; 6 — коленчатый вал; 7, 10 — полукольца упорного подшипника коленчатого вала; 8, 9 — вкладыши подшипника; 11 — задняя крышка подшипника вала; 12 — манжета уплотнения вала; 13 — пыльник манжеты; 14 — зубчатый венец маховика; 15 — выборка под дисбаланс; 16 — болт крепления маховика; 17 — шайба; 18 — втулка дистанционная; 19 — подшипник; 20 — центрирующая шейка вала; 21 — кольцо
Рисунок 27 — Установка крышек подшипников коленчатого вала: 1 — крышка подшипника коленчатого вала; 2 — коленчатый вал; 3 — коренные болты крепления крышки подшипника коленчатого вала; 4 — стяжной болт крепления крышки подшипника левый; 5 — шайбы; 6 — стяжной болт крепления крышки подшипника правый; 7 — блок цилиндров
Для восстановления двигателяпредусмотрены восемь ремонтных размеров вкладышей. Обозначение вкладышей подшипников коленчатого вала, диаметр коренной шейки коленчатого вала, диаметр отверстия в блоке цилиндров под эти вкладыши указаны в таблице 18 (см. раздел «Ремонт КШМ”).
В связи с высокими удельными нагрузками, действующими на подшипники в двигателях нового поколения, вкладыши имеют конструктивные отличия от ранее выпускаемых, направленные на повышение их работоспособности, при этом изменена маркировка вкладышей на 740.60-1004058 (шатунные), 740.60-1005170 и 740.60-1005171 (коренные).
При ремонте коленчатого вала допускается иерешлифовка коренных и шатунных шеек с уменьшением их диаметров на 0,25 мм и применением соответствующих ремонтных типоразмеров коренных и шатунных вкладышей (см. таблицы 18 и 19 , раздел «Ремонт двигателя»).Пределы допусков диаметров шеек ремонтного коленчатого вала при восстановлении двигателя должны быть такими же, как у диаметров шеек нового коленчатого вала. Клеймо ремонтного размера нанесено на тыльной стороне вкладыша.
При шлифовке коленчатого вала по коренным шейкам до диаметра менее 94,5 мм или по шатунным шейкам до диаметра менее 79,5 мм, необходимо коленчатый вал подвергнуть повторному азотированию по специальной технологии.
Внимание. Не рекомендуется замена вкладышей при ремонте на вкладыши с маркировкой 740, т.к. при этом произойдет существенное сокращение ресурса двигателя! Допустимо применение вкладышей номинального и ремонтного типоразмеров с маркировкой 7405.
КРЫШКИ КОРЕННЫХ ПОДШИПНИКОВ (см. рисунок 27 — Установка крышек подшипников коленчатого вала)изготовлены из высокопрочного чугуна.
Крепление крышек осуществляется с помощью вертикальных коренных 3 и горизонтальных стяжных 4 и 5 болтов, которые затягиваются по определенной схеме регламентированным моментом (см. таблицу 14, раздел «Ремонт двигателя»).
Крышка пятой коренной опоры центрируется в продольном направлении двумя вертикальными штифтами, обеспечивающими точность совпадения расточек под упорные полукольца коленчатого вала на блоке и на крышках.
Рисунок 28 — Поршень с кольцами в сборе с шатуном: 1 — поршень; 2, 3 — компрессионные кольца; 4 — маслосъемное кольцо; 5 — стержень шатуна; 6 — болт крепления крышки шатуна; 7 — гайка; 8 — крышка шатуна; 9 — вкладыш нижней головки шатуна; 10 — втулка верхней головки шатуна; 11 — поршневой палец; 12 — стопорные кольца
ПОРШЕНЬ С ШАТУНОМ (см. рисунок 28) соединены пальцем 11 плавающего типа, его осевое перемещение ограничено стопорными кольцами 12. Палец изготовлен из хромоникелевой стали, диаметр отверстия 20,7 мм, с обоих торцов выполнены фаски 16×25 .
Применение пальцев с другими величинами отверстий недопустимо, т.к. это нарушает балансировку двигателя.
ПОРШЕНЬ 1 отлит из алюминиевого сплава со вставкой из износостойкого чугуна под верхнее компрессионное кольцо 2. В головке поршня выполнена тороидальная камера сгорания с вытеснителем в центральной части, она смещена относительно оси поршня в сторону от выточек под клапаны на 5 мм.
Боковая поверхность представляет собой сложную овально-бочкообразную форму с занижением в зоне отверстий под поршневой палец.
На юбку нанесено графитовое покрытие. В нижней ее части выполнен паз, исключающий при правильной сборке контакт поршня с форсункой охлаждения при нахождении в нижней мертвой точке (НМТ). Поршень комплектуется кольцами — двумя компрессионными и одним маслосъемным.
С целью обеспечения топливной экономичности и экологических показателей, применен селективный подбор поршней для каждого цилиндра по расстоянию от оси поршневого пальца до днища. По указанному параметру поршни разбиты на четыре группы: 10, 20, 30 и 40. Каждая последующая группа от предыдущей отличается на 0,11 мм.
В запасные части поставляются поршни наибольшей высоты {размер от оси поршневого пальца до днища поршня 40-й группы составляет 71,04 .004 мм), поэтому во избежание возможного контакта между ними и головками цилиндров, в случае замены, необходимо контролировать надпоршневой зазор. Если зазор между поршнем и головкой цилиндра после затяжки болтов крепления будет менее 0,87 мм, необходимо подрезать днище поршня на недостающую до этого значения величину.
Маркировка 740.60-1004015-40 выполнена на внутренней поверхности поршня.
Внимание. Установка поршней с двигателей КАМАЗ других моделей недопустима!
ШАТУН — стальной, кованый, стержень 5 имеет двутавровое сечение. Верхняя головка шатуна неразъемная, нижняя выполнена с прямым разъемом и плоским стыком.
Для точной посадки вкладышей подшипника в нижнюю головку шатун окончательно обрабатывают в сборе с крышкой 8, поэтому крышки шатунов невзаимозаменяемые.
В верхнюю головку шатуна запрессована сталебронзовая втулка 10, а в нижнюю установлены сменные вкладыши 9. Крышка нижней головки шатуна крепится с помощью гаек 7, навернутых на болты 6, предварительно запрессованные в стержень шатуна.
Затяжка шатунных болтов осуществляется по схеме, указанной в таблице 14.
На крышке и стержне шатуна нанесены метки спаренности — трехзначные порядковые номера. На крышке шатуна выбит порядковый номер цилиндра.
КОМПРЕССИОННОЕ КОЛЬЦО 2 изготавливается из высокопрочного, кольцо 3 — из серого специального, а маслосъемное 4 — из серого чугунов. Верхнее компрессионное кольцо имеет форму двухсторонней трапеции, а второе имеет форму односторонней трапеции. При монтаже торец с отметкой ТОР должен располагаться со стороны камеры сгорания.
Рабочая поверхность верхнего компрессионного кольца 2 покрыта хромокерамикой и имеет бочкообразную форму. Рабочая поверхность второго компрессионного кольца 3 упрочнена азотированием. Ее форма на втором кольце представляет собой конус с уклоном к нижнему торцу, по этому характерному признаку кольцо получило название «минутное». Минутные кольца применены для снижения расхода масла на «угар», их установка в верхнюю канавку недопустима.
МАСЛОСЪЕМНОЕ КОЛЬЦО 4 — коробчатого типа, высотой 4 мм, с пружинным расширителем, имеющим переменный шаг витков и шлифованную наружную поверхность. Средняя часть расширителя с меньшим шагом витков при установке на поршень должна располагаться в зоне замка кольца. Рабочая поверхность кольца покрыта хромом.
Маркировка поршневых колец выполнена на верхнем торце колец рядом с замком. Маркировка содержит обозначение предприятия-изготовителя — GOE и обозначение верхнего торца кольца — ТОР.
Внимание. Установка поршневых колец с других моделей двигателей КАМАЗ может привести к увеличению расхода масла на «угар» и ухудшению экологических показателей.
В ремонтный комплектвходят:
— поршень; поршневые кольца; поршневой палец;
— стопорные кольца поршневого пальца;
— гильза цилиндра;
-уплотнительные кольца гильзы цилиндра.
ФОРСУНКИ ОХЛАЖДЕНИЯ (см. рисунок 22 — Установка гильзы и форсунки охлаждения поршня)устанавливаются в картерной части блока цилиндров и обеспечивают подачу масла из главной масляной магистрали на внутреннюю полость поршней.
При сборке двигателя необходимо контролировать правильность положения трубки 1 форсунки охлаждения поршня относительно гильзы 5 цилиндра и поршня. Контакт с поршнем и деталями кривошипно-шатунного механизма недопустим.
МАХОВИК (см. рисунок 26 — Установка полуколец, вкладышей подшипников, манжеты и маховика коленчатого вала) закреплен на торце хвостовика коленчатого вала 6 десятью болтами 16, изготовленными из легированной стали, и зафиксирован штифтом 4 на центрирующей шейке 20 коленчатого вала.
С целью исключения повреждения поверхности маховика, под головки болтов устанавливаются шайбы 17. На обработанную цилиндрическую поверхность маховика напрессован зубчатый венец 14, с которым входит в зацепление шестерня стартера при пуске двигателя. Под манжету уплотнения коленчатого вала устанавливается кольцо 21с наружной хромированной поверхностью. Во внутреннюю расточку маховика установлена дистанционная втулка 18 и подшипник 19 первичного вала с двухсторонним уплотнением.
Величина моментов затяжки болтов крепления маховика указана в таблице 14 (см. раздел «Ремонт двигателя»).
При выполнении регулировочных работ по установке угла опережения впрыскивания топлива и величин тепловых зазоров в клапанах маховик фиксируется при помощи фиксатора (см. рисунок 24 — Положения ручки фиксатора маховика).
Маркировка маховика выполнена на литой поверхности со стороны сцепления.
Применяемость маховиков на двигателях, комплектуемых сцеплениями, приведена в таблице 8.
Таблица 8
Маркировка маховика | Угол опережения впрыскивания топлива, градусов поворота коленчатого вала до В. | Применяемость |
740.60-1005115 | 9±1 | Двигатели КАМАЗ 740.62-280 и 740.65-240 с V-образным ТНВД ОАО «ЯЗДА» |
740.60-1005115-10 | 11+1 | Двигатели КАМАЗ 740.62-280 и 740.65-240 с рядным ТНВД ф. «BOSCH» |
Внимание. Установка маховиков других моделей двигателей КАМАЗ, а также маховиков двигателей одной модели, но с другими вариантами топливных аппаратур, при проведении ремонтных работ не допускается!
ГАСИТЕЛЬ КРУТИЛЬНЫХ КОЛЕБАНИЙ (см. рисунок 29)закреплен восемью болтами 11 на переднем носке коленчатого вала 6. Гаситель состоит из корпуса 8, в который установлен с зазором маховик 9 гасителя. Снаружи корпус гасителя закрыт крышкой 10.
Герметичность обеспечивается сваркой по стыку корпуса гасителя и крышки. Между корпусом гасителя и маховиком находится высоковязкостная силиконовая жидкость 4, дозировано заправленная перед заваркой крышки.
Гашение крутильных колебаний коленчатого вала происходит путем торможения корпуса гасителя, закрепленного на носке коленчатого вала, относительно маховика в среде силиконовой жидкости. При этом энергия торможения выделяется в виде теплоты.
Внимание. При проведении ремонтных работ категорически запрещается деформировать корпус и крышку гасителя. Гаситель с деформированным корпусом или крышкой к дальнейшей эксплуатации не пригоден. После установки гасителя проверить наличие зазора между гасителем и противовесом.
ПРИВОД ОТБОРА МОЩНОСТИ — передний, осуществляется с носка коленчатого ватта через фланец 15 отбора мощности, прикрепленный к носку коленчатого вала 6 восемью болтами 11. Центрирование фланца относительно коленчатого вала осуществляется по отверстию во фланце гасителя. Крутящий момент от фланца отбора мощности передается на шкив 1 электромагнитной муфты и далее через ременную передачу на привод генератора и водяного насоса. Шкив закреплен на фланце отбора мощности шестью специальными болтами 14 размером М12х1,25×30. На торце шкива выполнено шесть отверстий диаметром 14 мм.
Отверстия предназначены для проворачивания коленчатого вала при регулировании зазоров клапанов.
Рисунок 29 — Установка гасителя крутильных колебаний, фланца отбора мощности и шкива:1 — шкив; 2. 13 — болты крепления крышки блока цилиндров; 3 — пробка заправочного отверстия; 4 — силиконовая жидкость; 5 — фторопластовый подшипник; 6 — коленчатый вал; 7 — блок цилиндров; 8 — корпус гасителя крутильных колебаний; 9 — маховик гасителя; 10 — крышка; 11 — болт крепления гасителя; 12 — передняя крышка блока; 14 — болты крепления шкива; 15 — фланец отбора мощности; 16 — манжета
Рисунок 30 — Механизм газораспределения:1 — головка цилиндра; 2 — втулка направляющая; 3, 7, 13 — шайбы; 4, 5 — пружины клапана; 6 — манжета клапана; 8 — болт крепления головки; 9 — тарелка пружин; 10 — втулка тарелки пружин; 11 — сухарь клапана; 12 — болт крепления крышки; 14 — шайба виброизоляционная; 15 — крышка головки цилиндра; 16 — коромысло с регулировочным винтом; 17 — стойка коромысел; 18, 22 — прокладки; 19 — штанга; 20 — ввертыш крепления впускного коллектора; 21 — ввертыш крепления водяной трубы; 23 — толкатель; 24 — распред. вал; 25 — выпускной клапан; 26 — седло выпускное; 27 — гильза цилиндра; 28 — кольцо газового стыка; 29 — блок цилиндров; А — тепловой зазор
МЕХАНИЗМ ГАЗОРАСПРЕДЕЛЕНИЯ (см. рисунок 30)предназначен для обеспечения впуска в цилиндры свежего воздушного заряда и выпуска из них отработавших газов. Впускные и выпускные клапаны открываются и закрываются в определенных положениях поршня, что обеспечивается совмещением меток на зубчатых колесах привода агрегатов при их монтаже. Механизм газораспределения — верхнеклапанный, с нижним расположением распределительного вала. Кулачки распределительного вала 24 в соответствии с фазами газораспределения приводят в действие толкатели 23.
Штанги 19 сообщают качательное движение коромыслам 16, а они, преодолевая сопротивление пружин 4 и 5, открывают клапан 25. Закрываются клапаны под действием силы сжатия пружин.
РАСПРЕДЕЛИТЕЛЬНЫЙ ВАЛ (см. рисунок 31) — стальной (740.21-1006015 — из стали 45, 740.21-1006015-01 — из стали 18ХГТ). Кулачки и опорные шейки вала подвергнуты термообработке ТВЧ. Вал устанавливается в развале блока цилиндров на пяти подшипниках скольжения, представляющих собой стальные втулки, залитые антифрикционным сплавом.
На задний конец распределительного вала напрессована прямозубая шестерня 4.
Привод распределительного вала осуществляется от шестерни коленчатого вала через промежуточные шестерни.
Для обеспечения заданных фаз газораспределения шестерни при сборке устанавливаются по меткам «О», «Е» и рискам, выбитым на торцах (см. раздел «Привод агрегатов»).
Шестерни — стальные, штампованные, термообработанные, со шлифованными зубьями. От осевого перемещения вал фиксируется корпусом 2 подшипника задней опоры, который крепится к блоку цилиндров тремя болтами.
