Кулачки распределительного вала: Кулачок распределительного вала — Энциклопедия по машиностроению XXL
Кулачок распределительного вала — Энциклопедия по машиностроению XXL
В аналоговых САУ значе-ния непрерывных сигналов являются непрерывными функциями времени, которые реализуются в виде изменения каких-либо физических элементов. Примерами аналоговых (]АУ являются систему с кулачками, распределительными валами, с устройствами изменения угла сдвига по фазе двух напряжений и т. д. [c.479]Кулачковый командоаппарат. Кулачковые командоаппараты принципиально не отличаются от кулачковых распределительных валов, однако в отличие от них отдельные или все кулачки распределительного вала могут быть использованы для воздействия на переключатели, с помощью которых вводятся в действие сервоприводы отдельных рабочих органов или механизмов. Система командоаппаратов применяется тогда, когда приведение в действие рабочих органов или механизмов машин-автоматов непосредственно от кулачков распределительного вала сопряжено с возникновением значительных усилий, изнашиванием деталей и др.
Рабочий цикл четырехтактного двигателя совершается за два оборота коленчатого вала (рис. 5.10). В крышке цилиндра двигателя расположены клапаны впуска 1 свежего заряда и выпуска 2 продуктов сгорания, форсунки или свечи зажигания и другие устройства. Клапаны удерживаются в закрытом состоянии силой упругости пружин и избыточным давлением в цилиндре. Открытие клапанов в нужные моменты производится с помощью газораспределительного механизма. Этот механизм обычно состоит из рычагов, штанг и толкателей, на которые воздействуют кулачки распределительного вала. Последний приводится в движение от коленчатого вала двигателя и имеет частоту вращения [c.231]
Это относится, например, к зубьям шестерен, кулачкам распределительных валов автотракторных двигателей и другим подвергающимся трению с ударами элементам деталей машин. [c.38]
В практике приходится закаливать детали более сложной геометрии, чем цилиндры. Это могут быть шестерни, валы с модульными шлицами, кулачки распределительных валов, валы топливных насосов, пазовые валы, т. е, тела сложной формы .
[c.31]
Носик кулачка распределительного вала при радиочастотном нагреве значительно опережал пятку и боковые части в нагреве, а при низкой частоте оставался незакаленным, [c.32]
Возвращаясь к конструкции индукторов, рассмотрим четырех-витковый цилиндрический индуктор для одновременной закалки четырех кулачков распределительного вала автомобильного двигателя (рис. 24) [5]. Он представляет собой как бы четыре активных провода одновитковых индукторов, подобных показанному на рис. 19, включенных последовательно и согласно друг с [c.44]
Многолетний опыт закалки кулачков распределительных валов в цилиндрических индукторах, одиночных — для закалки одного кулачка, двухпозиционных, в которых калятся одновременно по одному кулачку на двух валах, с магнитными экранами или без них, показывает, что на равномерность закалки поверхности неблагоприятно сказывается влияние соседних кулачков.
Рис. 39. Макрошлиф поперечного (а) и продольного (б) разрезов кулачков распределительного вала, закаленного в разъемном бесконтактном индукторе. Частота 8 кГц |
В качестве примера на рис. 111, о показана схема механизма подъема шпиндельного барабана токарного многошпиндельного автомата. Барабан 4 поднимается на время его поворота (До = = 0,25- -0,3 мм),чтобы не изнашивались его постоянные опоры 5, являющиеся базовыми поверхностями. Подъем осуществляется от кулачка распределительного вала /, который, действуя на подшипник 2, приподнимает колодку 3 и фланец шпиндельного барабана 4. Ось подшипника и подъемной колодки помещена на качающемся рычаге 7. Функциональное назначение данного механизма состоит в подъеме барабана на такую величину, чтобы он отходил от своих постоянных опор 5.

Рис. 10-13. Индуктор для закалки шеек и кулачков распределительного вала с экранами из магнитопроводов и короткозамкнутых витков |
III. На позиции выгрузки захваты конвейера разжимаются, и завернутый пакет скатывается в лоток. Управление всеми движениями осуществляется через рычаги от кулачков распределительного вала, приводимого во вращение электродвигателем через червячный редуктор. При этом все рабочие движения осуществляются от пружин, а отвод механизмов — кулачками.
[c.470]
Пуансон движется к подшипнику и заталкивает сформированную часть бумаги в отверстие подшипника (положение IV). После возвращения толкателя в исходное положение изделие выгружается в лоток. Привод движения всех механизмов осуществляется от кулачков распределительного вала. [c.473]
На рисунке 19 показаны три положения кулачка распределительного вала автомобиля. Слева изображено состояние, при котором кулачок начинает поднимать клапан для впуска рабочей смеси в цилиндр. В середине — положение наибольшего открывания клапана. При дальнейшем повороте кулачка клапан под действием пружины будет опускаться и закрывать отверстие, где проходят газы, В правом положении кулачок повернулся настолько, что клапан почти закрыл отверстие. Как видно на рисунке, подъем клапана происходит при повороте кулачка примерно на 90°, а в продолжение около половины оборота клапан закрыт и не пропускает газы и горючую смесь.
[c.40]
Высокочастотная поверхностная закалка применяется для весьма обширной номенклатуры деталей (шейки коленчатых валов, кулачки распределительных валов, гильзы цилиндров двигателей внутреннего сгорания, зубья различных шестерён, валики, пальцы гусеничных траков, шпиндели и направляющие различных станков и многие другие детали) [1].
Кулачные шайбы 57 расположены таким образом, что сначала при вращении штурвала 3 шатуны 36 отводят ролики от кулачков распределительного вала 28, затем происходит продольная передвижка этого вала и, наконец, шатуны 36 вновь подводят ролики уже к другому комплекту кулачков. [c.343]
За этот период клапанные рычаги сначала продолжают подниматься, а затем возвращаются в положение, соответствующее началу этого периода. Наконец, во время поворота на последние 120° толкатели клапанов и топливных насосов опускаются на кулачки распределительного вала. Для фиксирования валика 5в крайних положениях служит стопор 12, входящий в вырез шайбы 13.
Детали двигателя смазываются под давлением и масляным туманом. Коренные и шатунные подшипники, подшипники распределительного вала, оси коромысел клапанов, упорный фланец и рабочие поверхности кулачков распределительного вала, шестерни привода смазочного насоса и распределителя зажигания, ведомая звездочка и цепь привода механизма газораспределения смазываются под давлением. [c.36]
Шеек и кулачков распределительных валов 0,32 30 0,8 [c.92]
Если колебания числа оборотов или нагрузки происходят только при определенном положении сервомотора и регулирующих клапанов, то причиной этого обычно являются неправильное парораспределение — слишком малая перекрыта какого-либо регулирующего клапана, отрыв клапана, попадание постороннего предмета под клапан, износ или неправильный профиль кулачка распределительного вала, большой износ ролика или его пальца у регулирующего клапана, местное заедание в распределительном вале, в поршне или штоке сервомоторов, в каком-либо регулирующем клапане паровое усилие под регулирующий клапан при значительном ослаблении или изломе пружины регулирующего клапана, при неисправном регуляторе давления пара (противодавления), при местной неисправности регулирования работающей в параллели более мощной турбины и др.
Основными причинами повышения числа оборотов турбины при сбросе полной нагрузки могут быть большая неравномерность 6 регулирования, т. е. большое сжатие (натяжение) пружин регулятора скорости большая нечувствительность регулирования в результате значительных заеданий или большого мертвого хода (слабины) в органах регулирования отставание роликов клапанов от своих кулачков распределительного вала повышенное трение штока стопорного клапана неплотное закрытие регулирующих клапанов и протечка через них пара из паропровода и паровой коробки регулирующих клапанов после стопорного клапана неплотное закрытие обратных клапанов на регенеративных отборах пара от турбины недостаточный запас хода муфты регулятора скорости на закрытие клапанов большой ход синхронизатора на увеличение числа оборотов недостаточное давление масла в системе регулирования большие зазоры между поршнем (или лопастью) и цилиндром сервомотора, т. е. малая мощность сервомотора недостаточное сечение окон в буксе золотника сервомотора для слива масла неправильная установка ограничителей хода (упоров) в сервомоторе большая частота тока сети и др.
Основными причинами повышения числа оборотов турбины при сбросе полной нагрузки могут быть большая неравномерность 6 регулирования, большая нечувствительность регулирования в результате значительного трения или люфтов в органах регулирования отставание роликов клапанов от своих кулачков распределительного вала неплотное закрытие обратных клапанов на регенеративных отборах пара от турбины недостаточный запас хода муфты регулятора скорости на закрытие клапанов большой ход синхронизатора на увеличение числа оборотов недостаточное давление масла в системе регулирования большие зазоры между поршнем (или лопастью) и цилиндром сервомотора, т. е. малая мощность сервомотора недостаточное сечение окон в буксе зо- [c.97]
Наличие на ремонтных предприятиях ленточно-полировального устройства позволяет расширить область применения финишной обработки при восстановлении различных деталей — поршневых пальцев, опорных шеек и кулачков распределительных валов, поверхностей цилиндрических деталей, контактирующих с сальниками, штоков гидравлических цилиндров и др.
[c.340]
Алмазное выглаживание при восстановлении деталей автомобилей можно рекомендовать в качестве финишной операции при обработке опорных шеек и кулачков распределительных валов, крестовин кардана, валика ротора [c.341]
В механизме газораспределения с верхним расположением клапанов клапан 5 (рис. 7, б) находится над цилиндром. Он состоит из тарелки и стержня. На тарелке выполнен конусный поясок, который при закрытом клапане плотно прижат пружиной к седлу 6, имеющему также конусную поверхность. Когда вращающийся кулачок 9 (рис. 7, а) приподнимает толкатель 8, регулировочный болт 4 упирается в стержень клапана, клапан отходит от седла и сообщает цилиндр с»впускным или выпускным каналом. Кулачок распределительного вала приводится во вращение от коленчатого вала 3 шестернями 1 м 2. Так как в течение одного рабочего цикла в четырехтактном двигателе за два оборота коленчатого вала необходимо открыть каждый клапан один раз, то передаточное число привода равно 2 1. Когда выступ кулачка сходит с толкателя, пружина 7 плотно прижимает клапан к седлу, обеспечивая тем самым герметичность внутренней полости цилиндра. Каждый клапан поднимается своим кулачком. Клапанам приходится работать в условиях высоких температур. Поэтому для обеспечения плотной посадки клапана на седло необходимо, чтобы на прогретом двигателе в деталях привода был небольшой зазор. Для изменения этого зазора, называемого тепловым, в механизмах газораспределения имеются регулировочные устройства.
[c.31]
Одновременный способ используется, когда мощность генератора достаточна для нагрева всей детали или ее части, подлежащей закалке. При одновременном способе, меняя зазор к и ширину индуктирующего провода или применяя магнитопроводы, можно добиться требуемого распределения температуры даже при закалке тел сложной формы, таких как кулачки распределительных валов, конические детали и т. п. Ширина индуктирующего провода при нагреве всей детали или отдельного ее элемента берется примерно равной ширине нагреваемой зоны. Если нагревается участок детали, то ширина провода берется на 10—20% большей ширины участка, что позволяет компенсировать теплоотвод в соседние зоны и ослабление магнитного поля у краев индуктора. Индукторы для одновременного нагрева обычно не имеют поетоянного охлаждения индуктирующего провода. Тепло, выделяющееся в индукторе во время нагрева, аккумулируется медью индуктирующего провода, толщина которого выбирается из условия нагрева до температуры не свыше 250 °С. Это требование обычно выполняется, если принять == (2,5- 4,0) % при средних частотах н = 5- 6 мм при частотах раднодиапазона. Накопленное тепло уносится закалочной водой, подаваемой на закаливаемую поверхность через отверстия в индукторе. Время охлаждения обычно превышает время нагрева.
[c.178]
На рис. 25 представлен профильный многопоэиционнын разъемный бесконтактный с трансформаторной связью между разъемными частями индуктор для закалки кулачков распределительного вала , разработанный во ВНИИ ТВЧ им.

Такой же инду зазор между полуобмотками и поверх- [c.168]
Технология упрочнения разработана также и для поверхностей кулачков распределительного вала двухтактных двигателей внутреннего сгорания (рис. 85). Ввиду того, что площадь контактиру- [c.105]
Примером может служить легко отличимый на слух стук толкателей клапанов автодвигателя, для выяснения причин которого необходимо проверить зазор между толкателями и клапанами, правильность профиля кулачков распределительного вала и т. п. [c.629]
Технологические роторы для обработки инструментом содержат систему исполнительных органов, оснащенных технологическими инструментами, расположенными равномерно по начальной окружности ротора и перемещающимися по замкнутой траектории — окружности ротор, состоящий из сплошного или полого центрального вала, дисков блокодержателя с механизмами крепления инструментальных блоков систему ползунов, являющихся подвижными элементами привода рабочего движения исполнительных органов неподвижные элементы системы привода технологических движений, выполняющие функции кулачков распределительного вала в автоматах систему передачи транспортного, обычно вращательного, движения ротору через зубчатый или червячный редуктор систему управления технологическими движениями инструментов систему наблюдения и контроля правильности функционирования механизмов технологического ротора и состояния потока обрабатываемых деталей.
[c.296]
Привод механизмов подналадчика осуществляется электродвигателем 75 через редуктор /4 и распределительный вал /б. После включения электродвигателя от реле времени подналадчик работает в сле-дующвй последовательности. Быстрый отвод прутка с помощью поджима его роликом 9, перемещающимся от кулачка распределительного вала, к непрерывно вращающемуся (в пределах цикла) ролику б с целью создания разрыва между контролируемым и следующим за ним обрабатываемым прутком. Отвод прутка осуществляется так, что [c.250]
Двигатель Дженерал Моторе (фиг. 2) имеет щелевую продувку и клапанный выхлоп. На каждый цилиндр поставлено но четыре клапана, приводимых попарно от двух кулачков распределительного вала. Продувочный воздух подаётся трёхлопастным насосом Рута, приводимым коленчатым валом через зубчатую передачу ротор и корпус насоса алюминиевые лопасти насоса винтовые. Давление [c.501]
Периодически включаемые червячные передачи применяются для поюрота шпиндельных блоков тяжёлых автоматов, где условия работы для мальтийских механизмов слишком тяжелы. Для предотвращения ударов при пуске червяк, сжимая пружину, мокет смещаться вдоль приводного вала. Управление включением и выключением производится кулачками распределительного вала.
[c.98]
Распределительный вал имеет одну скорость ираще-ния в течение всего цикла. Кулачки распределительного вала осуществляют все рабочие и вспомогательные ходы [c.221]
Поверхностная закалка применяется для шеек коленчатых валов, шеек и кулачков распределительных валов, гильз цилиндров, поршневых пальцев двигателей внутреннего сгорания, зубьев шестерен, валиков, шпинделей и направляющих станков, пальцев трака, паровозных параллелей и других деталей, изготовляемых главным образом из углеродистой и низколегированной стали со средним содержанием углерода марок 40, 45, 50, 40Х, 40ХН, 45Х, 40Г, 50Г, 40Г2, 45Г2. [c.676]
Из смазочной магистрали в (см. рис. 3.12) масло по каналам гид подводится к заднему подшипнику распределительного вала 6. Далее масло по кольцевой проточке на опорной шейке распределительного вала и по каналу е поступает к задней опоре и затем во внутреннюю полость оси коро.мысел выпускных клапанов. По каналам н и и масло из оси коромысел выпускных клапанов поступает к передней и средней шейкам распределительного вала. Из кольцевой проточки на передней шейке распределительного вала масло по каналу л поступает к передней опоре и далее во внутреннюю полость оси коромысел впускных клапанов. При вращении распределительного вала 6 и совмещении каждого из четырех каналов з в средней шейке с каналом и в средней опоре оси коромысел выпускных клапанов масло поступает в центральный канал вала. К подшипникам коромысел масло поступает по двум каналам ж. По канала.м к, просверленным в каждом кулачке распределительного вала, масло из центрального капала вала поступает для смазывания рабочих поверхностей кулачка и опорной пятки коромысла клапана.
[c.37]
Для расширения технологических возможностей шлифования в некоторых случаях целесообразно формировать рабочий цикл не только путем распределения припуска и поперечных подач, но также и варьированием частоты вращения шлифовального круга и обрабатываемой детали на этапах чернового и чистового съема. Примером эффективности подобного цикла может служить шлифование кулачков распределительного вала. При профильном шлифовании кулачков максимальную частоту вращения детали ограничивают 45 об/мин, чтобы избежать искажения профиля кулачка. В свою очередь, замедленное вращение детали вынуждает ограничивать скорость круга 35 м/с и уменьшать поперечную подачу, чтобы не вызвать шлифовочных при-жогов и снижения твердости кулачков. В новых станках частота вращения детали и скорость круга на этапе чернового съема увеличена в 2 раза (г = 60 м/с = 90 об/мин), благодаря чему значительно возросла поперечная подача и сократилось время снятия основного припуска. На этапах чистового съема и выхаживания, когда окончательно формируется профиль и качество рабочей поверхности кулачка, частота вращения детали и скорость круга уменьшаются в 2 раза.
[c.387]
Для впуска свежего и выпуска отработанного пара в паровых машинах служит парораспределение. К нему относятся части, непосредственно воздействуюш,ие на открытие и закрытие впуска и выпуска пара (золотники, клапаны и краны), составляюш,ие собственно парораспределение, и части, управляюш,ие их работой, к которым относятся приводные механизмы (коленчатые рычаги, тяги, эксцентрики, кулачки, распределительные валы и пр. ).
[c.226]
Дефектовка распределительного вала
Среди деталей двигателя именно распределительный вал Имеет кулачки, которые при вращении вала взаимодействуют с толкателями и обеспечивают выполнение машиной (двигателем) операций (процессов) по заданному циклу. является своеобразным «диспетчером» – он отвечает за порядок и продолжительность открывания клапанов. Если распредвал окажется сильно изношенным, двигатель не будет развивать полную мощность. А выход распредвала из строя, как правило, приводит к дорогому ремонту, вплоть до замены головки блока, клапанов и даже ремонта блока цилиндров. Грамотная дефектовка распределительного вала сбережёт немало времени и сил при ремонте.
Дефект 1. Сильный износ, задиры и царапины на поверхностях опорных шеек распределительного вала.
Причины:
- Работа двигателя с недостаточным давлением в системе смазки.
- Работа двигателя с недостаточным уровнем масла в картере.
- Работа двигателя на некачественном масле.
- Сильный перегрев, приводящий к разжижению масла.
- Попадание в масло топлива (бензина или дизтоплива), приводящее к разжижению масла.
- Работа двигателя с засоренным масляным фильтром.
- Работа двигателя на грязном масле.
- Большой пробег двигателя.
Действия:
- Капитальный ремонт двигателя. Замена распределительного вала. В некоторых случаях — шлифовка шеек распределительного вала в ремонтный размер и установка утолщённых (ремонтного размера) вкладышей или втулок. Проверка посадочных мест под распределительный вал в головке блока цилиндров или в блоке цилиндров. В некоторых случаях — ремонт посадочных мест под распредвал. Проверка системы смазки, масляного насоса и при необходимости ремонт или замена масляного насоса. Чистка, промывка и продувка масляных каналов блока цилиндров и головки блока. Применение моторного масла надлежащего качества и регулярная, в предписанные производителем сроки, замена моторного масла и фильтра.
Проверка системы охлаждения и при необходимости её ремонт. Проверка и при необходимости ремонт системы питания.
Дефект 2. Сильный износ и задиры на рабочих поверхностях кулачков распределительного вала.
Причины:
- Работа двигателя с недостаточным давлением в системе смазки.
- Работа двигателя с недостаточным уровнем масла в картере.
- Работа двигателя на некачественном масле.
- Сильный перегрев, приводящий к разжижению масла.
- Попадание в масло топлива (бензина или дизтоплива), приводящее к разжижению масла.
