Π’ΠΈΠΏΡ ΡΠΎΡΠΌΠΎΠ·Π½ΡΡ ΠΌΠ΅Ρ Π°Π½ΠΈΠ·ΠΌΠΎΠ² β ΠΠ°Π·Π½Π°ΡΠ΅Π½ΠΈΠ΅ ΠΈ ΡΠΈΠΏΡ ΡΠΎΡΠΌΠΎΠ·Π½ΡΡ ΡΠΈΡΡΠ΅ΠΌ Π°Π²ΡΠΎΠΌΠΎΠ±ΠΈΠ»Ρ.
ΠΠΈΠ΄Ρ ΡΠΎΠ²ΡΠ΅ΠΌΠ΅Π½Π½ΡΡ ΡΠΎΡΠΌΠΎΠ·Π½ΡΡ ΡΠΈΡΡΠ΅ΠΌ
ΠΠ½ΠΆΠ΅Π½Π΅ΡΡ ΡΠΏΡΠ°Π²Π΅Π΄Π»ΠΈΠ²ΠΎ Π½Π°Π·ΡΠ²Π°ΡΡ ΡΠΎΡΠΌΠΎΠ·Π½ΡΡ ΡΠΈΡΡΠ΅ΠΌΡ Π°Π²ΡΠΎΠΌΠΎΠ±ΠΈΠ»Ρ ΠΎΡΠ½ΠΎΠ²Π½ΠΎΠΉ ΡΠΎΡΡΠ°Π²Π»ΡΡΡΠ΅ΠΉ Π»ΡΠ±ΠΎΠ³ΠΎ ΡΡΠ°Π½ΡΠΏΠΎΡΡΠ½ΠΎΠ³ΠΎ ΡΡΠ΅Π΄ΡΡΠ²Π°. ΠΠ°Π΄Π°ΡΠ΅ΠΉ ΡΡΠΎΠ³ΠΎ ΡΡΡΡΠΎΠΉΡΡΠ²Π° ΡΠ²Π»ΡΠ΅ΡΡΡ ΠΎΠ±Π΅ΡΠΏΠ΅ΡΠ΅Π½ΠΈΠ΅ Π±Π΅Π·ΠΎΠΏΠ°ΡΠ½ΠΎΡΡΠΈ Π²ΠΎ Π²ΡΠ΅ΠΌΡ Π΄Π²ΠΈΠΆΠ΅Π½ΠΈΡ. ΠΠΌΠ΅Ρ Π² ΡΠ°ΡΠΏΠΎΡΡΠΆΠ΅Π½ΠΈΠΈ ΡΠΎΡΠΌΠΎΠ·, Π²ΠΎΠ΄ΠΈΡΠ΅Π»Ρ ΠΌΠΎΠΆΠ΅Ρ Π²ΠΎΠ²ΡΠ΅ΠΌΡ Π·Π°ΠΌΠ΅Π΄Π»ΠΈΡΡ Ρ ΠΎΠ΄, Π»ΠΈΠ±ΠΎ ΠΆΠ΅ ΠΎΡΡΠ°Π½ΠΎΠ²ΠΈΡΡ ΠΌΠ°ΡΠΈΠ½Ρ ΠΏΠΎΠ»Π½ΠΎΡΡΡΡ. ΠΠΎΠΏΠΎΠ»Π½ΠΈΡΠ΅Π»ΡΠ½ΡΠ΅ ΡΠΈΡΡΠ΅ΠΌΡ Π°ΠΊΡΠΈΠ²Π½ΠΎ ΠΏΠΎΠΌΠΎΠ³Π°ΡΡ ΠΏΡΠΈ Π΅Π·Π΄Π΅ ΠΈ Π²ΠΎ Π²ΡΠ΅ΠΌΡ ΡΡΠΎΡΠ½ΠΊΠΈ ΡΡΠ°Π½ΡΠΏΠΎΡΡΠ°. ΠΡΠ»ΠΈ ΠΈΠ·ΡΡΠΈΡΡ ΠΈΡΠΊΠ»ΡΡΠΈΡΠ΅Π»ΡΠ½ΠΎ ΠΌΠ΅Ρ Π°Π½ΠΈΡΠ΅ΡΠΊΠΈΠ΅ ΠΊΠΎΠΌΠΏΠΎΠ½Π΅Π½ΡΡ, Π½ΠΈΡΠ΅Π³ΠΎ ΡΠ»ΠΎΠΆΠ½ΠΎΠ³ΠΎ Π² ΡΠΈΡΡΠ΅ΠΌΠ΅ ΡΠΎΡΠΌΠΎΠΆΠ΅Π½ΠΈΡ Π²Ρ Π½Π΅ ΡΠ²ΠΈΠ΄ΠΈΡΠ΅. ΠΠ½Π° ΡΠΎΡΡΠΎΠΈΡ ΠΏΡΠ΅ΠΈΠΌΡΡΠ΅ΡΡΠ²Π΅Π½Π½ΠΎ ΠΈΠ· ΠΏΡΠΈΠ²ΠΎΠ΄Π° ΠΈ ΠΈΡΠΏΠΎΠ»Π½ΠΈΡΠ΅Π»ΡΠ½ΡΡ ΠΌΠ΅Ρ Π°Π½ΠΈΠ·ΠΌΠΎΠ². ΠΡΠΎΡ ΠΏΡΠΈΠ½ΡΠΈΠΏ ΡΡΡΡΠΎΠΉΡΡΠ²Π° ΠΏΡΠΈΠΌΠ΅Π½ΡΠ΅ΡΡΡ Π½Π° Π²ΡΠ΅Ρ ΡΠΎΡΠΌΠΎΠ·Π°Ρ . ΠΠΎ ΡΠΎΠ²ΡΠ΅ΠΌΠ΅Π½Π½ΡΠ΅ Π°Π²ΡΠΎΠΌΠΎΠ±ΠΈΠ»ΠΈ ΠΏΠΎΡΠ»ΠΈ Π½Π°ΠΌΠ½ΠΎΠ³ΠΎ Π΄Π°Π»ΡΡΠ΅. ΠΡΠΎΠΈΠ·Π²ΠΎΠ΄ΠΈΡΠ΅Π»ΠΈ Π½Π°ΡΠ°Π»ΠΈ ΠΈΡΠΏΠΎΠ»ΡΠ·ΠΎΠ²Π°ΡΡ Π²ΡΠΏΠΎΠΌΠΎΠ³Π°ΡΠ΅Π»ΡΠ½ΡΠ΅ ΡΠΈΡΡΠ΅ΠΌΡ, Ρ ΠΏΠΎΠΌΠΎΡΡΡ ΠΊΠΎΡΠΎΡΡΡ ΡΠ΄Π°Π»ΠΎΡΡ ΠΏΠΎΠ²ΡΡΠΈΡΡ ΡΡΡΠ΅ΠΊΡΠΈΠ²Π½ΠΎΡΡΡ ΡΠ°Π±ΠΎΡΡ ΡΠΎΡΠΌΠΎΠ·ΠΎΠ².
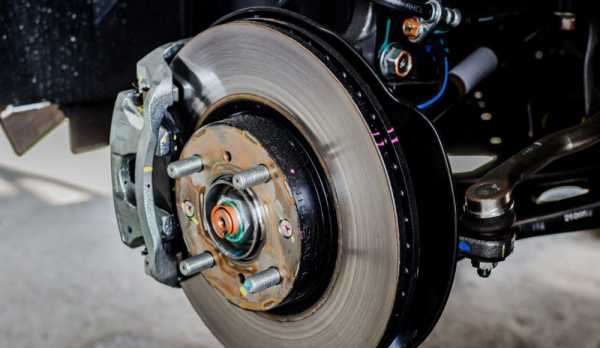
ΠΠΈΠ΄Ρ
ΠΠ»Ρ Π½Π°ΡΠ°Π»Π° Π½ΡΠΆΠ½ΠΎ ΠΏΠΎΠ·Π½Π°ΠΊΠΎΠΌΠΈΡΡΡΡ Ρ Π²ΠΈΠ΄Π°ΠΌΠΈ ΡΠΎΡΠΌΠΎΠ·Π½ΡΡ ΡΠΈΡΡΠ΅ΠΌ, ΠΊΠΎΡΠΎΡΡΠ΅ ΠΈΡΠΏΠΎΠ»ΡΠ·ΡΡΡΡΡ Π½Π° ΡΡΠ°Π½ΡΠΏΠΎΡΡΠ½ΡΡ ΡΡΠ΅Π΄ΡΡΠ²Π°Ρ . Π’ΠΎΡΠΌΠΎΠ·Π° ΠΈΡΠΏΠΎΠ»ΡΠ·ΡΡΡΡΡ Ρ ΡΠ°ΠΌΠΎΠ³ΠΎ ΠΏΠΎΡΠ²Π»Π΅Π½ΠΈΡ ΠΏΠ΅ΡΠ²ΡΡ ΠΌΠ°ΡΠΈΠ½. Π’ΠΎΠ³Π΄Π° ΠΊΠΎΠ½ΡΡΡΡΠΊΡΠΈΡ Π±ΡΠ»Π° ΠΏΡΠ΅Π΄Π΅Π»ΡΠ½ΠΎ ΠΏΡΠΎΡΡΠ°Ρ ΠΈ ΠΏΡΠΈΠΌΠΈΡΠΈΠ²Π½Π°Ρ. ΠΠΎ ΠΈ Π΅Ρ Ρ Π²Π°ΡΠ°Π»ΠΎ Π΄Π»Ρ ΠΎΠ±Π΅ΡΠΏΠ΅ΡΠ΅Π½ΠΈΡ ΡΡΡΠ΅ΠΊΡΠΈΠ²Π½ΠΎΠ³ΠΎ ΡΠΎΡΠΌΠΎΠΆΠ΅Π½ΠΈΡ ΠΈΠ·-Π·Π° ΠΌΠ°Π»ΠΎΠΉ ΠΌΠ°ΠΊΡΠΈΠΌΠ°Π»ΡΠ½ΠΎΠΉ ΡΠΊΠΎΡΠΎΡΡΠΈ. ΠΠΎ ΠΏΠΎΡΡΠ΅ΠΏΠ΅Π½Π½ΠΎ ΠΌΠ°ΡΠΈΠ½Ρ ΡΡΠ°Π½ΠΎΠ²ΠΈΠ»ΠΈΡΡ Π±ΡΡΡΡΠ΅Π΅. ΠΡΠΎ Π·Π°ΡΡΠ°Π²ΠΈΠ»ΠΎ ΠΏΡΠΎΠΈΠ·Π²ΠΎΠ΄ΠΈΡΠ΅Π»Π΅ΠΉ ΡΠ°Π·ΡΠ°Π±Π°ΡΡΠ²Π°ΡΡ Π±ΠΎΠ»Π΅Π΅ Π΄Π΅ΠΉΡΡΠ²Π΅Π½Π½ΡΠ΅ ΠΈ ΡΠ»ΠΎΠΆΠ½ΡΠ΅ ΡΠΎΡΠΌΠΎΠ·Π½ΡΠ΅ ΠΌΠ΅Ρ Π°Π½ΠΈΠ·ΠΌΡ. ΠΡΠ»ΠΈ Π³ΠΎΠ²ΠΎΡΠΈΡΡ ΠΎ ΡΠ°Π·Π½ΠΎΠ²ΠΈΠ΄Π½ΠΎΡΡΡΡ , ΡΠΎ ΠΊΠ»Π°ΡΡΠΈΡΠΈΠΊΠ°ΡΠΈΡ ΡΠΎΡΠΌΠΎΠ·Π½ΡΡ ΡΠΈΡΡΠ΅ΠΌ Π΄Π»Ρ Π°Π²ΡΠΎΠΌΠΎΠ±ΠΈΠ»Π΅ΠΉ ΠΏΡΠ΅Π΄ΡΡΠΌΠ°ΡΡΠΈΠ²Π°Π΅Ρ Π½Π΅ΡΠΊΠΎΠ»ΡΠΊΠΎ ΡΠ°Π·Π½ΡΡ ΡΠ΅ΡΠ΅Π½ΠΈΠΉ Π² Π·Π°Π²ΠΈΡΠΈΠΌΠΎΡΡΠΈ ΠΎΡ:
- Π½Π°Π·Π½Π°ΡΠ΅Π½ΠΈΡ;
- ΠΏΡΠΈΠ²ΠΎΠ΄Π°;
- ΡΠ°Π±ΠΎΡΠΈΡ ΠΌΠ΅Ρ Π°Π½ΠΈΠ·ΠΌΠΎΠ².