Маркировка распределительных валов 740.21-1006015, 740.21-1006015-01 выполнена ударным способом на торце его носка.
Внимание. Установка распределительных валов с другой маркировкой не допускается.
КЛАПАНЫ 25 (см. рисунок 30 — Механизм газораспределения) выполнены из жаропрочной стали. Угол рабочей фаски клапанов 90°.
Диаметр тарелки впускного клапана 51,6 мм, выпускного — 46,6 мм, высота подъема впускного клапана — 14,2 мм, выпускного — 13,7 мм. Геометрия тарелок впускных и выпускных клапанов обеспечивают соответствующие газодинамические параметры впуска-выпуска газов. Клапаны перемещаются в направляющих втулках изготовленных из металлокерамики. Для предотвращения попадания масла в цилиндры и снижения его расхода на «угар» на направляющих клапанов устанавливаются резиновые уплотнительные манжеты.
ТОЛКАТЕЛИ 23 — тарельчатого типа с профилированной направляющей частью, изготовлены из стали с последующей наплавкой поверхности тарелки отбеленным чугуном. Толкатель подвергнут химико-термической обработке.
ШТАНГИ 19 толкателей — стальные, пустотелые с запрессованными наконечниками.
КОРОМЫСЛА 16 клапанов — стальные, штампованные, представляют собой двуплечий рычаг, у которого отношение большего плеча к меньшему составляет 1,55. Коромысла впускного и выпускного клапанов устанавливаются на общей стойке и фиксируются в осевом направлении пружинным фиксатором.
СТОЙКА 17 коромысел — чугунная, цапфы которой подвергнуты термической обработке ТВЧ.
ПРУЖИНЫ 4 и 5 клапанов — винтовые, устанавливаются по две на каждый клапан. Пружины имеют различные направления навивки.
Диаметр проволоки наружной пружины 4,8 мм, внутренний — 3,5 мм. Предварительно устанавливаемое усилие пружин 355 Н (35,5 кге), суммарное рабочее — 821 Н (82,1 кгс).
Порядок регулирования зазоров между носиками коромысел и клапанами описан в разделе «Техническое обслуживание».
ГОЛОВКИ ЦИЛИНДРОВ 1 — отдельные на каждый цилиндр, изготовлены из алюминиевого сплава. Головка цилиндра для охлаждения имеет полость, сообщающуюся с полостью охлаждения блока.
Каждая головка цилиндра устанавливается на два установочных штифта, запрессованных в блок цилиндров и крепится четырьмя болтами из легированной стали. Один из установочных штифтов одновременно служит втулкой для подачи масла на смазку коромысел клапанов. Втулка уплотнена резиновыми кольцами.
Окна впускного и выпускного каналов расположены на противоположных сторонах головки цилиндров. Впускной канал имеет тангенциальный профиль для обеспечения оптимального вращательного движения воздушного заряда, определяющего параметры рабочего процесса двигателя и токсичность отработавших газов.
В головку запрессованы чугунные седла и металлокерамические направляющие втулки клапанов. Выпускные седла и клапаны профилированы для обеспечения меньшего сопротивления выпуску отработавших газов.
Стык «головка цилиндров-гильза” (газовый стык) — беспрокладочный (см. рисунок 32 — Газовый стык).В расточенную канавку на нижней плоскости головки запрессовано стальное уплотнительное кольцо 3, посредством которого головка цилиндра устанавливается на бурт гильзы. Герметичность уплотнения обеспечивается высокой точностью обработки сопрягаемых поверхностей уплотнительного кольца 3 и гильзы 5 цилиндра.
Рисунок 32 — Газовый стык:1 — головка цилиндра; 2 — кольцо уплотнительное перепуска охлаждающей жидкости; 3 — кольцо газового стыка; 4 — прокладка-заполнитель; 5 — гильза цилиндра; 6 — кольцо уплотнительное; 7 — прокладка уплотнительная; 8 — блок цилиндров; 9 — экран
Свинцовистое покрытие на поверхности кольца газового стыка дополнительно повышает герметичность за счет компенсации микронеровностей уплотняемых поверхностей.
Для уменьшения вредных объемов в газовом стыке установлена разового применения фторопластовая прокладка-заполнитель 4, которая фиксируется на кольце газового стыка за счет обратного конуса и посадки ее с натягом по выступающему пояску.
Применение прокладки-заполнителя снижает удельный расход топлива и дымность отработавших газов. Для уплотнения перепускных каналов охлаждающей жидкости в отверстия днища головки установлены уплотнительные кольца 2 из силиконовой резины.
Пространство между головкой и блоком, отверстия стока моторного масла и штанговые отверстия уплотнены прокладкой 7 головки цилиндра из термостойкой резины. На прокладке дополнительно выполнены уплотнительные бурт втулки подачи масла и канавка слива масла в штанговые отверстия.
Клапанный механизм закрыт алюминиевой крышкой 15 (см. рисунок 30 — Механизм газораспределения).Для шумоизоляции и уплотнения стыка “крышка-головка цилиндров” применены резиновая уплотнительная прокладка 18 и виброизоляционная шайба 14.
Периодичность и порядок регулирования тепловых зазоров между клапанами и коромыслами приведены в разделе «Техническое обслуживание двигателя» настоящего Руководства.
Маркировка головки цилиндра 740.30-1003014 отлита на боковой поверхности бобышки второго болта крепления головки.
Внимание. Установка головок цилиндров с другой маркировкой не допускается.
Кривошипно-шатунный и газораспределительный механизмы Картер двигателя (рис. 5) туннельного типа, отлит яз магниевого сплава МЛ-5. Средняя опора коленчатого вала разъемная, из двух половин, крепится к картеру коленчатого вала стяжным болтом 11 (рис. 6). Передний и задний коренные подшипники коленчатого вала неразъемные. Задний 9 (см. рис. 5) запрессован непосредственно в стенку картера и фиксируется стопором 10, а передний 9 (см. ![]() Цилиндры с оребренной наружной поверхностью отлиты из чугуна, взаимозаменяемы. Диаметр цилиндра 72 мм. Для обеспечения монтажного зазора между поршнем и цилиндром в пределах 0,05. . .0,07 мм цилиндры по диаметру сортируются на три размерные группы (см. прил. 2). Поршни изготовлены из алюминиевого сплава, луженые, имеют вогнутое днище. На головке поршня проточены канавки под поршневые кольца. Поршни, как и цилиндры, разбиты на размерные группы (см. прил. 2). Стрелка для правильного расположения смещения оси поршневого пальца при монтаже наносится на наружной поверхности днища поршня. Направление стрелки при монтаже в сторону шестерен газораспределения для всех поршней. По диаметру отверстия под палец поршни сортируются на четыре размерные группы. Поршневые пальцы —стальные, плавающие, закаленные и полированные. ![]() При сборке палец, поршень и шатун комплектуют из деталей только одной размерной группы. Этим обеспечивается натяг между пальцем и поршнем в пределах от нуля до 0,005 мм и зазор между пальцем и шатуном 0,002. . .0,007 мм (при температуре 20 °С). Поршневые кольца (рис.7) по три на каждом поршне, два компрессионных из специального чугуна. Верхнее компрессионное кольцо 1 хромированное, с тупыми кромками, нижнее 2 — фосфатированное с острыми кромками. На внутренней цилиндрической поверхности компрессионных колец выполнена прямоугольная фаска. При установке на поршень кольца устанавливаются фаской вверх. Маслосъемное кольцо стальное, состоит из четырех элементов, двух стальных дисков 3, осевого 4 и радиального 5 расширителей. Шатуны стальные, кованые, двутаврового сечения (рис. ![]() Нижняя головка шатуна разъемная с тонкостенными взаимозаменяемыми вкладышами. Крышка нижней головки шатуна не взаимозаменяема. При сборке крышки со стержнем шатуна цифры, указывающие номер цилиндра, должны располагаться с одной стороны. Гайки шатунных болтов 4 затягиваются усилием 3,2.. .3,6 кгс-м и стопорятся. Стопорение производится стопорными гайками 5 с поворотом их на 1,5. . .2 грани после соприкосновения с основными. Примечание: На ранее выпущенных двигателях стопорение гаек осуществлялось шплинтами. Для совмещения прорезей гаек с отверстиями в болтах допускается подтяжка гаек усилием не более 5,5 кгс-м. Разница в массе шатунов, установленных на двигатель, не должна превышать 10 г. Коленчатый вал трехопорный (рис. 9), литой из высокопрочного чугуна. ![]() При динамической балансировке на шатунные шейки устанавливаются разъемные, круглого сечения, статически отбалансированные противовесы массой 576 ± 2 г каждый. После балансировки на маховик и кожух сцепления наносятся метки их взаимного расположения. При сборке метки необходимо совмещать. Подшипник средней коренной шейки вместе со средней опорой монтируется на коленчатый вал до постановки в картер. Осевой разбег коленчатого вала (0,15.. .0,25 мм) ограничен буртом подшипника 9 (см. рис. 3) передней опоры с одной стороны и упорной шайбой 8 (см. рис.9) коленчатого вала с другой. Головка цилиндров (рис.10) из алюминиевого сплава имеет развитые ребра, взаимозаменяема, общая на два цилиндра. ![]() Для надежного уплотнения при установке бронзовых резьбовых гнезд 4 свечей, седел 2 клапанов, направляющих втулок 16 клапанов, кожухов штанг 15 и маслосливной трубки 6 головку цилиндров нагревают до температуры 200. . .220 ° С. Механизм газораспределения верхнеклапанный приводится в действие от распределительного вала при помощи толкателей, штанг и коромысел. Распределительный вал (рис. 11) двухопорный, стальной. От осевого перемещения фиксируется упором торца ведомой шестерни распределительного вала 20 в торец ведомой шестерни балансирного механизма 17 (см. рис. 3). Шестерня 1 распределительного вала отлита из магниевого сплава МЛ5 и крепится к фланцу распределительного вала тремя стальными заклепками 2 (рис. 11). Для правильной установки фаз газораспределения на шестернях набиты метки О, которые должны быть совмещены (рис. 12). При необходимости проверка фаз газораспределения (рис. 13) производится на собранном непрогретом двигателе при температуре 15. ![]() Четырехцилиндровые V образные двигатели имеют неуравновешенный момент от сил инерции первого порядка. Для уравновешивания момента в конструкции двигателя предусмотрены балансирный механизм (рис. 14) и уравновешивающая масса в виде противовесов коленчатого вала. Вал балансирного механизма 2 расположен внутри распределительного вала. На концах балансирного вала с одной стороны на лысках установлена ведомая 1 шестерня балансирного механизма с противовесом, на другом — противовес 3. Привод балансирного механизма осуществляется от коленчатого вала парой прямозубых шестерен (см. рис. 3) с передаточным отношением 1:1. Осевое перемещение балансирного механизма ограничивается плунжером 19 (см. рис. 3) и распорной пружиной, установленной в крышке распределительных шестерен 21. При установке балансирного механизма необходимо совместить метки О (см. ![]() Толкатели плунжерного типа, литые, чугунные с от беленной поверхностью торцов (рис. 15). Толкатели 1 выпускных клапанов первого и третьего цилиндров (первая пара со стороны вентилятора) имеют четыре отверстия на цилиндрической поверхности: одно —вверху для выема толкателя, второе — в проточке 12 для подвода масла через штанги в головку цилиндров к коромыслам и два внизу для слива масла, стекающего по кожухам штанг толкателей из головки. Вставка 10 этих толкателей имеет центральное и боковое сверления. Все остальные толкатели имеют вставки 9 с боковым сверлением и не имеют проточек по наружному диаметру. Штанги толкателей — дюралюминиевые трубки с напрессованными стальными наконечниками. В наконечниках просверлены отверстия для прохода смазки. Коромысла клапанов (рис. 16) стальные, литые с регулировочным винтом 7 и контргайкой 9. Различают правое 4 и левое 2 коромысла. Валик коромысел клапанов стальной, полый с проточками по наружному диаметру под коромыслами и отверстиями в них для подвода смазки коромысел выпускных клапанов первого и третьего цилиндров и слива масла из коромысел выпускных клапанов второго и четвертого цилиндров. ![]() Клапаны — подвесные, расположены в головке цилиндров. Диаметр впускного клапана 29 мм, а выпускного 25 мм (рис. 17). Угол наклона рабочей фаски 45″ . Рабочие фаски выпускных клапанов имеют жаропрочную наплавку. На стержни выпускных клапанов сверху надеты наконечники 1 высокой твердости, так как выпускные клапаны изготовлены из ненакаляющейся жаропрочной стали. Каждый клапан имеет по одной пружине. Для уменьшения попадания масла в камеру сгорания головок цилиндров через зазоры между стержнями клапанов и направляющими 8 втулками (т. е. для снижения расхода масла на угар) между тарелками 4 и пружинами клапанов 7 установлены стаканы 6. Крышка распределительных шестерен отлита из магниевого сплава МЛ5, фиксируется на картере коленчатого вала двумя штифтами и крепится болтами по контуру. В нижней части крышки смонтирован масляный насос. С правой стороны крышки установлены распределитель и топливный насос. На торцевой части имеется маслозаливная горловина, а в верхней части — направляющий аппарат с генератором в сборе. ![]() |
Форд Фокус 1 двигатель 1.8 устройство, ГРМ, характеристики – Цена нового авто
Форд Фокус 1 двигатель 1.8 литра – тема нашей сегодняшней статьи. Ford Focus первого поколения получил два схожих 16-клапанных бензиновых мотора, это двигатель Zetec-E 1.8i и Zetec-E 2.0i основная разница между моторами состояла в размере цилиндров. У 1.8 литрового диаметр цилиндра 80,6 мм, у 2.0 литрового цилиндр имел номинальный размер — 84,8 мм. Сам блок цилиндров чугунный, а цилиндры вытачиваются непосредственно в блоке. Двигатель 1.8 Форд Фокус для российского рынка имеет мощность 115 л.с. при крутящем моменте 160 Нм и адаптирован к бензину марки АИ-92.
Устройство двигателя Форд Фокус 1 1.8
Двигатель Фокуса 1 1.8 литра — бензиновый, четырехцилиндровый, рядный, шестнадцатиклапанный, с верхним расположением двух распределительных валов. Порядок работы цилиндров: 1 — 3 — 4 — 2 (отсчет от шкива коленчатого вала). Система питания — распределенный впрыск топлива с электронным управлением.
В нижней части блока выполнены опоры пяти коренных подшипников скольжения коленчатого вала со съемными крышками, которые крепятся к блоку болтами. Опоры обрабатываются в сборе с крышками, поэтому крышки не взаимозаменяемы. В верхних частях опор (в постелях блока) имеются выходные отверстия масляных каналов. На двигателе рабочим объемом 2,0 л, кроме того, в опорах выполнены сквозные отверстия, в которые запрессованы форсунки с шариковыми клапанами. Через форсунки масло разбрызгивается на днище поршня и стенку цилиндра.
На боковых стенках третьей (средней) опоры имеются проточки для двух упорных полуколец, препятствующих осевому смещению коленчатого вала и выполненных заодно с вкладышем коренного подшипника. Верхние вкладыши коренных подшипников (устанавливаемые в постели блока) двигателя объемом 1,8 л выполнены с канавками на внутренних поверхностях, а двигателя объемом 2,0 л — со сквозными прорезями. По прорези масло из выходного отверстия масляного канала поступает к форсунке с шариковым клапаном. Нижние вкладыши коренных подшипников (в постелях крышек) без канавок и прорезей.