- Работа двигателя с засорённым масляным фильтром.
- Работа двигателя на грязном масле.
- Большой пробег двигателя.
- Неотрегулированный зазор в клапанном механизме.
- Дефекты гидрокомпенсаторов.
- Дефекты и повреждения деталей привода клапанов (толкателей, штанг, коромысел).
- Неверно установленные фазы газораспределения.
Действия:
- Замена распределительного вала.
Проверка, регулировка и при необходимости ремонт клапанного механизма. Замена гидрокомпенсаторов. Проверка системы смазки, масляного насоса и при необходимости ремонт или замена масляного насоса. Чистка, промывка и продувка масляных каналов блока цилиндров и головки блока. Применение моторного масла надлежащего качества и регулярная, в предписанные производителем сроки, замена моторного масла и фильтра. Проверка системы охлаждения и при необходимости её ремонт. Проверка и при необходимости ремонт системы питания.
Дефект 3. Прогиб распределительного вала.
Во всех вышеизложенных случаях обязательно проверяйте изгиб распределительного вала. Распределительный вал укладывается на призмы, установленные на металлической плите. С помощью стрелочного индикатора, установленного на стойке, проверяем прогиб опорных шеек, вращая распред вал рукой. Изгиб не должен превышать: для легковых моторов 0,05 мм; для грузовых моторов 0,1 мм. При большем прогибе распредвал подлежит замене!
Дефект 4. Трещины распредвала.
Причины:
- Попадание в цилиндр посторонних предметов.
- Разрушение ремня или цепи привода газораспределительного механизма.
- Неверно установленные фазы газораспределения.
Действия:
- При наличии трещин распределительный вал ремонту не подлежит! Замена распредвала.
Примечание: Как правило, в результате описанных причин происходит соударение поршней и клапанов. Через детали привода клапанов энергия ударов передается распредвалу, что может привести к образованию трещин. В большинстве случаев трещины приводят к поломке распредвала прямо во время работы двигателя.
Дефект 5. Выработка и царапины на поверхности под сальники распределительного вала.
Причины:
- Длительная работа двигателя.
- Попадание посторонних частиц в моторное масло.
- Неаккуратное обращение с распредвалом при замене сальников на двигателе.
Действия:
- При наличии незначительных царапин возможна шлифовка поверхностей под сальники.
При наличии незначительной выработки устанавливаются новые сальники с небольшим осевым смещением. В противном случае — замена распредвала.
Дефект 6. Разрушение шпоночных пазов и посадочных мест под установочные штифты, а также под шкивы или шестерни привода распредвала.
Причины:
- Неправильная затяжка болтов, крепящих шкивы или шестерни.
- Биение шкивов или шестерён.
- Последствия аварии, при которой произошла деформация моторного отсека.
Действия:
- Замена распредвала.
Дефект 7. Разрушение резьбы в крепёжных отверстиях.
Причины:
- Неправильная затяжка крепёжных болтов.
Действия:
- Замена распредвала.
Типы грм. Назначение и характеристика 8 привод распределительного вала назначение и типы
Распределительный вал и его привод
Распределительный вал обеспечивает своевременное открытие и закрытие клапанов. Вал имеет впускные Г и выпускные Б кулачки, опорные шейки Л, шестерню Д для привода масляного насоса и распределителя системы зажигания и эксцентрик В для привода топливного насоса в карбюраторных двигателях.
Рис. 1. Типы распределительных валов
Вал штампуют из стали; кулачки и шейки его подвергают термической обработке для получения повышенной износостойкости, после чего шлифуют. Кулачки изготовляют как одно целое с валом. Применяют также литые чугунные распределительные валы.
Для каждого цилиндра у четырехтактных двигателей имеются два кулачка: впускной и выпускной. Форма (профиль) кулачка обеспечивает плавный подъем и опускание клапана и соответствующую продолжительность его открытия. Одноименные кулачки располагают в рядном четырехцилиндровом двигателе под углом 90° (рис. 1, а), в шестицилиндровом — под углом 60° (рис. 1, б). Разноименные кулачки устанавливают под углом, величина которого зависит от фаз газораспределения. Вершины кулачков располагаются в принятом для двигателя порядке работы с учетом направления вращения вала. По длине вала впускные и выпускные кулачки чередуются в соответствии с расположением клапанов.
В V-образных двигателях расположение кулачков на общем для обеих секций блока распределительном валу зависит от чередования тактов в цилиндрах, угла развала и принятых фаз газораспределения. Распределительный вал У-образного восьмицилиндрового карбюраторного двигателя показан на рис. 1, в.
В двухтактных дизелях (ЯАЗ -М204 и ЯАЗ -М206) для каждого цилиндра имеется по два выпускных кулачка, обращенных вершинами в одну сторону, и по одному кулачку, управляющему работой насос-форсунки.
При нижнем расположении распределительного вала его устанавливают в картере на опорах, представляющих собой отверстия в стенках и перегородках картера, в которые запрессованы стальные тонкостенные биметаллические или триметаллические втулки. Вал устанавливают иногда также в специальных вкладышах. Число опор распределительного вала для двигателей разных типов различно.
Осевые перемещения распределительного вала у большинства двигателей ограничиваются упорным фланцем (рис. 2), закрепленным на блоке и расположенным с определенным зазором между торцом передней шейки вала и ступицы шестерни; зазор между опорным фланцем и торцом шейки вала устанавливают для двигателей разных марок в пределах 0,05- 0,2 мм; величина этого зазора определяется толщиной распорного кольца, закрепленного на валу между торцом шейки и ступицей шестерни. У двухтактных дизелей ЯМЗ
осевые перемещения вала ограничиваются бронзовыми упорными шайбами, установленными по обеим сторонам переднего подшипника.
Распределительный вал приводится во вращение от коленчатого вала с помощью зубчатой или цепной передачи. При зубчатой передаче на конце коленчатого и распределительного валов закрепляют распределительные шестерни.
Для повышения бесшумности и плавности работы шестерни изготовляют с косыми зубьями; шестерню распределительного вала обычно делают из пластмассы — текстолита, а шестерню коленчатого вала — из стали.
При цепной передаче, обеспечивающей большую бесшумность работы (автомобили ЗИЛ -111), на конце коленчатого вала и на конце распределительного вала закрепляются звездочки, соединенные стальной гибкой бесшумной цепью. Зубья цепи входят в зацепление с зубьями звездочек.
Рис. 2. Типы приводов распределительного вала: а — зубчатая передача; б — цепная передача
Распределительные шестерни или звездочки при сборке устанавливают одну относительно другой по меткам, имеющимся на их зубьях.
На новых моделях двигателей получает применение верхнее расположение распределительного вала (на головке блока). Привод вала осуществляется цепной передачей (автомобиль «Москвич-412»).
Газораспределительный механизм обеспечивает своевременное поступление в цилиндры двигателя горючей смеси (или воздуха) и выпуск отработавших газов.
Двигатели могут иметь нижнее расположение клапанов (ГАЗ -52, ЗИЛ -157К, ЗИЛ -1Э0К), при котором клапаны размещены в блоке цилиндров, и верхнее (ЗМЗ -24, 3M3-S3, ЗИЛ -130, ЯМЗ -740 и др.), когда они расположены в головке цилиндров.
При нижнем расположении клапанов усилие от кулачка распределительного вала передается клапану или через толкатель. Клапан перемещается в направляющей втулке, запрессованной в блок цилиндров. Закрытие клапана осуществляется пружиной, упирающейся в блок и шайбу, закрепленную двумя сухариками на конце стержня клапана.
При верхнем расположении клапанов усилие от кулачка распределительного вала передается толкателю, штанге, коромыслу и клапану. Преимущественно применяется верхнее расположение клапанов, так как такая конструкция позволяет получить компактную камеру сгорания, обеспечивает лучшее наполнение цилиндров, уменьшает потери тепла с охлаждающей жидкостью и упрощает регулировку клапанных зазоров.
Распределительный вал обеспечивает своевременное открытие и закрытие клапанов. Изготовляют его из стали или чугуна.
При сборке распределительный вал вставляют в отверстие торца картера двигателя, поэтому диаметры опорных шеек последовательно уменьшаются, начиная с передней шейки. Количество опорных шеек обычно равно количеству коренных подшипников коленчатого вала. Втулки 8 опорных шеек изготовляют из стали, бронзы (ЯМЗ -740) или из металлокерамики.
Внутреннюю поверхность стальных втулок заливают слоем баббита или сплава СОС -6-6.
На распределительном валу расположены кулачки, воздействующие на толкатели; шестерня привода масляного насоса и прерывателя-распределителя; эксцентрик привода топливного насоса. Кулачков имеется по два на каждый цилиндр. Углы их взаимного расположения зависят для одноименных кулачков — от числа цилиндров и чередования рабочих ходов в разных цилиндрах, для разноименных — от фаз газораспределения. Кулачки и шейки стальных распределительных валов подвергают закалке токами высокой частоты, а чугунных — отбеливанию. Кулачкам при шлифовании придают небольшую конусность, что в сочетании со сферической формой торца толкателей обеспечивает поворот толкателя во время работы.
Рис. 3. Газораспределительный механизм с нижним расположением клапанов: а-схема, 6—детали; 1-распределительный вал, 2 — толкатель, 3- контргайка, 4- регулировочный болт, 5-сухарики, б — упорная. шайба пружины, 7- пружина клапана, 8—выпускной клапан, 9- направляющая втулка клапана, 10 — вставное седло выпускного клапана, 11 — впускной клапан
Между шестерней распределительного вала и передней опорной шейкой установлены распорная шайба и упорный фланец, который привертывается болтами к блоку цилиндров и удерживает вал от осевых перемещений.
Распределительный вал получает вращение от коленчатого вала. В четырехтактных двигателях рабочий цикл происходит за два оборота коленчатого вала. За этот период впускные и выпускные клапаны каждого цилиндра должны открываться один раз, а следовательно, распределительный вал должен повернуться на один оборот. Таким образом, распределительный вал должен вращаться в два раза медленнее коленчатого вала. Поэтому шестерня распределительного вала имеет в два раза больше зубьев, чем шестерня на переднем конце коленчатого вала. Шестерня коленчатого вала стальная, шестерня на распределительном валу чугунная (ЗИЛ -130) или текстолитовая (ЗМЗ -24, 3M3-53). Зубья у шестерен косые.
Рис. 4. Газораспределительный механизм с верхним расположением клапанов (ЗИГМЗО ): 1 — шестерня распределительного вала, 2 — упорный фланец, 3 — распорное кольцо, 4-опорные шейки, 5-эксцентрик привода топливного насоса, 6 — кулачки выпускных клапанов, 7 — кулачки впускных клапанов, 8- втул-ки, 9 — впускной клапан, 10 — направляющая втулка, 11-упорная шайба, 12 — пружина, 13 — ось коромысел, 14 — коромысло, 15 — регулировочный винт, 16-стойка оси коромысел, 17 — механизм поворота выпускного клапана, 18 — выпускной клапан, 19 — штанга, 20-толкатели, 21 — шестерня привода масляного насоса и прерывателя-распределителя
Распределительные шестерни двигателя ЯМЗ
-740 расположены на заднем торце блока цилиндров.
Распределительные шестерни входят в зацепление между собой при строго определенном положении коленчатого и распределительного валов. Это достигается совмещением меток на зубе одной шестерни и впадине между зубьями другой шестерни.
В высокооборотных двигателях («Москвич-412», ВАЗ -2101 «Жигули») распределительный вал располагается в головке цилиндров и его кулачки воздействуют непосредственно на коромысла, которые, поворачиваясь на осях, открывают клапаны. В таком клапанном механизме нет толкателей и штанг, упрощается отливка блока цилиндров, снижается шум при работе.
Ведомая звездочка распределительного вала приводится во вращение втулочно-роликовой цепью от ведущей звездочки коленчатого вала. Устройство для натяжения цепи имеет звездочку и рычаг.
Рис. 5. Газораспределительный механизм с верхним расположением распределительного вала («Москвич-412»): а- газораспределительный механизм, б — привод газораспределительного механизма; 1 — наконечник клапана, 2 — ось коромысел выпускных клапанов, 3,6 — коромысла, 4 — распределительный вал, 5 — ось коромысел впускных клапанов, 7 — контргайка, 8 — регулировочный винт, 9 — головка цилиндров, 10 — клапаны, 11 — ведущая звездочка, 12-звездочка натяжного устройства, 13 — рычаг, 14 — ведомая звездочка, 15 — цепь, 16 — коленчатый вал
К атегория: — Устройство и работа двигателя
Окт 26 2014
Двигатель автомобиля представляет собой сложнейший механизм, одним из важнейших элементов которого является распределительный вал, входящий в состав ГРМ. От точной и бесперебойной работы распределительного вала во многом зависит нормальная работа двигателя.
Одну из самых важных функций в работе двигателя автомобиля выполняет распределительный вал, который является составной частью газораспределительного механизма (ГРМ). Распредвал обеспечивает впуск-выпуск тактов работы двигателя.
В зависимости от того, каково устройство двигателя, газораспределительный механизм может иметь нижнее или верхнее расположение клапанов. На сегодняшний день чаще встречаются ГРМ с верхним расположением клапанов.
Такая конструкция позволяет ускорить и облегчить процесс обслуживания, включающий регулировку и ремонт распределительного вала, для которого потребуются запчасти на распредвал.
Устройство распределительного вала
С конструктивной точки зрения распределительный вал двигателя связан с коленвалом, что обеспечивается благодаря наличию цепи и ремня. Цепь или ремень распределительного вала надеваются на звездочку коленчатого вала или на шкив распредвала.
Такой шкив распредвала, как разрезная шестерня, считается наиболее практичным и эффективным вариантом, поэтому достаточно часто используется для тюнинга двигателей с целью увеличения их мощности.
Подшипники, внутри которых происходит вращение опорных шеек распредвала, располагаются на головке блока цилиндров. Если крепления шеек выходят из строя, для их ремонта используют ремонтные вкладыши распределительного вала.
Для того чтобы избежать осевого люфта, в конструкцию распределительного вала входят специальные фиксаторы. Непосредственно по оси вала проходит сквозное отверстие, предназначенное для смазки трущихся деталей. Это отверстие закрывается сзади при помощи специальной заглушки распределительного вала.
Важнейшей составной частью распредвала являются кулачки, количество которых указывает на количество впускных-выпускных клапанов. Кулачки отвечают за выполнение основной функции распределительного вала — регулирование фаз газораспределения двигателя и регулирование порядка работы цилиндров.
Каждый клапан оснащен кулачком. Кулачок набегает на толкатель, способствуя открыванию клапана. После того, как кулачок сходит с толкателя, мощная возвратная пружина обеспечивает закрывание клапана.
Кулачки распределительного вала находятся между опорными шейками. Газораспределительную фазу распредвала, зависящую от числа оборотов двигателя и от конструкции впускных-выпускных клапанов, определяют опытным путем. Подобные данные для конкретной модели двигателя можно найти в специальных таблицах и диаграммах, которые специально составляет производитель.
Как работает распределительный вал?
Конструктивно распредвал располагается в развале блока цилиндров. Зубчатая или цепная передача коленвала приводит в действие распредвал.
Когда распределительный вал вращается, кулачки оказывают воздействие на работу клапанов. Данный процесс будет происходить правильно только в случае строгого соответствия с порядком работы цилиндров двигателя и с фазами газораспределения.
Для того чтобы были установлены соответствующие фазы газораспределения, на приводной шкив или на распределительные шестерни наносятся специальные установочные метки. Кроме этого, необходимо, чтобы кулачки распределительного вала и кривошипы коленчатого вала находились в строго определенном положении по отношению друг к другу.
Когда установка производится по меткам, удается достичь соблюдения правильной последовательности тактов — порядка работы цилиндров двигателя, который, в свою очередь, зависит от расположения самих цилиндров, а также от особенности конструкции коленчатого и распределительного валов.
Рабочий цикл двигателя
Рабочим циклом двигателя называется период, за время которого впускной и выпускной клапаны открываются по одному разу. Как правило, период проходит за два оборота коленвала. За это время распределительный вал, шестерня которого имеет в два раза больше зубьев, чем шестерня коленчатого вала, делает один оборот.
Количество распределительных валов в двигателе
На количество распредвалов непосредственно влияет конфигурация двигателя. Двигатели, которые отличаются рядной конфигурацией, а также имеют одну пару клапанов на цилиндр, оснащаются одним распределительным валом. Если для каждого цилиндра предусмотрено по четыре клапана, двигатель оборудуется двумя распредвалами.
Двигатели оппозитные и V-образные отличаются наличием одного распредвала в развале либо имеют два распределительных вала, каждый из которых находится в головке блока. Бывают и исключения из общепринятых правил, связанные в первую очередь с конструктивными особенностями двигателя.
1. Подкатной гидравлический домкрат. Штатный домкрат автомобиля ваз 2107 часто или неудобен, или просто бесполезен при выполнении некоторых работ.
2. Опора под автомобиль, регулируемая по высоте и с допустимой нагрузкой не менее 1т. Желательно иметь четыре такие подставки.
3. Противооткатные упоры (не менее 2шт.).
4. Двухсторонние ключи для штуцеров
тормозной системы на 8, 10 и 13мм. Наиболее распространены два типа
таких ключей: зажимной ключ и накидной
ключ с прорезью. Зажимной ключ позволяет
отворачивать штуцеры с изношенными
гранями. Чтобы надеть ключ на штуцер
тормозной трубки, необходимо вывернуть
стяжной болт. Накидной ключ с прорезью
позволяет более оперативно выполнять
работу, однако такой ключ должен быть
изготовлен из качественной стали с
соответствующей термической обработкой.
5. Специальные щипцы для снятия стопорных колец. Существует два типа таких щипцов: сдвижные — для извлечения стопорных колец из отверстий, и раздвижные — для снятия стопорных колец с валов, осей, тяг. Щипцы также бывают с прямыми и изогнутыми губками.
6. Съемник масляного фильтра.
7. Универсальный двухзахватный съемник для снятия шкивов, ступиц, шестерней.
8. Универсальные трехзахватные съемники для снятия шкивов, ступиц, шестерен.
9. Съемник карданного шарнира.
10. Съемник и оправка для замены маслосъемных колпачков.
11. Рассухариватель для разборки
клапанного механизма головки блока
цилиндров.
12. Приспособление для снятия шаровых опор.
13. Приспособление для извлечения поршневого пальца.
14. Приспособление для выпрессовки и запрессовки сайлентблоков рычагов передней подвески.
15. Приспособление для снятия рулевых тяг.
16. Ключ храповика коленчатого вала.
17. Съемник пружин.
18. Ударная отвертка с набором насадок.
19. Цифровой мультиметр для проверки параметров электрических цепей.
20. Специальный щуп или контрольная лампа на 12В для проверки электрических цепей автомобиля ваз 2107, находящихся под напряжением.
21. Манометр для проверки давления в шинах (при отсутствии манометра на шинном насосе).
22. Манометр для измерения давления
в топливной рампе двигателя.
23. Компрессометр для проверки давления в цилиндрах двигателя.
24. Нутромер для измерения диаметра цилиндров.
25. Штангенциркуль с глубиномером.
26. Микрометры с пределом измерений 25-50 мм и 50-75 мм.
27. Набор круглых щупов для проверки зазора между электродами свечей зажигания. Можно использовать комбинированный ключ для обслуживания системы зажигания с набором необходимых щупов. Ключ имеет специальные прорези для подгибания бокового электрода свечи зажигания.
28. Набор плоских щупов для измерения зазоров при оценке технического состояния агрегатов.
29. Широкий щуп 0,15мм для проверки зазоров в клапанном механизме.
30. Оправка для центрирования ведомого диска сцепления.
31. Оправка для обжима поршневых колец при установке поршня в цилиндр.
32. Ареометр для измерения
плотности жидкости (электролита в
аккумуляторной батарее или антифриза
в расширительном бачке).