ΠΠΎΡΠΊΠΎΠ»ΡΠΊΡ Π² ΡΠΎΡΠΌΠΎΠΆΠ΅Π½ΠΈΠΈ ΠΏΡΠΈΠ½ΠΈΠΌΠ°Π΅Ρ ΡΡΠ°ΡΡΠΈΠ΅ ΡΠ΅Π»ΡΠΉ ΡΡΠ΄ ΡΠ»Π΅ΠΌΠ΅Π½ΡΠΎΠ² ΠΈ Π°Π³ΡΠ΅Π³Π°ΡΠΎΠ², Π½ΡΠΆΠ½ΠΎ ΠΏΠΎΠ½ΡΡΡ, ΡΠ΅ΠΌ ΡΠΈΡΡΠ΅ΠΌΡ Π΄ΡΡΠ³ ΠΎΡ Π΄ΡΡΠ³Π° ΠΎΡΠ»ΠΈΡΠ°ΡΡΡΡ.
ΠΠ°Π·Π½Π°ΡΠ΅Π½ΠΈΠ΅
ΠΠ°ΡΠ½ΡΠΌ Ρ Π½Π°Π·Π½Π°ΡΠ΅Π½ΠΈΠΉ ΠΈ ΡΠΈΠΏΠΎΠ² ΡΠΎΡΠΌΠΎΠ·Π½ΡΡ ΡΠΈΡΡΠ΅ΠΌ. ΠΠ΅Π³ΠΊΠΎΠ²ΡΠ΅ ΠΌΠ°ΡΠΈΠ½Ρ ΠΏΡΠ΅Π΄ΡΡΠΌΠ°ΡΡΠΈΠ²Π°ΡΡ ΠΈΡΠΏΠΎΠ»ΡΠ·ΠΎΠ²Π°Π½ΠΈΠ΅ ΡΠ°Π±ΠΎΡΠ΅Π³ΠΎ ΠΈ ΡΡΠΎΡΠ½ΠΎΡΠ½ΠΎΠ³ΠΎ ΡΠΎΡΠΌΠΎΠ·Π°. Π ΡΠΎΠ»ΠΈ Π΄ΠΎΠΏΠΎΠ»Π½ΠΈΡΠ΅Π»ΡΠ½ΡΡ ΡΡΡΡΠΎΠΉΡΡΠ² Π²ΡΡΡΡΠΏΠ°ΡΡ ΡΠ΅Π·Π΅ΡΠ²Π½ΡΠ΅ ΠΈ Π³ΠΎΡΠ½ΡΠ΅ ΡΠΈΡΡΠ΅ΠΌΡ ΡΠΎΡΠΌΠΎΠΆΠ΅Π½ΠΈΡ. Π Π°Π±ΠΎΡΠΈΠΉ ΡΠΈΠΏ ΡΠΎΡΠΌΠΎΠ·Π½ΠΎΠΉ ΡΠΈΡΡΠ΅ΠΌΡ Π»Π΅Π³ΠΊΠΎΠ²ΡΡ Π°Π²ΡΠΎΠΌΠΎΠ±ΠΈΠ»Π΅ΠΉ Π·Π°ΠΌΠ΅Π΄Π»ΡΠ΅Ρ Π΄Π²ΠΈΠΆΠ΅Π½ΠΈΠ΅ ΡΡΠ°Π½ΡΠΏΠΎΡΡΠ° ΠΈ ΠΏΠΎΠ·Π²ΠΎΠ»ΡΠ΅Ρ ΠΏΠΎΠ»Π½ΠΎΡΡΡΡ ΠΎΡΡΠ°Π½ΠΎΠ²ΠΈΡΡΡΡ. ΠΡΠΎΠ±Π΅Π½Π½ΠΎΡΡΡΡ ΡΠ²Π»ΡΠ΅ΡΡΡ ΡΠΎ, ΡΡΠΎ ΠΈΠ½ΡΠ΅Π½ΡΠΈΠ²Π½ΠΎΡΡΡ ΡΠ½ΠΈΠΆΠ΅Π½ΠΈΡ ΡΠΊΠΎΡΠΎΡΡΠΈ Π½Π°ΠΏΡΡΠΌΡΡ Π·Π°Π²ΠΈΡΠΈΡ ΠΎΡ ΡΠΎΠ³ΠΎ, ΠΊΠ°ΠΊ ΡΠΈΠ»ΡΠ½ΠΎ Π²ΠΎΠ΄ΠΈΡΠ΅Π»Ρ Π½Π°ΠΆΠΈΠΌΠ°Π΅Ρ Π½Π° ΡΠΎΠΎΡΠ²Π΅ΡΡΡΠ²ΡΡΡΡΡ ΠΏΠ΅Π΄Π°Π»Ρ. ΠΠ°Π·Π²Π°Π½ΠΈΠ΅ ΡΡΠΎΡΠ½ΠΎΡΠ½ΠΎΠ³ΠΎ ΡΠΎΡΠΌΠΎΠ·Π° Π³ΠΎΠ²ΠΎΡΠΈΡ ΡΠ°ΠΌΠΎ Π·Π° ΡΠ΅Π±Ρ. Π‘ Π΅Π³ΠΎ ΠΏΠΎΠΌΠΎΡΡΡ ΠΌΠ°ΡΠΈΠ½Π° Π±Π»ΠΎΠΊΠΈΡΡΠ΅Ρ Π»ΡΠ±ΡΠ΅ Π²ΠΎΠ·ΠΌΠΎΠΆΠ½ΡΠ΅ ΠΏΠ΅ΡΠ΅ΠΌΠ΅ΡΠ΅Π½ΠΈΡ, Π½Π°Ρ ΠΎΠ΄ΡΡΡ Π½Π° ΡΡΠΎΡΠ½ΠΊΠ΅. ΠΠΎΠ»ΡΡΠ° ΠΎΠ±Π΅Π·Π΄Π²ΠΈΠΆΠΈΠ²Π°ΡΡΡΡ, Π° ΠΏΠΎΡΠΎΠΌΡ ΠΈΡΠΊΠ»ΡΡΠ°Π΅ΡΡΡ ΠΏΡΠΎΠΈΠ·Π²ΠΎΠ»ΡΠ½ΠΎΠ΅ Π΄Π²ΠΈΠΆΠ΅Π½ΠΈΠ΅, ΠΊΠΎΡΠΎΡΠΎΠ΅ ΠΌΠΎΠΆΠ΅Ρ Π²ΠΎΠ·Π½ΠΈΠΊΠ½ΡΡΡ ΠΏΡΠΈ Π½Π°Ρ ΠΎΠΆΠ΄Π΅Π½ΠΈΠΈ Π’Π‘ Π½Π° ΠΊΠ°ΠΊΠΎΠΌ-Π½ΠΈΠ±ΡΠ΄Ρ ΡΠΊΠ»ΠΎΠ½Π΅.