Коленчатый вал Фокус 1.8 выполнен из высокопрочного чугуна, снабжен противовесами, отлитыми заодно с валом. На переднем конце коленчатого вала устанавливаются зубчатый шкив привода газораспределительного механизма и шкив привода вспомогательных агрегатов. От проворачивания шкивы удерживает шпонка, установленная в пазу вала. К заднему фланцу коленчатого вала шестью болтами крепится маховик. Для подачи масла от коренных шеек вала к шатунным в вале просверлены каналы.
Шатуны — стальные, двутаврового сечения. Нижними разъемными головками шатуны соединены с коленчатым валом. Шатуны обрабатываются вместе с крышками. Чтобы при сборке их не перепутать, на боковых поверхностях шатуна и крышки нанесен порядковый номер цилиндра. В верхнюю головку шатуна запрессован поршневой палец.
Поршневой палец — стальной, трубчатого сечения, свободно вращается в бобышках поршня.
Поршень — из алюминиевого сплава с короткой юбкой. В верхней части поршня проточены три канавки под поршневые кольца. Канавка маслосъемного кольца имеет шесть сверлений для отвода масла, собранного кольцом со стенок цилиндров. Два сверления(из шести) подводят масло к поршневому пальцу. При сборке двигателя необходимо обеспечить расчетный зазор между поршнями и цилиндрами. Для этого после механической обработки блоки цилиндров и поршни сортируются потрем размерным группам. Ремонтные группы не предусмотрены.
Головка блока цилиндров двигателя Форд Фокус 1 1.8
Головка блока цилиндров Ford Focus 1.8 литра из алюминиевого сплава. Она центрируется на блоке на двух втулках и крепится десятью винтами. Между блоком и головкой установлена безусадочная металлоармированная прокладка. В верхней части головки блока цилиндров расположены по пять опор (подшипников скольжения) двух распределительных валов. Ближние к шкивам опоры удерживают распределительные валы от осевого смещения. Опоры разъемные. Нижние части опор выполнены заодно с головкой блока цилиндров, а верхние (крышки) — крепятся к головке винтами. Отверстия опор обрабатываются в сборе с крышками, поэтому крышки не взаимозаменяемы и на каждой крышке имеется порядковый номер. Распределительные валы — литые, чугунные. Они приводятся во вращение зубчатым ремнем от шкива коленчатого вала. Натяжение ремня обеспечивается пружиной натяжного ролика.
Седла и направляющие втулки клапанов изготовлены из специальных сплавов и запрессованы в головку блока цилиндров. Клапаны — стальные, расположены в два ряда и приводятся в действие распределительными валами через толкатели и шайбы. С помощью шайб регулируются тепловые зазоры в приводе клапанов. Пружина клапана — конусная, широким основанием упирается в нижнюю тарелку, выполненную заодно с маспоотражательным колпачком. Газораспределительный механизм закрыт пластмассовой крышкой головки блока цилиндров. В ней установлен маслоотделитель системы вентиляции картера. Смазка двигателя комбинированная: под давлением смазываются коренные и шатунные подшипники коленчатого вала, опоры распределительных валов, остальные детали смазываются разбрызгиванием.
Масляный насос двигателя Форд Фокус 1 1.8
Масляный насос — шестеренчатый, с шестернями внутреннего зацепления и редукционным клапаном. Корпус насоса прикреплен к блоку цилиндров шестью болтами. С внутренней стороны насос закрыт крышкой. Ведущая шестерня (меньшего диаметра) установлена на шейке коленчатого вала и фиксируется от проворачивания на ней двумя лысками. Снизу к блоку цилиндров через резинометаллическую прокладку болтами прикреплен картер из алюминиевого сплава, к которому крепится стальной штампованный поддон. Уплотнительная прокладка у поддона отсутствует — его устанавливают на герметик. В поддоне выполнено отверстие с резьбовой пробкой для слива моторного масла.
Привод ГРМ двигателя Форд Фокус 1 1.8
1.8 литровый 16 клапанный движок, как и его 2-литровая модификация имеют ремень в приводе ГРМ. Замену ремня необходимо проводить раз в 60 000 км пробега. В случае обрыва ремня гнет клапана! Имейте это в виду. К сожалению никаких меток на шкивах распредвалов вы не найдете. При замене ремня необходимо совместить метку ВМТ коленвала и зафиксировать шкивы распредвала от проворачивания. Для этого имеются специальные прорези в торцах распределительных валов, которые должны быть параллельны привалочной плоскости головки блока цилиндров. Необходимо подобрать подходящую пластину и вставить в прорези распредвалов, тем самым получится зафиксировать распредвалы от проворачивания. Что бы не проворачивался коленвал необходимо будет вкрутить специальный болт в технологическое отверстие блока цилиндров со стороны радиатора. После полной фиксации можно будет приступать к замене ремня ГРМ Форд Фокус 1 1.8 литра. Размеры болта для фиксации коленвала далее на фото.
Технические характеристики двигателя Форд Фокус 1 1.8
- Рабочий объем – 1796 см3
- Количество цилиндров – 4
- Количество клапанов – 16
- Диаметр цилиндра – 80,6 мм
- Ход поршня – 88 мм
- Привод ГРМ – ремень
- Мощность л.
с.(кВт) – 115 (85) при 5500 об. в мин.
- Крутящий момент – 160 Нм при 4400 об. в мин.
- Максимальная скорость – 185 км/ч
- Разгон до первой сотни – 10.3 секунд
- Тип топлива – бензин АИ-92
- Степень сжатия – 10
- Расход топлива в смешанном цикле – 9 литров
При смене масла с заменой фильтра уходит примерно 4,25 литра. При замене масла без учета фильтра уходит 3,75 литра.
Осевая вибрация – обзор
Осевая вибрация
Расчет характеристик осевой вибрации необходим только для низкоскоростных двухтактных двигателей. Когда кривошип нагружается давлением газа через шатунный механизм, плечи кривошипа отклоняются в осевом направлении коленчатого вала, возбуждая осевые колебания. Эти вибрации могут передаваться на корпус корабля через упорный подшипник.
Как правило, поясняет MAN Diesel, интерес представляют только осевые вибрации нулевого узла.Таким образом, необходимо учитывать влияние дополнительных изгибающих напряжений в коленчатом валу и возможные вибрации конструкции корабля из-за силы реакции в упорном подшипнике.
На все двигатели MC устанавливается соответствующий осевой демпфер для сведения к минимуму воздействия осевых вибраций (рис. 1.18). Для некоторых типов двигателей в пяти- и шестицилиндровом исполнении с ВОМ, установленным в передней части, требуется монитор осевой вибрации для сигнализации и замедления. Однако для самого коленчатого вала такой демпфер необходим только для двигателей с большим числом цилиндров.
Рисунок 1.18. Установка предыдущих и улучшенных гасителей осевых колебаний для двигателей MAN B&W с диаметром цилиндра 500–900 мм MC
Исследование осевой вибрации (иногда называемой продольной вибрацией) можно ограничить главным валом, охватывающим коленчатый вал, промежуточный вал и карданный вал, поскольку осевое возбуждение не передается через редукторы ВОМ на ответвления валов. Система колебаний может быть построена в эквивалентных постоянных массах и жесткостях, как и при крутильных колебаниях.
Массы определяются вращающимися компонентами в целом и могут быть очень точно рассчитаны с помощью программ САПР. Осевые жесткости коленчатого вала выводятся, как и значения на кручение, из эмпирической формулы и, при необходимости, корректируются путем сравнения измеренных и рассчитанных осевых собственных частот. В качестве альтернативы осевая жесткость может быть рассчитана непосредственно методом конечных элементов. Демпфирование коленчатого вала выводится из измерений осевой вибрации.
Преобладающий порядок осевой вибрации соответствует числу цилиндров для двигателей с числом цилиндров менее семи. Для двигателей с более чем шестью цилиндрами преобладающий порядок равен половине номеров цилиндров. Для двигателей с нечетным числом цилиндров преобладающими являются в основном два порядка, ближайшие к половине числа цилиндров.
Когда компания MAN Diesel представила серию MAN B&W MC, гаситель осевых колебаний входил в стандартную комплектацию только для двигателей с шестью и более цилиндрами.Это было необходимо, потому что в противном случае резонанс с порядком, соответствующим номеру цилиндра, вызвал бы слишком высокие напряжения в кривошипах.
Ранее был зарегистрирован случай, когда пятицилиндровый двигатель L50MC, установленный на цистерне для сжиженного нефтяного газа, зафиксировал чрезмерную осевую вибрацию коленчатого вала во время пробного рейса. Более тщательный анализ показал, что коленчатый вал не находился в резонансе и что ситуация была вызвана связанным явлением. Вибрация коленчатого вала передавалась на раму двигателя и двойное дно, которые, в свою очередь, передавали энергию вибрации обратно на коленчатый вал.В результате и весь двигатель, и надстройка страдали от сильной продольной вибрации.
Компания MAN Diesel решила подойти к проблеме с двух сторон. На коленчатый вал был модернизирован гаситель осевых колебаний, а на задний конец двигателя была установлена верхняя распорка в продольном направлении. Обе контрмеры повлияли на поведение вибрации коленчатого вала, рамы двигателя и надстройки.
Один лишь гаситель осевых колебаний фактически устранил проблемы; и одна только продольная верхняя распорка снизила уровень вибрации в рубке до значений ниже рекомендованных ISO. При действии обеих контрмер продольная распорка сверху имела незначительное влияние. Инцидент вместе с опытом некоторых других пятицилиндровых моделей побудил MAN Diesel установить гасители осевых колебаний на двигатели со всеми номерами цилиндров, хотя для двигателей с меньшим количеством цилиндров такая мера предосторожности может не потребоваться.
Патент США на устройство для управления углом сдвига фаз между первым и вторым коленчатыми валами. Патент (Патент № 6,763,787, выдан 20 июля 2004 г.)
ПЕРЕКРЕСТНАЯ ССЫЛКА НА РОДСТВЕННЫЕ ПРИЛОЖЕНИЯНастоящая заявка является продолжением международной заявки №PCT/SE01/01233, поданная 1 июня 2001 г., в настоящее время отмененная, которая была опубликована на английском языке в соответствии со статьей 21(2) Договора о патентной кооперации и испрашивает приоритет по отношению к заявке Швеции № 0002088-3, поданной 5 июня. , 2000. Обе заявки включены сюда посредством ссылки во всей их полноте.
ПРЕДПОСЫЛКИ ИЗОБРЕТЕНИЯ 1. Область техники
Настоящее изобретение относится к устройству для управления углом сдвига фаз между первым и вторым коленчатыми валами двигателя внутреннего сгорания типа, включающего по меньшей мере один первичный цилиндр, сообщающийся по меньшей мере с одним вторичным цилиндром.Обычно имеется первичный поршень, который подвижно расположен в каждом первичном цилиндре и соединен с первым коленчатым валом. В каждом вторичном цилиндре подвижно расположен вторичный поршень, соединенный со вторым коленчатым валом. Первый и второй коленчатые валы обычно соединены друг с другом посредством трансмиссии и средства или механизма для получения управления фазовым сдвигом. Для управления фазовым углом также предусмотрен удлинитель коленчатого вала, который неподвижно соединен против относительного вращения с одним из коленчатых валов и соединен с возможностью вращения со вторым из коленчатых валов.
2. Предыстория
В двигателях внутреннего сгорания поршневого типа, например двигателях Отто и дизелях с одним или несколькими цилиндрами с совершающими возвратно-поступательное движение поршнями, топливно-воздушная смесь сжимается в камере сгорания, где воспламеняется и сгорает при нахождении поршня в самое верхнее положение.
Сжатие топливно-воздушной смеси определяется степенью сжатия конкретного рассматриваемого двигателя, параметром, который определяется как соотношение между объемом в цилиндре, когда поршень находится в самом нижнем и самом верхнем положениях.Современные двигатели Otto обычно имеют степень сжатия около 10:1 (сжатие на фиг. 10), в то время как двигатели с наддувом, например двигатели с турбонаддувом, имеют более низкую степень сжатия, а дизельные двигатели имеют значительно более высокую степень сжатия. Степень сжатия двигателя влияет на сгорание топливно-воздушной смеси.
Высокая степень сжатия способствует эффективному сгоранию, что, в свою очередь, способствует высокой эффективности и низкому расходу топлива. В то же время, однако, необходимо использовать высокооктановое топливо, особенно при высоких нагрузках двигателя, чтобы избежать неконтролируемого сгорания.С учетом этого становится очевидным, что желательно иметь возможность изменять степень сжатия во время работы двигателя в зависимости от качества топлива и нагрузки двигателя.
Патент США. US 5638777 раскрывает двигатель внутреннего сгорания с переменной степенью сжатия. Двигатель имеет ряд первичных цилиндров и соответствующее количество вторичных цилиндров, каждый из которых сообщается с соответствующим первичным цилиндром. В каждом первичном цилиндре первичный поршень соединен с первым коленчатым валом и предназначен для выполнения возвратно-поступательного движения.Соответственно, в каждом вторичном цилиндре имеется вторичный поршень, соединенный со вторым коленчатым валом, при этом вторичный поршень также выполнен с возможностью совершать возвратно-поступательное движение. Между первым и вторым коленчатыми валами расположены зубчатая передача и устройство фазового сдвига между валами с целью получения степени сжатия, зависящей от текущей нагрузки двигателя. Устройство содержит ведущий вал, неподвижно соединенный со вторым коленчатым валом и снабженный спиралевидными шлицами, концентрически расположенными внутри наружного кожуха.На внешнем корпусе размещено первое зубчатое колесо, предназначенное для взаимодействия со вторым зубчатым колесом, расположенным на первом коленчатом валу и имеющее внутренние спиралевидные шлицы. Между наружным корпусом и приводным валом расположен подвижный трубный элемент, огибающая поверхность которого снабжена спиралевидными шлицами, предназначенными для взаимодействия с внутренними спиралевидными шлицами внешнего корпуса. Кроме того, трубный элемент снабжен внутренними спиралевидными шлицами, взаимодействующими со спиралевидными шлицами, расположенными на приводном валу.В случае осевого смещения трубчатого элемента, например, в случае гидравлической системы управления, получается фазовый сдвиг между первыми зубчатыми колесами и приводным валом, а тем самым также между первым и вторым коленчатыми валами.
Хотя устройство, представленное в патенте США No. № 5638777 позволяет хорошо контролировать сдвиг фаз между коленчатыми валами, но имеет определенные недостатки. Одним из недостатков является относительно высокая стоимость его изготовления, так как он относительно сложен по своей конструкции, особенно это касается подвижного элемента трубы, снабженного как на огибающей поверхности, так и внутри спиралевидными шлицами. Еще одним недостатком является то, что элемент трубы, включая гидравлическую систему управления, требует относительно большого вмещающего пространства в его осевом направлении. Это затрудняет его установку в автомобилях с боковыми многоцилиндровыми двигателями. Кроме того, сборка/разборка этого устройства относительно сложна в осуществлении.
Целью настоящего изобретения является создание устройства для управления углом сдвига фаз между первым и вторым коленчатыми валами двигателя внутреннего сгорания, которое по сравнению с предыдущей технологией является более экономичным в производстве.