33. Специальное приспособление с металлическими щетками для очистки клемм проводов и выводов аккумуляторной батареи.
34. Масляный шприц для заливки масла в коробку передач и задний мост.
35. Нагнетательный шприц для смазки шлицов карданного вала.
36. Шланг с грушей для перекачки топлива. Шланги можно использовать для удаления топлива из бака перед его снятием.
37. Медицинский
шприц или груша для отбора жидкостей
(например, при необходимости снятия
бачка главного тормозного цилиндра
без слива всей тормозной жидкости из
системы). Шприц также незаменим для
чистки деталей карбюратора.При
выполнении ремонтных работ на автомобиле
ваз 2107 могут также потребоваться: технический фен (термопистолет),
электродрель с набором сверл по
металлу, струбцина, пинцет, шило,
рулетка, широкая слесарная линейка,
бытовой безмен, широкая емкость для
слива масла и охлаждающей жидкости
объемом не менее 10л.
Расположение данного механизма целиком зависит от конструкции ДВС, поскольку в некоторых моделях распредвал размещается внизу, в основании блока цилиндров, а в других – вверху, прямо в головке блока цилиндров. На данный момент оптимальным считается верхнее расположение распредвала, поскольку это существенно упрощает сервисный и ремонтный доступ к нему. Распредвал напрямую связан с коленвалом. Они соединяются между собой цепной или ременной передачей посредством обеспечения связи между шкивом на валу ГРМ и звездочкой на коленвале. Это необходимо потому, что приводится в движение распредвал именно коленвалом.
Устанавливается распределительный вал в подшипники, которые в свою очередь надежно закрепляются в блоке цилиндров. Осевой люфт детали не допускается за счет применения в конструкции фиксаторов. Ось любого распредвала имеет сквозной канал внутри, через который осуществляется смазка механизма. Сзади данное отверстие закрыто заглушкой.
Важными элементами являются кулачки распредвала. По количеству они соответствуют числу клапанов в цилиндрах. Именно эти детали выполняют основную функцию ГРМ – регулирование порядка работы цилиндров.
На каждый клапан приходится отдельный кулачок, открывающий его через нажим на толкатель. Освобождая толкатель, кулачок позволяет распрямиться пружине, возвращающей клапан в закрытое состояние. Устройство распределительного вала предполагает наличие двух кулачков для каждого цилиндра – по числу клапанов.
Следует отметить, что от распределительного вала также осуществляется привод топливного насоса и распределителя масляного насоса.
Принцип действия и устройство распредвала
Распределительный вал соединяется с коленвалом при помощи цепи или ремня, надетого на шкив распредвала и звездочку коленчатого вала. Вращательные движения вала в опорах обеспечивают специальные подшипники скольжения, благодаря этому вал воздействует на клапана, запускающие работу клапанов цилиндров. Этот процесс происходит в соответствии с фазами образования и распределения газов, а также рабочим циклом двигателя.
Установка фаз распределения газов происходит согласно установочным меткам, которые имеются на шестернях или шкиве. Правильная установка обеспечивает соблюдение последовательности наступления рабочих циклов двигателя.
Основной деталью распредвала являются кулачки. При этом количество кулачков, которыми оснащается распредвал, зависит от количества клапанов. Основное назначение кулачков – осуществление регулировки фаз процесса газообразования. В зависимости от типа конструкции ГРМ кулачки могут взаимодействовать с коромыслом или толкателем.
Кулачки устанавливаются между опорными шейками, по два на каждый цилиндр двигателя. Распредвалу во время работы приходится преодолевать сопротивление пружин клапанов, которые служат возвратным механизмом, приводя клапана в исходное (закрытое) положение.
На преодоление этих усилий расходуется полезная мощность двигателя, поэтому конструкторы постоянно думают, как можно уменьшить потери мощности.
Для того чтобы уменьшить трение между толкателем и кулачком, толкатель может оснащаться специальным роликом.
Помимо этого, разработан специальный десмодромный механизм, в котором реализована беспружинная система.
Опоры распределительных валов оснащены крышками, при этом передняя крышка является общей. Она имеет упорные фланцы, которые соединяются с шейками валов.
Распредвал изготавливается одним из двух способов – ковкой из стали или литьем из чугуна.
Поломки распредвала
Существует довольно много причин, по которым в работу двигателя вплетается стук распредвала, что свидетельствует о появлении проблем с ним. Вот только наиболее типичные из них:
Распределительный вал требует должного ухода: замену сальников, подшипников и периодичной дефектовке.
- износ кулачков, что ведет к появлению стука сразу только при запуске, а потом и все время работы двигателя;
- износ подшипников;
- механическая поломка одного из элементов вала;
- проблемы с регулировкой подачи топлива, из-за чего возникает асинхронность взаимодействия распредвала и клапанов цилиндров;
- деформация вала, ведущая к осевому биению;
- некачественное моторное масло, изобилующее примесями;
- отсутствие моторного масла.
По утверждениям специалистов при возникновении легкого стука распредвала автомобиль может ездить еще не один месяц, но это ведет к усиленному износу цилиндров и других деталей. Поэтому при обнаружении проблемы следует заняться ее устранением. Распредвал – разборный механизм, поэтому ремонт чаще всего осуществляется методом замены его всего или только некоторых элементов, например, подшипников.свобождение камеры от выхлопных газов, имеет смысл начать открывать впускной клапан. Что и происходит при использовании тюнингового распредвала.
ГЛАВНЫЕ ХАРАКТЕРИСТИКИ РАСПРЕДВАЛА
Известно, что среди главных характеристик распредвала конструкторы форсированных двигателей часто используют понятие продолжительности открывания. Дело в том, что именно этот фактор непосредственно влияет на производимую мощность двигателя. Так, чем клапаны дольше открыты, тем мощнее агрегат. Таким образом, получается максимальная скорость двигателя. Например, когда продолжительность открытия составляет больше стандартного показателя, то двигатель сможет выработать дополнительную максимальную мощность, которая будет получаться от работы агрегата на низких оборотах. Известно, что для гоночных автомобилей максимальная скорость двигателя является приоритетной целью. Что касается классических машин, то при их разработке силы инженеров направлены на крутящий момент при низких оборотах и приемистость.
Увеличение мощности может также зависеть от увеличения подъема клапана, которое может прибавить максимальную скорость. С одной стороны, дополнительная скорость будет получаться при помощи короткой продолжительности открывания клапанов. С другой стороны, приводы клапанов имеют не такой простой механизм. Например, при высоких скоростях движения клапанов у двигателя не получится выработать дополнительную максимальную скорость. В соответствующем разделе нашего сайта вы сможете найти статью про основные особенности системы выпуска выхлопных газов. Так, при низкой продолжительности открывания клапана после закрытого положения клапану остается меньше времени, чтобы добраться до исходной позиции. После продолжительность становится еще меньше, что, главным образом, отражается на выработке дополнительной мощности. Дело в том, что в этот момент требуются клапанные пружины, у которых будет как можно больше усилий, что считается невозможным.
Стоит отметить, что сегодня существует понятие надежного и практичного подъема клапана. В этом случае величина подъема должна быть более 12,7 миллиметров, что обеспечит высокую скорость открывания и закрывания клапанов. Продолжительность такта насчитывает от 2 850 оборотов в минуту. Однако такие показатели создают нагрузку на механизмы клапана, что в итоге приводит к недолгой службе клапанных пружин, стержней клапанов и кулачков распредвала. Известно, что вал с высокими показателями скорости подъема клапанов работают без сбоя первое время, например, до 20 тысяч километров. Все же сегодня автопроизводители разрабатывают такие двигательные системы, где распредвал имеет одинаковые показатели продолжительности открывания клапанов и их подъема, что заметно увеличивает их срок службы.
Кроме того, на мощность двигателя влияет такой фактор, как открывание и закрывание клапанов по отношению к положению распредвала. Так, фазы распределения распредвала можно найти в таблице, которая к нему прилагается. Согласно этим данным, можно узнать об угловых положениях распредвала в момент открытия и закрытия клапанов. Все данные обычно берутся в момент поворота коленчатого вала до и после верхней и нижней мертвых точек, указываются в градусах.
Что касается продолжительности открывания клапанов, то она рассчитывает, согласно фазам распределения газа, которые указаны в таблице. Обычно в этом случае нужно суммировать момент открывания, момент закрывания и прибавить 1 800. Все моменты указываются в градусах.
Теперь стоит разобраться с соотношением фаз распределения газа мощности и распредвала. В этом случае представим, что один распредвал будет А, другой – В. Известно, что оба этих вала имеют аналогичные формы впускных и выпускных клапанов, а также схожую продолжительность открывания клапанов, которая составляет 2 700 оборотов. В данном разделе нашего сайта вы сможете найти статью троит двигатель: причины и методы устранения. Обычно такиераспредвалы называются конструкциями с одним профилем. Все же между этими распредвалами есть некоторые отличия. Например, у вала А кулачки расположены так, что впускной открывается за 270 до верхней мертвой точки, а закрывается в 630 после нижней мертвой точки.
Что касается выпускного клапана вала А, то он открывается в 710 до нижней мертвой точки и закрывается за 190 после верхней мертвой точки. То есть, фазы газораспределения выглядят следующим образом: 27-63-71 – 19. Что касается вала В, то у него прослеживается другая картина: 23 o67 — 75 -15. Вопрос: Как валы А и В могут повлиять на мощность двигателя? Ответ: вал А создаст дополнительную максимальную мощность. Все же стоит отметить, что двигатель будет иметь характеристики хуже, кроме того, у него будет прослеживаться более узкая кривая мощности по сравнению с валом В. Сразу стоит отметить, что на такие показатели никак не влияет продолжительность открывания и закрывания клапанов, так как она, как мы отметили выше, одинакова. На самом деле на такой результат влияют изменения в фазах распределения газа, то есть, в углах, находящихся между центрами кулачков в каждом распределительном вале.
Этот угол представляет собой угловое смещение, которое происходит между впускным и выпускным кулачками. Стоит отметить, что в этом случае данные будут указываться в градусах поворота распределительного вала, а не в градусах поворота коленчатого вала, которые указывались ранее. Так, перекрытие клапанов зависит, главным образом, от угла. Например, в момент уменьшения угла между центрами клапанов впускной и выпускной клапаны будут перекрываться больше. Кроме того, в момент увеличения продолжительности открывания клапанов, их перекрытие тоже повышается.
Распределительный вал или попросту распредвал в газораспределительном механизме обеспечивает выполнение основной функции – своевременного открытия и закрытия клапанов, за счет чего производится приток свежего воздуха и выпуск отработавших газов. В общем виде распределительный вал управляет процессом газообмена в двигателе.
Для уменьшения инерционных нагрузок, увеличения жесткости элементов газораспределительного механизма распределительный вал должен располагаться как можно ближе к клапанам. Поэтому стандартное положение распредвала на современном двигателе в головке блока цилиндров – т.н. верхнее расположение распределительного вала .
В газораспределительном механизме используется один или два распределительных вала на ряд цилиндров. При одновальной схеме обслуживаются впускные и выпускные клапаны (два клапана на цилиндр ). В двухвальном газораспределительном механизме один вал обсуживает впускные клапаны, другой – выпускные (два впускных и два выпускных клапана на цилиндр ).
Основу конструкции распределительного вала составляют кулачки . На каждый клапан используется, как правило, один кулачок. Кулачок имеет сложную форму, которая обеспечивает открытие и закрытие клапана в установленное время, и его подъем на определенную высоту. В зависимости от конструкции газораспределительного механизма кулачок взаимодействует либо с толкателем, либо с коромыслом.
При работе распределительного вала кулачки вынуждены преодолевать усилия возвратных пружин клапанов и силы трения от взаимодействия с толкателями. На все это расходуется полезная мощность двигателя. Указанных недостатков лишена беспружинная система, реализованная в десмодромном механизме . Для уменьшения силы трения между кулачком и толкателем плоская поверхность толкателя может заменяться роликом . В отдаленной перспективе использование магнитной системы для управления клапанами, обеспечивающей полный отказ от распределительного вала.
Распределительный вал изготавливается из чугуна (литьем) или стали (ковкой). Распредвал вращается в опорах, которые представляют собой подшипники скольжения. Число опор на одно превышает число цилиндров. Опоры, в основном, разъемные, реже – неразъемные (выполнены как одно целое с головкой блока). В опорах, выполненных в чугунной головке, используются тонкостенные вкладыши, которые при изнашивании заменяются.
От продольного перемещения распредвал удерживают упорные подшипники, располагающиеся около приводной шестерни (звездочки). Распределительный вал смазывается под давлением. Предпочтительным является индивидуальный подвод масла к каждому подшипнику.
Значительно повышается эффективность газораспределительного механизма с использованием различных систем изменения фаз газораспределения , которые позволяют добиться повышения мощности, топливной экономичности, снижения токсичности отработавших газов. Различают несколько подходов к изменению фаз газораспределения:
- поворот распределительного вала на различных режимах работы;
- использования нескольких кулачков с различным профилем на один клапан;
- изменение положения оси коромысла.
Распределительный вал приводится в действие от коленчатого вала двигателя . В четырехтактном двигателе внутреннего сгорания привод обеспечивает вращение коленчатого вала со скоростью в два раза медленнее коленчатого вала.
На двигателях легковых автомобилей привод распределительного вала осуществляется с помощью цепной или ременной передачи. Данные виды привода на равных используются как в бензиновых двигателях, так и дизелях. Ранее для привода использовалась шестеренная передача, но ввиду громоздкости и повышенного шума перестала применяться.
Цепной привод объединяет металлическую цепь, которая обегает звездочки на коленчатом и распределительном валу. Помимо этого в приводе используются натяжитель и успокоитель. Цепь состоит из звеньев, соединенных шарнирами. Одна цепь может обслуживать два распределительных вала.
Цепной привод распределительного вала достаточно надежный, компактный, может использоваться на больших межосевых расстояниях. Вместе с тем, износ шарниров при эксплуатации, приводит к растяжению цепи, последствия которого могут быть самые печальные для ГРМ. Не спасают даже натяжитель с успокоителем. Поэтому цепной привод требует регулярного контроля состояния.
В ременном приводе распределительного вала используется зубчатый ремень, который охватывает соответствующие зубчатые шкивы на валах. Приводной ремень оборудуется натяжным роликом. Ременный привод компактный, почти бесшумный, достаточно надежный, что делает его популярным у производителей. Современные зубчатые ремни имеют значительный ресурс — до 100 тыс. км пробега и более.
Привод распределительного вала может использоваться для привода и других устройств – масляного насоса , топливного насоса высокого давления , распределителя зажигания.
Чем наварить кулачки распредвала
Восстановление (напыление) распредвалов своими руками
О том, что распредвал вашего двигателя требует ремонта или, как минимум диагностики, вы узнаете практически сразу. О неисправности вам подскажут: датчик распредвала и нарушение штатной работы двигателя. Ведь распредвал – это деталь, которая во многом влияет на фазы газораспределения, а значит за стабильную работу цилиндров и т.д.
И, прежде, чем сразу же бросаться в крайность и думать о замене распредвала, его нужно попробовать отремонтировать. Если, конечно, вы уже не задумывались о том, чтобы поменять свой штатный на тюнинговый спортивный распредвал.
Когда речь идёт о такой процедуре, как ремонт распредвала, то своими руками основную процедуру ремонта в гараже вы вряд ли сможете выполнить. Ваша задача, снять головку блока цилиндров и вместе с распредвалом приехать в мастерскую, где возможен ремонт или восстановление распредвалов.
Основные дефекты, при которых требуется восстановление распредвала: биение (деформация) вала, износ кулачков и износ шеек. Не забывайте, для чего мы привозим в мастерскую ГБЦ – дефектовка и, при необходимости ремонт постели распредвала, обязательная комплексная процедура.
Устранение деформации распредвала. Этот дефект устраняется способом поэлементной холодной правки, которая позволяет привести в порядок как стальные, так и чугунные распредвалы.
Биение (изгиб) распредвала устраняют на призмах при помощи пресса. При этом методе естественным образом должны быть учтены допуски производителя распредвала, относительно допустимого биения.
После устранения биения обязательно производится динамическая балансировка. Иначе все усилия были напрасны. Восстановление распредвалов таким методом производится на специальных станках.
Восстановление кулачков распредвала и износ шейки устраняется таким методом, как напыление распредвала либо шлифовкой.
Изношенный кулачок шлифуется до вывода износа и восстановления профиля. Не следует забывать, что после шлифовки кулачка высота подъёма клапана не должна измениться. Иначе будет нарушен процесс фаз газораспределения.
Восстановление кулачков распредвала методом шлифовки, рекомендуется выполнять всего один раз. В противном случае нарушается радиус вершины кулачка, и, соответственно, происходит сбой фазы газораспределения. То есть, следующим этапом, после первого ремонта распредвала, служит замена распредвала.
Для опорных шеек распредвала применяется расточка (шлифовка) до уменьшенных ремонтных размеров. При этом варианте ремонта распредвала, затем применяются втулки. Если же шейки наращивают, то другие детали растачивают под их размер. Для небольшого слоя наращивания применяется осталивание либо хромирование шеек.
Реставрация методом напыления распредвала производится с применением порошковой проволоки многокомпонентного состава (алюминий – цинк). После процедуры напыления распредвала твёрдость покрытия не уступает заводским параметрам. Но, специалисты не рекомендуют проводить ремонт методом напыления более одного раза.
Необходимые параметры после ремонта распредвала
Реставрированный распредвал должен иметь следующие, обязательные параметры:
- допустимая шероховатость поверхности изделия – не ниже 8 класса;
- конусность и овальность элементов распредвала не более 0,01 мм;
- отреставрированные поверхности должны иметь твёрдость НКС 54-62.
Ремонт распредвала сопровождается обязательной заменой на новые, изношенных: роликов, осей, подшипников, втулок толкателей.
Удачи вам при восстановлении распредвала. Не торопитесь покупать новый распредвал, если не собирались этого делать.
Ремонт распределительного вала
Распределительный вал изготовляют из стали 13h4A, поверхность кулачков цементуют на глубину 1,3—2,0 мм. Твердость цементованной поверхности HRC≥58; нецементованной НВ 170.
Возможные неисправности детали следующие: износ шеек, износ поверхности буртика упорной шейки, износ вершины кулачков, износ шлицев, повреждение резьбы, прогиб вала и коррозия.
Технологический процесс ремонта распределительного вала состоит из таких операций:
- шлифования вершин кулачков;
- наплавки кулачков;
- шлифования торцов и профилей кулачков, правки вала;
- шлифования шеек под хромирование;
- хромирования шеек и буртиков;
- шлифования шеек после хромирования;
- полирования;
- оксидирования.
Износ кулачков допускается до размера h — 50 мм (см. рис. 38). Если размер кулачка не выходит за этот предел, то ограничиваются зачисткой вершины кулачка для придания ей плавной закругленной формы. Вблизи вершины кулачка допускаются следы износа шириной до 3 мм.
Кулачки высотой менее 50 мм наплавляют твердым сплавом сормайт № 2. Перед наплавкой вершину кулачка срезают шлифовальным кругом до размера h = 48 мм. Затем деталь укладывают в призмы специальной ванны так, чтобы подлежащий наплавке кулачок выступал над поверхностью зеркала проточной воды на 7— 8 мм (рис. 115). Температура воды должна быть 30—45° С. После этого вершину кулачка подогревают ацетилено-кислородным науглероживающим пламенем с помощью горелки с наконечником № 4. Рис. 115. Схема наплавки кулачка. |
Для наплавки используют прутки диаметром 6 мм, флюсом служит порошок буры или состав с содержанием хлористого натрия. Флюс периодически добавляют в сварочную ванночку. Пруток copмайта помещают под пламенем горелки так, чтобы стекающие капли сормайта покрывали наплавленную поверхность кулачка.