Π Π΅Π·Π΅ΡΠ²Π½ΡΠ΅ ΠΈΠ»ΠΈ Π°Π²Π°ΡΠΈΠΉΠ½ΡΠ΅ ΡΠΎΡΠΌΠΎΠ·Π° ΡΠ»ΡΠΆΠ°Ρ Π² ΠΊΠ°ΡΠ΅ΡΡΠ²Π΅ Π²ΡΠΏΠΎΠΌΠΎΠ³Π°ΡΠ΅Π»ΡΠ½ΠΎΠ³ΠΎ ΠΌΠ΅Ρ Π°Π½ΠΈΠ·ΠΌΠ° Π½Π° ΡΠΎΡ ΡΠ»ΡΡΠ°ΠΉ, ΠΊΠΎΠ³Π΄Π° Π»ΠΎΠΌΠ°Π΅ΡΡΡ ΠΎΡΠ½ΠΎΠ²Π½ΠΎΠΉ Π°Π³ΡΠ΅Π³Π°Ρ. Π£ Π±ΠΎΠ»ΡΡΠΈΠ½ΡΡΠ²Π° Π»Π΅Π³ΠΊΠΎΠ²ΡΡ ΠΌΠ°ΡΠΈΠ½ Π·Π°ΠΏΠ°ΡΠ½ΠΎΠΉ Π°Π²Π°ΡΠΈΠΉΠ½ΡΠΉ ΡΠΎΡΠΌΠΎΠ· ΠΏΡΠ΅ΠΈΠΌΡΡΠ΅ΡΡΠ²Π΅Π½Π½ΠΎ ΠΎΡΡΡΡΡΡΠ²ΡΠ΅Ρ, Π° Π²ΠΌΠ΅ΡΡΠΎ Π½Π΅Π³ΠΎ ΡΡΠ° ΡΠΎΠ»Ρ ΠΏΠ΅ΡΠ΅Π΄Π°ΡΡΡΡ ΡΡΠΎΡΠ½ΠΎΡΠ½ΠΎΠΉ ΡΠΈΡΡΠ΅ΠΌΠ΅. ΠΠΎΡΠ½ΡΠ΅ ΡΠΎΡΠΌΠΎΠ·Π° Π°ΠΊΡΡΠ°Π»ΡΠ½ΠΎ ΠΏΡΠΈΠΌΠ΅Π½ΡΡΡ Π² ΠΊΠΎΠ½ΡΡΡΡΠΊΡΠΈΠΈ Π³ΡΡΠ·ΠΎΠ²ΡΡ ΠΌΠ°ΡΠΈΠ½. Π’Π°ΠΊΠ°Ρ ΡΠΈΡΡΠ΅ΠΌΠ° ΠΏΠΎΠ·Π²ΠΎΠ»ΡΠ΅Ρ ΠΏΡΠΈΠ½ΡΠ΄ΠΈΡΠ΅Π»ΡΠ½ΠΎ ΡΠ±ΡΠΎΡΠΈΡΡ ΠΎΠ±ΠΎΡΠΎΡΡ Π΄Π²ΠΈΠ³Π°ΡΠ΅Π»Ρ, ΠΊΠΎΠ³Π΄Π° Π³ΡΡΠ·ΠΎΠ²ΠΎΠΉ ΡΡΠ°Π½ΡΠΏΠΎΡΡ Π΄Π²ΠΈΠΆΠ΅ΡΡΡ Ρ Π³ΠΎΡΡ. Π’Π°ΠΊ Π·Π°ΠΌΠ΅Π΄Π»ΡΠ΅ΡΡΡ Π΄Π²ΠΈΠΆΠ΅Π½ΠΈΠ΅ Π°Π²ΡΠΎ Π±Π΅Π· ΠΏΡΠΈΠΌΠ΅Π½Π΅Π½ΠΈΡ ΠΎΡΠ½ΠΎΠ²Π½ΠΎΠ³ΠΎ ΡΠ°Π±ΠΎΡΠ΅Π³ΠΎ ΡΠΎΡΠΌΠΎΠ·Π°. ΠΡΠΎ ΠΏΠΎΠ»Π΅Π·Π½ΠΎΠ΅ ΡΠ΅ΡΠ΅Π½ΠΈΠ΅, ΠΏΠΎΡΠΊΠΎΠ»ΡΠΊΡ ΠΈΡΠΊΠ»ΡΡΠ°Π΅ΡΡΡ ΠΏΠ΅ΡΠ΅Π³ΡΠ΅Π² ΠΈ ΠΏΡΠ΅Π΄ΠΎΡΠ²ΡΠ°ΡΠ°Π΅ΡΡΡ Π²ΠΎΠ·ΠΌΠΎΠΆΠ½ΡΠΉ ΠΎΡΠΊΠ°Π· Π³Π»Π°Π²Π½ΠΎΠΉ ΡΠΈΡΡΠ΅ΠΌΡ.
ΠΡΠΈΠ²ΠΎΠ΄
Π’Π°ΠΊΠΆΠ΅ ΡΠΎΡΠΌΠΎΠ·Π½ΡΠ΅ ΡΠΈΡΡΠ΅ΠΌΡ ΡΠ°Π·Π»ΠΈΡΠ°ΡΡ Π² Π·Π°Π²ΠΈΡΠΈΠΌΠΎΡΡΠΈ ΠΎΡ ΡΠΎΠ³ΠΎ, ΠΊΠ°ΠΊΠΎΠΉ ΡΠΈΠΏ ΠΏΡΠΈΠ²ΠΎΠ΄Π° Π½Π° ΠΊΠ°ΠΆΠ΄ΠΎΠΉ ΠΈΠ· Π½ΠΈΡ ΠΈΡΠΏΠΎΠ»ΡΠ·ΡΠ΅ΡΡΡ. ΠΠ°Π΄Π°ΡΠ΅ΠΉ ΠΏΡΠΈΠ²ΠΎΠ΄Π° ΡΠ²Π»ΡΠ΅ΡΡΡ ΠΏΠ΅ΡΠ΅Π΄Π°ΡΠ° ΡΡΠΈΠ»ΠΈΡ ΡΠ°Π±ΠΎΡΠΈΡ ΠΌΠ΅Ρ Π°Π½ΠΈΠ·ΠΌΠΎΠ², Π»ΠΈΠ±ΠΎ ΠΆΠ΅ Π²ΡΠΏΠΎΠ»Π½Π΅Π½ΠΈΠ΅ ΡΠ΅Ρ ΠΈΠ»ΠΈ ΠΈΠ½ΡΡ Π΄Π΅ΠΉΡΡΠ²ΠΈΠΉ Ρ ΠΊΠΎΠΌΠΏΠΎΠ½Π΅Π½ΡΠ°ΠΌΠΈ ΡΠΈΡΡΠ΅ΠΌΡ, ΠΎΡΠ²Π΅ΡΠ°ΡΡΠ΅ΠΉ Π·Π° ΡΠΎΡΠΌΠΎΠΆΠ΅Π½ΠΈΠ΅. ΠΡΠΈΠ²ΠΎΠ΄ Π±ΡΠ²Π°Π΅Ρ:
- ΠΌΠ΅Ρ Π°Π½ΠΈΡΠ΅ΡΠΊΠΈΠΌ;
- Π³ΠΈΠ΄ΡΠ°Π²Π»ΠΈΡΠ΅ΡΠΊΠΈΠΌ;
- ΠΏΠ½Π΅Π²ΠΌΠ°ΡΠΈΡΠ΅ΡΠΊΠΈΠΌ;
- ΠΊΠΎΠΌΠ±ΠΈΠ½ΠΈΡΠΎΠ²Π°Π½Π½ΡΠΌ.
Π ΠΌΠ΅Ρ Π°Π½ΠΈΡΠ΅ΡΠΊΠΈΡ ΡΠΈΡΡΠ΅ΠΌΠ°Ρ Π²ΠΎΠ·Π΄Π΅ΠΉΡΡΠ²ΠΈΠ΅ Π½Π° ΡΠ°Π±ΠΎΡΠΈΠ΅ ΡΠ·Π»Ρ ΠΎΡΡΡΠ΅ΡΡΠ²Π»ΡΠ΅ΡΡΡ Ρ ΠΏΠΎΠΌΠΎΡΡΡ ΡΡΠ³, ΡΡΡΠ°Π³ΠΎΠ² ΠΈ ΡΠΏΠ΅ΡΠΈΠ°Π»ΡΠ½ΡΡ ΡΡΠΎΡΠΎΠ². Π ΠΎΠ±ΡΡΠ½ΡΡ ΡΠΎΡΠΌΠΎΠ·Π°Ρ ΡΡΠΎΡ ΠΏΡΠΈΠ²ΠΎΠ΄ ΠΏΡΠ°ΠΊΡΠΈΡΠ΅ΡΠΊΠΈ Π½Π΅ ΠΏΡΠΈΠΌΠ΅Π½ΡΠ΅ΡΡΡ. ΠΠ°ΡΠΎ ΡΠ°ΡΡΠΎ ΠΎΠΊΠ°Π·ΡΠ²Π°Π΅ΡΡΡ Π² ΡΠΎΡΡΠ°Π²Π΅ ΡΡΠΎΡΠ½ΠΎΡΠ½ΠΎΠ³ΠΎ ΡΠΎΡΠΌΠΎΠ·Π°. ΠΠΈΠ΄ΡΠ°Π²Π»ΠΈΡΠ΅ΡΠΊΠΈΠ΅ ΠΏΡΠΈΠ²ΠΎΠ΄Ρ ΡΠ²Π»ΡΡΡΡΡ Π½Π°ΠΈΠ±ΠΎΠ»Π΅Π΅ ΡΠ°ΡΠΏΡΠΎΡΡΡΠ°Π½ΡΠ½Π½ΡΠΌΠΈ ΠΏΡΠΈ ΡΠΎΠ·Π΄Π°Π½ΠΈΠΈ Π»Π΅Π³ΠΊΠΎΠ²ΡΡ ΠΌΠ°ΡΠΈΠ½. ΠΡΠ½ΠΎΠ²ΠΎΠΉ Π΅Π³ΠΎ ΡΠ°Π±ΠΎΡΡ ΡΠ²Π»ΡΠ΅ΡΡΡ ΡΠΈΠ·ΠΈΡΠ΅ΡΠΊΠΎΠ΅ ΡΠ²ΠΎΠΉΡΡΠ²ΠΎ ΠΆΠΈΠ΄ΠΊΠΎΡΡΠΈ, ΠΊΠΎΡΠΎΡΠΎΠ΅ Π·Π°ΠΊΠ»ΡΡΠ°Π΅ΡΡΡ Π² Π΅Ρ Π½Π΅ΡΠΆΠΈΠΌΠ°Π΅ΠΌΠΎΡΡΠΈ. Π‘ Π΅Ρ ΠΏΠΎΠΌΠΎΡΡΡ ΡΡΠΈΠ»ΠΈΠ΅ Π΄ΠΎΠ²ΠΎΠ»ΡΠ½ΠΎ Π»Π΅Π³ΠΊΠΎ ΠΏΠ΅ΡΠ΅Π΄Π°ΡΡΡΡ Π½Π° ΡΠ°Π±ΠΎΡΠΈΠ΅ ΠΌΠ΅Ρ Π°Π½ΠΈΠ·ΠΌΡ, Π° ΠΏΠΎΡΠΎΠΌΡ Π²ΠΎΠ΄ΠΈΡΠ΅Π»Ρ Π½Π΅ ΠΏΡΠΈΡ ΠΎΠ΄ΠΈΡΡΡ ΡΠΈΠ»ΡΠ½ΠΎ Π΄Π°Π²ΠΈΡΡ Π½Π° ΠΏΠ΅Π΄Π°Π»Ρ.