В примерном варианте осуществления такое устройство включает по меньшей мере один первичный цилиндр, который сообщается по меньшей мере с одним вторичным цилиндром и имеет первичный поршень, подвижно расположенный в этом первичном цилиндре. Первичный поршень соединен с первым коленчатым валом, а в каждом вторичном цилиндре установлен подвижно вторичный поршень, соединенный со вторым коленчатым валом. Первый и второй коленчатые валы соединены друг с другом посредством трансмиссии, и устройство дополнительно включает в себя средство для получения управления фазовым сдвигом и удлинитель коленчатого вала, предназначенный для такого фазового управления.Удлинитель неподвижно соединен с одним из коленчатых валов и закреплен с возможностью вращения с другим коленчатым валом. За счет того, что удлинение коленчатого вала расположено со смещением относительно одного из коленчатых валов, получается механическая поверхность раздела, на которой можно осуществлять фазовый сдвиг без введения дополнительных компонентов.
В соответствии с предпочтительным вариантом средство или устройство согласно изобретению выполнено с возможностью осевого смещения конца коленчатого вала, в результате чего смещается фазовый угол.Средство или устройство предпочтительно состоит из гидравлического поршня, расположенного в корпусе для воздействия на конец коленчатого вала, по меньшей мере, в одном направлении. Это обеспечивает быстрый фазовый сдвиг с хорошей точностью при высоких нагрузках двигателя.
В соответствии с другим предпочтительным вариантом осуществления гидравлический поршень также предназначен для воздействия на выдвижение коленчатого вала во втором направлении, чтобы обеспечить оптимальное управление фазовым углом между первым и вторым коленчатыми валами, например, в случае быстрого изменения нагрузки двигателя.
Поскольку гидравлический поршень в соответствии с настоящим изобретением не вращается относительно корпуса, между поршнем и корпусом достигается упрощенное масляное уплотнение. Кроме того, это создает благоприятные условия для получения простого и надежного устройства подачи масла к поршню.
В другом предпочтительном варианте осуществления изобретения удлинение коленчатого вала на одном конце снабжено шлицами, которые обеспечивают подвижное соединение, зафиксированное от вращения, с одним из коленчатых валов.Удлинитель коленчатого вала дополнительно на другом конце снабжен канавкой, предпочтительно трапециевидной канавкой, для вращательного соединения.
Благодаря выполнению удлинения коленчатого вала в соответствии с настоящим изобретением с фланцем между снабженной шлицами частью и частью с канавкой, на которую воздействует гидравлический поршень, обеспечивается компактное и короткое в осевом направлении устройство для управления фазовым углом; атрибут, который чрезвычайно выгоден в большинстве автомобилей.
Другие преимущества и цели изобретения можно найти в прилагаемой формуле изобретения и в описании ниже.
КРАТКОЕ ОПИСАНИЕ ЧЕРТЕЖЕЙДалее изобретение будет описано в связи с примерами предпочтительных вариантов осуществления и в отношении прилагаемых фигур, на которых:
РИС. 1 показан вид в перспективе, частично в виде точек, двигателя внутреннего сгорания, снабженного устройством для управления углом сдвига фаз между коленчатыми валами согласно настоящему изобретению; и
РИС.2 показан вид сбоку в частичном разрезе предпочтительного варианта устройства для регулирования такого фазового угла между коленчатыми валами.
ПОДРОБНОЕ ОПИСАНИЕРИС. 1 показан вид в перспективе с частичным разрезом двигателя внутреннего сгорания 1 с блоком цилиндров 2 с первичными цилиндрами 3а, 3b, 3с, 3d, сообщающимися соответственно через каналы 4а, 4b, 4с, 4d с вторичными цилиндрами 5а, 5b, 5c, 5d, расположенные в головке блока цилиндров 6 двигателя внутреннего сгорания 1.В каждом первичном цилиндре первичные поршни 7а, 7b, 7с, 7d расположены возвратно-поступательно и посредством первичных шатунов 8а, 8b, 8с, 8d соединены с первым коленчатым валом 9. В каждом вторичном цилиндре 5а, 5b, 5с, 5d вторичные поршни 10а, 10b, 10с, 10d расположены с возвратно-поступательным движением и соединены со вторым коленчатым валом 12 посредством вторичных шатунов 11а, 11b, 11с, 11d. Первый коленчатый вал 9 установлен в подшипниках в блоке цилиндров 2, а второй коленчатый вал 12 установлен в подшипниках в головке блока цилиндров 6.Коленчатые валы 9, 12 соединены друг с другом посредством трансмиссии 13, которая включает в себя зубчатый приводной ремень 14, проходящий по первому 15 и второму 16 ведущим колесам. Размер ведущих колес 15, 16 выбран таким образом, чтобы второй коленчатый вал 12 вращался с половиной частоты вращения первого коленчатого вала 9. Вторые ведущие колеса 16 частично охватывают корпус 18 устройства фазовращателя 17, расположенного на головка блока цилиндров 6.
Со ссылкой на фиг. 2 будет описан предпочтительный вариант осуществления средства или устройства для управления фазовым сдвигом 17.В показанном варианте осуществления второе ведущее колесо 16 установлено в корпусе 18 с помощью шарикоподшипников 19, предпочтительно с двухрядным угловым контактным слоем. Ведущее колесо 16 дополнительно снабжено канавкой 20, взаимодействующей с соответствующей канавкой 22 на выступе 21 коленчатого вала. под углом 120 градусов при осевом смещении конца коленчатого вала 21 на 20 мм.Удлинитель 21 коленчатого вала, кроме того, имеет участок, снабженный шлицами 23, которые взаимодействуют с соответствующим участком 24, снабженным шлицами, на втором коленчатом валу 12 для соединения, которое выполнено с возможностью смещения и зафиксировано от вращения. Ось вращения коленчатого вала 21 при этом совпадает с осью вращения второго коленчатого вала 12.
Удлинитель 21 коленчатого вала предпочтительно изготавливают из стали и на рифленой части 22 и части 23 снабжены шлицами, покрытыми слоем, состоящим из химически осажденного никеля, который пропитан и покрыт фторопластом и термически закаленные.Таким образом достигается низкое трение, а это означает, что для управления фазовым сдвигом потребуются меньшие усилия. Покрытия такого типа имеются в продаже под торговой маркой Nedox® и ранее применялись, среди прочего, в качестве поверхностных покрытий на зубчатых колесах и на формовочных инструментах для пластмассовых изделий с малыми углами наклона.
Устройство 17 дополнительно включает в себя средство или механизм 25 для выполнения смещения удлинителя 21 коленчатого вала. Для этой цели удлинитель 21 коленчатого вала, таким образом, снабжен фланцем 26 между канавкой 22 и шлицевой частью 23, на которую гидравлический поршень 27, расположенный с возможностью перемещения в корпусе 18, выполнен с возможностью работы.Между фланцем 26 и гидравлическим поршнем 27 расположены подшипники 28, 29 игольчатого типа, выполненные с возможностью воспринимать осевые усилия, возникающие в результате крутящего момента, передаваемого на пазовые участки 20, 22. Поскольку гидравлический поршень 27 окружает удлинение 21 коленчатого вала, конструкция 17 становится компактной и короткой в осевом направлении, что чрезвычайно выгодно для автомобилей.
Кроме того, гидравлический поршень 27 на окружающей его поверхности имеет упор 30, который делит камеру на первую 31 и вторую 32 подкамеры, каждая из которых сообщается с первой 33 и второй 34 масляными трубками соответственно.Маслопроводы 33, 34 соединены с гидрораспределителем, который в зависимости от системы управления двигателем 1 регулирует подачу масла в ту или иную подкамеру 31, 32 и тем самым вызывает фазовый сдвиг. между первым 9 и вторым 12 коленчатыми валами. При использовании части масла, которое обычно находится под давлением насоса сервоуправления в двигателе 1, нет необходимости в дополнительном масляном насосе.
Корпус 18 дополнительно снабжен уплотнительными кольцами 35, 36, которые расположены так, чтобы контактировать с поршнем 27, по одному с каждой стороны упора 30, и выполнять функцию масляных уплотнений для подкамер 31, 32. .По внешнему периметру упора 30 между первой 31 и второй 32 подкамерами расположено соответствующее уплотнительное кольцо для масляного уплотнения. Поскольку конец 21 коленчатого вала соединен с поршнем 27 через подшипники 28, 29, по крайней мере в принципе крутящий момент не передается на поршень 27, когда конец 21 коленчатого вала вращается. В результате поршень 27 из-за трения между ним и уплотнительными кольцами 35, 36, 37 не будет вращаться с удлинителем 21 коленчатого вала при его вращении, что упрощает масляное уплотнение.
Согласно изложенному выше, функция устройства 17 заключается в следующем: подача масла по трубопроводу 33 в подкамеру 31 приводит к повышению давления в подкамере 31, объем которой ограничивается упором 30, расположенным на поршне 27. Это, в свою очередь, вызывает прижатие поршня 27 в направлении головки цилиндра 6. Поскольку продолжение коленчатого вала 21 через подшипники 28, 29 соединено с поршнем 27 Таким образом, возникает относительное осевое смещение в шлицевом соединении 23, 24 между удлинителем 21 коленчатого вала и коленчатым валом 12.При этом происходит соответствующее относительное осевое смещение между продолжением коленчатого вала 21 и вторым ведущим колесом 16, при этом ведущее колесо 16 вращается в трапециевидных канавках 20, 22, что вызывает фазовый сдвиг между первым 9 и ведущим колесом 16. второй 12 коленвал. Соответствующим образом сдвиг угла фаз в противоположном направлении достигается за счет подачи масла по трубопроводу 34 в подкамеру 32.
Изобретение не ограничивается тем, что было описано выше; следует понимать, что возможны и другие варианты осуществления.Например, электрический двигатель вместо гидравлического поршня может воздействовать на фланец коленчатого вала. Смещение конца коленчатого вала также может происходить относительно катушки, например спиральной катушки, при этом гидравлический поршень или электрический двигатель устроены так, чтобы вызывать смещение только в одном направлении. В соответствии с альтернативным вариантом удлинение коленчатого вала расположено в противоположном направлении, так что шлицевая муфта может быть расположена на втором ведущем колесе, а трапециевидная канавка расположена между продолжением коленчатого вала и вторым коленчатым валом.В еще одном альтернативном варианте устройство управления фазовым углом, в отличие от описанного выше варианта, расположено на первом коленчатом валу. Наконец, удлинение коленчатого вала может быть снабжено вместо использования шлицев другим поперечным сечением, например квадратным поперечным сечением, которое взаимодействует с соответствующим квадратным отверстием на коленчатом валу для получения подвижного соединения, которое фиксируется от вращения.
(PDF) Пример силы изменения тяги из-за связанной крутильной и осевой вибрации на двухтактных тихоходных дизельных двигателях
ICSV24, Лондон, 23–27 июля 2017 г. Рисунок 10: Сила изменения тяги, основанная на измеренном осевом смещении промежуточного вала
Эти фактические расчеты измерения вибрации подтвердили силу изменения тяги из-за влияния сопряженной
крутильных и осевых вибраций на динамическое поведение системы карданного вала
.Однако предполагается, что, учитывая большую длину коленчатого вала двигателя модели А,
, гребной винт не влияет на связанное явление крутильных и осевых колебаний системы гребного вала
. Кроме того, хотя тенденция и величина не сильно отличались между теоретическим и фактическим расчетами измерений, было подтверждено, что осевая вибрация имеет много сложностей в моделях демпфирования и силы возбуждения, а также в модели вибрации, дающей большой анализ.
sis и отклонения измерений.Однако, даже если амплитуда будет увеличиваться, пока активен осевой демпфер
, проблем с защитой коленчатого вала не будет.
5. Выводы
В этой статье динамические характеристики осевой вибрации двигателя 14RT-flex96C мощностью 80 080 кВт
и сверхдлинноходового двигателя 7G80ME мощностью 24 400 кВт были исследованы посредством теоретического анализа и измерений.
1. Несмотря на то, что анализ связанных осевых
колебаний и результаты измерений широко используются, более практические результаты были получены при рассмотрении анализа
крутильных колебаний как значительной вибрационной силы для анализа продольных колебаний в этом
учиться.
2. При измерении осевой вибрации проверяется пиковая амплитуда вибрации, работает ли демпфер осевой вибрации
. Однако необходимо подтвердить изменение силы тяги
, поскольку сила тяги, вызванная крутильными колебаниями, больше по сравнению с простыми продольными колебаниями и оказывает большое влияние на вибрацию корпуса.
3. Для расчета осевой вибрации низкоскоростного двухтактного дизельного двигателя просто применяются прямое моделирование и сила возбуждения.Тем не менее, дополнительные методы моделирования и методы приложения силы возбуждения должны быть дополнительно исследованы
и признаны необходимыми для определения более точных результатов.
ССЫЛКИ
1 Фуджи К. и Танида К. Возбуждающие силы судовых вибраций, вызванные крутильными и продольными колебаниями валопровода
, ICMES’84 (1984).
2 Hylarides S. и Gent van W., Гидродинамические реакции на колебания пропеллера, Trans.I Mar E(C), Vol.91, Conference
, конференция No.4, Paper C37. (1979).
3 Ли, Д. К., Нам, Дж. Г. и Ко, Дж. Ю., Исследование осевой вибрации двухтактного тихоходного дизельного двигателя на дизельной электростанции
, Журнал Корейского общества инженеров по шуму и вибрации, Vol. 11 № 9,
, стр. 398–405 (2001 г.).
Объемный насос в сравнении с центробежным насосом.
При перекачивании жидкостей из одного корпуса в другой при выборе насоса необходимо учитывать несколько факторов.Иногда лучше использовать центробежный насос, а в других случаях предпочтительнее объемный насос. В этом блоге мы кратко рассмотрим, как работают насосы. Затем мы углубимся в различия между двумя насосами и дадим совет, когда какой насос использовать.
Что такое центробежный насос?
Центробежные насосы используются для перекачивания жидкостей путем преобразования энергии вращения, приводимой в действие каким-либо двигателем или двигателем, в энергию, перемещающую жидкость. Жидкость поступает в крыльчатку насоса по оси вращения, где она ускоряется крыльчаткой по направлению к диффузору или шнеку.Жидкости получают как давление, так и скорость, проходя через рабочее колесо.
Что такое объемный насос?
Объемный насос перекачивает жидкости, захватывая фиксированное количество жидкости и нагнетая ее в напорную трубу. Движение запускается двумя или тремя шпинделями, которые движутся в противоположных направлениях друг от друга; перекачивая и тем самым вытесняя жидкость.
В чем разница?
Оба насоса вытесняют жидкости, однако между ними есть некоторые различия.
Механика.
Очевидная разница между ними заключается в том, как они работают. Как показано выше, центробежные насосы сообщают жидкости скорость, в результате чего на выходе возникает давление. Насосы прямого вытеснения захватывают ограниченное количество жидкости и перекачивают ее из всасывающего патрубка в нагнетательный патрубок. Короче говоря, с центробежными насосами создается давление и возникает поток, тогда как с поршневыми насосами создается поток и возникает давление.
Производительность.
В связи с тем, что расход зависит от давления, в центробежных насосах расход изменяется при изменении давления. Поскольку поршневые насосы работают наоборот, их поток соответствует изменению давления. Оба типа насосов способны регулировать поток путем изменения скорости. Скорость потока вращающегося поршневого насоса пропорциональна скорости вращения (коэффициент изменения часто превышает 10:1) и почти не зависит от перепада давления.В отличие от центробежных насосов (диапазон динамического диапазона 3:1), нет необходимости как в многоцелевом применении, так и в насосных агрегатах для конкретных продуктов. Работой можно управлять без обработки жидкости или дросселирования насоса. Для центробежных насосов это необходимо, несмотря на регулируемую скорость.