Кулачок, наплавленный сплавом при температуре 870—900° С, быстро погружают в воду, поворачивая вал на 180°.
Разрешается наплавлять не более трех кулачков. Наплавленный слой должен быть плотным, без раковин, пор и трещин. Твердость наплавленного металла должна быть HRC≥48.
После наплавки кулачков вал подвергают отпуску при температуре 200—220° С в течение 30 мин. Затем его правят на призмах под реечным прессом.
При укладке вала 1-й и 6-й шейками в призмы допускается биение рабочих шеек и наружной поверхности шлицев не более 0,07 мм.
Механическую обработку наплавленных кулачков начинают с удаления с помощью шлифовального круга из электрокорунда зернистостью 34—46 и твердостью CM2—C1 наплывов металла на торцовых поверхностях кулачков. Ширина кулачка должна быть 16±0,4 мм. Профильную поверхность кулачка шлифуют кругом из электрокорунда на керамической связке зернистостью 60—80 и твердостью C2—CT1 на специальном профильно-шлифовальном станке по схеме, показанной на рис. 116.
Вал устанавливают в центры и жестко связывают со шпинделем 3, несущим копир 5. Рис. 116. Схема обработки профиля кулачка. |
Для того чтобы сохранить фазы газораспределения при сборке дизеля, не рекомендуется снимать слой металла в местах перехода рабочей части профиля в нерабочую.
Согласно техническим условиям нa регулировку дизеля зазор между затылком кулачка и тарелкой клапана (рис. 117, а) равен 2,34 мм, а расстояние от оси вала до тарелки клапана 20 мм.
Клапан начинает открываться в тот момент, когда точка А1 кулачка коснется тарелки клапана (рис. 117, б) и линия ОА1 будет перпендикулярна плоскости тарелки. Закрытие клапана закончится, когда точка А2 отойдет от тарелки. Рис. 117. Схема работы кулачка: а — кулачок в верхнем положении; б — начало открытия клапана. |
Если ОА1 = 17,66 мм и а = 0,1 мм, то β составит 6°. Следовательно, незначительная ошибка в расположении точки сопряжения боковых дуг профиля с параллельными участками вызывает значительный сдвиг фазы; в этом случае регулировка газораспределения дизеля становится невозможной.
Для того чтобы сохранились правильные фазы распределения, ось симметрии кулачка должна быть параллельна оси копира. Установку кулачка относительно копира производят с помощью стрелочного приспособления (рис. 118). По градуированной шкале копир устанавливают в нулевое (неходное) положение. Затем шкалу 6 приспособления устанавливают основанием 1 на качающийся стол против кулачка, который подлежит шлифованию. Скобу 3 стрелки 5 устанавливают так, чтобы упор 4 коснулся затылка кулачка. Покачиванием скобы на угол, ограничиваемый роликами 2, по шкале прибора определяют величину угла колебания стрелки. Распределительный вал поворачивают относительно неподвижного шпинделя до тех пор, пока стрелка не будет одинаково отклоняться вправо и влево от нулевой линии шкалы. После этого вал жестко связывают со шпинделем станка. Таким образом устанавливают каждую пару шлифуемых кулачков. Рис. 118 Стрелочное приспособление. |
При шлифовании кулачков не рекомендуется устанавливать вал по делительному устройству станка, так как весьма вероятно, что погрешности деления данного станка не совпадают с погрешностями станков, на которых кулачок шлифовался при изготовлении и ремонте; вследствие этого возможен значительный сдвиг фаз.
Точность обработки кулачка также зависит от формы копира, определяемой профилем кулачка и конструктивными элементами станка.
Изношенные шейки вала (диаметром менее 29,85 мм) восстанавливают хромированием. Для того чтобы шейкам придать правильную геометрическую форму, их предварительно шлифуют. Диаметр шеек после шлифования должен быть не менее 29,65 мм; овальность и конусность не более 0,04 мм.
Для шлифования шеек вала рекомендуется круг из корунда на керамической связке зернистостью 46—60, твердостью C2—СT1.
После шлифования гаейки обрабатывают наждачным полотном и промывают бензином. Поверхности, не подлежащие хромированию, изолируют листовым целлулоидом или полихлорвиниловым пластикатом. К одной из средних шеек вала прикрепляют подвесное приспособление, представляющее собой стяжной хомут с крючком. Шейки вала, которые будут хромироваться в первый прием, обезжиривают бензином и кашицей кальциево-магниевой извести. Затем вал промывают холодной проточной водой, подвешивают в ванне для хромирования, декапируют и покрывают блестящим осадком хрома. Толщина хромового покрытия должна быть 0,15—0,20 мм. После промывки вала в дистиллированной и холодной проточной воде приступают к подготовке и хромированию остальных шеек вала. При необходимости также хромируют рабочие поверхности упорных буртиков первой шейки. Хромированные шейки шлифуют. Диаметр шейки после шлифования должен быть равен 30Ш-0,06-0,095 мм (см. рис. 38), ширина между буртиками первой шейки 44 Л+0,344+0,17 мм. Овальность и конусность не более 0,03 мм.
При срыве не более двух ниток резьбу в отверстии распределительного вала исправляют метчиком.
Следы коррозии на нерабочих поверхностях вала удаляют полированием войлочным кругом, накатанным корундовым порошком зернистостью 100—120. Для отделки рабочих поверхностей детали до металлического блеска применяют мягкий круг и пасту ГОИ. Отремонтированный вал для предохранения от коррозии оксидируют.
Архив! Самодельные распредвалы для моторов МеМЗ. Часть 2. Изготовление — ЗАЗ 1102, 1.1 л., 1991 года на DRIVE2
Продолжение. Начало статьи по ссылке.
По уцелевшему кулачку был сделан слепок с помощью пластичной холодной сварки. На кулачек накладывалась тонкая полоска из полиэтиленового пакета, а сверху, холодной сваркой облепливался как пластилином. При схватывании, сварка не прилипает к кулачку, а полиэтиленовая полоска легко отдирается от слепка. Получилась хорошая матрица для восстановления всего распредвала.
Свежие кулачки были грубо наварены простым полуавтоматом и обрабатывались (подгонялись) на большом круге шлифовального станка. Практически, это можно сделать на любом наждаке. Точность процесса корректировалась штангенциркулем и матрицей (штангелем — высота, матрицей — форма). Все получилось без особого фанатизма.Конечно, технологии закалки у нас никакой не было, но это и не планировалось…
В планах давно было желание поставить коромысла с роликами, которые могли бы работать как с обычными распредвалами с закалкой, так и с экспериментальными. Об изготовлении таких роликов, в скором времени выйдет отдельная статья (уже вышла, доступна по ссылке).
самодельный распредвал для Таврии
самодельный распредвал для Таврии
самодельный распредвал для Таврии
На фото показаны кулачки «как они есть», без лишней показухи: мелкие (и не очень) раковинки при сварке – не помеха для роликов.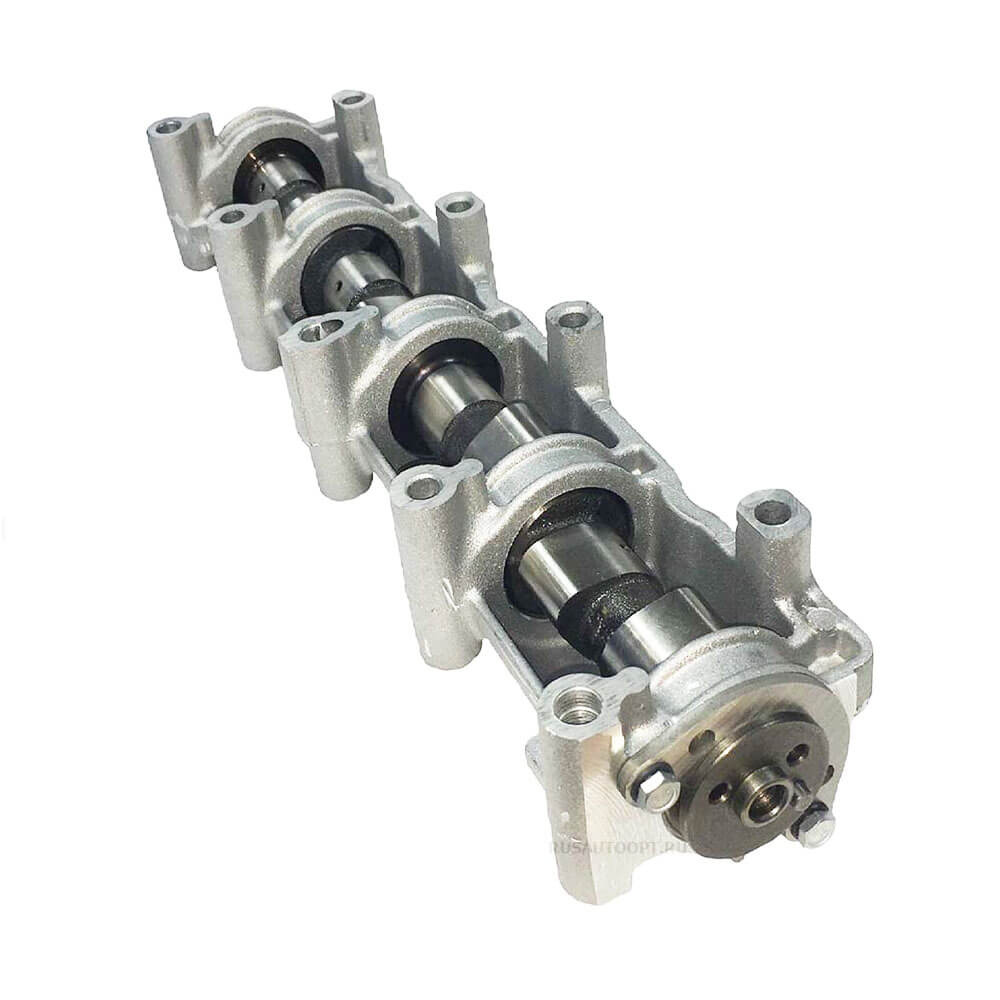
роликовое коромысло для Таврии (двигателя МеМЗ)
Распредвал показал свою работоспособность вместе с роликовыми коромыслами. Работал четко, без стуков и шума до 6900 об/мин (почему только до этой «отсечки» — будет написано в следующей статье).Восстановленный распредвал с фазами 274 градуса, напомнил работу электродвигателя: ощущалась его ровная характеристика, без резких подхватов, но с уверенным разгоном. Обычная городская езда на таком распредвале комфортная, но для спорта – этого мало.
Таврия SNP
Сразу с появлением на рынке Daewoo Lanos 1.4 и двигателя МеМЗ – 317, был немедленно куплен 317-ый распредвал для переделки на наш мотор и последующих экспериментов. Распредвал МеМЗ-317 показал себя с самой лучшей стороны. Поэтому, мы его смело рекомендуем для двигателей с умеренными доработками или вообще без них.Но совсем через непродолжительное время, он был отложен на отдых, так как мы приобрели еще один тюнинговый распредвал, который по фазам был «круче» чем 317-ый, а значит больше подходит для спорта. По фазам практически такой, как восстановленный самодельный распредвал, но более резкий и «вспыльчивый». У него прекрасная закалка – он уже 7 лет работает на Таврии SNP с обычными коромыслами. Но настоящего «гоночного» распредвала, мы так и не нашли. Поэтому, решили изготовить сами.
Коротко о работе над самым широкофазным распредвалом.
На снимке только заготовка, но даже в таком виде, распредвал был опробован на машине. Он работал вместе с роликовыми коромыслами, но в стационарном режиме, без выезда на испытания, так как кулачки только прихвачены.
На снимке видно, что радиус кулачка почти равен радиусу базы распредвала:
самодельный распредвал для Таврии
самодельный распредвал для Таврии
Если точно, то диаметр базы – 27 мм, а кулачка – 25 мм.Пример такой конфигурации распредвала, был взят с гоночного автомобиля опель 70-ых годов:
фото с книги Сингуринди Э.Г. «Авторалли», 1978 г.
Здесь удивил сам факт того, что двигатель заработал с этими бешеными фазами.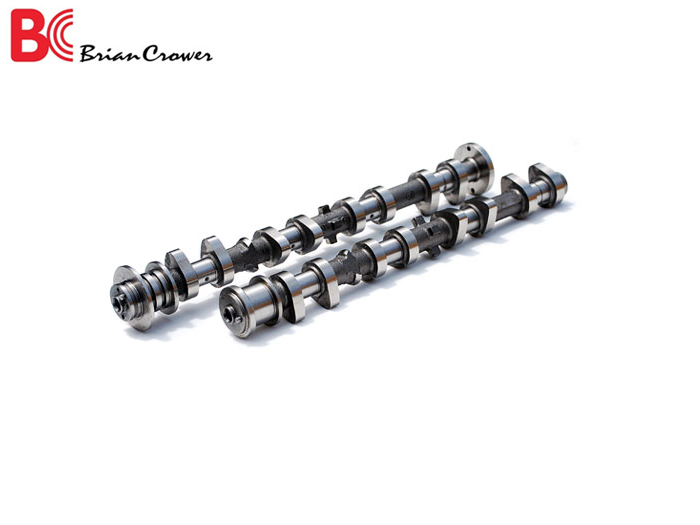
Замер фаз распредвала можно сделать прямо на машине, нужно только снять крышку клапанов и крышку распредшестерен, чтобы видеть работу клапанов и углы поворота шестерни распредвала.
Гораздо удобнее со снятой ГБЦ, но также, чтобы шестерня ГЗРМ стояла на месте, как у нас на фото:
самодельный распредвал для Таврии
Замер можно проводить при наличии всех коромысел на ГБЦ, или хотя бы, пары коромысел на любом из цилиндров.Продолжение в следующей заметке…
Кулачки анфас и в профиль
КЛУБ
Автолюбителей
КУЛАЧКИ АНФАС И В ПРОФИЛЬ
Два года назад журнал рассказал о «резвом» распредвале для «москвичей» с уфимскими моторами (ЗР, 1995, № 4). Этот новый кулачковый вал заметно улучшает характеристики двигателя, в чем убедились многие читатели, ставшие клиентами фирмы-изготовителя «Мастер-Мотор». Вернуться к теме распредвалов побудили многочисленные письма автомобилистов, заинтересовавшихся новинкой. Наш корреспондент Антон ЧУЙКИН беседует с Анатолием РОЖКОВЫМ, разработчиком «резвых» валов и главным конструктором «Мастер-Мотора».
— Анатолий Павлович, какие цели вы преследуете, проектируя новый распредвал для старого (по конструкции) мотора?
— Задача — поднять кривую крутящего момента в области наиболее используемых рабочих режимов двигателя. Говоря проще, приблизить характеристики автомобиля к… троллейбусным. Это легкое троганье, уверенное движение при минимальных оборотах коленвала, хорошая приемистость и тяговитость.
— К слову, именно этим вы и соблазнили наших читателей. Автор одного письма — владелец «сорок первого» — отмечал, что с «резвым валом» его «Москвич» легче тянет груженый прицеп, по дороге на дачу переключать передачи можно значительно реже — машина уверенно берет подъемы на четвертой и даже пятой…
— Особенно внимательно мы относимся к «низам», то есть к частотам вращения коленвала от 1000 до 3500 об/мин, где и стремимся добиться наибольшего роста крутящего момента. В то же время стараемся не снизить мощность, хотя максимальное ее значение, как правило, представляет для обычного водителя только теоретический интерес — кто же ездит, держа стрелку тахометра за 5000 об/мин? А ведь максимальную мощность двигатель развивает, как правило, только в этом режиме. Впрочем, для спортсменов мы можем изготовить валы, прибавляющие именно мощность.
Чтобы получить желаемые результаты, мы выбираем оптимальные подъемы кулачков и их взаимное расположение на валу. Эта задача не слишком проста, достаточно упомянуть об ограничениях: кулачки и детали привода клапанов не должны испытывать контактные напряжения выше допустимых, рычаг (коромысло, толкатель) не должен отрываться от поверхности кулачка, клапанные пружины желательно не изменять, и т.д., и т.п.
Приведу интересный пример, иллюстрирующий разные подходы к проектированию распредвалов. Казалось бы, ясно, что впускные и выпускные клапаны должны работать по-разному — тем не менее на всех серийных двигателях ВАЗ и УЗАМ все кулачки на распределительном вале одинаковые (двигатели модернизированной «Нивы» VAZ 21213 и «Оки» не в счет — их валы проектировал ваш собеседник). На наших валах (и на некоторых «иномарочных») кулачки всегда разные.
— В чем же состоит ваш метод проектирования кулачков?
— В основе любой методики проектирования профиля (грубо говоря, формы кулачка) лежит своя теория расчета.
Раньше, когда под рукой не было точной вычислительной техники, способы расчета кулачка были, по сегодняшним меркам, простые. Широко использовали так называемый кулачок Курца — его профиль можно было рассчитать вручную. Естественно, он был далек от идеала.
Американцы придумали «полидайн» — кулачок, профиль которого описан полиномом (многочленом) высокой степени. Есть патент на профиль, в основе которого лежит ряд Фурье.
Меня к проектированию кулачков подвел известный лет 15–20 назад дефект «жигулевского» распредвала, страдавшего быстрым износом. Одна из причин была в негладкости профиля кулачка; моя задача — создать кулачок абсолютно гладкий, с плавным профилем, без резких переходов от одного участка к другому.
Вкратце скажу, что проектирование профиля «моего» кулачка начинается с его четвертой производной. Если она является гладкой кривой (а выбрать таковую в наших силах) — то и сам кулачок будет плавным и гладким «от природы».
— Выходит, новый профиль избавил «жигулевский» распредвал от ненормально быстрого износа?
— Да, в основном, хотя об этом широко не известно. Напомню — на рубеже 70-80-х годов вал для автомобилей ВАЗ стал лучшим подарком автолюбителю — дефицит этих деталей был страшный, а служили они очень недолго.
Кулачки первых двигателей закаливали ТВЧ, затем распредвал стали азотировать, наконец, применили отбел кулачков переплавом. Однако почему-то никто всерьез не рассматривал кинематику привода клапана, а между тем именно в ней была, считаю, причина всех бед. Изменение технологии только обнажило скрытый дефект.
Я в ту пору работал инженером на
ВАЗе и распредвалом, честно говоря, занялся случайно, как хобби. Анализ профиля кулачка показал, что на его вершине есть притупление, которое плохо влияет на работу всего механизма. Тщательные натурные исследования, эксперименты с тензометром и датчиком виброускорений тоже показали, что при прохождении вершины кулачка по рычагу привода клапана в механизме возникает повышенная вибрация, провоцирующая быстрый износ.
Оказывается, в профиле кулачка таилась ошибка. Разработчик (фирма ФИАТ) «разрезал» кулачок по оси, проходящей через вершину, раздвинул половинки и вставил в промежуток кусок цилиндра протяженностью три градуса, слегка его загладив (рис. 1). Очевидно, целью было увеличение «времени-сечения» открытия клапанов и лучшее наполнение цилиндра рабочей смесью. Такие решения известны на тихоходных судовых двигателях, но здесь прием сыграл злую шутку — «кусочный» профиль в быстроходном механизме приводил к возникновению ударных нагрузок и, естественно, сокращал жизнь валу и рокерам.
В 1983 году кулачки стали делать с новым профилем, разработанным по описанному выше методу (авторское свидетельство № 1237778), и проблема «жигулевского» вала стала отступать (рис. 2). Тогда, при первом опыте внедрения такого профиля, подъем кулачка и фазы газораспределения были оставлены без изменений — стремились только повысить долговечность. Но потом стало интересно, как вообще влияет профиль на показатели двигателя, и я стал проектировать новые валы, чтобы улучшить характеристики моторов. ..
— И что же сейчас можете предложить автолюбителям?