ΠΠ½Π΅Π²ΠΌΠ°ΡΠΈΡΠ΅ΡΠΊΠΈΠΉ ΠΏΡΠΈΠ²ΠΎΠ΄ ΠΏΠΎΠ»ΡΡΠΈΠ» ΡΠΈΡΠΎΠΊΠΎΠ΅ ΡΠ°ΡΠΏΡΠΎΡΡΡΠ°Π½Π΅Π½ΠΈΠ΅ Π² ΠΊΠΎΠ½ΡΡΡΡΠΊΡΠΈΠΈ Π³ΡΡΠ·ΠΎΠ²ΡΡ ΠΌΠ°ΡΠΈΠ½. Π Π°Π±ΠΎΡΠΈΠΌ ΡΠ΅Π»ΠΎΠΌ ΡΡΡ ΡΠ²Π»ΡΠ΅ΡΡΡ ΡΠΆΠ°ΡΡΠΉ Π²ΠΎΠ·Π΄ΡΡ , Π½Π°Π³Π½Π΅ΡΠ°Π½ΠΈΠ΅ ΠΊΠΎΡΠΎΡΠΎΠ³ΠΎ ΠΎΡΡΡΠ΅ΡΡΠ²Π»ΡΠ΅ΡΡΡ Π·Π° ΡΡΡΡ ΠΈΡΠΏΠΎΠ»ΡΠ·ΠΎΠ²Π°Π½ΠΈΡ ΠΊΠΎΠΌΠΏΡΠ΅ΡΡΠΎΡΠ°. ΠΠΎΠ³Π΄Π° Π²ΠΎΠ΄ΠΈΡΠ΅Π»Ρ Π΄Π°Π²ΠΈΡ Π½Π° ΠΏΠ΅Π΄Π°Π»Ρ, ΠΎΡΠΊΡΡΠ²Π°ΡΡΡΡ ΡΠΏΠ΅ΡΠΈΠ°Π»ΡΠ½ΡΠ΅ ΠΊΠ°Π½Π°Π»Ρ. ΠΠΎ Π½ΠΈΠΌ Π²ΠΎΠ·Π΄ΡΡ ΠΈΠ΄ΡΡ Π² ΠΊΠ°ΠΌΠ΅ΡΡ, Π½Π΅ΠΏΠΎΡΡΠ΅Π΄ΡΡΠ²Π΅Π½Π½ΠΎ ΡΠ²ΡΠ·Π°Π½Π½ΡΠΌΠΈ Ρ ΡΠ°Π±ΠΎΡΠΈΠΌΠΈ ΡΠΎΡΠΌΠΎΠ·Π½ΡΠΌΠΈ ΠΌΠ΅Ρ Π°Π½ΠΈΠ·ΠΌΠ°ΠΌΠΈ. ΠΠΎΠΌΠ±ΠΈΠ½ΠΈΡΠΎΠ²Π°Π½Π½ΡΠΉ ΠΏΡΠΈΠ²ΠΎΠ΄ Π°ΠΊΡΡΠ°Π»Π΅Π½ Π΄Π»Ρ ΡΠΏΠ΅ΡΡΠ΅Ρ Π½ΠΈΠΊΠΈ. ΠΡΠΎΠ±Π΅Π½Π½ΠΎΡΡΡΡ ΡΠΈΡΡΠ΅ΠΌΡ ΡΠ²Π»ΡΠ΅ΡΡΡ ΠΎΠ΄Π½ΠΎΠ²ΡΠ΅ΠΌΠ΅Π½Π½ΠΎΠ΅ ΠΈΡΠΏΠΎΠ»ΡΠ·ΠΎΠ²Π°Π½ΠΈΠ΅ ΡΠ°Π·Π½ΡΡ ΠΏΡΠΈΠ²ΠΎΠ΄ΠΎΠ². ΠΠ° Π»Π΅Π³ΠΊΠΎΠ²ΡΡ ΠΌΠ°ΡΠΈΠ½Π°Ρ Π½Π΅ ΡΡΡΠ°Π½Π°Π²Π»ΠΈΠ²Π°Π΅ΡΡΡ.
Π Π°Π±ΠΎΡΠΈΠ΅ ΠΌΠ΅Ρ Π°Π½ΠΈΠ·ΠΌΡ
Π Π°Π±ΠΎΡΠΈΠΉ ΠΌΠ΅Ρ Π°Π½ΠΈΠ·ΠΌ Π½ΡΠΆΠ΅Π½ Π΄Π»Ρ ΡΠΎΠ³ΠΎ, ΡΡΠΎΠ±Ρ ΠΎΠΊΠ°Π·ΡΠ²Π°ΡΡ Π²ΠΎΠ·Π΄Π΅ΠΉΡΡΠ²ΠΈΠ΅ Π½Π° Π°Π²ΡΠΎΠΌΠΎΠ±ΠΈΠ»ΡΠ½ΡΠ΅ ΠΊΠΎΠ»ΡΡΠ°, Π·Π°ΠΌΠ΅Π΄Π»ΡΡ ΡΠΊΠΎΡΠΎΡΡΡ ΠΈΡ Π²ΡΠ°ΡΠ΅Π½ΠΈΡ. ΠΠΎΡΠΎΠΌΡ ΡΡΠΎ Π³Π»Π°Π²Π½ΡΠ΅ ΠΊΠΎΠΌΠΏΠΎΠ½Π΅Π½ΡΡ Π²ΡΠ΅ΠΉ ΡΠΈΡΡΠ΅ΠΌΡ. ΠΡ Π΄Π΅Π»ΡΡ Π½Π° Π»Π΅Π½ΡΠΎΡΠ½ΡΠ΅, Π΄ΠΈΡΠΊΠΎΠ²ΡΠ΅ ΠΈ Π±Π°ΡΠ°Π±Π°Π½Π½ΡΠ΅. ΠΠ΅Π½ΡΠΎΡΠ½ΡΠ΅ ΠΌΠ΅Ρ Π°Π½ΠΈΠ·ΠΌΡ ΠΏΡΠ°ΠΊΡΠΈΡΠ΅ΡΠΊΠΈ Π½Π΅ ΠΏΡΠΈΠΌΠ΅Π½ΡΡΡΡΡ. ΠΠ΄ΠΈΠ½ΡΡΠ²Π΅Π½Π½ΡΠΌ ΠΈΡΠΊΠ»ΡΡΠ΅Π½ΠΈΠ΅ΠΌ ΡΠ²Π»ΡΠ΅ΡΡΡ ΡΠΏΠ΅ΡΡΠ΅Ρ Π½ΠΈΠΊΠ°. Π‘ΡΡΡ Π·Π°ΠΊΠ»ΡΡΠ°Π΅ΡΡΡ Π² ΡΠΎΠΌ, ΡΡΠΎ Π½Π° ΠΎΡΡ, ΠΏΡΠ΅Π΄Π½Π°Π·Π½Π°ΡΠ΅Π½Π½ΡΡ Π΄Π»Ρ ΠΏΠ΅ΡΠ΅Π΄Π°ΡΠΈ Π²ΡΠ°ΡΠ΅Π½ΠΈΠΉ Π½Π° ΠΊΠΎΠ»ΡΡΠ°, ΡΡΡΠ°Π½Π°Π²Π»ΠΈΠ²Π°Π΅ΡΡΡ Π±Π°ΡΠ°Π±Π°Π½ Ρ Π»Π΅Π½ΡΠΎΠΉ. ΠΠΎΠ³Π΄Π° Π²ΠΎΠ΄ΠΈΡΠ΅Π»Ρ ΡΠΎΡΠΌΠΎΠ·ΠΈΡ, Π»Π΅Π½ΡΠ° Π½Π°ΡΡΠ³ΠΈΠ²Π°Π΅ΡΡΡ, ΠΈ Π·Π° ΡΡΡΡ ΡΠΈΠ»Ρ ΡΡΠ΅Π½ΠΈΡ ΡΠΊΠΎΡΠΎΡΡΡ Π²ΡΠ°ΡΠ΅Π½ΠΈΡ Π±Π°ΡΠ°Π±Π°Π½Π° ΠΏΠ°Π΄Π°Π΅Ρ. ΠΠΈΡΠΊΠΎΠ²ΡΠ΅ ΠΌΠ΅Ρ Π°Π½ΠΈΠ·ΠΌΡ ΠΎΠΊΠ°Π·Π°Π»ΠΈΡΡ ΡΠ°ΠΌΡΠΌΠΈ ΡΠ°ΡΠΏΡΠΎΡΡΡΠ°Π½ΡΠ½Π½ΡΠΌΠΈ ΡΡΠ΅Π΄ΠΈ Π»Π΅Π³ΠΊΠΎΠ²ΡΡ ΡΡΠ°Π½ΡΠΏΠΎΡΡΠ½ΡΡ ΡΡΠ΅Π΄ΡΡΠ². ΠΡΠ½ΠΎΠ²Π½ΡΠΌ ΡΠ»Π΅ΠΌΠ΅Π½ΡΠΎΠΌ ΡΠ²Π»ΡΠ΅ΡΡΡ Π΄ΠΈΡΠΊ, ΠΊΠΎΡΠΎΡΡΠΉ ΠΆΡΡΡΠΊΠΎ ΡΠΈΠΊΡΠΈΡΡΡΡ Π½Π° ΡΡΡΠΏΠΈΡΠ΅ ΠΊΠΎΠ»Π΅ΡΠ°.