Вязкость.
Эффективность центробежных насосов снижается при увеличении вязкости. Это связано с потерями на трение внутри насоса. По этой причине эти насосы обычно не используются при вязкости выше 850 сСт.Производительность центробежного насоса снижается уже при вязкости 100 сСт. Напротив, эффективность поршневых насосов увеличивается с увеличением вязкости.
Эффективность.
Пик центробежных насосов при BEP (точка максимальной эффективности). При более высоких или более низких уровнях давления эффективность снижается. В пределах окна 80-110% своего BEP эта помпа адекватна. Для поршневых насосов эффективность увеличивается с увеличением давления.
Условия на входе .
В центробежных насосах необходимо, чтобы жидкости находились в насосе для создания перепада давления. Кроме того, центробежный насос не может обеспечить GVF (объемную долю газа) выше 15 %. Поэтому всасывающий трубопровод и насос должны быть заполнены жидкостью. Сухой насос не будет работать сам по себе. В объемных насосах на входе создается отрицательное давление (всасывание). Насос также необходимо один раз заполнить жидкостью.Однако, в отличие от центробежного насоса, он также может самостоятельно перекачивать большие объемы газа и заливки со значением NPSHr (требуемый чистый положительный напор на всасывании) до 1,8 м. Эта очень хорошая высота всасывания может максимизировать операции по зачистке трубопроводов, при этом она способна выдерживать всасывание увлеченного воздуха и других газов без образования паровых пробок.
Итак, какой насос использовать?
На этот вопрос не так просто ответить, как кажется. Как правило, с увеличением вязкости объемные насосы становятся необходимостью.То же самое касается работы с переменным давлением или при работе с сухим насосом. Однако, чтобы быть на 100% уверенным в том, какой тип насоса использовать, свяжитесь с нашей командой экспертов в KRAL. Расскажите нам о своей области применения, и вместе мы выберем лучший насос для вашего бизнеса.
28.10.2019
Полное руководство по насосам для мойки высокого давления (обновлено видео, чтобы показать вам, как они работают)
Если вы хотите узнать разницу между тремя лучшими типами насосов для мойки высокого давления, вы попали по адресу.
Для каждого насоса мойки высокого давления здесь собрана следующая информация:
- Анимация, показывающая, как работает каждый тип насоса.
- Преимущества и недостатки.
- Различные бренды.
- В каких мойках высокого давления используются какие насосы.
Для мойки под давлением требуется насос, способный создавать высокое давление при малом расходе по сравнению с другими распространенными насосными установками (отстойные насосы требуют высокого расхода при низком давлении).Насос также должен быть легким, компактным и экономичным.
Типы насосов для мойки под давлениемСуществуют две основные группы объемных насосов:
- Поршневые – используются поршни , плунжеры или диафрагмы.
- Вращающийся – Используются винты, шестерни, лопасти или лепестки.
Все насосы для мойки высокого давления относятся к поршневой группе и используют поршни или плунжеры для добавления энергии воде. Есть два основных различия между поршневым и плунжерным насосом.
- В поршневом насосе уплотнение цилиндра прикреплено к поршню, поэтому он перемещается вместе с ним при каждом ходе. Плунжерный насос имеет уплотнение цилиндра в неподвижной точке, через которое поршень проходит при каждом ходе.
- Поршневой насос приводится в действие приводным валом, прикрепленным к наклонной шайбе или качающейся шайбе. Плунжерный насос приводится в движение коленчатым валом.
В литературе по мойкам высокого давления упоминаются 3 типа насосов (все поршневые или плунжерные):
- Колебание (1) и осевые кулачковые (2) насосы приводятся в действие непосредственно приводным валом и используют поршни
- Трехплунжерные (3) насосы имеют привод от распределительного вала/кривошипа и используют плунжеры
Загляните внутрь каждого, чтобы лучше понять различия:
Читайте также: 7 малоизвестных фактов (вы должны знать) о замене масла в водяном насосе мойки высокого давления
Давайте объясним плюсы и минусы каждого типа и более подробно рассмотрим, как каждый из них работает:
Поршневой насос с приводом от приводного вала Насос с качающейся пластинойНасос начального уровня, в котором используется качающаяся пластина, соединенная с приводным валом, чтобы толкать поршни вперед и назад, создавая всасывание, а затем выталкивая воду.
Для каждого поршня предусмотрена большая пружина, позволяющая качающейся пластине прижиматься к ним. Это приводит к тому, что эффективность насоса составляет всего 70%, потому что ему приходится давить на воду и пружины. Вихревые насосы экономически нецелесообразно ремонтировать, поскольку они имеют много сложных деталей, которые трудно добраться до мест, и перед отправкой с завода они запечатываются.
Их срок службы примерно сравним с аксиально-кулачковыми насосами и составляет около 200–400 часов (~3 часа в неделю в течение 2–3 лет).
- Используется в : Некоторые мойки высокого давления ниже 2500 фунтов на квадратный дюйм и с низким расходом (менее 2 галлонов в минуту).
- Плюсы : Нет уплотнений, перемещающихся вперед и назад вместе с поршнем, самовсасывающий, может работать всухую, может создавать высокое давление.
- Минусы : Многие движущиеся части рекламной сложности, низкий поток. Не может заменить экономически. Не так эффективен, как другие насосы.
Читайте также: Как выбрать лучший дренажный насос для ваших нужд
Нажмите кнопку воспроизведения внизу видео, чтобы посмотреть, как оно работает:
Видео с полным исходным кодом
Насос с наклонной шайбой (аксиальный кулачок)Насос промежуточного уровня, который предлагает множество преимуществ по сравнению с вобулятором и способен работать при более высоких значениях PSI и GPM.Вы можете видеть на анимации ниже, что она похожа на колебание, но немного отличается тем, что поршни фактически вращаются вокруг шайбы автомата перекоса. Угол наклона шайбы заставляет поршни двигаться, когда они идут с одной стороны, чтобы всасывать воду, а затем с другой, чтобы выталкивать воду. Операция позволяет увеличить резервуар для масла и подшипники большего размера, что продлевает срок службы. Он вращается вокруг той же оси, что и приводной вал, так как напрямую соединен с ним.
Их срок службы в чем-то сопоставим, но немного лучше, чем у насосов с волатильностью, насчитывающих около 500–800 часов (~2-3 раза больше срока службы вобуляции).
- Используется в : Большинство моек высокого давления с давлением менее 3500 PSI.
- Плюсы : Маленький, легкий и компактный. Можно регулировать поток, регулируя угол наклона шайбы. Самовсасывание. Более длительный срок службы и более эффективный, чем колебания.
- Минусы : Работает на частоте вращения двигателя (читай: на высокой скорости) и не может охлаждаться так же легко, как тройной насос, поскольку цилиндры вращаются. Уплотнение цилиндра находится на головке поршня и перемещается при каждом ходе поршня, вызывая его износ.Вращающаяся масса может вызвать чрезмерную вибрацию, если она не сбалансирована должным образом.
Нажмите кнопку воспроизведения , чтобы заглянуть внутрь и посмотреть, как это работает:
Видео с полным исходным кодом
Фиксированный и переменный рабочий объем — Вы можете отрегулировать угол наклонной шайбы в поршневом насосе с переменным рабочим объемом, чтобы изменить расход. В исправленной версии нельзя.
Изображение является скриншотом из источника видео, указанного вышеТеперь рассмотрим плунжерный насос, привод которого от коленчатого вала.
Плунжерный насос с приводом от коленчатого вала Трехплунжерный насосНасосы профессионального уровня используют тройные насосы, потому что они обеспечивают очень высокое давление и могут работать тысячи часов без какого-либо обслуживания. Вы можете видеть на анимации ниже, что он использует установку, аналогичную двигателю вашего автомобиля (коленчатый вал, шатуны), чтобы управлять поршнями положительного действия, чтобы всасывать воду, а затем выталкивать воду с каждым ходом. Они имеют почти 90% КПД и меньше нагреваются, поскольку работают на меньших оборотах, чем двигатель.В тройном (3-поршневом) плунжерном насосе поршни перемещаются на 120 градусов друг от друга, что обеспечивает равномерный поток на протяжении всего оборота коленчатого вала.
Продолжительность их жизни в основном ограничена только тем, насколько хорошо вы их поддерживаете. Удобный доступ к головке насоса и легко заменяемые клапаны делают ремонт и техническое обслуживание экономичными. (~ 10-кратный срок службы по сравнению с осевым).
- Используется в : Большинство моек высокого давления выше 3000 PSI.
- Плюсы : Очень эффективно.Стационарное уплотнение означает увеличенный срок службы, меньшую подверженность утечкам и гораздо более высокое давление. Более низкая рабочая скорость позволяет ему работать в холодном состоянии, что опять же увеличивает срок службы.
- Минусы : Более высокая стоимость приобретения.
Нажмите кнопку воспроизведения , чтобы посмотреть, как это выглядит в действии:
И крупный план того, как течет вода:
Теперь давайте рассмотрим различные марки насосов для мойки высокого давления.
Марки насосов для мойки высокого давленияЭтот список не является исчерпывающим.Компании, похоже, не любят ставить насос той марки, которую они используют, в свои мойки высокого давления. В своей литературе они предпочитают просто говорить «осевой кулачок» или «тройной поршень». Дайте мне знать, если что-то нужно добавить.
Аннови Ревербери (АР)AR — итальянский производитель насосов. Они также производят электродвигатели под торговой маркой Ravel. Они производят мойки высокого давления под маркой AR Blue Clean, а также продают свои мойки высокого давления под марками Black & Decker и Michelin.
Используется в мойках высокого давления этих марок : AR, BE, насос высокого давления Briggs & Stratton, Campbell Hausfeld, насос высокого давления Craftsman, насос высокого давления Generac, Kranzle, Mi-T-M, Pressure-Pro.
Типы насосов производства AR : качающийся, с осевым кулачком, трехплунжерный.
Насосы CAT«Насос с девятью жизнями» впервые представил насос для мытья под давлением 4 галлона в минуту 700 фунтов на квадратный дюйм в 1968 году.Затем они занялись автомойкой в США и Европе. Сегодня они предлагают сотни различных моделей насосов самых разных типов.
Используется в мойках высокого давления этих марок : BE, Campbell Hausfeld, DeWalt, Pressure-Pro, Simpson.
Типы насосов производства CAT : Все типы.
КометаComet является дистрибьютором в США другого итальянского производителя насосов, Comet SpA.Их насосы используются во многих отраслях промышленности, от пивоваренных заводов, цементных заводов и нефтяных месторождений до целлюлозно-бумажной промышленности и моек высокого давления.
Используется в мойках высокого давления этих марок : Насос для мойки высокого давления Excell.
Типы насосов производства Comet : Осевой, Триплекс.
Общий насосКомпания General Pump, базирующаяся в Миннесоте, хорошо известна в сфере мойки высокого давления и мойки автомобилей своими превосходными трехплунжерными насосами.Они предлагают сотни различных моделей.
Используется в мойках высокого давления этих марок : BE, DeWalt, Easy-Kleen.
Типы насосов General : Triplex.
КерхерKarcher — немецкая компания, крупнейший производитель моек высокого давления в мире. Поэтому имеет смысл, что они делают свои собственные насосы. Они разработали свои насосы с нуля, используя устойчивый к коррозии материал «N-COR», который представляет собой комбинацию полиамида и стекловолокна.
Используется в мойках высокого давления этих марок : Karcher.
Типы насосов производства Karcher : Осевой кулачок, тройной поршень.
КранцлеKranzle — немецкая компания, производящая мойки высокого давления, пылеуловители, промышленные пылесосы и подметальные машины.
Используется в мойках высокого давления этих марок : Kranzle.
Типы насосов производства Kranzle : Вибрационный, осевой кулачковый.
Насосы AAA (группа FNA)AAA Pumps — это насос производства FNA Group для использования в мойках высокого давления. Им принадлежит торговая марка Simpson Cleaning.
Используется в мойках высокого давления следующих марок: Simpson.
Типы насосов производства AAA : Осевой кулачок, Triplex.
Как купить сменный насос и деталиЕсть много хороших мест, где можно купить сменный насос.Интернет-магазины, такие как Amazon и RepairClinic, предлагают наибольшее разнообразие.
На что следует обратить внимание. Описание насоса часто говорит все, что вам нужно знать о том, может ли насос работать с вашей мойкой высокого давления. Однако убедитесь, что размеры приводного вала совпадают… И что мощность двигателя/мотора достаточна для насоса. Также убедитесь, что это правильная конфигурация — вертикальная или горизонтальная — для монтажа.
Насосы Amazon.com — выбор из сотен насосов.Найдите свою по этой ссылке и используйте фильтр уточнения поиска на левой боковой панели, чтобы сузить поиск.
Ремонт насосаОбратитесь к местному дилеру моек высокого давления за услугами по ремонту насоса.
Узнайте здесь, как заменить масло в водяном насосе мойки высокого давления.
Источники- «Насосы прямого вытеснения» Джо Эванса, доктора философии. Pumped101.com . Проверено 12 августа 2015 г.
- Michael Volk (21 октября 2013 г.), Характеристики и применение насоса, третье издание, стр. 34.Проверено 12 августа 2015 г.
- «Как работает плунжерный насос — анимация». Канал TechTrixInfo на youtube.com . Просмотрено 12 августа 2015 г.
- «Анимация. Как работает осевой поршневой насос переменной производительности». Канал TechTrixInfo на youtube.com. Проверено 12 августа 2015 г.
- «Поршневой насос фиксированного рабочего объема». mekanizmaler youtube.com канал . Просмотрено 11 августа 2015 г.
- «Руководство по типам насосов. Найдите насос, подходящий для работы». Пампскаут.ком. Проверено 13 августа 2015 г.
- «Насос очистителя высокого давления, сопла и моющее средство». www.QualityPumps.com. Проверено 13 августа 2015 г.
Об авторе: Джейми тестирует и анализирует мойки высокого давления уже 7 лет. Он работал в качестве коммерческого мойщика высокого давления на заводе по рендерингу в течение 3 лет, и все это время он использовал коммерческие и бытовые мойки высокого давления более 15 лет. Он также является инженером-механиком и, работая в горнодобывающей промышленности, разработал несколько моечных площадок для легких промышленных транспортных средств «под ключ».
Поршневой компрессор — PetroWiki
Поршневые компрессоры — это машины объемного типа, в которых сжимающим и перемещающим элементом является поршень, совершающий возвратно-поступательное движение внутри цилиндра. Обсуждение поршневых компрессоров на этой странице включает описание конфигурации процесса для многоступенчатых агрегатов, а также объяснение концепций:
- Регулятор скорости
- Дросселирование на входе
- Переработка
- Сброс давления
- Продувка
- Вставка для вентиляции и слива
Типы поршневых компрессоров
Существует два типа поршневых компрессоров:
- Высокоскоростной (разборный)
- Низкоскоростная (встроенная)
Высокоскоростная категория также называется «отдельной», а низкоскоростная категория также известна как «интегральная».”
Американский институт нефти (API) разработал два отраслевых стандарта: стандарт API 11P и стандарт API 618 , которые часто используются для управления проектированием и производством поршневых компрессоров.