— Фирма «Мастер-Мотор» делает целую гамму распредвалов для двигателей УЗАМ любого рабочего объема — от 1,5 до 2 л. Что они дают, видно по графикам на рис. 3, а. Здесь в качестве базового взят двигатель УЗАМ-3317 (рабочий объем 1,7 л), но подобная картина будет и на других моторах. Для УЗАМ мы предлагаем в первую очередь варианты, улучшающие характеристики при низких оборотах. Надо учитывать, что уфимские моторы не слишком любят, когда их «раскручивают» — хотя бы потому, что у них недостаточно уравновешенный коленвал. Не стоит выводить двигатель на предельные режимы.
Почти все валы требуют несколько измененных коромысел, поэтому при их замене приходится демонтировать головку блока цилиндров. Единственный вал, работающий с серийным коромыслом, хоть и проще установить, но получите вы меньший эффект — примерно 3/4 от того, что дают другие.
— А как насчет «жигулевских» моторов?
— Есть валы и для двигателей 21011, 2103, 2106. «Действие» одного из новых валов, например, в двигателе 2106 показано на рис. 3, б. Кстати, именно этот вал очень хорошо подходит к мотору 21213.
— Как же так, ведь на этом двигателе установлен изначально «ваш» распредвал?..
—…спроектированный больше 10 лет назад! Теперь я могу предложить нечто лучшее. Нынешний увеличивает крутящий момент на небольших оборотах; с таким двигателем езда спокойнее и приятнее.
Есть и другие валы для моторов 21213 и 2130 (1,7 и 1,8 л), увеличивающие крутящий момент на всех режимах. Однако при установке таких деталей, чтобы обеспечить больший ход клапана, надо зенковать рабочие фаски седел клапанов, что требует специального оборудования и квалификации.
— Последний вопрос — традиционный: каковы перспективы?
— Занимаемся моторами 2108 — им большая тяговитость на малых оборотах была бы очень кстати. Наработки есть, но пока они не увидели свет. Пробуем силы на ЗМЗ-402.
Кроме того, работаем над микропроцессорным зажиганием — правда, пока только для моторов УЗАМ. Эта новая система со специально подобранной характеристикой очень хорошо дополняет наши валы. Правда, сбыт разработок вызывает некоторые опасения — АЗЛК стоит уже давно, надеяться приходится на «Ижмаш», ВАЗ, ГАЗ. Судя по первым откликам клиентов, усилия наши востребованы и работаем мы не зря.
Рис. 1. Профили кулачков распредвала VAZ 2101 с эпюрами кривизны: а — исходный ФИАТ; б — ФИАТ без цилиндрического участка на вершине; в — новый профиль, разработанный А. Рожковым.
Рис. 2. Рекламации по износу кулачков «жигулевского» распредвала (на 1000 автомобилей в гарантийный период). После внедрения нового профиля летом 1983 года претензии пошли на убыль.
Рис. 3. Внешние скоростные характеристики двигателей УЗАМ (слева) и VAZ 2106. Черные линии — серийный вариант, цветные — с различными распредвалами «Мастер-Мотор».
НАША СПРАВКА. По многочисленным просьбам читателей публикуем заводские характеристики серийных двигателей Уфимского моторного производственного объединения. Обратите внимание на их обозначения: двигатель 412 имеет рабочий объем не 1,5, а 1,6 л — это новая модель со старым индексом. Двухлитровому мотору присвоено обозначение 248.
Электродуговая наплавка кулачков вручную
Восстанавливают кулачки распределительных валов электронаплавкой вручную в следующей последовательности.
Валы очищают от грязи, масла, а кулачки и от ржавчины до металлического блеска.
Для предохранения кулачков от боковых наплывов при наплавке на валы устанавливают защитные экраны (пластины) (рис. 48), изготовленные из меди или графита. Экраны должны плотно примыкать к торцовым поверхностям кулачков.
Вал устанавливают в ванну с водой на призмы так, чтобы вода покрывала его до половины (рис. 48).
Ванна сварной конструкции и все ее детали изготовлены из стали Ст. 1.
Кулачки наплавляют кругом электродом Т-590 или Т-620 диаметром 4 мм при силе тока 140—170 а. Наплавку производят вразброс отдельными участками (ширина шва 8—;10 мм). Толщина наплавленного слоя должна быть на вершине кулачка не менее 3 мм и на остальной части до 2 мм. Кулачки наплавляют в следующей последовательности: 1, 7, 2, 5, 3, 6, 4 и 8-й.
Наплавленный слой металла должен быть плотным, без глубоких раковин, трещин и пережога.
В качестве оборудования могут быть использованы сварочный преобразователь ПСО-500, ПСО-300 или электросварочный трансформатор СТН-350 или СТН-500.
Механическую обработку кулачков производят по технологии восстановления опорных шеек вибродуговой наплавкой.
Так как во время сварки вал может быть покороблен, то перед механической обработкой его необходимо подвергнуть правке.
Кулачки анфас и в профиль — журнал За рулем
КЛУБ
Автолюбителей
КУЛАЧКИ АНФАС И В ПРОФИЛЬ
Два года назад журнал рассказал о «резвом» распредвале для «москвичей» с уфимскими моторами (ЗР, 1995, № 4). Этот новый кулачковый вал заметно улучшает характеристики двигателя, в чем убедились многие читатели, ставшие клиентами фирмы-изготовителя «Мастер-Мотор». Вернуться к теме распредвалов побудили многочисленные письма автомобилистов, заинтересовавшихся новинкой. Наш корреспондент Антон ЧУЙКИН беседует с Анатолием РОЖКОВЫМ, разработчиком «резвых» валов и главным конструктором «Мастер-Мотора».
— Анатолий Павлович, какие цели вы преследуете, проектируя новый распредвал для старого (по конструкции) мотора?
— Задача — поднять кривую крутящего момента в области наиболее используемых рабочих режимов двигателя. Говоря проще, приблизить характеристики автомобиля к… троллейбусным. Это легкое троганье, уверенное движение при минимальных оборотах коленвала, хорошая приемистость и тяговитость.
— К слову, именно этим вы и соблазнили наших читателей. Автор одного письма — владелец «сорок первого» — отмечал, что с «резвым валом» его «Москвич» легче тянет груженый прицеп, по дороге на дачу переключать передачи можно значительно реже — машина уверенно берет подъемы на четвертой и даже пятой…
— Особенно внимательно мы относимся к «низам», то есть к частотам вращения коленвала от 1000 до 3500 об/мин, где и стремимся добиться наибольшего роста крутящего момента. В то же время стараемся не снизить мощность, хотя максимальное ее значение, как правило, представляет для обычного водителя только теоретический интерес — кто же ездит, держа стрелку тахометра за 5000 об/мин? А ведь максимальную мощность двигатель развивает, как правило, только в этом режиме. Впрочем, для спортсменов мы можем изготовить валы, прибавляющие именно мощность.
Чтобы получить желаемые результаты, мы выбираем оптимальные подъемы кулачков и их взаимное расположение на валу. Эта задача не слишком проста, достаточно упомянуть об ограничениях: кулачки и детали привода клапанов не должны испытывать контактные напряжения выше допустимых, рычаг (коромысло, толкатель) не должен отрываться от поверхности кулачка, клапанные пружины желательно не изменять, и т.д., и т.п.
Приведу интересный пример, иллюстрирующий разные подходы к проектированию распредвалов. Казалось бы, ясно, что впускные и выпускные клапаны должны работать по-разному — тем не менее на всех серийных двигателях ВАЗ и УЗАМ все кулачки на распределительном вале одинаковые (двигатели модернизированной «Нивы» VAZ 21213 и «Оки» не в счет — их валы проектировал ваш собеседник). На наших валах (и на некоторых «иномарочных») кулачки всегда разные.
— В чем же состоит ваш метод проектирования кулачков?
— В основе любой методики проектирования профиля (грубо говоря, формы кулачка) лежит своя теория расчета.
Раньше, когда под рукой не было точной вычислительной техники, способы расчета кулачка были, по сегодняшним меркам, простые. Широко использовали так называемый кулачок Курца — его профиль можно было рассчитать вручную. Естественно, он был далек от идеала.
Американцы придумали «полидайн» — кулачок, профиль которого описан полиномом (многочленом) высокой степени. Есть патент на профиль, в основе которого лежит ряд Фурье.
Меня к проектированию кулачков подвел известный лет 15–20 назад дефект «жигулевского» распредвала, страдавшего быстрым износом. Одна из причин была в негладкости профиля кулачка; моя задача — создать кулачок абсолютно гладкий, с плавным профилем, без резких переходов от одного участка к другому.
Вкратце скажу, что проектирование профиля «моего» кулачка начинается с его четвертой производной. Если она является гладкой кривой (а выбрать таковую в наших силах) — то и сам кулачок будет плавным и гладким «от природы».
— Выходит, новый профиль избавил «жигулевский» распредвал от ненормально быстрого износа?
— Да, в основном, хотя об этом широко не известно. Напомню — на рубеже 70-80-х годов вал для автомобилей ВАЗ стал лучшим подарком автолюбителю — дефицит этих деталей был страшный, а служили они очень недолго.
Кулачки первых двигателей закаливали ТВЧ, затем распредвал стали азотировать, наконец, применили отбел кулачков переплавом. Однако почему-то никто всерьез не рассматривал кинематику привода клапана, а между тем именно в ней была, считаю, причина всех бед. Изменение технологии только обнажило скрытый дефект.
Я в ту пору работал инженером на
ВАЗе и распредвалом, честно говоря, занялся случайно, как хобби. Анализ профиля кулачка показал, что на его вершине есть притупление, которое плохо влияет на работу всего механизма. Тщательные натурные исследования, эксперименты с тензометром и датчиком виброускорений тоже показали, что при прохождении вершины кулачка по рычагу привода клапана в механизме возникает повышенная вибрация, провоцирующая быстрый износ.
Оказывается, в профиле кулачка таилась ошибка. Разработчик (фирма ФИАТ) «разрезал» кулачок по оси, проходящей через вершину, раздвинул половинки и вставил в промежуток кусок цилиндра протяженностью три градуса, слегка его загладив (рис. 1). Очевидно, целью было увеличение «времени-сечения» открытия клапанов и лучшее наполнение цилиндра рабочей смесью. Такие решения известны на тихоходных судовых двигателях, но здесь прием сыграл злую шутку — «кусочный» профиль в быстроходном механизме приводил к возникновению ударных нагрузок и, естественно, сокращал жизнь валу и рокерам.
В 1983 году кулачки стали делать с новым профилем, разработанным по описанному выше методу (авторское свидетельство № 1237778), и проблема «жигулевского» вала стала отступать (рис. 2). Тогда, при первом опыте внедрения такого профиля, подъем кулачка и фазы газораспределения были оставлены без изменений — стремились только повысить долговечность. Но потом стало интересно, как вообще влияет профиль на показатели двигателя, и я стал проектировать новые валы, чтобы улучшить характеристики моторов. ..
— И что же сейчас можете предложить автолюбителям?
— Фирма «Мастер-Мотор» делает целую гамму распредвалов для двигателей УЗАМ любого рабочего объема — от 1,5 до 2 л. Что они дают, видно по графикам на рис. 3, а. Здесь в качестве базового взят двигатель УЗАМ-3317 (рабочий объем 1,7 л), но подобная картина будет и на других моторах. Для УЗАМ мы предлагаем в первую очередь варианты, улучшающие характеристики при низких оборотах. Надо учитывать, что уфимские моторы не слишком любят, когда их «раскручивают» — хотя бы потому, что у них недостаточно уравновешенный коленвал. Не стоит выводить двигатель на предельные режимы.
Почти все валы требуют несколько измененных коромысел, поэтому при их замене приходится демонтировать головку блока цилиндров. Единственный вал, работающий с серийным коромыслом, хоть и проще установить, но получите вы меньший эффект — примерно 3/4 от того, что дают другие.
— А как насчет «жигулевских» моторов?
— Есть валы и для двигателей 21011, 2103, 2106. «Действие» одного из новых валов, например, в двигателе 2106 показано на рис. 3, б. Кстати, именно этот вал очень хорошо подходит к мотору 21213.
— Как же так, ведь на этом двигателе установлен изначально «ваш» распредвал?..
—…спроектированный больше 10 лет назад! Теперь я могу предложить нечто лучшее. Нынешний увеличивает крутящий момент на небольших оборотах; с таким двигателем езда спокойнее и приятнее.
Есть и другие валы для моторов 21213 и 2130 (1,7 и 1,8 л), увеличивающие крутящий момент на всех режимах. Однако при установке таких деталей, чтобы обеспечить больший ход клапана, надо зенковать рабочие фаски седел клапанов, что требует специального оборудования и квалификации.
— Последний вопрос — традиционный: каковы перспективы?
— Занимаемся моторами 2108 — им большая тяговитость на малых оборотах была бы очень кстати. Наработки есть, но пока они не увидели свет. Пробуем силы на ЗМЗ-402.
Кроме того, работаем над микропроцессорным зажиганием — правда, пока только для моторов УЗАМ. Эта новая система со специально подобранной характеристикой очень хорошо дополняет наши валы. Правда, сбыт разработок вызывает некоторые опасения — АЗЛК стоит уже давно, надеяться приходится на «Ижмаш», ВАЗ, ГАЗ. Судя по первым откликам клиентов, усилия наши востребованы и работаем мы не зря.
Рис. 1. Профили кулачков распредвала VAZ 2101 с эпюрами кривизны: а — исходный ФИАТ; б — ФИАТ без цилиндрического участка на вершине; в — новый профиль, разработанный А. Рожковым.
Рис. 2. Рекламации по износу кулачков «жигулевского» распредвала (на 1000 автомобилей в гарантийный период). После внедрения нового профиля летом 1983 года претензии пошли на убыль.
Рис. 3. Внешние скоростные характеристики двигателей УЗАМ (слева) и VAZ 2106. Черные линии — серийный вариант, цветные — с различными распредвалами «Мастер-Мотор».
НАША СПРАВКА. По многочисленным просьбам читателей публикуем заводские характеристики серийных двигателей Уфимского моторного производственного объединения. Обратите внимание на их обозначения: двигатель 412 имеет рабочий объем не 1,5, а 1,6 л — это новая модель со старым индексом. Двухлитровому мотору присвоено обозначение 248.
Замена распредвала своими руками.
Замена распредвала может понадобиться в двух случаях — или он изношен и его необходимо заменить новым, или штатный распределительный вал меняют на спортивный (тюнинговый — с более высоким профилем кулачков). В этой статье мы рассмотрим, как заменить своими руками распределительный вал на другой, новый или спортивный и что для этого понадобится.
Замена штатного распредвала новым.
Какой бы твёрдой (цементированной) не была бы поверхность кулачков и шеек распредвала, и каким бы качественным не было бы моторное масло, но после достаточно долгой эксплуатации двигателя, трущиеся детали распределительного вала, такие как кулачки и шейки — см. фото слева, всё равно постепенно изнашиваются и двигатель начинает очень плохо работать (пример плохой работы мотора с изношенным распредвалом, показан в видеоролике под этой статьёй) и вал приходится заменять новым.
Но при желании можно немного доработать новый распределительный вал, и его ресурс увеличится почти вдвое. Как это сделать, советую почитать вот в этой статье.
Чтобы заменить изношенный распредвал, потребуется новый распредвал и некоторый набор инструмента: набор гаечных рожковых ключей, накидных головок и динамометрический ключ.
Конечно же сейчас есть фирмы, которые восстанавливают износ распредвалов напылением, но они есть не везде и поэтому многие просто покупают новый распредвал, взамен изношенного. Что и будет описано ниже.
Для начала снимаем кожух ремня (или цепи ГРМ) и поставив коробку передач машины на нейтральную передачу, прокручиваем коленвал двигателя (ключом за болт шкива коленвала) по часовой стрелке, пока метка на шкиве (звёздочке) распредвала не сойдётся с меткой на внутреннем кожухе ремня (советую уточнить в мануале вашего двигателя, где находятся метки на вашем моторе). Шкив коненвала тоже установится по метке на блоке двигателя . Это означает, что поршень первого цилиндра находится в ВМТ и это выставление по меткам поможет новичкам избежать проблем при сборке.
То есть после замены распредвала, на него нужно будет надеть шкив и затем прокрутив распредвал и выставив его по меткам, только после этого нужно будет надевать ремень. И так, чтобы произвести замену распредвала, следует сделать следующее:
- Снимаем клапанную крышку.
- Ослабляем натяжитель ремня, а если цепь, то снимаем натяжитель.
- Снимаем ремень с шкива распредвала (если цепь, то снимаем звёздочку вместе с цепью и привязываем проволокой, чтобы цепь не соскочила с зубьев).
- Снимаем шкив распределительного вала, окрутив удерживающий его болт (используем съёмник). Чтобы открутить болт, ставим машину на первую передачу и используем накидную головку (обычно на 17 мм). Не забываем, что на многих машинах, перед откручиванием болта шкива, нужно отогнуть с помощью отвёртки фиксирующую гайку шайбу.
- Откручиваем на пол оборота болты корпусов постелей распредвала: сначала болты крайних постелей (подшипников скольжения), затем средних.
- Полностью откручиваем болты постелей распредвала и снимаем верхние крышки постелей, укладывая их вместе с болтами на картон (картон с отверстиями для болтов), на котором заранее помечены номера постелей и болтов — это важно и это поможет собрать всё как было до разборки.
- Извлекаем распределительный вал из корпусов постелей (подшипников скольжения).
- Перед установкой нового распредвала, советую установить новые вкладыши распредвала (если они съёмные). Но на многих иномарках вкладыши не используют, так как корпус постелей сам является подшипником скольжения.
Установив новый распредвал, советую замерить зазор между шейками распредвала и подшипниками скольжения и затем сверить его с допустимыми зазорами, описанными в мануале именно вашего двигателя. Чтобы замерить зазор, нужно вставить между шейкой вала и корпусом подшипника (или вкладышем если он есть) специальную пластиковую калибровочную проволоку (типа рыболовной лески) — она бывает в продаже, а затем сжать постели распредвала с помощью динамометрического ключа, с требуемым в мануале моментом.
Далее откручиваются болты постелей, и сплющенная проволока извлекается и замеряется микрометром — это и будет зазор между шейкой распредвала и подшипником скольжения. И этот зазор далее сверяется с допустимыми зазорами, описанными в мануале именно вашего мотора.
Если зазоры будут больше допустимых значений, то нужно будет или заменить распредвал на деталь с шейками чуть большего диаметра (бывают такие ремонтные валы) или установить новые корпуса подшипников (или вкладыши, если конечно они есть на вашей машине). Лучше конечно заменить постели (подшипники скольжения) новыми, так как изнашиваются они неравномерно (в виде овала).
В итоге, если после установки нового распредвала, вы добьётесь нужных зазоров между его шейками и подшипниками скольжения, то отремонтированный вами узел будет такой же как и на новом автомобиле и с давлением масла будет всё в порядке (это же касается и вкладышей коленвала).
Кстати, сальник распредвала тоже желательно заменить новым, подробнее об этом вот тут. Всё собирается в обратной последовательности. Болты постелей затягиваются постепенно, в четыре приёма, согласно рисунку слева. Разумеется используем при затяжке динамометрический ключ и затягиваем болты с требуемым моментом, который указан в мануале вашего двигателя (на некоторых машинах момент затяжки отличается, поэтому изучите мануал именно вашего двигателя).
После замены распредвала новым (и его подшипников, если это необходимо), следует надеть на распредвал шкив, на шкив ремень и затем правильно натянуть его (с помощью чего правильно натягивается ремень ГРМ, советую почитать вот здесь) и обязательно следует отрегулировать зазоры клапанов.
Кстати, на более свежих моторах, у которых имеется два распределительных вала, всё делается аналогично, только деталей в два раза больше.
Замена распредвала на спортивный.
Многие автолюбители, пытаясь поднять мощность своего мотора, вместе с другими комплексными мероприятиями по тюнингу двигателя, покупают и устанавливают распредвал с более высоким и острым профилем кулачков (острые кулачки хорошо видны на фото слева).