ΠΡΠΈΠ²ΠΎΠ΄ ΠΈΠΌΠ΅Π΅Ρ Π½Π΅ΠΏΠΎΡΡΠ΅Π΄ΡΡΠ²Π΅Π½Π½ΡΡ ΡΠ²ΡΠ·Ρ Ρ ΡΡΠΏΠΏΠΎΡΡΠΎΠΌ, ΡΡΠΎΡΡΠ΅ΠΌ Π½Π° Π΄ΠΈΡΠΊΠ΅ ΡΠΎΡΠΌΠΎΠΆΠ΅Π½ΠΈΡ. ΠΠ΄Π΅ΡΡ ΠΈΠΌΠ΅ΡΡΡΡ ΠΊΠΎΠ»ΠΎΠ΄ΠΊΠΈ ΡΡΠΈΠΊΡΠΈΠΎΠ½Π½ΠΎΠ³ΠΎ ΡΠΈΠΏΠ°. ΠΠΎΠ³Π΄Π° Π½Π°ΠΆΠΈΠΌΠ°Π΅ΡΡΡ ΠΏΠ΅Π΄Π°Π»Ρ, ΠΊΠΎΠ»ΠΎΠ΄ΠΊΠ° ΠΏΡΠΈΠΆΠΈΠΌΠ°Π΅ΡΡΡ ΠΊ Π΄ΠΈΡΠΊΡ, ΠΈ ΡΠΈΠ»Π° ΡΡΠ΅Π½ΠΈΡ ΡΠΏΠΎΡΠΎΠ±ΡΡΠ²ΡΠ΅Ρ Π·Π°ΠΌΠ΅Π΄Π»Π΅Π½ΠΈΡ. ΠΡΠ»ΠΈ ΡΠΈΡΡΠ΅ΠΌΠ° Π±Π°ΡΠ°Π±Π°Π½Π½Π°Ρ, ΡΠΎΠ³Π΄Π° ΠΌΠ΅ΡΡΠΎ Π΄ΠΈΡΠΊΠ° Π·Π°Π½ΠΈΠΌΠ°Π΅Ρ Π±Π°ΡΠ°Π±Π°Π½, ΡΡΡΠ°Π½ΠΎΠ²Π»Π΅Π½Π½ΡΠΉ Π½Π° ΡΡΡΠΏΠΈΡΡ. ΠΠ½ΡΡΡΠΈ Π±Π°ΡΠ°Π±Π°Π½Π° Π΅ΡΡΡ ΠΏΠ°ΡΠ° ΠΊΠΎΠ»ΠΎΠ΄ΠΎΠΊ, ΠΊΠΎΡΠΎΡΡΠ΅ ΠΈΠΌΠ΅ΡΡ ΡΠΎΡΠΌΡ ΠΏΠΎΠ»ΡΠΌΠ΅ΡΡΡΠ°. ΠΡ ΠΌΠΎΠ½ΡΠΈΡΡΡΡ Π½Π° Π½Π΅ΠΏΠΎΠ΄Π²ΠΈΠΆΠ½ΡΡ ΡΠ°ΡΡΡ ΡΡΡΠΏΠΈΡΡ. ΠΠΎΠ³Π΄Π° ΠΏΡΠΎΠΈΡΡ ΠΎΠ΄ΠΈΡ ΡΠΎΡΠΌΠΎΠΆΠ΅Π½ΠΈΠ΅, ΡΡΠΎΡ ΠΏΡΠΎΠ²ΠΎΠ΄ ΡΠ°Π·ΠΆΠΈΠΌΠ°Π΅Ρ ΠΊΠΎΠ»ΠΎΠ΄ΠΊΠΈ, ΠΏΠΎΡΠ»Π΅ ΡΠ΅Π³ΠΎ ΠΎΠ½ΠΈ Π½Π°ΡΠΈΠ½Π°ΡΡ ΠΏΡΠΈΠΆΠΈΠΌΠ°ΡΡΡΡ ΠΊ Π±Π°ΡΠ°Π±Π°Π½Ρ, ΡΠ΅ΠΌ ΡΠ°ΠΌΡΠΌ Π·Π°ΠΌΠ΅Π΄Π»ΡΡ ΡΠΊΠΎΡΠΎΡΡΡ Π΅Π³ΠΎ Π²ΡΠ°ΡΠ΅Π½ΠΈΡ.
ΠΡΠ΅ΠΈΠΌΡΡΠ΅ΡΡΠ²Π° ΠΈ Π½Π΅Π΄ΠΎΡΡΠ°ΡΠΊΠΈ
ΠΠΎΡΠΊΠΎΠ»ΡΠΊΡ ΠΎ Π»Π΅Π½ΡΠΎΡΠ½ΡΡ ΠΏΡΠΈΠ²ΠΎΠ΄Π°Ρ Π³ΠΎΠ²ΠΎΡΠΈΡΡ Π½Π΅ ΠΈΠΌΠ΅Π΅Ρ ΡΠΌΡΡΠ»Π°, ΡΡΠΎΠΈΡ ΠΎΠ±ΡΡΠ΄ΠΈΡΡ ΡΠΈΠ»ΡΠ½ΡΠ΅ ΠΈ ΡΠ»Π°Π±ΡΠ΅ ΡΡΠΎΡΠΎΠ½Ρ Π΄ΠΈΡΠΊΠΎΠ²ΡΡ ΠΈ Π±Π°ΡΠ°Π±Π°Π½Π½ΡΡ ΡΠΎΡΠΌΠΎΠ·Π½ΡΡ ΡΠΈΡΡΠ΅ΠΌ. Π Π΄ΠΎΡΡΠΎΠΈΠ½ΡΡΠ²Π°ΠΌ Π΄ΠΈΡΠΊΠΎΠ²ΡΡ ΡΠ΅ΡΠ΅Π½ΠΈΠΉ ΠΎΡΠ½ΠΎΡΡΡ ΡΠ»Π΅Π΄ΡΡΡΠΈΠ΅ ΠΌΠΎΠΌΠ΅Π½ΡΡ:
- Π²ΡΡΠΎΠΊΠΈΠΉ ΡΡΠΎΠ²Π΅Π½Ρ ΡΡΡΠ΅ΠΊΡΠΈΠ²Π½ΠΎΡΡΠΈ;
- Π½Π΅Π±ΠΎΠ»ΡΡΠΎΠΉ Π²Π΅Ρ;
- ΠΊΠΎΠΌΠΏΠ°ΠΊΡΠ½ΡΠ΅ ΡΠ°Π·ΠΌΠ΅ΡΡ;
- Π½ΠΈΠ·ΠΊΠ°Ρ ΡΠ΅ΠΌΠΏΠ΅ΡΠ°ΡΡΡΠ° Π³ΠΈΠ΄ΡΠ°Π²Π»ΠΈΡΠ΅ΡΠΊΠΎΠΉ ΠΆΠΈΠ΄ΠΊΠΎΡΡΠΈ ΠΏΡΠΈ ΡΠ°Π±ΠΎΡΠ΅;
- Π²ΡΡΠΎΠΊΠΈΠ΅ ΠΏΠΎΠΊΠ°Π·Π°ΡΠ΅Π»ΠΈ Π½Π°Π΄ΡΠΆΠ½ΠΎΡΡΠΈ;
- ΡΡΠ°Π±ΠΈΠ»ΡΠ½ΠΎΡΡΡ.
ΠΡΠΈ ΡΡΠΎΠΌ Π΄ΠΈΡΠΊΠΎΠ²ΡΠ΅ ΡΠΎΡΠΌΠΎΠ·Π° Π½Π΅Π΄ΠΎΡΡΠ°ΡΠΎΡΠ½ΠΎ Ρ ΠΎΡΠΎΡΠΎ Π·Π°ΡΠΈΡΠ΅Π½Ρ ΠΎΡ Π³ΡΡΠ·ΠΈ, ΠΊΠΎΡΠΎΡΠ°Ρ ΡΠΏΠΎΡΠΎΠ±Π½Π° Π½Π΅Π³Π°ΡΠΈΠ²Π½ΠΎ ΠΏΠΎΠ²Π»ΠΈΡΡΡ Π½Π° ΡΠ°Π±ΠΎΡΠΎΡΠΏΠΎΡΠΎΠ±Π½ΠΎΡΡΡ Π²ΡΠ΅ΠΉ ΡΠΈΡΡΠ΅ΠΌΡ. Π§ΡΠΎ ΠΆΠ΅ ΠΊΠ°ΡΠ°Π΅ΡΡΡ Π±Π°ΡΠ°Π±Π°Π½Π½ΡΡ Π°Π½Π°Π»ΠΎΠ³ΠΎΠ², ΡΠΎ ΠΈΡ ΠΏΡΠ΅ΠΈΠΌΡΡΠ΅ΡΡΠ²Π°ΠΌΠΈ ΡΠ²Π»ΡΡΡΡΡ:
- ΠΠΎΠ»ΡΡΠΈΠ΅ ΠΏΠΎΠΊΠ°Π·Π°ΡΠ΅Π»ΠΈ ΡΡΠΈΠ»ΠΈΡ. ΠΡΠΎ ΠΏΠΎΠ·Π²ΠΎΠ»ΡΠ΅Ρ ΡΡΡΠ΅ΠΊΡΠΈΠ²Π½ΠΎ ΠΈΡΠΏΠΎΠ»ΡΠ·ΠΎΠ²Π°ΡΡ Π±Π°ΡΠ°Π±Π°Π½Ρ Π½Π° Π±ΠΎΠ»ΡΡΠΈΡ ΠΌΠ°ΡΠΈΠ½Π°Ρ ΠΈ Π³ΡΡΠ·ΠΎΠ²ΠΈΠΊΠ°Ρ , ΠΏΠΎΡΠΊΠΎΠ»ΡΠΊΡ ΠΈΡ ΠΌΠ°ΡΡΠ° Π²Π½ΡΡΠΈΡΠ΅Π»ΡΠ½Π°Ρ, Π° ΠΏΠΎΡΠΎΠΌΡ Π΄ΠΈΡΠΊΠΎΠ²ΡΠΌΠΈ ΡΠΎΡΠΌΠΎΠ·Π°ΠΌΠΈ ΠΎΡΡΠ°Π½Π°Π²Π»ΠΈΠ²Π°ΡΡ ΠΏΠΎΠ΄ΠΎΠ±Π½ΡΠ΅ ΡΡΠ°Π½ΡΠΏΠΎΡΡΠ½ΡΠ΅ ΡΡΠ΅Π΄ΡΡΠ²Π° ΡΠ»ΠΎΠΆΠ½Π΅Π΅.