Съемные компрессоры
Термин «отдельный» используется потому, что эта категория поршневых компрессоров отделена от своего привода. Либо двигатель, либо электродвигатель обычно приводит в движение отделяемый компрессор. Часто редуктор требуется в поезде сжатия.Рабочая скорость обычно составляет от 900 до 1800 об/мин.
Съемные блоки монтируются на салазках и являются автономными. Они просты в установке, имеют относительно небольшую первоначальную стоимость, легко перемещаются в другие места и доступны в размерах, подходящих для сбора в полевых условиях — как на суше, так и на море. Однако раздельные компрессоры требуют более высоких затрат на техническое обслуживание, чем встроенные компрессоры.
На рис. 1 показано поперечное сечение типичного разъемного компрессора. На рис. 2 показан отделяемый компрессорный агрегат с приводом от двигателя.
Рис. 1—Поперечное сечение разъемного компрессора (любезно предоставлено Dresser-Rand).
Рис. 2 — Съемный компрессорный агрегат двигателя (предоставлено компанией Dresser-Rand).
Встроенные компрессоры
Термин «интегральный» используется потому, что силовые цилиндры, приводящие в действие компрессор, смонтированы за одно целое с рамой, содержащей цилиндры компрессора. Интегральные агрегаты работают со скоростью от 200 до 600 об/мин.Они обычно используются на газовых заводах и трубопроводах, где эффективность использования топлива и длительный срок службы имеют решающее значение. Интегральные компрессоры могут быть оснащены от двух до десяти компрессорных цилиндров мощностью от 140 до 12 000 л.с.
Встроенные компрессоры обеспечивают высокую эффективность в широком диапазоне условий эксплуатации и требуют меньшего обслуживания, чем отдельные агрегаты. Однако интегральные блоки обычно должны монтироваться на месте и требуют тяжелого фундамента и высокой степени подавления вибрации и пульсации.У них самая высокая начальная стоимость установки.
Рис. 3 представляет собой поперечное сечение типичного интегрального компрессора. На рис. 4 показан составной компрессорный агрегат.
Рис. 3—Поперечное сечение встроенного компрессора (любезно предоставлено Dresser-Rand).
Рис. 4 — Встроенный поршневой компрессор (предоставлено компанией Dresser-Rand).
Основные компоненты
Поршневые компрессоры доступны в различных конструкциях и компоновках.Основные компоненты типичного поршневого компрессора показаны на рис. 5 .
Рис. 5 — Компоненты поршневого компрессора (любезно предоставлено Dresser-Rand).
Рама
Рама представляет собой тяжелый, прочный корпус, содержащий все вращающиеся части, на котором установлены цилиндр и направляющая крейцкопфа. Производители компрессоров оценивают рамы по максимальной непрерывной мощности и нагрузке на раму (см. раздел о нагрузке на шток ниже).
Съемные компрессоры обычно располагаются в сбалансированно-оппозитной конфигурации, характеризующейся соседней парой кривошипов, которые сдвинуты по фазе на 180 градусов и разделены только перемычкой кривошипа. Шатуны устроены так, что движение каждого поршня уравновешивается движением противоположного поршня.
Встроенные компрессоры обычно имеют силовые цилиндры компрессора и двигателя, установленные на одной раме и приводимые в движение одним и тем же коленчатым валом. Цилиндры встроенных компрессоров обычно располагаются только на одной стороне рамы (т.е., не уравновешенно-противоположное).
Цилиндр
Баллон представляет собой сосуд высокого давления, в котором содержится газ в цикле сжатия. Цилиндры одностороннего действия сжимают газ только в одном направлении движения поршня. Они могут быть как головными, так и кривошипными. Цилиндры двустороннего действия сжимают газ в обоих направлениях движения поршня (см. рис. 6 ). В большинстве поршневых компрессоров используются цилиндры двойного действия.
Рис. 6 — Цилиндры двустороннего действия (любезно предоставлено Dresser-Rand).
Выбор материала цилиндра определяется рабочим давлением. Чугун обычно используется для давления до 1000 фунтов на квадратный дюйм. Чугун с шаровидным графитом используется для давления до 1500 фунтов на квадратный дюйм. Литая сталь обычно используется для давления от 1500 до 2500 фунтов на квадратный дюйм. Кованая сталь выбирается для рабочих давлений цилиндров более 2500 фунтов на квадратный дюйм.
Максимально допустимое рабочее давление (МДРД) баллона должно быть как минимум на 10 % выше расчетного давления нагнетания (минимум 25 фунтов на кв. дюйм).Дополнительное номинальное давление позволяет настроить предохранительный датчик высокого давления (PSH) выше расчетного давления нагнетания, а предохранительный клапан (PSV) настроить на давление выше PSH.
Износоустойчивость трущихся деталей (поршневых колец и цилиндра, поршневого штока и уплотнительных колец и т. д.) также является критерием выбора материалов. Цилиндры испытывают износ в месте контакта с поршневыми кольцами. В горизонтальном расположении из-за веса поршня износ цилиндра больше всего в нижней части.В большинстве поршневых компрессоров используются термопластичные кольца и натяжные ленты для уменьшения такого износа.
Цилиндры часто поставляются с гильзами для снижения затрат на восстановление. Вкладыши прижимаются или сжимаются на месте, чтобы гарантировать, что они не скользят. Замена гильзы цилиндра намного дешевле, чем замена всего цилиндра. Кроме того, производительность может быть адаптирована к новым требованиям путем изменения внутреннего диаметра гильзы. Однако гильзы цилиндров увеличивают зазор между клапаном и поршнем, снижают эффективность охлаждения рубашки и снижают производительность компрессора при заданном диаметре.
Распорка
Распорка обеспечивает разделение между цилиндром компрессора и рамой компрессора. На рис. 7 показаны распорки стандарта API 11P и стандарта API 618. Распорки могут содержаться как в одно-, так и в двухсекционном исполнении. В однокамерной конструкции пространство между набивкой цилиндра и диафрагмой удлиняется таким образом, что ни одна часть штока не попадает одновременно в картер и сальник цилиндра.Масло мигрирует между цилиндром и картером. Если загрязнение маслом вызывает беспокойство, можно предусмотреть маслоотражатель, чтобы предотвратить попадание сальникового смазочного масла в раму компрессора. Для работы с токсичными веществами может использоваться двухкамерная конструкция. Никакая часть штока не попадает ни в картер, ни в отсек, примыкающий к газовому баллону.
Рис. 7 — Двухкамерная вставка, показывающая расположение уплотнения и буферного газа (любезно предоставлено Dresser-Rand).
Упаковочный ящик должен вентилироваться через всасывание первой ступени или через систему отвода газов.Распорки имеют вентиляционное отверстие для отвода дополнительной утечки технологического газа из набивки. Диафрагма и набивка предназначены для предотвращения попадания газа в картер. Требуется эффективная вентиляция, чтобы технологический газ не загрязнял картерное масло.
Каждый компрессор должен быть оборудован отдельной системой вентиляции и слива для распорок и набивки. Прокладка и вентиляционные отверстия сальника должны быть подключены к открытой вентиляционной системе, которая заканчивается снаружи и над корпусом компрессора на расстоянии не менее 25 футов по горизонтали от выхлопного отверстия двигателя.Дренажная вставка должна быть отведена в отдельный отстойник, который можно опорожнять вручную. Отстойник должен вентилироваться снаружи и над кожухом компрессора. Смазочное масло из поддона можно смешивать с сырой нефтью или, при определенных обстоятельствах, его необходимо транспортировать для утилизации или переработки.
Коленчатый вал
Коленчатый вал вращается вокруг оси рамы и приводит в движение шатун, шток поршня и поршень (см. рис. 8 ).
- Шатун, соединяющий коленчатый вал с пальцем крейцкопфа
- Крейцкопф преобразует вращательное движение шатуна в линейное колебательное движение, приводящее в движение поршень
- Шток поршня соединяет крейцкопф с поршнем.
Рис. 8 — Коленчатый вал в сборе (любезно предоставлено Dresser-Rand).
Поршень
Поршень расположен на конце штока поршня и действует как подвижная перегородка в цилиндре компрессора. Выбор материала зависит от прочности, веса и совместимости со сжимаемым газом. Поршень обычно изготавливается из легкого материала, такого как алюминий, чугун или сталь, с полым центром для снижения веса.Термопластичные изнашиваемые (или накладные) кольца часто устанавливаются на поршни для увеличения срока службы колец и снижения риска контакта поршня с цилиндром. Чугун обычно обеспечивает удовлетворительно низкие характеристики трения, что устраняет необходимость в отдельных износостойких лентах.
Изнашиваемые ленты распределяют вес поршня вдоль нижней части цилиндра или стенки гильзы. Поршневые кольца минимизируют утечку газа между поршнем и цилиндром или отверстием гильзы. Поршневые кольца изготовлены из более мягкого материала, чем стенка цилиндра или гильзы, и заменяются через регулярные интервалы технического обслуживания.По мере того, как поршень проходит через отверстие подачи лубрикатора в стенке цилиндра, поршневое кольцо собирает масло и распределяет его по длине хода.
Подшипники
Подшипники, расположенные по всей раме компрессора, обеспечивают правильное радиальное и осевое расположение компонентов компрессора. Коренные подшипники установлены в раме для правильного положения коленчатого вала. Подшипники шатунной шейки расположены между коленчатым валом и каждым шатуном. Подшипники поршневого пальца расположены между каждым шатуном и пальцем крейцкопфа.Подшипники крейцкопфа расположены вверху и внизу каждой крейцкопфа.
Большинство подшипников поршневых компрессоров представляют собой подшипники с гидродинамической смазкой. Масло под давлением подается к каждому подшипнику через канавки подачи масла на поверхности подшипника. Размер канавок обеспечивает достаточный поток масла для предотвращения перегрева.
Сальник штока поршня обеспечивает динамическое уплотнение между цилиндром и штоком поршня. Набивка состоит из ряда неметаллических колец, установленных в корпусе и прикрученных к цилиндру болтами.Уплотнительные кольца работают попарно и предназначены для автоматической компенсации износа. Поскольку каждая пара колец выдерживает ограниченный перепад давления, требуется несколько пар в зависимости от давления, требуемого приложением. Для безопасного отвода утечки газа через набивку вентиляционное отверстие обычно располагается между двумя узлами наружных колец (см. раздел о распорке выше).
Вспомогательные соединения с набивкой могут потребоваться для:
- Охлаждающая вода
- Смазочное масло
- Продувка азотом
- Вентиляция
- Измерение температуры
Смазка должна быть тонко отфильтрована, чтобы избежать повреждений, которые могут возникнуть в результате попадания в корпус мелких твердых частиц.Смазочное масло обычно впрыскивается во второе кольцо в сборе, при этом масло перемещается вдоль вала под давлением.
Клапаны компрессора
Основной функцией клапанов компрессора является обеспечение потока газа в желаемом направлении и блокирование всего потока в противоположном (нежелательном) направлении. Каждый рабочий конец цилиндра компрессора должен иметь два комплекта клапанов. Набор впускных (всасывающих) клапанов впускает газ в баллон. Набор выпускных клапанов используется для откачки сжатого газа из баллона.Производитель компрессора обычно указывает тип и размер клапана.
Пластинчатые клапаны, состоящие из колец, соединенных перемычками в единую пластину, являются распространенным типом клапанов. В зависимости от материала уплотнительной пластины пластинчатые клапаны способны выдерживать давление до 15 000 фунтов на квадратный дюйм, перепад давления до 10 000 фунтов на квадратный дюйм, скорость до 2000 об/мин и температуру до 500°F. Пластинчатые клапаны плохо работают в присутствии жидкостей.
Клапаны с концентрическими кольцами способны выдерживать давление до 15 000 фунтов на квадратный дюйм, дифференциальное давление до 10 000 фунтов на квадратный дюйм, скорость до 2000 об/мин и температуру до 500°F.К преимуществам концентрических кольцевых клапанов относятся:
- Умеренная стоимость запчастей
- Низкая стоимость ремонта
- Способность работать с жидкостями лучше, чем у тарельчатых клапанов
Тарельчатые клапаны, как правило, обеспечивают более высокие характеристики, чем у тарельчатых клапанов и клапанов с концентрическими кольцами. В тарельчатом стиле используются отдельные круглые тарелки, которые прилегают к отверстиям в седле клапана. Этот тип клапана обеспечивает высокий подъем и низкий перепад давления, что приводит к более высокой эффективности использования топлива. Тарельчатые клапаны широко используются в трубопроводах, газоочистных и перерабатывающих установках.Металлические тарелки хорошо работают при:
- Давление до 3000 фунтов на кв. дюйм
- Перепад давления до 1400 фунтов на кв. дюйм
- Скорость до 450 об/мин
- Температуры до 500°F
Тарелки из термопласта могут применяться в следующих случаях:
- Давление до 3000 фунтов на кв. дюйм
- Перепад давления до 1500 фунтов на кв. дюйм
- Скорость до 720 об/мин
- Температура до 400°F
Большинство компрессоров имеют клапаны, установленные в цилиндрах.Относительно новая концепция конструкции помещает клапаны в поршень. Конструкция «клапан в поршне» ( рис. 9 ) работает с низкими скоростями клапана и обеспечивает более длительный срок службы и сокращение времени обслуживания.
Рис. 9 — Конструкция «клапан в поршне» (предоставлено Dresser-Rand).
Производительность компрессора
Производительность и мощность компрессора зависят от смещения поршня и зазора цилиндра. Пропускная способность данного цилиндра является функцией смещения поршня и объемного КПД.Объемный КПД зависит от зазора цилиндра, степени сжатия и свойств сжимаемого газа. Производительность компрессора можно рассчитать с помощью любого из следующих трех уравнений.
…………….(1)
…………….(2)
и
…………….(3)
где
q а | = | впускная способность цилиндра при фактических входных условиях, акф/мин, |
Е в | = | объемный КПД, |
ПД | = | объем поршня, акф/мин, |
q г | = | пропускная способность цилиндра на входе, станд. куб. фут/мин, |
и | ||
Q г | = | пропускная способность цилиндра на входе, млн станд. фут./сут. |
Объем поршня
Рабочий объем поршня определяется как фактический объем цилиндра, охватываемый поршнем в единицу времени. Рабочий объем обычно выражается в фактических кубических футах в минуту (Acf/min). Расчет рабочего объема поршня представляет собой простую процедуру, которая зависит от типа конфигурации компрессора. Цилиндры одностороннего действия могут иметь смещение головки или кривошипа. уравнения. 4 и 5 используются для расчета рабочего объема цилиндров одностороннего действия.уравнение 4 для смещения головной части и уравнение. 5 — для смещения конца кривошипа.
…………….(4)
…………….(5)
где
ПД | = | объем поршня, акф/мин, |
С | = | ход поршня, дюйм, |
Н | = | Частота вращения компрессора, об/мин, |
г в | = | диаметр цилиндра, дюйм, |
д р | = | диаметр штока, дюйм |
Рабочий объем цилиндра двустороннего действия рассчитывается по уравнению . 6 .
…………….(6)
где
ПД | = | объем поршня, акф/мин, |
С | = | ход поршня, дюйм, |
Н | = | Частота вращения компрессора, об/мин, |
г в | = | диаметр цилиндра, дюйм, |
и | ||
д р | = | диаметр штока, дюйм |
Методы, используемые для изменения рабочего объема поршня, включают изменение скорости компрессора, удаление или отключение всасывающих клапанов в цилиндре двустороннего действия и изменение диаметра гильзы цилиндра и поршня.