Клапана от этого поднимаются чуть выше, зазор между тарелками клапанов и сёдлами становится больше, время, при котором клапан находится в открытом состоянии увеличивается, продувка улучшается, мотор начинает «дышать» полнее и мощность возрастает.
К тому же после замены штатного распредвала спортивным, как бы отодвигается граница стука пальцев при резком разгоне (на малых и средних оборотах двигателя).
Но здесь есть ряд некоторых нюансов. Во первых для некоторых машин, сейчас можно приобрести даже три вида распредвалов, каждый из которых имеет разную высоту кулачков: малую, среднюю и самую высокую высоту (различие по высоте кулачков всего в пару мм, а то и меньше).
К тому же к спортивному распредвалу следует купить так называемую разрезную шестерню или шкив (см. фото слева), у которой отверстия её крепления не круглые, а овальные. И благодаря этому можно «играться» с фазами, то есть выбирать регулировками (сдвигом фаз) шестерни наиболее приемлемый вариант для разных распредвалов.
Низовой распредвал. Распредвал с самой малой высотой кулачков (так называемый низовой, у него почти такие же кулачки, как у штатного вала, но чуть выше) рассчитан для самого спокойного движения, то есть для поездок по городу.
Низовым такой распредвал назван потому, что двигатель автомобиля не нужно будет постоянно раскручивать до высоких оборотов, и мощность мотора будет повышена даже на низких оборотах, да и рычагом переключения можно будет работать реже, чем с распредвалами с более высоким профилем кулачков.
То есть например при снижении скорости автомобиля, нужно резко ускориться, и при этом не нужно будет переходить на пониженную передачу, так как мощность мотора на низах с низовым распредвалом достаточная для уверенного разгона. К тому же у низового распредвала отсутствует (или совсем маленькая) зона перекрытия клапанов.
Средний распредвал. Распредвал с средней высотой профиля кулачков — это так называемый универсальный распредвал, который подходит и для спокойного темпа движения и для не слишком спортивного. Мотор с таким распредвалом самый гибкий по оборотам.
Верховой распредвал. Ну и распредвал с самым высоким (острым) профилем кулачков, рассчитан для гонок на треке и с ним мощность мотора будет самой большой. Фазы газораспределения расширятся и появится зона перекрытия клапанов.
Но мотор нужно будет хорошо раскручивать, так как пик мощности будет на самых высоких оборотах. После установки такого распредвала, нагрузки на детали двигателя возрастут, поэтому нужно будет хорошо отюнинговать двигатель, заменив подшипники на самые качественные, установить кованые поршни , облегчённые шатуны и прямоточный глушитель. И это далеко не всё.
Клапана начнут открываться ощутимо больше, и возможна их встреча с поршнями. Поэтому и поршни устанавливают с большей глубиной выемок под клапана, а если купить такие нет возможности, а толщина донышек достаточно толстая, то в поршнях нужно будет фрезернуть выемки под клапана чуть глубже, то есть ровно на столько мм глубже, на сколько больше стали открываться клапана с тюнинговым распредвалом.
И еще — работать рычагом коробки передач придётся чаще, но на больших оборотах мощность будет поболее, чем с другими валами. Зато на средних оборотах и на низах, с таким распредвалом мощность будет недостаточной. Будет проявляться так называемый провал на низах, так как фаза газораспределения станет более широкой и на низких оборотах горючая смесь будет выталкиваться назад в впускной тракт. Но зато на высоких оборотах, как я уже говорил, мощность будет ощутимо больше, чем с другими распредвалами (с более низким профилем кулачков).
Такие распредвалы кроме того, что добавят провалов на низах двигателю, ещё и мотор станет работать не устойчиво на холостых оборотах. К тому же постоянное раскручивание мотора до высоких оборотов, снизит ресурс двигателя (особенно не усиленного дорогими и более качественными деталями).
Спортивные верховые распредвалы как правило устанавливают для гонок, или для рекордов скорости (скоростных заездов), а для машины, рассчитанной для каждодневных поездок, лучше сделать замену распредвала на средний вариант (то есть универсальный распредвал с средней высотой профиля кулачков).
Разумеется каждый водитель выбирает для себя нужный распредвал в зависимости от того, где и в каких условиях будет впоследствии эксплуатироваться автомобиль. И замена распредвала на нужный вариант, будет конечно же одним из видов полной (комплексной) доводки двигателя, ведь только так можно заметно увеличить мощность любого мотора, успехов всем.
Кулачок распределительного вала: поломки и их устранение
Распределительный вал отвечает за работу газораспределительной системы транспортного средства. Его конструкция состоит их нескольких элементов, среди которых важное место занимаю кулачки. Количество кулачков часто совпадает с количеством клапанов двигателя автомобиля. Они отвечают за открытие и закрытие выпускного клапана и отвод отработанных газов. В ходе продолжительной службы или масляном голодании кулачки могут износиться и деформироваться что приводит к сбоям в работе двигателя и пожжет привести к его поломке. Для нормализации работы распределительного вала может помочь восстановление кулачков распредвалов, такой ремонт оптимален для тех кто не хочет менять весь узел.
Показатели неисправности
Неисправности в распределительном вале могут привести к поломке силового агрегата, по этой причине при появлении симптомов поломки следует провести диагностику и визуальный осмотр на предмет выявления дефектов. Основные показатели поломки распределительного вала это стук и сбои при работе двигателя. Определение причины поломки проводят в несколько шагов:
- Открутить удерживающие болты клапанной крышки;
- Снять крышку;
- Провести визуальный осмотр;
- Демонтировать вал;
- Провести более тщательную диагностику.
В случае деформации кулачков визуальный осмотр не поможет необходимо более тщательно провести диагностику, а для этого демонтировать узел. После демонтажа и определения повреждения кулачков можно приступать к ремонту.
Восстановление
Повреждение кулачков происходит редко и чаще всего после длительного срока службы. Приблизительно распределительный вал рассчитан на такой же срок жизни как и двигатель автомобиля. В случае появления поломок вала необходимо провести профилактический осмотр двигателя.
Для восстановления кулачков применяют два метода:
- Напыление – восстановление целостности детали при помощи наплавления сваркой;
- Шлифовка – устранение деформаций, заусениц или небольших неровностей шлифованием.
Важно в ходе работы не допустить изменение размеров кулачков, это может привести к дополнительным проблемам и еще одному ремонту.
Предыдущая статьяАуди Q7 — надежность и болезниСледующая статьяМеждународные перевозки грузов: особенности организации Анализ отказа распределительного вала: что вызывает чрезмерный износ кулачка распределительного вала?
Все мы знаем, насколько важны распределительные валы для работы вашего двигателя, и когда они выходят из строя, это может привести к проблемам. Независимо от того, есть ли у вас плоский толкатель или роликовый распределительный вал, одной из наиболее распространенных причин проблем с распределительным валом является износ или повреждение кулачка.
Знаете ли вы, что всего 0,001 дюйма износа лепестков может отрицательно сказаться на фазе газораспределения на целых 3 градуса? Этот износ приводит, среди прочего, к потере мощности и экономии топлива.И это даже без учета воздействия более обширных повреждений, вызванных механическим вмешательством или другими серьезными проблемами.
Если вы заметили износ или повреждение распределительного вала, важно определить причины проблемы перед установкой нового кулачка. Если вы этого не сделаете, вы рискуете испортить новый распределительный вал и потерять больше денег.
Что может быть причиной этих проблем? Читайте дальше, чтобы узнать о некоторых наиболее распространенных причинах повреждения кулачков распределительного вала.
Признаки повреждения кулачка распределительного вала
Точечная коррозия на распределительном валу
Во многих случаях точечная коррозия на кулачках возникает из-за нормального износа деталей в результате многочасовой работы. Тем не менее, важно определить и заменить распределительный вал до того, как он полностью выйдет из строя или вызовет повреждение других компонентов из-за неправильной эксплуатации.
В других случаях питтинг может быть вызван мусором в компонентах. Убедитесь, что при установке все чисто, а масляные каналы чисты и не содержат грязи или других частиц.Это жизненно важно для правильной установки, так как грязь и мусор могут вызвать серьезные проблемы с распределительным валом и подшипниками.
На изображениях ниже показаны питтинги на кулачках распределительного вала.
Отсутствие смазки
Правильная смазка жизненно важна для поддержания нормальной работы распределительного вала. При недостатке смазки, будь то из-за заблокированных масляных каналов или из-за слишком большого зазора, вы начнете замечать характер износа. Это связано с повышенным трением при вращении распределительного вала.Если не принять меры, вы рискуете испортить подшипники или даже сломать крышку распредвала из-за большого трения и тепла.
Два основных места, которые вы должны обеспечить надлежащей смазкой, — это между штифтом и роликом и между кулачком и роликом. Это поможет уменьшить трение, что, в свою очередь, уменьшит степень износа компонентов.
Повреждение подъемника/толкателей
Неправильное функционирование подъемника может привести к повреждению выступа.Скорее всего, вы заметите выемки на выступах, а также повреждения на самом подъемнике. Это может быть вызвано тем, что подъемник находится не на своем месте и ударяется о кулачок, слабым давлением пружины клапана, недостаточным давлением масла или стрессовыми условиями эксплуатации, такими как превышение скорости.
Существуют и другие виды повреждений распределительного вала или связанных с ним деталей, помимо износа кулачков. Многие из них являются результатом неправильной техники установки. Чтобы предотвратить повреждение, связанное с установкой, убедитесь, что ваш распределительный вал правильно расположен и установлен. Прочтите наше руководство по установке для получения дополнительной информации. У нас есть большой выбор распределительных валов, если вы заметили, что ваш нуждается в замене.
Если вас интересуют распределительные валы или любые другие детали для вашего дизельного двигателя, позвоните нам по телефону 844-304-7688 или запросите расценки онлайн.
Угол разделения лопастей протестирован и объяснен
Если головки цилиндров — это легкие двигателя, то распределительный вал — его мозг. Это влияет на диапазон мощности и темперамент двигателя больше, чем любая другая отдельная деталь, и небольшое изменение может превратить автомобиль из кроткого продавца продуктов в совершенно неприятную машину.На первый взгляд, работа распределительного вала проста — открывать и закрывать клапаны, — но помимо этого актуального описания это один из самых загадочных и непонятых компонентов двигателя.
Видеокарта с множеством цифр, акронимов и аббревиатур находится в одном росчерке красной ручкой от проваленного теста по математике. Но чтобы выбрать идеальную камеру, нужно понимать всю эту информацию. Каждая спецификация представляет собой дорожную карту того, что делают клапаны, наиболее распространенными из которых являются подъем, продолжительность и угол разделения лепестков (LSA) — последний нуждается в наибольшем объяснении.
Что такое угол разделения лепестков?
LSA — это расстояние от осевой линии впускного патрубка до осевой линии выпускного патрубка. Это средняя осевая линия между обеими лепестками, выраженная в градусах в диапазоне от 95 на очень узкой/узкой стороне до более 120 на широком конце. LSA — это способ суммирования относительной синхронизации событий впускного клапана (впускное открытие, впускное закрытие) и выпускного клапана (выпускное открытие, выпускное закрытие) по отношению друг к другу, и это отличное приближение того, как двигатель будет работать.
Чтобы продемонстрировать изменения в разделении кулачков в действии, мы заказали у Comp Cams три распределительных вала, все шлифованные, с одинаковой подъемной силой (0,541 впуск и 0,537 выпуск) и продолжительностью (230 впуск и 236 выпуск), но с тремя разными LSA: 101, а 107 и 113. Мы позаимствовали заводской мул Westech Performance, малоблочный Chevy 370ci и его динамометрический стенд для двигателя SuperFlow 902, и провели день, запуская каждый кулачок вплотную, чтобы оценить его влияние на пиковую мощность, максимальный крутящий момент, компрессию при проворачивании. , вакуум на холостом ходу и диапазон мощности в целом — все переменные, которые определяют характер двигателя на улице и на треке.
С первым кулачком, загруженным в двигатель (101 LSA), Стив Брюл из Westech сделал три тяги на динамометрическом стенде, среднее значение которых было сохранено для сравнения со следующим камера Чтобы еще больше свести к минимуму любые отклонения на динамометрическом стенде, температура масла и воды в двигателе поддерживалась одинаковой для каждого рывка. Кулачок 101 LSA с неравномерным холостым ходом выдавал в среднем 484,0 л.с. при 6100 об/мин с крутящим моментом 493,9 фунт-фут при 4400 об/мин. У него был надежный диапазон мощности с тоннами полезного крутящего момента. Однако обильное перекрытие выхлопных газов (31 градус) означало сильное разбавление выхлопных газов при низких оборотах двигателя и высоком вакууме. Качество холостого хода было грубым, а вакуумметр показывал всего 9,8 дюйма ртутного столба (дюймы ртутного столба). Брюл провернул двигатель с помощью стартеров динамометрического стенда и зафиксировал сжатие при проворачивании коленчатого вала 185 фунтов на квадратный дюйм.
Тест 1 был простым.Тесты 2 и 3 означали разборку двигателя на динамометрическом стенде, чтобы вытащить старый кулачок. Клапанные крышки, клапанный механизм, впускной коллектор, гармонический балансир, передняя крышка, комплект ГРМ и кулачок были выдернуты. Брюл вставил кулачок 113-LSA, самый широкий из испытанных, в сердце двигателя и приступил к установке всех деталей на место.
После следующих трех рывков стало ясно, что 113-й кулачок сильно опустился на низком крутящем моменте. На пике он выдавал 472,4 фунта-фута, что на 21,5 фунта-фута меньше, чем у 101 кулачка. Средняя мощность также снизилась, но двигатель опережал 101 кулачок при 5400 об/мин, набирая 6.5 лс на пике. При испытании на сжатие при проворачивании Брюл зафиксировал 175 фунтов на квадратный дюйм, падение на 10 фунтов на квадратный дюйм по сравнению с выходным кулачком 101. Вакуум на холостом ходу показал значительный всплеск до 14,7 дюймов ртутного столба, что, вероятно, является разницей между возможностью использовать силовые тормоза и обязательной тренировкой ног.
В очередной раз разобрали двигатель для установки третьего тестового кулачка, 107 LSA. Этот кулачок разделил разницу между 101 и 113 посередине, и теоретически должен был пройти линию между результатами двух последних тестов во всех отношениях, что он и сделал.Кривая мощности и крутящего момента лежала прямо между двумя последними кулачками, как и пиковая мощность и крутящий момент: 488,7 л. с. при 6200 об/мин и 487,1 л.с. при 4600 об/мин соответственно. Это была наука в действии, и с данными на буксире пришло время обработать цифры и выяснить, что происходит.
LSA | Мощность | Момент затяжки | Пусковой компрессионный | Холостой вакуум |
101 | 484.0 при 6100 об/мин | 493,9 при 4400 об/мин | 185 фунтов на кв. дюйм | 9,8 |
107 | 488,7 при 6200 об/мин | 487.1 при 4600 об/мин | 180 фунтов на кв. дюйм | 12,2 |
113 | 490,5 при 6200 об/мин | 472,4 при 4700 об/мин | 175 фунтов на кв. дюйм | 14,7 |
Вывод из этого теста: распредвал LSA — палка о двух концах. Самый узкий LSA (101) стоил 21. 5 фунт-фут крутящего момента и гораздо более широкий диапазон мощности — за счет гораздо более низкого вакуума на холостом ходу, что сделало бы его более темпераментным в уличном автомобиле. Что касается мощности, разница между всеми тремя кулачками составляла всего 6,5 л.с., при этом пики разделялись скудными 100 об/мин.
Вывод прост на первый взгляд: более плотный LSA обеспечивает больший крутящий момент на низких и пиковых оборотах за счет всего нескольких пони на высоких оборотах. Если бы это было единственным соображением, кулачок 101 был бы явным победителем. Однако в применении нужно учитывать гораздо больше.Такие факторы, как вакуум холостого хода, экономия топлива и настройка, влияют на выбор правильного кулачка.
Плотные кулачки LSA обеспечивают превосходный крутящий момент на низких оборотах и имеют красивую кривую мощности. Но ничто не обходится без затрат, и холостой вакуум страдает по мере уменьшения LSA. Это приводит к тому, что уличные манеры и настройка двигателя становятся непостоянными. Кулачок с более жестким LSA потребует более слабого гидротрансформатора, может не иметь возможности запуска тормозов с вакуумным усилителем и плохо работает с впрыском топлива.
Этот всеми любимый хлипкий холостой ход, являющийся частью привлекательности жесткого кулачка LSA, на самом деле является пропуском зажигания из-за разбавления выхлопных газов во впускном коллекторе и плохого наполнения цилиндров на холостом ходу.Это создает неустойчивое состояние вакуума в коллекторе, которое на двигателе с впрыском топлива сбивает с толку датчики давления воздуха в коллекторе (MAP), затрудняя им регулирование подачи топлива. Клапан управления впускным воздухом (IAC), который регулирует обороты холостого хода, также вынужден работать сверхурочно и часто пытается «поймать» холостой ход, но обычно стреляет то вверх, то вниз. Эти проблемы часто могут быть решены продвинутым настройщиком, но всегда представляют собой проблему и компромисс в стратегии настройки.
Мир впрыска топлива — это то, где широко распредвалы LSA, такие как 113, действительно блестят. Благодаря минимальному перекрытию и стабильному сигналу вакуума в коллекторе они отлично работают с системами впрыска топлива и являются нормой для современных двигателей с толкателями, таких как LS и Hemi Gen III. Если вы OEM-производитель автомобилей, который ищет стабильный холостой ход, хорошую экономию топлива и минимальные выбросы выхлопных газов, это кулачок выбора. Широкие кулачки LSA также применимы в приложениях с принудительной индукцией, где требуется меньшее перекрытие выхлопных газов.
Камеры среднего класса (110112)
Если вы посмотрите любой каталог камер, вы обнаружите, что большинство уличных камер попадают в этот диапазон.Это не случайно. Кулачок серии 110112 LSA обеспечивает необходимый кулачок холостого хода, чтобы успокоить уши редуктора приемлемым вакуумом в коллекторе для работы вспомогательного оборудования с вакуумным приводом. Баланс среднего крутящего момента и максимальной мощности делает этот диапазон LSA подходящим для большинства уличных/полосных двигателей. Около 70 процентов кулачков для мощных автомобилей попадают в этот диапазон.
Поток в головке блока цилиндров и LSA напрямую связаны: как правило, чем лучше поток в головке цилиндра, тем шире может быть LSA. Более широкий LSA смещает события впускного и выпускного клапанов дальше друг от друга и создает меньше перекрытий, что вредит настройке волны впуска.
«Когда вы правильно настроили мощный двигатель, вы создаете волны высокого и низкого давления на впуске и выпуске, которые помогают наполнять цилиндры», — сказал Билли Годболд из Comp Cams. «Когда волна низкого давления в выхлопе отражается во впуске, дельта давления фактически помогает втягивать воздух и топливо в цилиндр. Когда у вас нет перекрытия, вы не можете настроить волну. всегда будет больше перекрытий, что позволяет выхлопной и впускной системам — если они хорошо настроены — работать вместе.
Эта волновая настройка помогает двигателям с высокими рабочими характеристиками достигать объемной эффективности более 100 %. Чтобы решить эту проблему, присущую широким распределительным валам LSA, вам просто нужен впускной канал с большей пропускной способностью. Вот почему серия LS и многие другие современные двигатели, могут развивать большую мощность сверху и снизу с широкими распределительными валами LSA, и почему множество заводских головок цилиндров текут около (или выше) 300 кубических футов в минуту
Какой распредвал мне подходит? идеальная камера, безусловно, может быть сложной задачей.В конечном счете, все сводится к тому, как вы хотите, чтобы работал двигатель, предназначению автомобиля и тому, что вы готовы терпеть. Вооружившись дополнительной информацией о теории распределительных валов, что вы будете строить?