- ΠΠ»ΠΈΡΠ΅Π»ΡΠ½ΡΠΉ ΡΡΠΎΠΊ ΡΠ»ΡΠΆΠ±Ρ. ΠΠ½ΡΡΡΡ ΠΏΡΠΈΠ²ΠΎΠ΄Π° Π½Π΅ ΠΏΡΠΎΠ½ΠΈΠΊΠ°Π΅Ρ Π³ΡΡΠ·Ρ, Π° ΠΏΠΎΡΠΎΠΌΡ Π½Π°ΠΊΠ»Π°Π΄ΠΊΠΈ ΠΈΠ·Π½Π°ΡΠΈΠ²Π°ΡΡΡΡ Ρ ΠΌΠ΅Π½ΡΡΠ΅ΠΉ ΠΈΠ½ΡΠ΅Π½ΡΠΈΠ²Π½ΠΎΡΡΡΡ.
- ΠΠΎΡΡΡΠΏΠ½Π°Ρ ΡΠ΅Π½Π°. ΠΡΠΎ ΠΊΠ°ΡΠ°Π΅ΡΡΡ ΠΏΠΎΠΊΡΠΏΠΊΠΈ ΠΈ ΠΎΠ±ΡΠ»ΡΠΆΠΈΠ²Π°Π½ΠΈΡ.
ΠΠΎ Π½Π΅ Π²ΡΡ ΡΠ°ΠΊ ΠΈΠ΄Π΅Π°Π»ΡΠ½ΠΎ Ρ Π±Π°ΡΠ°Π±Π°Π½Π½ΡΠΌΠΈ ΡΠΎΡΠΌΠΎΠ·Π°ΠΌΠΈ. ΠΠ΅Π»ΡΠ·Ρ Π·Π°Π±ΡΠ²Π°ΡΡ ΠΏΡΠΎ ΠΌΠ΅Π΄Π»Π΅Π½Π½ΡΡ ΡΠΊΠΎΡΠΎΡΡΡ ΠΈΠ· ΡΠ΅Π°ΠΊΡΠΈΠΈ Π½Π° Π½Π°ΠΆΠ°ΡΠΈΠ΅ ΠΏΠ΅Π΄Π°Π»ΠΈ, Π° ΡΠ°ΠΊΠΆΠ΅ Π²Π΅ΡΠΎΡΡΠ½ΠΎΡΡΡ Π·Π°Π»ΠΈΠΏΠ°Π½ΠΈΡ ΡΠΎΡΠΌΠΎΠ·Π½ΡΡ ΠΊΠΎΠ»ΠΎΠ΄ΠΎΠΊ. Π’Π°ΠΊΠΎΠ΅ ΠΏΡΠΎΠΈΡΡ ΠΎΠ΄ΠΈΡ, Π΅ΡΠ»ΠΈ ΠΌΠ°ΡΠΈΠ½Ρ Π² ΡΡΠ»ΠΎΠ²ΠΈΡΡ ΡΠΈΠ»ΡΠ½ΠΎΠΉ ΠΆΠ°ΡΡ ΠΈΠ»ΠΈ ΡΡΠ΅Π·ΠΌΠ΅ΡΠ½ΠΎΠ³ΠΎ Ρ ΠΎΠ»ΠΎΠ΄Π° ΠΎΡΡΠ°Π²Π»ΡΡΡ Π½Π° ΡΠ»ΠΈΡΠ΅ Ρ Π²ΠΊΠ»ΡΡΡΠ½Π½ΡΠΌ ΡΡΡΠ½ΡΠΌ ΡΠΎΡΠΌΠΎΠ·ΠΎΠΌ.
Π‘ΠΈΡΡΠ΅ΠΌΡ Π±Π΅Π·ΠΎΠΏΠ°ΡΠ½ΠΎΡΡΠΈ
Π‘ΠΎΠ²ΡΠ΅ΠΌΠ΅Π½Π½ΡΠ΅ Π°Π²ΡΠΎΠΌΠΎΠ±ΠΈΠ»ΠΈ ΠΎΡΠ½Π°ΡΠ°ΡΡΡΡ Π΄ΠΎΠΏΠΎΠ»Π½ΠΈΡΠ΅Π»ΡΠ½ΡΠΌ ΠΎΠ±ΠΎΡΡΠ΄ΠΎΠ²Π°Π½ΠΈΠ΅ΠΌ, ΠΊΠΎΡΠΎΡΠΎΠ΅ ΠΏΡΠΈΠ·Π²Π°Π½ΠΎ ΠΏΠΎΠ²ΡΡΠΈΡΡ Π±Π΅Π·ΠΎΠΏΠ°ΡΠ½ΠΎΡΡΡ ΠΈ ΠΏΠΎΠ΄Π½ΡΡΡ ΡΡΡΠ΅ΠΊΡΠΈΠ²Π½ΠΎΡΡΡ ΠΎΡΠ½ΠΎΠ²Π½ΡΡ ΡΠΎΡΠΌΠΎΠ·Π½ΡΡ ΠΌΠ΅Ρ Π°Π½ΠΈΠ·ΠΌΠΎΠ². ΠΠ½ΠΎΠ³ΠΈΠ΅ Π·Π½Π°ΡΡ ΠΎ ΡΠΎΠΌ, ΡΡΠΎ ΡΠ°ΠΊΠΎΠ΅ Π°Π½ΡΠΈΠ±Π»ΠΎΠΊΠΈΡΠΎΠ²ΠΎΡΠ½Π°Ρ ΡΠΎΡΠΌΠΎΠ·Π½Π°Ρ ΡΠΈΡΡΠ΅ΠΌΠ° ΠΈ Π·Π°ΡΠ΅ΠΌ ΠΎΠ½Π° Π½ΡΠΆΠ½Π°. ΠΠΏΠ΅ΡΠ²ΡΠ΅ ΠΎ Π½Π΅ΠΉ Π½Π° ΠΏΡΠ°ΠΊΡΠΈΠΊΠ΅ ΡΠ·Π½Π°Π»ΠΈ Π² 1978 Π³ΠΎΠ΄Ρ, ΠΊΠΎΠ³Π΄Π° ΠΊΠΎΠΌΠΏΠ°Π½ΠΈΡ Bosch ΡΠ°Π·ΡΠ°Π±ΠΎΡΠ°Π»Π° Π½ΠΎΠ²ΠΈΠ½ΠΊΡ ΠΈ Π·Π°ΠΏΡΡΡΠΈΠ»Π° Π΅Ρ Π² ΠΏΡΠΎΠΈΠ·Π²ΠΎΠ΄ΡΡΠ²ΠΎ. Π’ΠΎΡΠΌΠΎΠ·Π½Π°Ρ ΡΠΈΡΡΠ΅ΠΌΠ° ΠΠΠ‘ ΠΏΡΠ΅Π΄Π½Π°Π·Π½Π°ΡΠ΅Π½Π° Π΄Π»Ρ ΠΏΡΠ΅Π΄ΠΎΡΠ²ΡΠ°ΡΠ΅Π½ΠΈΡ Π±Π»ΠΎΠΊΠΈΡΠΎΠ²ΠΊΠΈ Π°Π²ΡΠΎΠΌΠΎΠ±ΠΈΠ»ΡΠ½ΡΡ ΠΊΠΎΠ»ΡΡ, ΠΊΠΎΠ³Π΄Π° Π²ΠΎΠ΄ΠΈΡΠ΅Π»Ρ ΡΠ΅Π·ΠΊΠΎ Π½Π°ΠΆΠΈΠΌΠ°Π΅Ρ Π½Π° ΠΏΠ΅Π΄Π°Π»Ρ ΠΈ ΡΠΎΡΠΌΠΎΠ·ΠΈΡ. ΠΡΠΎ ΠΏΠΎΠ·Π²ΠΎΠ»ΡΠ΅Ρ ΠΌΠ°ΡΠΈΠ½Π΅ ΡΠΎΡ ΡΠ°Π½ΡΡΡ ΡΡΡΠΎΠΉΡΠΈΠ²ΠΎΡΡΡ Π΄Π°ΠΆΠ΅ ΠΏΡΠΈ ΡΡΠ»ΠΎΠ²ΠΈΠΈ ΡΠΊΡΡΡΠ΅Π½Π½ΠΎΠΉ ΠΎΡΡΠ°Π½ΠΎΠ²ΠΊΠΈ. ΠΠ»ΡΡ ΠΠΠ‘ ΡΠΏΠΎΡΠΎΠ±ΡΡΠ²ΡΠ΅Ρ ΡΠΎΡ ΡΠ°Π½Π΅Π½ΠΈΡ ΡΠΏΡΠ°Π²Π»ΡΠ΅ΠΌΠΎΡΡΠΈ ΡΡΠ°Π½ΡΠΏΠΎΡΡΠ½ΡΠΌ ΡΡΠ΅Π΄ΡΡΠ²ΠΎΠΌ. ΠΠΎ ΡΠΎΠ²ΡΠ΅ΠΌΠ΅Π½Π½ΡΠ΅ ΡΠ΅Π½Π΄Π΅Π½ΡΠΈΠΈ ΠΈ ΡΠ²Π΅Π»ΠΈΡΠ΅Π½ΠΈΠ΅ ΡΠΊΠΎΡΠΎΡΡΠ΅ΠΉ Π·Π°ΡΡΠ°Π²ΠΈΠ»ΠΈ ΠΏΡΠΎΠΈΠ·Π²ΠΎΠ΄ΠΈΡΠ΅Π»Π΅ΠΉ ΠΏΡΠΈΠ΄ΡΠΌΡΠ²Π°ΡΡ Π½ΠΎΠ²ΡΠ΅ ΡΠ΅ΡΠ΅Π½ΠΈΡ Π΄Π»Ρ ΠΎΠ±Π΅ΡΠΏΠ΅ΡΠ΅Π½ΠΈΡ Π½Π°Π΄Π»Π΅ΠΆΠ°ΡΠ΅ΠΉ Π±Π΅Π·ΠΎΠΏΠ°ΡΠ½ΠΎΡΡΠΈ. ΠΠΎΠΌΠΈΠΌΠΎ ΠΠΠ‘, ΠΊΠΎΡΠΎΡΠ°Ρ ΡΡΠ°Π»Π° ΡΠΆΠ΅ ΡΡΠ°Π½Π΄Π°ΡΡΠ½ΡΠΌ ΡΠ΅ΡΠ΅Π½ΠΈΠ΅ΠΌ Π½Π° Π²ΡΠ΅Ρ ΠΌΠ°ΡΠΈΠ½Π°Ρ , Π΄ΠΎΠ±Π°Π²ΠΈΠ»ΠΈ Π΅ΡΡ Π½Π΅ΡΠΊΠΎΠ»ΡΠΊΠΎ Π½ΠΎΠ²ΡΡ ΡΠΈΡΡΠ΅ΠΌ. Π ΠΈΠΌΠ΅Π½Π½ΠΎ:
- Brake Assist;
- Dynamic Brake Control;
- Cornering Brake Control;
- Electronic Brake Force Distribution.