Разгрузка одного конца может значительно снизить производительность цилиндра двустороннего действия. Лучший способ разгрузить баллон — отключить или снять всасывающие клапаны с одного конца, чтобы предотвратить сжатие газа на этом конце.В зависимости от частоты разгрузки и молекулярной массы газа разгрузочное устройство с портом или заглушкой является следующим лучшим методом разгрузки баллона. Кольцевая заглушка заменяет один всасывающий клапан из трех или более клапанов на угол, а на каждый конец цилиндра требуется только одно разгрузочное устройство. В концентрических кольцевых клапанах можно разместить пробку для разгрузки в центре всасывающего клапана для разгрузки. В зависимости от молекулярной массы газа портовые и пробковые разгрузочные устройства снижают BHP/MMscf/D и значительно повышают надежность разгрузочной системы.
Если всасывающий клапан удерживается открытым с помощью пальцевых депрессоров во время такта сжатия, газ будет течь через открытый клапан обратно во всасывающий канал, и газ не будет выходить из конца цилиндра, содержащего ненагруженный всасывающий клапан. Деактивация клапанов может выполняться вручную при выключенном компрессоре или с помощью разгрузочного клапана или подъемника во время работы компрессора. Управление разгрузочным клапаном может быть ручным или автоматическим с помощью диафрагмы, которая разгружает компрессор с помощью датчика давления всасывания.Мембранные приводы более надежны, чем ручные подъемники или разгрузчики.
Разгрузка обоих концов одного и того же цилиндра может привести к перегреву цилиндра; таким образом, лучше всего разгружать только один конец цилиндра компрессора двойного действия. В большинстве случаев предпочтительно снимать всасывающий клапан при разгрузке головной части цилиндра, чтобы обеспечить изменение направления нагрузки в штоках. (См. раздел о нагрузке на стержень ниже)
Объем клиренса
Рабочий объем — это пространство, остающееся в цилиндре компрессора в конце хода.Зазор состоит из пространств в канавках клапанов и пространства между поршнем и торцом цилиндра. По завершении каждого такта сжатия сжатый газ, попавший в зазор, расширяется против поршня и увеличивает усилие обратного хода. Рис. 10 представляет собой диаграмму зависимости давления от объема ( P-V ), иллюстрирующую влияние зазора.
Рис. 10—Поршневой компрессор модели PV (предоставлено Dresser-Rand).
Расширение газа, попавшего в зазор, происходит до того, как всасывающий клапан откроется, чтобы впустить новый газ в цилиндр. В результате часть смещения поршня происходит до открытия всасывающего клапана. Процесс сжатия в поршневых компрессорах почти изоэнтропический, поэтому энергия, необходимая для сжатия газа в воздушном пространстве, рекуперируется, когда газ расширяется в конце такта сжатия. По этой причине изменение зазора не влияет на мощность компрессора.
Объем зазора выражается в процентах от рабочего объема поршня с использованием одного из следующих уравнений, зависящих от конфигурации:
- Цилиндр одностороннего действия (зазор в головке) [ Ур. 7 ]
- Цилиндр одностороннего действия (зазор кривошипа) [ Ур. 8 ]
- Цилиндр двустороннего действия (зазор головки и кривошипа) [ Ур. 9 ]
…………….(7)
…………….(8)
…………….(9)
где
% С | = | зазор цилиндра, %, |
С НЕ | = | зазор головной части, дюйм 3 , |
С СЕ | = | зазор коленчатого вала, дюймы 3 , |
г в | = | внутренний диаметр цилиндра, дюйм, |
д р | = | Диаметр штока, дюйм, |
С | = | длина хода, дюйм |
Применение
Зазор может быть добавлен к цилиндру как:
- Прорезные карманы фиксированного объема
- Карманы с переменным зазором
- Хомуты раздельных клапанов
Зазоры фиксированного объема
Зазорный карман фиксированного объема обычно представляет собой бутылку, постоянно прикрепленную к цилиндру.Фиксированный объем также может быть увеличен за счет заглушки бокового прохода, состоящей из фланца с заглушкой переменной длины, вставляемой в проход, встроенный в боковую часть цилиндра. Зазорный карман фиксированного объема может быть постоянно открыт, или его можно контролировать, открывая или закрывая его. Управление может осуществляться ручным маховиком или автоматическим приводом. Управление приводом позволяет открывать или закрывать зазор снаружи цилиндра во время работы компрессора.
Карманы с переменным зазором
Гнезда с переменным зазором позволяют добавить к цилиндру переменный зазор и могут быть прикреплены либо к головке, либо к кривошипу цилиндра.Чаще всего к головному концу крепятся карманы с переменным зазором, как показано на рис. 11 .
Рис. 11 — Карман с ручным управлением регулируемым объемом (любезно предоставлено Dresser-Rand).
Хомуты раздельных клапанов
Чрезмерный зазор в цилиндре компрессора может привести к захлопыванию нагнетательных клапанов. При наличии слишком большого зазора газ не будет выходить. Может произойти быстрый перегрев из-за того, что в цилиндр не поступает холодный всасываемый газ.
Объемный КПД
Объемный КПД – это отношение фактического объема газа (куб. фут/мин), всасываемого в цилиндр, к объему поршня (куб. фут/мин). Это отношение меньше единицы из-за трех фундаментальных эффектов. Во-первых, газ нагревается при поступлении в баллон. Во-вторых, происходит утечка через клапаны и поршневые кольца. И в-третьих, происходит повторное расширение газа, попавшего в зазорный объем от предыдущего такта. Из этих трех, повторное расширение, безусловно, оказывает наибольшее влияние на объемную эффективность.
Производители компрессоров не пришли к единому мнению относительно подходящего метода расчета, поскольку измерение этих эффектов чрезвычайно сложно. Учитывая это, для оценки объемной эффективности можно использовать следующее приближенное уравнение.
…………….(10)
где
Е в | = | объемный КПД, |
Р | = | степень сжатия, |
С | = | зазор цилиндра, % рабочего объема поршня, |
Z с | = | коэффициент сжимаемости на входе, |
Z д | = | коэффициент сжимаемости нагнетания, |
д р | = | диаметр штока, дюйм, |
к | = | отношение удельных теплоемкостей, C p / C v , |
Л | = | проскальзывание газа через поршневые кольца, % (1% для быстроходных разъемных, 5% для несмазываемых компрессоров и 4% для работы на пропане), |
и | ||
96 | = | допуск на потери из-за падения давления в клапанах. |
Нагрузка на штангу
Нагрузки на шток состоят из газовых нагрузок, вызванных нагрузками от давления и инерции, возникающими в результате ускорения и замедления поршня, штока поршня, крейцкопфа и приблизительно одной трети веса шатуна. Производители указывают максимальную нагрузку на шток для защиты компрессора, поскольку перегрузка штоков может серьезно повредить компрессор. Нагрузки должны быть оценены для нормальных условий эксплуатации, а также в аварийных условиях. Нагрузку на шток следует проверять при минимальном давлении всасывания и давлении предохранительного клапана, чтобы обеспечить достаточный запас прочности.
Изменение направления нагрузки на шток должно быть достаточным для обеспечения смазки втулки пальца крейцкопфа. Втулки смазываются насосным действием открытия и закрытия зазора подшипника, которое происходит, когда нагрузка на шток меняется от растяжения к сжатию. Эксплуатация без реверсирования штока также может серьезно повредить компрессор.
Нагрузки на шток для различных конфигураций компрессора рассчитываются по следующим уравнениям:
- Цилиндр одностороннего действия (головка)
- Цилиндр одностороннего действия (со стороны кривошипа)
- Цилиндр двустороннего действия
Цилиндр одностороннего действия (головка)
…………….(11)
…………….(12)
РЛ с | = | Нагрузка на штокпри сжатии, фунт-сила, |
РЛ т | = | Нагрузка на стерженьпри растяжении, фунт-сила, |
а р | = | площадь поперечного сечения поршня, дюйм 2 , |
а р | = | Площадь поперечного сечения стержня, дюйм 2 , |
П д | = | давление нагнетания, фунтов на квадратный дюйм, |
П с | = | давление всасывания, фунтов на квадратный дюйм, |
и | ||
П у | = | давление в разгруженном конце, фунтов на квадратный дюйм. |
Цилиндр одностороннего действия (кривошип)
…………….(13)
…………….(14)
РЛ с | = | Нагрузка на штокпри сжатии, фунт-сила, |
РЛ т | = | Нагрузка на стерженьпри растяжении, фунт-сила, |
а р | = | площадь поперечного сечения поршня, дюйм 2 , |
а р | = | Площадь поперечного сечения стержня, дюйм 2 , |
П д | = | давление нагнетания, фунтов на квадратный дюйм, |
П с | = | давление всасывания, фунтов на квадратный дюйм, |
и | ||
П у | = | давление в разгруженном конце, фунтов на квадратный дюйм. |
Цилиндр двустороннего действия
…………….(15)
…………….(16)
РЛ с | = | Нагрузка на штокпри сжатии, фунт-сила, |
РЛ т | = | Нагрузка на стерженьпри растяжении, фунт-сила, |
а р | = | площадь поперечного сечения поршня, дюйм 2 , |
а р | = | Площадь поперечного сечения стержня, дюйм 2 , |
П д | = | давление нагнетания, фунтов на квадратный дюйм, |
П с | = | давление всасывания, фунтов на квадратный дюйм, |
и | ||
П у | = | давление в разгруженном конце, фунтов на квадратный дюйм. |
Прочие факторы эффективности
Дополнительные соображения по производительности включают:
- Давление всасывания .При постоянном давлении нагнетания со степенью сжатия более 2,0 степень сжатия уменьшается по мере увеличения давления всасывания. Снижение степени сжатия снижает потребность в мощности на единицу потока. Однако емкость цилиндра увеличивается с давлением всасывания более быстрыми темпами, что приводит к общему увеличению мощности. Чтобы не перегружать водителя, необходимо добавить дополнительный зазор, чтобы уменьшить объем цилиндра.
- Температура всасывания . Объем цилиндра обратно пропорционален абсолютной температуре всасывания.По мере снижения температуры баллон заполняет больше стандартных кубических футов. Таким образом, снижение температуры всасывания на 10°F увеличивает массовый расход компрессора почти на 2%. Предварительное охлаждение газа может быть эффективным способом увеличения емкости цилиндра.
- Давление нагнетания . Изменения давления нагнетания мало влияют на рабочий объем цилиндра. Объемный КПД незначительно зависит от степени сжатия, а требуемая мощность прямо пропорциональна изменению степени сжатия.
- Отношение удельных теплоемкостей (k) .Увеличение значения k приводит к увеличению объемной эффективности, как определено уравнением . 10 . Таким образом, данный цилиндр компрессора имеет более высокую фактическую производительность при сжатии природного газа ( к = 1,25), по сравнению с его производительностью при сжатии пропана ( к = 1,15). Более высокая производительность при сжатии природного газа по сравнению с пропаном также приводит к большему энергопотреблению.
- Скорость . Объем цилиндра прямо пропорционален скорости компрессора.Обычной практикой является регулирование скорости компрессора (в разумных пределах) для поддержания желаемого давления всасывания. Снижение скорости водителя снижает расход топлива и эксплуатационные расходы.
Карты производительности
Карты производительности могут быть разработаны для конкретного компрессора с постоянными базовыми условиями. На рис. 12 показано, что по мере увеличения давления всасывания увеличиваются как расход на входе, так и мощность при постоянном давлении и температуре нагнетания. При очень низких соотношениях мощность может фактически уменьшаться с увеличением давления всасывания.
Рис. 12 — Схема поршневого компрессора с восемью ступенями разгрузки (предоставлено Dresser-Rand).
Технологическая установка
Компрессор является составной частью полной компрессорной системы. На рис. 13 представлена типовая технологическая схема установки поршневого компрессора.
Рис. 13 — Технологическая схема компрессора со встроенным (пульсационный сосуд) сепаратором (любезно предоставлена компанией Dresser-Rand).
Клапан рециркуляции
Давление всасывания компрессора уменьшается по мере уменьшения расхода до тех пор, пока газ не расширится, чтобы удовлетворить расход, необходимый для цилиндра. Увеличение степени сжатия, вызванное снижением давления всасывания, приводит к увеличению температуры нагнетания. Таким образом, рециркуляционный клапан в системе должен быть настроен таким образом, чтобы низкое давление всасывания не создавало чрезмерной температуры нагнетания. Кроме того, пределы нагрузки на шток могут определять минимально допустимое давление всасывания для компрессорной установки.Там, где это возможно, клапан рециркуляции должен располагаться после газоохладителей.
Продувочный клапан
Продувочный клапан сбрасывает оставшееся давление, когда компрессор останавливается на техническое обслуживание. Управление клапаном обычно автоматическое, но иногда оно осуществляется вручную на некоторых небольших береговых компрессорных установках.
Всасывающий скруббер
Попадание жидкостей в компрессор через входной газовый поток может привести к повреждению внутренних компонентов компрессора. По этой причине требуется всасывающий скруббер подходящего размера с приспособлениями для слива.При правильном планировании скруббер может быть частью системы контроля пульсации (см. раздел о пульсации ниже). Если входящий поток близок к насыщению, рекомендуются горизонтально ориентированные цилиндры и выпускные патрубки с нижним соединением.
Предохранительные клапаны
Клапаны сброса давления, установленные с запасом на 10 % выше максимального давления нагнетания ступени или минимум на 15–25 фунтов на кв. дюйм, обеспечивают защиту трубопроводов и охладителей от статического давления. Настройка предохранительного клапана никогда не должна превышать максимально допустимое рабочее давление в баллоне (см. раздел о баллонах выше).Следует соблюдать осторожность, чтобы убедиться, что все газовые трубопроводы, баллоны и предохранительные клапаны на стороне всасывания рассчитаны на давление осаждения в системах охлаждения с замкнутым контуром или при низких температурах газа.
Пульсация
Поток газа через поршневой компрессор по своей природе вызывает пульсацию, поскольку всасывающий и выпускной клапаны не открыты на протяжении всего такта сжатия. Демпфирование пульсаций необходимо для создания более равномерного потока через компрессор, чтобы обеспечить равномерную нагрузку и снизить уровень вибрации трубопровода.
Устройства контроля пульсации
Если могут быть обеспечены длинные прямые участки трубопровода того же диаметра, что и соединение с линией цилиндра компрессора, а мощность ступени составляет менее 150 л.с., отдельные баллоны или пульсационные сосуды могут не потребоваться. Для большинства применений объемные баллоны или пульсационные сосуды с внутренними перегородками и/или дроссельными трубками должны располагаться как можно ближе к цилиндру для обеспечения оптимальной надежности клапана. Добавление отверстий в ключевых местах трубопровода также может уменьшить пульсации трубопровода.Доступно несколько различных формул для определения размеров бутылок. Типичные размеры бутылок в пять-десять раз превышают рабочий объем цилиндра.
Пульсация
Цифровой анализ пульсации трубопровода — это относительно недорогой метод, позволяющий убедиться, что трубопроводная система рассчитана на приемлемые уровни пульсаций (обычно от 2 до 7% от пика к пику). Схема системы трубопроводов должна определять расположение и объемы выбивных барабанов, бутылок, охладителей и предохранительных клапанов. Анализ должен включать первый крупный сосуд или объем до и после компрессора.Рабочие условия двойного и одинарного действия (если применимо) должны быть проанализированы.