Просмотреть все 29 фото Известный как «Гладиатор» в Westech Performance, этот малоблочный Chevy на базе блока Dart SHP с двигателем 370 куб. народ вынудил Стива Брюла из Westech присоединиться к нему.Двигатель имеет головки AFR, коромысла Crane, балансир TCI, узел Scat Rotating с поршнями Mahle, воздухозаборник Edelbrock RPM Air-Gap, зажигание MSD и топливную систему Aeromotive.
Мифы о сжатии при запуске двигателя
LSA | Впускной клапан |
101 | 36 АБДК |
107 | 42 АБДК |
113 | 44 АБДК |
Распространенное заблуждение состоит в том, что перекрытие впуска/выпуска способствует снижению компрессии при проворачивании коленчатого вала.Это представление совершенно ложно. «Девяносто девять процентов компрессии при проворачивании определяется статической степенью сжатия и точкой закрытия впускного клапана», — сказал Билли Годболд из Comp Cams. Как вы можете видеть на графике, кулачок 101 LSA на самом деле имел самое высокое сжатие при запуске из всей партии: 185 фунтов на квадратный дюйм. Только после закрытия впускного клапана может начаться компрессия. Поскольку кулачки кулачка 101 LSA расположены ближе друг к другу, точка закрытия впуска смещена вперед (закрывается раньше), и поршень имеет больше времени для создания сжатия — именно то, что показал датчик. На приведенном выше графике сравниваются точки закрытия впускного клапана трех кулачков, использованных в тесте.
- Перемещает крутящий момент на более низкие обороты
- Увеличивает максимальный крутящий момент
- Узкий диапазон мощности
- Увеличение вероятности детонации двигателя
- Увеличить компрессию при запуске
- Простой вакуум и качество снижаются
- Перекрытие клапана увеличивается
- Уменьшает зазор между поршнем и клапаном
- Увеличить крутящий момент до более высоких оборотов
- Уменьшает максимальный крутящий момент
- Расширяет диапазон мощности
- Уменьшение вероятности детонации двигателя
- Уменьшить пусковую компрессию
- Вакуум на холостом ходу и улучшено качество
- Перекрытие клапана уменьшается
- Увеличивает зазор между поршнем и клапаном
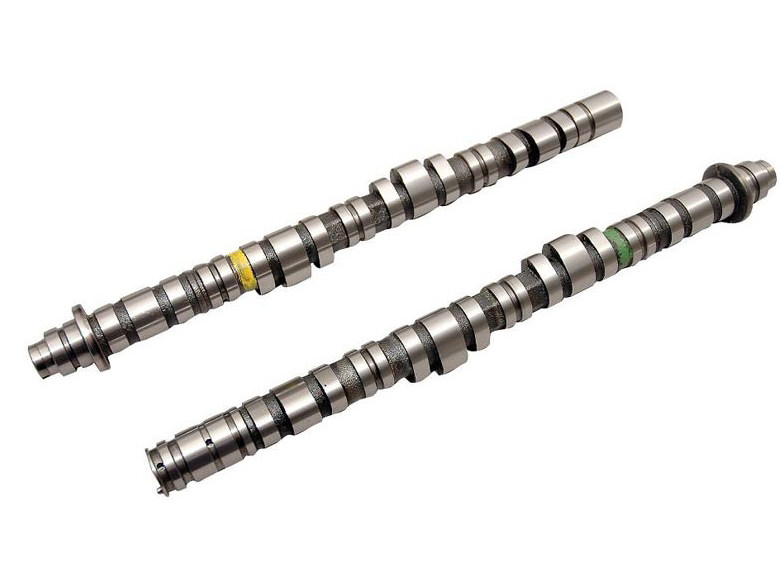
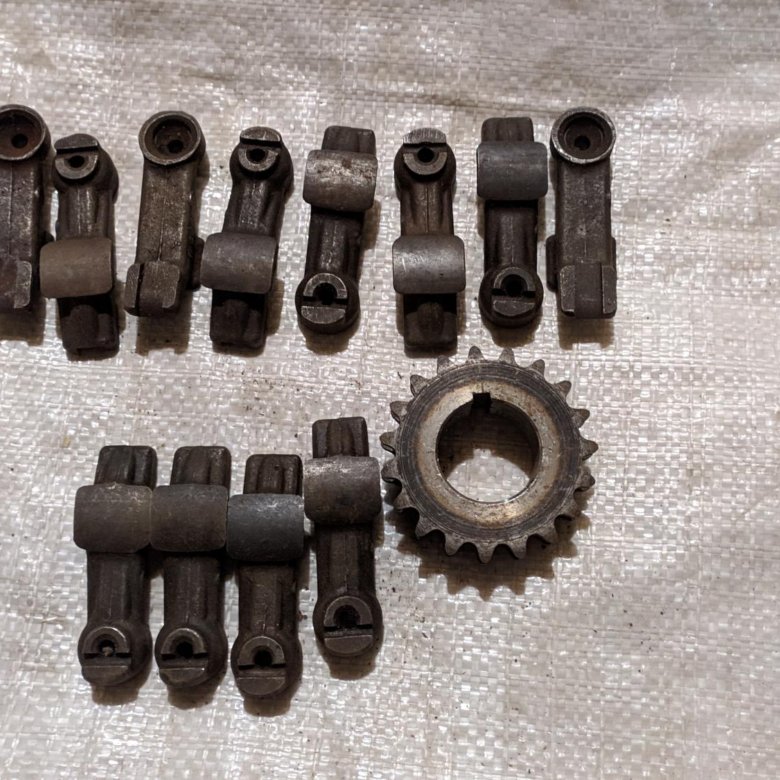
Динамометры SuperFlow и стенды потока ; 515.254.1654; SuperFlow.com
Просмотреть все 29 фотоВыбор распределительного вала для конкретного двигателя обычно включает в себя компромисс между вариантами низкой или высокой мощности, и угол разделения кулачков (LSA) является одним из тех факторов, при которых производители двигателей должны сделать выбор между этими приоритетами.
«Угол разделения кулачков — это угол в градусах распределительного вала между точками максимального подъема или центральными линиями впускных и выпускных кулачков», — говорит Эрик Боландер из Erson Cams.«Это влияет на величину перекрытия клапанов; это короткий период времени, когда и впускной, и выпускной клапаны открыты».
Например, малый блок с овальной колеей, который должен мотивировать автомобиль быстро выходить из поворота, может иметь узкий LSA около 106 градусов, что приводит к большему перекрытию. Узкий, более специфический диапазон мощности также является продуктом узкого LSA, как и неравномерное качество холостого хода, часто называемое звуком 106.
«Чем меньше угол разделения лепестков, тем острее будет кривая мощности», — подтверждает Боландер.«Он создает пиковый крутящий момент раньше, быстрее и сильнее, но и падает быстрее. На графике крутящего момента он имеет тенденцию напоминать треугольную форму».
Широкий LSA уменьшает перекрытие клапанов, смягчает холостой ход и улучшает общую управляемость, особенно на улице, где производительность двигателей увеличивается от 112 до 114 LSA. Но это не значит, что высоконагруженные гоночные двигатели также не могут получить прибыль.
Производитель двигателей Pro Stock может предпочесть широкий LSA, чтобы мощность не теряла тягу слишком рано.
«Двигатели с наддувом и закиси азота обычно выигрывают от более широкого LSA, потому что им не требуется такого большого перекрытия для продувки выхлопных газов, как безнаддувному двигателю», — продолжает Боландер. «Кроме того, более широкий LSA способствует устойчивости шасси в дрэг-рейсинге, позволяя избежать мощного выброса мощности, который может нарушить сцепление шин с дорогой. Таким образом, более широкий LSA вводит более широкий и, следовательно, более длинный диапазон крутящего момента».
«Изменение угла разделения лепестков изменяет степень перекрытия, которое существует в то время, когда впускной и выпускной клапаны открыты», — вторит Дуг Паттон из Pro Line Race Engines.«В безнаддувном двигателе угол разделения кулачков влияет на то, достигает ли двигатель максимального крутящего момента немного раньше или позже в диапазоне оборотов. Как правило, более узкое расстояние между лепестками развивает пиковый крутящий момент при более низких оборотах, а увеличение расстояния приводит к увеличению пикового крутящего момента в более высоком диапазоне оборотов. Двигатели с закисью азота, которые развивают большую мощность и крутящий момент, часто имеют большие углы раскрытия лепестков для умеренных давлений и температур в цилиндрах.
Создатели двигателей Чак Лоуренс (слева) и Дуг Паттон.
«Углы разделения кулачков, — продолжает он, — зависят от притирки распределительного вала. Если у уличного автомобиля меньшие значения подъемной силы и продолжительности, они могут работать со скоростью 112 или 114. Увеличение их угла разделения помогает увеличить выходную мощность на верхних оборотах. В качестве альтернативы, если вы используете распредвал большего размера, чтобы получить максимальную максимальную мощность, производители распредвалов часто предлагают уменьшить угол разделения лепестков, чтобы восстановить мощность, потерянную в более низком диапазоне оборотов».
Возвращаясь к звуку двигателя, не секрет, что хриплые, неровные холостые обороты часто предпочитают стритрейсеры, несмотря на дурные манеры и неэффективность такой настройки двигателя.Именно так хочет работать заказчик, и производители двигателей считают, что поставлять такую силовую установку несложно. Чака Лоуренса из Jon Kaase Racing Engines попросили придать 520ci BBF звук «Pro Stock», поэтому он выбрал 108 LSA вместо более традиционного 112 LSA.
«Результат звучал замечательно, но он не разгонялся с таким воодушевлением и выдавал на 30 лошадиных сил меньше, чем обычно», — говорит Лоуренс.
Подъем клапана будет иметь значение при принятии любого решения относительно LSA.
«Если бы вы изменили разнос лопастей уличного двигателя со 112 градусов на 106 и больше ничего не делали», — добавляет Каасе.«Двигатель будет работать на холостом ходу намного грубее и будет производить более тяжелые выбросы выхлопных газов в основном из-за несгоревшего топлива».
Одним из сегментов, который действительно выигрывает от более широкого LSA, является морской морской рынок. Боландер говорит, что эти кулачки помогают повышать крутящий момент контролируемым и предсказуемым образом, особенно в зонах без следа и вокруг доков. Они также снижают нагрузку на разгон.
«Кроме того, очень важно, чтобы перекрытие клапанов было сведено к минимуму, поскольку система впуска может создавать всасывание, которое втягивает воду в двигатель», — добавляет Боландер.
Опять же, это общепринятые рассуждения. Когда вводятся наддув или закись азота, и производители двигателей рассматривают выбор между распределительными валами с одинарным, двойным или обратным расположением валов, тогда обсуждение становится гораздо более техническим.
Усталостная прочность при кручении и износостойкость
В течение последних пяти лет использование собранных распределительных валов на автомобильном рынке Северной Америки неуклонно росло. Для клапанных механизмов, которые работают с роликовыми толкателями при относительно высоком контактном напряжении, распределительные валы в собранном виде представляют собой экономичное решение по сравнению с распределительными валами, изготовленными из кованых прутковых заготовок.Кованые подшипниковые стали и, в меньшей степени, порошковые кованые стали были предпочтительными материалами для изготовления кулачков распределительных валов в сборе. Спеченные сплавы представляют собой привлекательную альтернативу кованой стали, поскольку очень точные кулачки могут быть изготовлены путем прессования и спекания. Однако использование спеченных сплавов было ограничено их относительно низкими усталостными свойствами при контакте качения.
В этом документе представлено применение спеченных лепестков в механически собранных распределительных валах, которые работают в механизмах толкателей роликов при относительно высоком контактном напряжении.Кулачки кулачков были спрессованы и спечены до плотности в диапазоне 7,6-7,65 г/см 3 и цементированы до макротвердости 58-60 HRc. Лопасти были собраны на трубе из низколегированной стали. Интерференционное напряжение создавалось между трубой и компонентами за счет механического расширения трубы оправкой.
Ключевым функциональным аспектом распределительных валов в сборе является прочность сборки. В частности, статическая прочность на кручение и усталостная прочность связи между валом и кулачком или любым другим собранным компонентом e.г. ведущие звездочки, опорные подшипники и кулачки для унитарных дизельных форсунок. Статические и усталостные испытания на кручение показывают, что при относительно легкой конструкции (толщина стенки трубы в диапазоне 2-3 мм) можно достичь пределов прочности при статическом крутящем моменте в диапазоне 200-300 Нм и пределов усталостной выносливости при кручении в диапазоне 190-210 Нм. . Для тяжелых условий эксплуатации распределительные валы с толщиной стенки трубы 6 мм могут увеличить статическую прочность до 1500 Нм. Режимы статического и усталостного разрушения различаются.Статическое разрушение возникает в результате смещения лепестка относительно трубы. Напротив, при усталости при кручении разрушение происходит из-за усталости трубы, при этом трещина возникает в областях с высокой концентрацией напряжений. Благодаря правильной конструкции распределительного вала может быть достигнуто необходимое сочетание статической и усталостной прочности.
Разработанные спеченные сплавы имеют предел выносливости при контакте качения, который может превышать 2500 МПа. Распределительные валы, изготовленные из этих сплавов, были проверены в ходе испытаний двигателя с огнем, в том числе 3.4-литровый двигатель V6 с клапанным механизмом типа 5 (толкатель с роликовым толкателем), который работает при контактном напряжении около 2000 МПа. Было завершено три 300-часовых испытания мощности и одно 1000-часовое испытание в режиме ожидания. Спеченные кулачки кулачков не имели точечной коррозии, а износ кулачков был незначительным.
Движение кулачка — Список основных каталогов кулачков кулачка
ДВИЖЕНИЕ КУЛАЧКА — СПИСОК КУЛАЧКОВ
Конструкции кулачков распределительного вала, победившие в чемпионате
Чтобы выигрывать чемпионаты на самых высоких уровнях гонок, вы должны знать, как добиться большей мощности, чем у конкурентов.Первоочередной задачей при разработке распределительного вала, обеспечивающего мощность, является обеспечение стабильной и управляемой системы клапанов. Cam Motion более 30 лет занимается разработкой распределительных валов для гонок на уровне чемпионатов, что гарантирует, что вы получите более стабильные и мощные кулачки кулачка, чем любые другие конструкции на рынке.
Получите точную продолжительность и подъем, который вы хотите, с помощью Cam Motion
При работе с другими производителями вам придется просматривать мастер-каталоги кулачков и их различные типы кулачков распределительного вала в надежде найти кулачок, который правильно разработан для вашего применения и доступен в течение нужного вам периода времени. Теперь вы можете попрощаться с охотой на лепестков. Cam Motion позволяет легко получить идеальный дизайн лепестка. Просто сообщите нам все подробности о вашем двигателе, клапанном механизме, желаемой продолжительности и подъемной силе, и мы предоставим вам правильный лепесток, который будет оптимальным для вашего применения.
Cam Motion Список выступов распределительного вала с гидравлическим роликом
Ниже приведен список гидравлических лепестков распределительного вала, которые Cam Motion предлагает для двигателей Chevy серий LS и Gen 5 LT. Мы делаем продолжительность в 0,050 дюйма, которая варьируется от 193 до 282 градусов с шагом в один градус.Эти лепестки доступны в широком диапазоне подъемов с шагом подъема кулачков 0,005 дюйма. Как видите, благодаря уникальной способности Cam Motion создавать практически любые рабочие кулачки, которые вам нужны, это практически делает каталоги кулачков кулачков устаревшими. И наши лепестки спроектированы с помощью компьютера, чтобы обеспечить оптимальную производительность для их конкретного применения.
Никогда больше не соглашайтесь на лепесток, который «близок» к тому, что вам нужно. Получите точную продолжительность и подъем, который вы хотите. Позвоните в Cam Motion, чтобы заказать индивидуальный распределительный вал сегодня.
кулачковых лепестков | Начать гонку
Кулачки распределительного вала оказывают наибольшее влияние на то, когда впускные и выпускные клапаны открываются и закрываются, как долго они остаются открытыми и как далеко они перемещаются от седла.Поскольку производительность двигателя внутреннего сгорания напрямую связана с тем, насколько эффективно он перемещает воздух, жизненно важен лучший кулачок для этой работы. Но расшифровка кодов, чисел и углов, связанных с выбором распределительного вала на основе стольких параметров двигателя, может быть невероятно запутанной. «Существует так много переменных, что трудно уследить за ними всеми», — говорит Ричард Искендерян из Isky. «У нас четыре страницы профилей, у некоторых производителей даже больше».
Информация для оптимального выбора кулачка выходит далеко за рамки самого двигателя, поскольку следует учитывать такие факторы, как размер шин и вес автомобиля, а также крен гусеницы и радиус поворота.Каждый аспект влияет на оптимальную конструкцию кулачка и может значительно изменить соответствие кулачка. «Когда дело доходит до загадок, мы на первом месте с карбюраторами», — говорит Чейз Найт из Crane.
Кулачок состоит из ряда лепестков, расположенных под углом друг к другу вдоль вала. Каждый лепесток распределительного вала можно разделить на шесть отдельных областей.
Базовый круг или пятка — это место, где подъемник перемещается, когда клапан закрыт. Именно с этого участка лепестка начинаются все измерения.Когда распределительный вал вращается по часовой стрелке, подъемник перемещается по окружности основания кулачка к небольшому уклону, называемому рампой открытия, который обеспечивает небольшое увеличение подъемной силы и подготавливает подъемник к быстрому вертикальному ускорению на боковой стороне отверстия, где он быстро поднимается до достижения пика или нос.
Максимальный подъем находится в носовой части кулачка. Достигнув носа, подъемник быстро начинает возвращаться на замыкающий фланг, прежде чем закрывающаяся рампа постепенно переместит его на базовую окружность.
Продолжительность подъема измеряется в градусах поворота коленчатого вала. Это, казалось бы, простое измерение привело к большой путанице, поскольку некоторые производители основывали свои значения продолжительности на эффективной подъемной силе, в то время как другие измеряли с момента, когда клапан слегка отклонялся от седла, и заключали, когда он полностью вернулся. Они часто сообщали о 360° продолжительности.
Для единообразия был разработан отраслевой стандарт. Он ограничивает измерение продолжительности тем временем, когда лифтер находится на минимальном уровне.050″ от базовой окружности по мере движения. «Crane впервые установила показатели продолжительности подъема 0,050″, чтобы люди могли сравнивать кулачки», — говорит Найт.
В то время как стандарт подъема 0,050 дюйма хорошо служил гонщикам и отрасли на протяжении десятилетий, многие переосмысливают значение продолжительности подъема 0,050 дюйма. «Некоторые ребята покупают только числа 0,050″ по подъему и продолжительности», — говорит Дэйв Кроуэр из Crower. «Это может быть запутанным и бесплодным с точки зрения производительности».
Современные технологии проектирования и обработки сделали кулачки более специализированными в рамках типичных параметров, таких как продолжительность при .Лифт 050 дюймов. «В наши дни это такая маленькая часть уравнения», — говорит Найт. «У нас может быть пять разных кулачков с одинаковой продолжительностью и подъемной силой, но они могут быть для пяти совершенно разных целей: от улицы до овальной трассы с низкими оборотами, овальной трассы с высокими оборотами, гонок на выносливость и дрэг-рейсинга».
Дин Харви из Comp Cams говорит, что современные технологии проектирования, обработки и измерения означают, что среди кулачков, которые кажутся похожими, могут существовать значительные различия.«В некоторых случаях разница между кулачками невелика, если посмотреть на число .050″ и подъемную силу, но они могут сильно различаться по ускорению и другим параметрам», — говорит он. «Большинство производителей кулачков предоставляют значения длительности при различной высоте подъема».
Несмотря на изменения, производители по-прежнему рекомендуют гонщикам постоянно владеть терминологией распределительных валов. Искендерян говорит: «Эти термины действительны и сегодня, это уточнение того, что вы можете делать с лепестками.