ΠΡΠ΅ ΡΡΠΈ Π²ΡΠΏΠΎΠΌΠΎΠ³Π°ΡΠ΅Π»ΡΠ½ΡΠ΅, Π½ΠΎ ΠΎΡΠ΅Π½Ρ ΠΏΠΎΠ»Π΅Π·Π½ΡΠ΅ Π΄ΠΎΠΏΠΎΠ»Π½ΠΈΡΠ΅Π»ΡΠ½ΡΠ΅ ΡΠΈΡΡΠ΅ΠΌΡ ΡΠΎΡΠΌΠΎΠΆΠ΅Π½ΠΈΡ Π½Π°Π·ΡΠ²Π°ΡΡ ΡΠΎΠΊΡΠ°ΡΡΠ½Π½ΠΎ BA (BAS ΠΈΠ»ΠΈ EBS), DBC, CBC ΠΈ EBD.
BA
Π§ΡΠΎΠ±Ρ ΠΏΠΎΠ²ΡΡΠΈΡΡ ΡΡΡΠ΅ΠΊΡΠΈΠ²Π½ΠΎΡΡΡ, ΠΏΠΎΡΠ»Π΅ Π²Π½Π΅Π΄ΡΠ΅Π½ΠΈΡ ΠΠΠ‘ Π½Π°ΡΠ°Π»ΠΈ ΠΈΡΠΏΠΎΠ»ΡΠ·ΠΎΠ²Π°ΡΡ Π΄ΠΎΠΏΠΎΠ»Π½ΠΈΡΠ΅Π»ΡΠ½ΠΎ ΡΠΎΡΠΌΠΎΠ·Π½ΡΠ΅ ΡΠΈΡΡΠ΅ΠΌΡ EBS. ΠΠ° Π½Π΅ΠΊΠΎΡΠΎΡΡΡ Π°Π²ΡΠΎΠΌΠΎΠ±ΠΈΠ»ΡΡ Π΅Ρ Π½Π°Π·ΡΠ²Π°ΡΡ ΠΏΡΠΎΡΡΠΎ BA ΠΈΠ»ΠΈ BAS. ΠΡ Π½Π°Π·Π²Π°Π½ΠΈΡ ΡΡΡΡ Π½Π΅ ΠΌΠ΅Π½ΡΠ΅ΡΡΡ. Π‘ΠΈΡΡΠ΅ΠΌΠ° Π½Π°ΠΏΡΠ°Π²Π»Π΅Π½Π° Π½Π° ΡΠ½ΠΈΠΆΠ΅Π½ΠΈΠ΅ Π²ΡΠ΅ΠΌΠ΅Π½ΠΈ, Π½Π΅ΠΎΠ±Ρ ΠΎΠ΄ΠΈΠΌΠΎΠ³ΠΎ Π΄Π»Ρ ΡΡΠ°Π±Π°ΡΡΠ²Π°Π½ΠΈΡ ΡΠΎΡΠΌΠΎΠ·Π½ΠΎΠΉ ΡΠΈΡΡΠ΅ΠΌΡ. ΠΠΠ‘ ΠΏΠΎΠ·Π²ΠΎΠ»ΡΠ΅Ρ ΠΌΠ°ΠΊΡΠΈΠΌΠ°Π»ΡΠ½ΠΎ ΠΏΠΎΠ²ΡΡΠΈΡΡ ΡΡΡΠ΅ΠΊΡΠΈΠ²Π½ΠΎΡΡΡ ΡΠΎΡΠΌΠΎΠΆΠ΅Π½ΠΈΡ, Π΅ΡΠ»ΠΈ ΠΏΠ΅Π΄Π°Π»Ρ ΡΠΎΡΠΌΠΎΠ·Π° Π²ΡΠΆΠ°ΡΠ° ΠΏΠΎΠ»Π½ΠΎΡΡΡΡ. ΠΠΎ ΠΎΠ½Π° Π½Π΅ Π°ΠΊΡΠΈΠ²ΠΈΡΡΠ΅ΡΡΡ, ΠΊΠΎΠ³Π΄Π° ΠΏΠ΅Π΄Π°Π»Ρ Π½Π°ΠΆΠΈΠΌΠ°ΡΡ ΡΠ»Π°Π±ΠΎ. Π£ΡΠΈΠ»ΠΈΡΠ΅Π»Ρ ΡΡΠ°Π±Π°ΡΡΠ²Π°Π΅Ρ Π² ΠΎΠΏΡΠ΅Π΄Π΅Π»ΡΠ½Π½ΡΡ ΡΠΈΡΡΠ°ΡΠΈΡΡ ΠΈ ΠΎΠ±Π΅ΡΠΏΠ΅ΡΠΈΠ²Π°Π΅Ρ Π°Π²Π°ΡΠΈΠΉΠ½ΠΎΠ΅ ΡΠΎΡΠΌΠΎΠΆΠ΅Π½ΠΈΠ΅, Π΅ΡΠ»ΠΈ Π²ΠΎΠ΄ΠΈΡΠ΅Π»Ρ ΡΠ΅Π·ΠΊΠΎ ΠΆΠΌΡΡ Π½Π° ΠΏΠ΅Π΄Π°Π»Ρ, Π½ΠΎ Π΅ΠΌΡ Π½Π΅ ΡΠ΄Π°ΡΡΡΡ ΠΏΡΠΈΠ»ΠΎΠΆΠΈΡΡ Π΄ΠΎΡΡΠ°ΡΠΎΡΠ½ΠΎΠ΅ ΡΡΠΈΠ»ΠΈΠ΅. Π‘ΠΈΡΡΠ΅ΠΌΠ° ΠΈΠ·ΠΌΠ΅ΡΡΠ΅Ρ, ΠΊΠ°ΠΊ Π±ΡΡΡΡΠΎ ΠΈ Ρ ΠΊΠ°ΠΊΠΈΠΌ ΠΏΡΠΈΠ»ΠΎΠΆΠ΅Π½Π½ΡΠΌ ΡΡΠΈΠ»ΠΈΠ΅ΠΌ ΠΎΡΡΡΠ΅ΡΡΠ²Π»ΡΠ΅ΡΡΡ Π½Π°ΠΆΠ°ΡΠΈΠ΅. ΠΡΠ»ΠΈ ΡΡΠΎ Π½ΡΠΆΠ½ΠΎ, Π°Π²ΡΠΎΠΌΠ°ΡΠΈΡΠ΅ΡΠΊΠΈ ΠΈ ΠΌΠΎΠΌΠ΅Π½ΡΠ°Π»ΡΠ½ΠΎ ΡΠ²Π΅Π»ΠΈΡΠΈΠ²Π°Π΅ΡΡΡ Π΄Π°Π²Π»Π΅Π½ΠΈΠ΅ Π²Π½ΡΡΡΠΈ ΡΠΈΡΡΠ΅ΠΌΡ ΡΠΎΡΠΌΠΎΠΆΠ΅Π½ΠΈΡ Π΄ΠΎ ΠΌΠ°ΠΊΡΠΈΠΌΠ°Π»ΡΠ½ΡΡ Π·Π½Π°ΡΠ΅Π½ΠΈΠΉ.