Вопросы вибрации
Дисбаланс вращающихся элементов в компрессоре вызывает механическую вибрацию. Противовесы на коленчатом валу и расположение цилиндров попарно с обеих сторон коленчатого вала (на виду) могут минимизировать, но не устранить силы дисбаланса. Таким образом, всегда будут механические вибраторы, которые необходимо учитывать при проектировании фундамента.
Вибрация трубопроводов
Трубопровод технологического газа компрессора должен быть правильно спроектирован и установлен, чтобы избежать проблем, связанных с чрезмерной вибрацией.Важно, чтобы собственная частота всех пролетов труб была больше частоты пульсаций компрессора. Частота пульсаций компрессора рассчитывается по формуле . 17 .
…………….(17)
где
ж р | = | Частота пульсаций компрессора, цикл/с, |
Н | = | Частота вращения компрессора, об/мин, |
нет | = | коэффициент цилиндра, |
= | 1 для цилиндра одностороннего действия | |
и | ||
= | 2 (для цилиндра двустороннего действия). |
Трубопроводы должны быть надежно закреплены с использованием коротких отрезков труб, неодинаковых по длине. Адекватное демпфирование пульсаций помогает предотвратить проблемы с вибрацией, связанные с трубопроводом.
Проект фундамента
Для больших встроенных компрессоров или для компрессоров, установленных на сложных конструкциях или мягких грунтах, лучше всего выполнить динамическую конструкцию с использованием сил дисбаланса, предусмотренных производителем.
Для высокоскоростных компрессоров, установленных в районах с почвой, способной выдержать пикап, полезны следующие правила.
- Вес бетонного фундамента должен как минимум в три-пять раз превышать вес оборудования.
- Используйте грунтовую опору для конструкции, которая составляет менее 50% от допустимой для статических условий.
- Обычно лучше увеличить длину и/или ширину, а не глубину, чтобы соответствовать требованиям по весу.
- Для прямоугольного блока не менее 40% высоты (но не менее 18 дюймов) должны быть заглублены в ненарушенный грунт.
- Бетон следует заливать в «аккуратную» выемку без сформированных боковых граней.
Цилиндр охлаждения
Теплота сжатия и трения между поршневыми кольцами и цилиндром нагревает цилиндр. Отвод части этого тепла благотворно влияет на производительность и надежность компрессора по нескольким причинам. Охлаждение цилиндров снижает потери мощности и мощности, связанные с подогревом всасываемого газа. Он также отводит тепло от газа, тем самым снижая температуру газа нагнетания. Охлаждение цилиндра также способствует лучшему смазыванию, что продлевает срок службы и снижает потребность в техническом обслуживании.Когда в качестве охлаждающей среды используется вода, по всей окружности цилиндра поддерживается одинаковая температура, что снижает вероятность тепловой деформации цилиндра.
Необходимо соблюдать осторожность, чтобы избежать образования конденсата, который может возникнуть в результате чрезмерного охлаждения. Этого можно добиться, поддерживая температуру охлаждающей жидкости в рубашке цилиндра не менее чем на 10°F выше температуры всасываемого газа.
Недостаточное охлаждение может привести к снижению производительности и загрязнению цилиндров. По этой причине рекомендуется, чтобы температура баллона не превышала температуру всасываемого газа более чем на 30°F.
Системы охлаждения
Типы систем охлаждения включают:
- С воздушным охлаждением . Системы с воздушным охлаждением используются для небольших мощностей и низких тепловых нагрузок. Охлаждающие ребра обеспечивают достаточную площадь поверхности для охлаждения цилиндра.
- Статический . Статические системы иногда используются на небольших компрессорах для поддержки систем с воздушным охлаждением. Охлаждающая жидкость действует как статический поглотитель тепла и действует скорее как термостабилизатор, чем как система охлаждения. Некоторое количество тепла передается от системы теплопроводностью в атмосферу.
- Термосифон . Движущей силой термосифона является изменение плотности охлаждающей жидкости от горячих участков системы к холодным. Стандарт API 618 разрешает использование этой системы, когда температура нагнетаемого газа ниже 210°F или когда повышение температуры в цилиндре составляет менее 150°F.
- Герметичный . Системы охлаждения под давлением являются наиболее распространенными. В местах, где охлаждающая вода недоступна, может использоваться автономная закрытая система охлаждающей жидкости.Система состоит из циркуляционного насоса, расширительного бака и радиатора с вентиляторным охлаждением или теплообменника воздух-жидкость. Радиатор может иметь несколько секций: одну для охлаждающей жидкости цилиндра, одну для охлаждения смазочного масла и одну (или несколько) для охлаждения нагнетаемого газа. В качестве охлаждающей жидкости используется вода или смесь воды и этиленгликоля. Коленчатый вал обычно приводит в движение циркуляционный насос.
Смазка
Смазка рамы
Система смазки рамы подает масло к подшипникам рамы, шатунным подшипникам и башмакам крейцкопфа.Некоторые системы смазки рамы также подают масло на сальник и цилиндры. Для большинства поршневых компрессоров система смазки встроена в раму.
Смазка разбрызгиванием
Системы смазки разбрызгиванием распределяют смазочное масло путем разбрызгивания кривошипа через поверхность смазки в насосе. Ковши могут быть прикреплены к коленчатому валу для усиления эффекта. Системы разбрызгивания используются на небольших горизонтальных одноступенчатых компрессорах мощностью до 100 л.с.
Двумя основными преимуществами систем разбрызгивания являются:
- Низкая начальная стоимость
- Минимальное присутствие оператора
Основными недостатками являются то, что системы разбрызгивания ограничены:
- Маленькие размеры корпуса
- Масло нельзя фильтровать
Смазка под давлением
Наиболее распространенным типом смазки рамы является система под давлением. Масло поступает в каналы, просверленные в коленчатом валу, и течет через коренной вал и подшипники шатунной шейки.Система смазки под давлением состоит из следующих компонентов.
Главный масляный насос
Главный масляный насос приводится в действие коленчатым валом или может иметь отдельный привод. Обычно он рассчитан на подачу 110% от максимально ожидаемого расхода. Когда для управления производительностью используется снижение скорости, необходимо позаботиться о том, чтобы этот насос обеспечивал достаточную смазку при минимальной рабочей скорости.
Вспомогательный насос (дополнительно)
Вспомогательный насос предназначен для дублирования основного насоса.Вспомогательный насос обычно приводится в действие электродвигателем и предназначен для автоматического запуска, когда давление подачи масла падает ниже заданного уровня.
Насос предварительной смазки (дополнительно)
Насос предварительной смазки подает масло к подшипникам перед запуском компрессора. Это гарантирует, что подшипники не будут сухими при запуске. Поскольку эту функцию выполняет вспомогательный насос, насос предварительной смазки требуется только в том случае, если в системе нет вспомогательного насоса.
Масляный радиатор
Масляный радиатор обеспечивает, чтобы температура масла, подаваемого к подшипникам, не превышала максимальное значение, необходимое для защиты подшипников от износа.Типичная максимальная температура подачи масла составляет 120°F. Вода для охлаждения рубашки кожухотрубного теплообменника часто используется для охлаждения смазочного масла.
Масляные фильтры
Масляные фильтрызащищают подшипники, удаляя твердые частицы из смазочного масла. Некоторые системы оснащены двойными полнопоточными масляными фильтрами с перепускными клапанами. Перепускные клапаны позволяют переключаться с одного фильтра на другой, что позволяет очищать фильтры без отключения компрессора.
Верхний бак
Верхний бак обеспечивает подачу масла к подшипникам в случае отказа насоса.Масло из верхнего резервуара самотеком подается к подшипникам. Размер бака должен обеспечивать подачу масла до полного отключения компрессора. Резервуар обычно оборудован индикатором уровня.
Трубопровод
Компоненты системы смазки соединяются трубопроводом. Важными факторами являются чистота и коррозионная стойкость. Следует избегать использования оцинкованных труб из-за возможной коррозии. Трубопроводы из углеродистой стали должны быть протравлены или механически очищены и покрыты ингибитором ржавчины.После фильтров следует использовать трубопровод из нержавеющей стали. Система трубопроводов должна быть спроектирована так, чтобы не было карманов, в которых может скапливаться грязь или мусор. По этой причине следует избегать сварки труб в раструб. Перед первоначальным запуском систему смазки следует промыть смазочным маслом при температуре приблизительно 170°F. В систему следует добавить сито 200 меш, и промывку следует продолжать до тех пор, пока сетка не станет чистой. Защитные приборы должны включать датчик низкого уровня масла в картере, датчик отключения при низком давлении масла и датчик высокой температуры масла.
Для компрессоров со встроенным приводом двигателя рекомендуется, чтобы компрессор и привод смазывались отдельными системами, чтобы выхлопные газы двигателя не загрязняли смазочное масло. В этом случае смазка набивки и цилиндра обеспечивается системой смазки компрессора. Для установок в очень холодных условиях следует рассмотреть возможность использования погружных или встроенных нагревателей и специальных смазочных масел.
Смазка цилиндра и набивки
Количество масла, необходимое для смазки набивки и цилиндров, невелико по сравнению с требованиями к маслу подшипников.В то время как количество невелико, давление масла, необходимое для подачи масла на сальник и цилиндры, высокое. Небольшой плунжерный насос (лубрикатор принудительной подачи) используется на каждой ступени сжатия. Разделительные блоки служат для распределения потока масла между цилиндрами и набивкой. Масло может подаваться либо из системы смазки рамы, либо из верхнего бака. Для защиты от загрязнения необходимо проверить совместимость масла с технологическим газом.
Номенклатура
q а | = | впускная способность цилиндра при фактических входных условиях, акф/мин, |
Е в | = | объемный КПД, |
ПД | = | объем поршня, акф/мин, |
q г | = | пропускная способность цилиндра на входе, станд. куб. фут/мин, |
Q г | = | пропускная способность цилиндра на входе, млн станд. фут./сут. |
ПД | = | объем поршня, акф/мин, |
С | = | ход поршня, дюйм, |
Н | = | Частота вращения компрессора, об/мин, |
г в | = | Диаметр цилиндра, дюйм, |
д р | = | диаметр штока, дюйм |
% С | = | зазор цилиндра, %, |
С НЕ | = | зазор в головной части, дюйм 3 , |
С СЕ | = | зазор коленчатого вала, дюймы 3 , |
г в | = | Внутренний диаметр цилиндра, дюйм, |
д р | = | Диаметр штока, дюйм, |
С | = | длина хода, дюйм |
Е в | = | объемный КПД, |
Р | = | степень сжатия, |
С | = | зазор цилиндра, % рабочего объема поршня, |
Z с | = | коэффициент сжимаемости на входе, |
Z д | = | коэффициент сжимаемости нагнетания, |
д р | = | диаметр штока, дюйм, |
к | = | отношение удельных теплоемкостей, C p / C v , |
Л | = | проскальзывание газа через поршневые кольца, % (1% для быстроходных разъемных, 5% для несмазываемых компрессоров и 4% для работы на пропане), |
96 | = | допуск на потери из-за падения давления в клапанах |
РЛ с | = | Нагрузка на штокпри сжатии, фунт-сила, |
РЛ т | = | Нагрузка на стерженьпри растяжении, фунт-сила, |
а р | = | Площадь поперечного сечения поршня, дюйм 2 , |
а р | = | площадь поперечного сечения стержня, дюйм 2 , |
П д | = | давление нагнетания, фунтов на квадратный дюйм, |
П с | = | давление всасывания, фунтов на квадратный дюйм, |
П у | = | давление в разгруженном конце, фунтов на квадратный дюйм |
РЛ с | = | Нагрузка на штокпри сжатии, фунт-сила, |
РЛ т | = | Нагрузка на стерженьпри растяжении, фунт-сила, |
а р | = | Площадь поперечного сечения поршня, дюйм 2 , |
а р | = | площадь поперечного сечения стержня, дюйм 2 , |
П д | = | давление нагнетания, фунтов на квадратный дюйм, |
П с | = | давление всасывания, фунтов на квадратный дюйм, |
П у | = | давление в разгруженном конце, фунтов на квадратный дюйм |
ф р | = | Частота пульсаций компрессора, цикл/с, |
Н | = | Частота вращения компрессора, об/мин, |
нет | = | коэффициент цилиндра, |
= | 1 для цилиндра одностороннего действия | |
и | ||
= | 2 (для цилиндра двустороннего действия) |
Каталожные номера
Используйте этот раздел для цитирования элементов, на которые есть ссылки в тексте, чтобы показать ваши источники.[Источники должны быть доступны читателю, т. е. не являются внутренним документом компании.]
Примечательные статьи в OnePetro
Используйте этот раздел, чтобы перечислить статьи в OnePetro, которые обязательно должен прочитать читатель, желающий узнать больше.
Внешние ссылки
Используйте этот раздел для размещения ссылок на соответствующие материалы на веб-сайтах, отличных от PetroWiki и OnePetro.
См. также
Компрессоры
Центробежный компрессор
Компрессоры объемные ротационные
PEH:Компрессоры
насос| инжиниринг | Британика
насос , устройство, расходующее энергию для подъема, транспортировки или сжатия жидкостей.Самые ранние насосы были устройствами для подъема воды, такими как персидские и римские водяные колеса и более сложный винт Архимеда ( qv ).
Горнодобывающая промышленность Средневековья привела к развитию всасывающих (поршневых) насосов, многие типы которых описаны Георгиусом Агриколой в De re metallica (1556). Всасывающий насос работает за счет атмосферного давления; когда поршень поднимается, создавая частичный вакуум, внешнее атмосферное давление выталкивает воду в цилиндр, откуда она выходит через выпускной клапан.Только атмосферное давление может нагнетать воду на максимальную высоту около 34 футов (10 метров), поэтому нагнетательный насос был разработан для осушения более глубоких шахт. В силовом насосе ход поршня вниз вытесняет воду через боковой клапан на высоту, которая просто зависит от силы, приложенной к поршню.
Классификация насосов.
Насосы классифицируются по способу передачи энергии жидкости. Основными методами являются (1) объемное перемещение, (2) добавление кинетической энергии и (3) использование электромагнитной силы.
Жидкость можно вытеснить либо механически, либо с помощью другой жидкости. Кинетическая энергия может быть добавлена к жидкости либо путем ее вращения с высокой скоростью, либо путем создания импульса в направлении потока. Чтобы использовать электромагнитную силу, перекачиваемая жидкость должна быть хорошим электрическим проводником. Насосы, используемые для транспортировки или повышения давления газов, называются компрессорами, воздуходувками или вентиляторами. Насосы, в которых перемещение осуществляется механически, называются объемными насосами.Кинетические насосы передают кинетическую энергию жидкости с помощью быстро вращающегося рабочего колеса.
Вообще говоря, поршневые насосы перекачивают относительно небольшие объемы жидкости при высоком давлении, а кинетические насосы перекачивают большие объемы при низком давлении.
Требуется определенное давление, чтобы жидкость поступала в насос, прежде чем можно будет добавить дополнительное давление или скорость. Если давление на входе слишком мало, произойдет кавитация (образование вакуумного пространства в насосе, обычно занятого жидкостью).Испарение жидкости во всасывающей линии является частой причиной кавитации. Пузырьки пара, попадающие в насос вместе с жидкостью, разрушаются при попадании в область более высокого давления, что приводит к чрезмерному шуму, вибрации, коррозии и эрозии.