Дело не только в форме лепестков, их взаимодействие друг с другом оказывает огромное влияние на производительность. Угол разделения лепестков — это расстояние, измеренное между осевой линией впускного лепестка и осевой линией выпускного кулачка, выраженное в градусах.
Угол разделения лепестков напрямую влияет на диапазон крутящего момента и качество холостого хода. Широкий угол разделения кулачков (угол от 110 до 114 градусов) поднимет диапазон крутящего момента так, что максимальный крутящий момент и мощность будут достигаться при более высоких оборотах, обеспечивая при этом более плавный холостой ход.Гонщики на шорт-треке обычно выбирают более узкий угол (от 104 до 106 градусов).
Время, в течение которого впускной и выпускной клапаны одного и того же цилиндра открыты, называется перекрытием. Он обратно пропорционален углу разделения лепестков, поскольку сужение угла разделения лепестков увеличивает перекрытие.
Вы будете платить одинаковую сумму за детали независимо от того, покупаете ли вы камеру, наиболее подходящую для вашего приложения, или ту, которая не подходит. «Это гораздо больше, чем выбор подъема, продолжительности и центральной линии», — говорит Найт.«Работа с производителем двигателей, который имеет опыт работы со всеми компонентами, которые должны работать вместе, имеет смысл».
Джессика Дио и Карл Фредриксон
Основы работы с распределительным валом и клапанным механизмом
Кулачки, подъемники, толкатели, коромысла, пружины, фиксаторы, клапаны
ПРИМЕЧАНИЕ. Все наши продукты, дизайны и услуги являются ОРГАНИЧЕСКИМИ, БЕЗ ГЛЮТЕНОВ, ГМО и не огорчают чьи-либо драгоценные ЧУВСТВА
ФОН
Как мы представили в предыдущем разделе, пропускная способность головок цилиндров, впускных и выпускных каналов в 4-тактном
(«Четырехтактный») чрезвычайно важен для работы двигателя. Однако движение створок относительно положения
а скорость поршня, возможно, даже более важна для определения мощности, которую может производить данная конфигурация.
Движение клапана создается формой выступа кулачка, который давит на какой-то толкатель кулачка, который затем соединяет к клапану с помощью различных механизмов. Система, которая нас больше всего интересует, — это толкатель кулачка в отверстии, приводящий толкатель, который перемещает поворотный рычаг («коромысло»), который давит на кончик клапана и сообщает возвратно-поступательное движение открыть клапан.В этой системе закрытие клапана осуществляется пружиной клапана. Следующее изображение (любезно предоставлено Ford Motor Company ) показывает компоненты этой системы.
Рисунок 1: Поперечное сечение двигателя толкателя (Ford Smallblock)
Система, которой посвящена эта статья, толкатель / коромысло / верхний клапанный механизм, использовалась в отечественных автомобильных двигателях с начала 20-го века из-за явно превосходной дышащей способности, обеспечиваемой «клапаном». «в головке» по сравнению с распространенной конструкцией двигателя с «боковым клапаном» или «плоской головкой», в которой клапаны находятся в блоке цилиндров рядом с цилиндрами.
Эта система использовалась в начале массового производства в Chevrolet inline-4, который производился до 1936 года и который был заменен Chevrolet inline 6, начиная с 1935 года. Система стала доминировать в автомобильных двигателях внутреннего производства, начиная с Oldsmobile «Rocket» 324 1949 года. кубический дюйм V8. Из-за присущей ей производительности и экономической эффективности система OHV с толкателем / коромыслом продолжала совершенствоваться и до сих пор используется во многих современных (начало 21 века) двигателях.Одним из наиболее примечательных является плодовитое семейство отличных двигателей GM smallblock V8 4-го поколения (семейство двигателей «LS»).
Обратите внимание, что существует множество других систем, начиная от примитивных двигателей с «боковым клапаном», в которых кулачок приводит в действие толкатель в отверстии, который затем непосредственно управляет клапаном, до множества различных конфигураций верхнего кулачка, которые управляют клапанами либо напрямую от толкателя кулачка («прямого действия») или с помощью любой из нескольких различных реализаций коромысла, и достигает чрезвычайной сложности с системами, в которых есть один профиль кулачка для открытия клапана и другой дополнительный профиль кулачка, который непосредственно закрывает клапан. клапан, устраняющий необходимость в пружине клапана (известные как «десмодромные» системы).
Вот более подробное описание этой системы с толкателем и верхним клапаном. В 4-тактном двигателе коленчатый вал приводит в движение распределительный вал со скоростью, равной 1/2 скорости коленчатого вала (очевидно, поскольку каждый клапан открывается и закрывается один раз за каждые два оборота коленчатого вала). Распределительный вал обычно содержит по одной кулачковой кулачке для каждого клапана в двигателе, хотя это не обязательно так. (Например, в двигателях оппозитной компоновки, таких как двигатели VW-Porsche с горизонтально-оппозитными толкателями, два впускных клапана, по одному с каждой стороны двигателя, приводятся в действие одним кулачком, приводящим в движение два разных толкателя.) Для удобства рисунок 1 воспроизведен ниже, чтобы помочь в последующем описании.
Рисунок 1 (повторно): Поперечное сечение двигателя толкателя (Ford Smallblock)
ОСНОВЫ
При вращении каждого кулачка он контактирует с толкателем кулачка (он же «подъемник», он же «толкатель») и отводит толкатель от оси вращения распределительного вала. Кулачковый толкатель, ограниченный отверстием, в котором он перемещается, производит линейное движение вдоль оси отверстия.Это линейное движение толкателя передается на один конец толкателя. Другой конец толкателя движется несколько менее предсказуемо, сдерживаемый гнездом толкателя в коромысле, но также подвергается отклонениям изгиба толкателя, как сжимающим, так и изгибающим, которые зависят от сил и возбуждений, приложенных к толкателю. Коромысло вращается вокруг своей оси вращения (обычно либо вала, либо полушария на шпильке), а другой конец коромысла контактирует с кончиком штока клапана и заставляет клапан двигаться вдоль оси отверстия. («направляющая клапана») в которой он едет.
Иногда полагают, что выступ кулачка может непосредственно управлять лишь открывающей частью движения клапана, отталкивая толкатель от него, а пружина клапана управляет закрывающей половиной цикла.
Это мнение очень неверно. На самом деле кулачок и пружина клапана при правильной работе работают в тесной гармонии на протяжении всего цикла открытия-закрытия, создавая желаемое движение клапана. Кулачок обеспечивает рабочее усилие примерно в первой половине цикла открытия и последней половине цикла закрытия, а пружина клапана обеспечивает рабочее усилие примерно в течение последней половины цикла открытия и первой половины цикла закрытия. цикл.Эта концепция станет более ясной позже в ходе обсуждения.
Прекрасным примером влияния профилей кулачков на рабочие характеристики является эволюция так называемых «ограниченных» гоночных двигателей. Эти двигатели «ограничены» в отношении модификаций, которые могут быть в них внесены, с целью ограничить мощность и, следовательно, ограничить (теоретически, но не на практике) стоимость двигателей.
Наиболее распространенным двигателем в этой категории является малоблочный Chevy (SBC) V8 с железным блоком объемом 355 кубических дюймов, который обычно ограничивается серийными (непортированными, немодифицированными) чугунными головками цилиндров и впускными коллекторами.В некоторых классах эти двигатели ограничены одним двухкамерным карбюратором, который в стандартной комплектации не может пропускать более 500 кубических футов в минуту воздуха при перепаде давления в 3 дюйма вод. -ограниченный» двигатель.
В начале разработки этих двигателей максимальная мощность, которую мы могли получить от этих двигателей, была около 425 л.с. (что само по себе впечатляет). Примерно с 2006 года мы превысили 500 л.с. и постоянно, но медленно приближаемся к 525, используя по существу те же головки и коллекторы (как указано в правилах NASCAR для этих двигателей).Все эти разработки стоят ДЕНЬГИ, а стоимость этих двигателей непомерно высока для многих гонщиков.
Одним из основных факторов этого прогресса стала разработка все более агрессивных профилей кулачков, оптимизированных для этой конкретной конфигурации с ограничением потока. Конечно, как и следовало ожидать, эти профили кулачков очень тяжело воздействуют на компоненты клапанного механизма, поэтому успешная работа системы зависит от разработки все более сложных компонентов клапанного механизма.Здесь мы попытаемся объяснить, почему и как различные требования могут быть удовлетворены за счет различных компромиссов, принятых в конструкции кулачка.
Учитывая неотъемлемые ограничения этой компоновки при высоких оборотах двигателя, это огромная дань уважения навыкам и знаниям производителей двигателей NASCAR на уровне «Кубка», что они преуспели в создании этого типа двигателя (358 кубических дюймов, с плоским толкателем, толкателем / коромыслом, с двумя клапанами на цилиндр, без наддува, с одним карбюратором V8) надежно работают при скорости более 9500 об / мин и обеспечивают беспрецедентный уровень мощности (более 860 л.с. по состоянию на 2012 г.) в течение нескольких часов. вовремя.(Чтобы узнать больше об этих удивительных двигателях, НАЖМИТЕ ЗДЕСЬ.)
Причина, по которой мы сосредоточили внимание на этой конфигурации, заключается в том, что в отношении авиационных двигателей мы считаем, что эта система толкатель/коромысло является лучшим решением компромиссов, необходимых для достижения хорошего авиационного двигателя: (a) максимальная мощность на фунт веса двигателя в сочетании с (b) разумными скоростями поршня и нагрузками на клапанный механизм для максимальной надежности. Мы обеспечим поддержку этого аргумента по ходу статьи.
Нет никаких сомнений в том, что двигатель с конфигурацией с двумя верхними распредвалами (DOHC) и четырьмя клапанами на цилиндр будет производить больше мощности на кубический дюйм рабочего объема, но это превосходство происходит из-за превосходных дышащих свойств, чем у 4-цилиндрового двигателя. конфигурация клапана обеспечивает при высоких оборотах двигателя и более точное движение клапана, которое конфигурация с верхним расположением распредвала обеспечивает при высоких оборотах двигателя. Однако ограничения надежности исторически препятствовали использованию высоких оборотов двигателя в авиационных двигателях, поэтому дополнительный вес конфигурации DOHC имеет тенденцию благоприятствовать компоновке толкатель / коромысло.
ДВИЖЕНИЕ КУЛАЧКОВОГО ПОСЛЕДОВАТЕЛЯ
Основные события распределительного вала (открытие, закрытие и максимальный подъем клапана) обычно относятся к положению коленчатого вала, поскольку движение клапанов необходимо изучать относительно положения (и скорости) поршня. Например, типичный впускной лепесток может начать открывать клапан за 20 градусов до верхней точки (BTC, до того, как поршень достигнет точной верхней точки своего хода) и закончить закрытие клапана за 50 градусов после нижней мертвой точки (BDC).И да, поршень все еще движется вверх, когда впускной клапан открывается, и также движется вверх, когда впускной клапан закрывается. Эта и другие очевидные аномалии связаны с динамикой движения воздуха и будут обсуждаться позже.
Вот график, показывающий осевое перемещение толкателей одного цилиндра двухклапанного (один впускной, один выпускной) двигателя в зависимости от вращения распределительного вала. Красная кривая — это ход выхлопного патрубка, а синяя — это ход впускного патрубка.Обратите внимание, что ось вращения показана в градусах вращения коленчатого вала (что в два раза больше, чем вращение распределительного вала, поскольку в 4-тактном двигателе распредвал вращается с половиной скорости вращения коленчатого вала). Изображенные здесь лепестки обеспечивают максимальный подъем лепестков примерно на 0,420 дюйма. Этот подъем кулачка, работающий при номинальном передаточном числе коромысла 1,6, теоретически обеспечивает почти 0,675 подъема клапана.
Рисунок 2: Положение толкателя кулачка в зависимости от положения коленчатого вала
Наиболее часто упоминаемыми характеристиками кулачковых кулачков являются подъем, продолжительность, перекрытие и разделение лепестков.Спецификация «Подъем» — это максимальный ход, который испытывает толкатель кулачка, когда кулачок кулачка вращается под ним. «Точка нулевой подъемной силы» может быть определена как подъемная сила, когда лепесток поворачивается на 180 градусов от точки максимальной подъемной силы, когда говорят, что толкатель кулачка находится в точке 90 375 «на базовой окружности» 90 376 (участок с постоянным радиусом) кулачка. доля.
«Продолжительность» – это количество градусов поворота коленчатого вала, в течение которых подъем толкателя кулачка превышает некоторое заданное значение. Без знания значения подъема лепестка, при котором измеряется продолжительность, значение продолжительности не имеет смысла. Это связано с тем, что выступ кулачка содержит наклоны замедленного движения в начале и в конце периода подъема (подробности ниже), чтобы использовать зазоры и постепенно приводить детали в движение. Свойства этих аппарелей могут сильно различаться в зависимости от предполагаемого использования конкретной конструкции лепестка и предпочтений разработчика лепестка, поэтому спецификация кулачка, которая оценивает продолжительность этих медленных периодов взлета и посадки, просто обманчива.
Стало общепринятой отраслевой практикой (инициированной Харви Крейном еще в 1960-х годах) указывать продолжительность лепестка как количество градусов между точками открытия и закрытия, в которых подъемник равен 0.050 от базового круга.
Перекрытие, относящееся к рис. 2 выше, представляет собой число градусов поворота коленчатого вала, в течение которого оба клапана находятся вне своих седел одновременно, и измеряется как число градусов вращения коленчатого вала, в течение которого оба толкателя находятся в большем заданное расстояние от точки нулевой подъемной силы (вне базовой окружности). Опять же, без этого справочного номера спецификация перекрытия практически бесполезна. Если мы используем исходное значение подъема толкателя 0,050, перекрытие кулачка, показанного на рис. 2 , составляет примерно 40 градусов.
Перекрытие, как мы обсудим позже, очень важно влияет на работу двигателя. Эд Искендерян, один из первых разработчиков распределительных валов вторичного рынка, называл перекрытие «5-м циклом».
Рис. 3 ниже представляет собой расширенную версию профиля подъема впускного лепестка, показанного на Рис. 2 . Ось подъемной силы не обозначена, но каждое деление по вертикальной оси соответствует 0,050 подъемной силы лепестка.
Рис. 3: Профиль движения кулачка (подъемника)
Как показано на рис. 3 , кулачок начинает перемещать толкатель и клапанный механизм примерно за 60 градусов до верхней мертвой точки (BTC) и не прекращает движение клапанного механизма примерно до 95 градусов ПОСЛЕ нижней мертвой точки (ABC) . Однако ясно, что движение (крутизна профиля подъемной силы), наиболее близкое к точкам открытия и закрытия, является относительно медленным по сравнению с движением, например, в точке ВМТ.
Теперь, как и следовало ожидать, на реальном двигателе может быть трудно определить с достаточной точностью точное положение коленчатого вала, когда клапан начинает открываться или закрываться, из-за постепенности движения в этих точках. И точное значение положения коленчатого вала относительно точек открытия или закрытия может резко измениться за счет изменения статического зазора между клапаном и механизмом, который его перемещает (коромысло или кулачковый толкатель).
Ситуация не сильно улучшится, если вместо движения клапана для определения этих точек использовать движение подъемника. Причина в том, что выступ кулачка не приводит в движение подъемник внезапно. Каждый лепесток кулачка включает открывающиеся и закрывающиеся «пандусы», которые позволяют кулачку постепенно начинать и заканчивать движение подъемника. Таким образом, современный метод определения событий кулачка кулачка состоит в том, чтобы указать число градусов до и после ВМТ/НМТ, при котором подъемник переместился на расстояние, равное 0.050″ от его «положения нулевого движения» . Положение нулевого движения измеряется, когда толкатель находится на части поверхности лепестка с нулевой подъемной силой (известной как «базовая окружность» или «пятка» лепестка) и максимальная подъемная часть выступа кулачка находится напротив толкателя (180° от него).
Две темные вертикальные линии на Рисунок 3 (слева от ВМТ и справа от НМТ) показывают 0,050 точки подъема на профиле открытия и закрытия, где крутизна профиля подъема немного увеличилась.Эти 0,050 точки подъема приходятся на 20 градусов до ВМТ и 58 градусов до ВМТ.
Со ссылкой на обычные точки подъема лепестка 0,050, продолжительность этого лепестка составляет 258 градусов (20 градусов до ВМТ, плюс 180 градусов от ВМТ до НМТ, плюс 58 градусов до НМТ). Что касается влияния на характеристики двигателя, эта цифра продолжительности 0,050 гораздо более значима, чем то, что некоторые производители рекламируют как продолжительность этой доли (336 градусов, взятые при 0,003 точки подъема).
Осевая линия лепестка (точка максимального подъема лепестка, показанная зеленой линией) расположена под углом 105 градусов после ВМТ.В этом примере центральная линия проходит посередине между событиями открытия и закрытия. Однако это не обязательно так. Теперь мы часто используем лепестки с профилями подъема, которые асимметричны относительно центральной линии, чтобы адаптировать скорость открытия и закрытия для различных целей.
Следующая кривая (Рисунок 4) показывает тот же профиль подъема (синий), что и на Рисунке 3 выше, но кое-что было добавлено. Красная кривая представляет скорость толкателя по отношению к вращению кулачка в дюймах на градус (или мм на градус, если вы используете метрическую систему). .
Рисунок 4: Профили движения и скорости кулачка (подъемника)
Следующая кривая показывает ускорение (черный цвет) и скорость следящего механизма (красный), которые соответствуют кривой подъема толкателя (синяя).
Рисунок 5: Профили движения, скорости и ускорения кулачка (подъемника)
Кулачок кулачка обеспечивает «запрограммированное» движение кулачкового толкателя на протяжении всего цикла. Приблизительно в течение первой 1/4 цикла кулачок также обеспечивает силу, которая ускоряет компоненты клапанного механизма (толкатель, толкатель, коромысло, клапан, фиксатор, фиксатор и пружина) в направлении открытия.В течение последней примерно 1/4 цикла выступ кулачка обеспечивает усилие, которое тормозит быстро движущиеся компоненты клапанного механизма до упора и позволяет клапану плавно закрыться на седле клапана. Во время средней половины цикла пружина клапана создает усилия, необходимые для замедления компонентов до остановки при максимальном подъеме клапана и для ускорения этих компонентов от этой мгновенной остановки до высокой скорости обратно в направлении закрытия клапана.
На следующем графике показано движение подъемника, вызванное двумя разными выступами кулачка, оба из которых имеют одинаковые характеристики открытия и закрытия (согласно измерению 0.050″ точек хода подъемника). Эти графики известны как «кривые подъема». Горизонтальная ось представляет собой вращение коленчатого вала относительно ВМТ и НМТ.
Рисунок 6: Сравнение профиля движения кулачка (подъемника)
Как видите, обе кривые подъемной силы выглядят довольно гладкими. Однако существует существенная разница между силой и вибрацией, которую каждая из этих двух лепестков оказывает на остальную часть клапанного механизма, которым они управляют. Эти различия можно увидеть, только изучив кривые, которые показывают скорость и ускорение, создаваемые этими лепестками.
Рисунок 7: Сравнение движения, скорости и ускорения кулачка (подъемника)
Еще не все:
Кривые: подробные пояснения и подробности о предыдущих кривых
Кулачковые толкатели: плоскоцилиндрические, плоско-грибовидные, радиусные, роликовые, коромысла
Толкатели: цилиндрические, конические, Эйлера -колонна, жесткость, масса
Коромысел: вал, опора, плоский конец, роликовый конец, игольчатый подшипник, гладкий
подшипник, сферический шарнир, mmoi
Пружины: одинарные, двойные, тройные, реверс-комплект, круглая проволока, овальная проволока, скорость, частота рез, масса
Возбуждения: подъемная сила, ускорение, содержание кривых Фурье
Силы и Прогибы: ускорение , вибрация
, резонансные точки