Π§ΡΠΎΠ±Ρ ΡΠ΅Π°Π»ΠΈΠ·ΠΎΠ²Π°ΡΡ ΡΠ°ΠΊΡΡ Π·Π°Π΄ΡΠΌΠΊΡ, Π² ΠΏΠ½Π΅Π²ΠΌΠΎΡΡΠΈΠ»ΠΈΡΠ΅Π»ΠΈ Π²ΠΌΠΎΠ½ΡΠΈΡΠΎΠ²Π°Π»ΠΈ Π΄Π°ΡΡΠΈΠΊ ΡΠΊΠΎΡΠΎΡΡΠΈ, ΠΊΠΎΡΠΎΡΡΠΉ ΡΠ»Π΅Π΄ΠΈΡ Π·Π° ΠΏΠ΅ΡΠ΅ΠΌΠ΅ΡΠ΅Π½ΠΈΠ΅ΠΌ ΡΡΠΎΠΊΠ°, ΠΈ ΡΠ»Π΅ΠΊΡΡΠΎΠΌΠ°Π³Π½ΠΈΡΠ½ΡΠΉ ΡΠΈΠΏ ΠΏΡΠΈΠ²ΠΎΠ΄Π°. ΠΠΎΠ³Π΄Π° ΠΎΡ Π΄Π°ΡΡΠΈΠΊΠ° ΠΏΠΎΡΡΡΠΏΠ°Π΅Ρ ΡΠΈΠ³Π½Π°Π» ΠΎΠ± ΠΎΡΠ΅Π½Ρ Π±ΡΡΡΡΠΎΠΌ ΠΏΠ΅ΡΠ΅ΠΌΠ΅ΡΠ΅Π½ΠΈΠΈ ΡΡΠΎΠΊΠ°, ΡΠΎ Π΅ΡΡΡ Π²ΠΎΠ΄ΠΈΡΠ΅Π»Ρ ΡΠ΅Π·ΠΊΠΎ Π½Π°Π΄Π°Π²ΠΈΡΡ Π½Π° ΠΏΠ΅Π΄Π°Π»Ρ, Π²ΠΊΠ»ΡΡΠ°Π΅ΡΡΡ ΡΠ»Π΅ΠΊΡΡΠΎΠΌΠ°Π³Π½ΠΈΡ ΠΈ ΠΏΠΎΠ²ΡΡΠ°Π΅Ρ Π²Π΅Π»ΠΈΡΠΈΠ½Ρ Π²ΠΎΠ·Π΄Π΅ΠΉΡΡΠ²ΡΡΡΠ΅ΠΉ Π½Π° ΡΡΠΎΠΊ ΡΠΈΠ»Ρ. ΠΠΌΠ΅Π½Π½ΠΎ ΡΡΠΎ ΠΏΠΎΠ·Π²ΠΎΠ»ΡΠ΅Ρ ΡΠ½ΠΈΠ·ΠΈΡΡ Π²ΡΠ΅ΠΌΡ ΡΠΎΡΠΌΠΎΠΆΠ΅Π½ΠΈΡ, ΠΏΠΎΡΠΎΠΉ ΡΠΏΠ°ΡΠ°Ρ Π²ΠΎΠ΄ΠΈΡΠ΅Π»Ρ ΠΆΠΈΠ·Π½Ρ. Π‘ΠΎΠ²ΡΠ΅ΠΌΠ΅Π½Π½ΡΠ΅ ΡΠΈΡΡΠ΅ΠΌΡ EBS ΡΠΏΠΎΡΠΎΠ±Π½Ρ Π·Π°ΠΏΠΎΠΌΠΈΠ½Π°ΡΡ ΠΎΡΠΎΠ±Π΅Π½Π½ΠΎΡΡΠΈ ΡΠ°Π±ΠΎΡΡ Ρ ΡΠΎΡΠΌΠΎΠ·Π°ΠΌΠΈ Π²ΠΎΠ΄ΠΈΡΠ΅Π»Ρ Π² ΠΎΠ±ΡΡΠ½ΠΎΠΌ ΡΠ΅ΠΆΠΈΠΌΠ΅, ΡΠ΅ΠΌ ΡΠ°ΠΌΡΠΌ ΡΠ°ΡΠΏΠΎΠ·Π½Π°ΡΡΡΡ ΡΠΊΡΡΡΠ΅Π½Π½ΠΎΠ΅ ΡΠΎΡΠΌΠΎΠΆΠ΅Π½ΠΈΠ΅. ΠΠ°Π»ΠΈΡΠΈΠ΅ EBS Π²ΠΎΠ·ΠΌΠΎΠΆΠ½ΠΎ ΡΠΎΠ»ΡΠΊΠΎ ΠΏΡΠΈ ΡΡΠ»ΠΎΠ²ΠΈΠΈ ΠΏΡΠΈΡΡΡΡΡΠ²ΠΈΡ Π½Π° Π°Π²ΡΠΎΠΌΠΎΠ±ΠΈΠ»Π΅ ABS, ΠΏΠΎΡΠΊΠΎΠ»ΡΠΊΡ ΠΎΠ½ΠΈ ΡΠ΅ΡΠ½ΠΎ Π²Π·Π°ΠΈΠΌΠΎΠ΄Π΅ΠΉΡΡΠ²ΡΡΡ Π΄ΡΡΠ³ Ρ Π΄ΡΡΠ³ΠΎΠΌ.
ΠΡΠ»ΠΈ Π³ΠΎΠ²ΠΎΡΠΈΡΡ ΠΊΠΎΡΠΎΡΠΊΠΎ, ΡΠΎ EBS ΡΠ»ΡΠΆΠΈΡ Π΄Π»Ρ Π΄ΠΎΠ΄Π°Π²Π»ΠΈΠ²Π°Π½ΠΈΡ ΠΏΠ΅Π΄Π°Π»ΠΈ ΡΠΎΡΠΌΠΎΠ·Π°, Π±Π»Π°Π³ΠΎΠ΄Π°ΡΡ ΡΠ΅ΠΌΡ Π°ΠΊΡΠΈΠ²ΠΈΡΡΠ΅ΡΡΡ ΡΠΈΡΡΠ΅ΠΌΠ° ABS. ΠΠΎ ΠΏΡΠΈ ΡΡΠΎΠΌ EBS Π½Π΅ ΡΠΏΠΎΡΠΎΠ±Π½Π° ΡΠ°ΡΠΏΡΠ΅Π΄Π΅Π»ΡΡΡ ΡΡΠΈΠ»ΠΈΡ Π½Π° ΡΠ°Π·Π½ΡΠ΅ ΠΊΠΎΠ»ΡΡΠ°. Π‘Π΅ΠΉΡΠ°Ρ Π²Π΅Π΄ΡΡΡΡ Π°ΠΊΡΠΈΠ²Π½ΡΠ΅ ΡΠ°Π·ΡΠ°Π±ΠΎΡΠΊΠΈ ΡΡΠΎΠ²Π΅ΡΡΠ΅Π½ΡΡΠ²ΠΎΠ²Π°Π½Π½ΠΎΠΉ Π²Π΅ΡΡΠΈΠΈ ΡΡΠΎΠΉ ΡΠΎΡΠΌΠΎΠ·Π½ΠΎΠΉ ΡΠΈΡΡΠ΅ΠΌΡ, ΠΏΠΎΠ·Π²ΠΎΠ»ΡΡΡΠ΅ΠΉ ΡΠΎΠ²ΠΌΠ΅ΡΡΠ½ΠΎ ΡΠ°Π±ΠΎΡΠ°ΡΡ Ρ ΠΊΡΡΠΈΠ·-ΠΊΠΎΠ½ΡΡΠΎΠ»Π΅ΠΌ, ΡΠ°ΡΠΏΠΎΠ·Π½Π°Π²Π°ΡΡ Π°Π²ΡΠΎΠΌΠ°ΡΠΈΡΠ΅ΡΠΊΠΈ ΠΏΡΠ΅ΠΏΡΡΡΡΠ²ΠΈΡ Π²ΠΏΠ΅ΡΠ΅Π΄ΠΈ ΠΈ ΠΏΠΎΠΌΠΎΠ³Π°ΡΡ Π² ΡΠΎΠΊΡΠ°ΡΠ΅Π½ΠΈΠΈ ΡΠΎΡΠΌΠΎΠ·Π½ΠΎΠ³ΠΎ ΠΏΡΡΠΈ. Π‘ΠΏΠ΅ΡΠΈΠ°Π»ΠΈΡΡΡ ΠΈΠ· ΠΊΠΎΠΌΠΏΠ°Π½ΠΈΠΈ Bosch ΡΠ²Π΅ΡΠ΅Π½Ρ, ΡΡΠΎ Π½ΠΎΠ²ΠΈΠ½ΠΊΠ° ΠΎΠΊΠ°ΠΆΠ΅ΡΡΡ Π΅ΡΡ ΡΡΡΠ΅ΠΊΡΠΈΠ²Π½Π΅Π΅ ΡΡΠ°Π½Π΄Π°ΡΡΠ½ΠΎΠ³ΠΎ Brake Assist.
DBC
ΠΠ²ΡΠΎΡΠ°ΠΌΠΈ ΡΡΠΎΠΉ ΡΠΈΡΡΠ΅ΠΌΡ ΡΠΎΡΠΌΠΎΠΆΠ΅Π½ΠΈΡ Π²ΡΡΡΡΠΏΠ°ΡΡ ΠΈΠ½ΠΆΠ΅Π½Π΅ΡΡ Π½Π΅ΠΌΠ΅ΡΠΊΠΎΠΉ ΠΊΠΎΠΌΠΏΠ°Π½ΠΈΠΈ BMW. Π§Π΅ΠΌ-ΡΠΎ ΡΠ΅ΡΠ΅Π½ΠΈΠ΅ Π½Π°ΠΏΠΎΠΌΠΈΠ½Π°Π΅Ρ ΡΠ°ΡΡΠΌΠΎΡΡΠ΅Π½Π½ΡΠΉ ΡΠ°Π½Π΅Π΅ BA. ΠΠΎ Π½Π΅ΠΌΠ΅ΡΠΊΠ°Ρ ΡΠΈΡΡΠ΅ΠΌΠ° ΠΏΠΎΠΌΠΎΠ³Π°Π΅Ρ ΡΡΠΊΠΎΡΡΡΡ ΠΈ Π΄ΠΎΠΏΠΎΠ»Π½ΠΈΡΠ΅Π»ΡΠ½ΠΎ ΡΡΠΈΠ»ΠΈΠ²Π°ΡΡ ΡΠΎΡΡ Π΄Π°Π²Π»Π΅Π½ΠΈΡ Π² ΠΏΡΠΈΠ²ΠΎΠ΄Π΅ ΡΠΎΡΠΌΠΎΠ·Π° Π°Π²ΡΠΎΠΌΠΎΠ±ΠΈΠ»Ρ ΠΏΡΠΈ ΡΠΊΡΡΡΠ΅Π½Π½ΠΎΠΉ ΠΎΡΡΠ°Π½ΠΎΠ²ΠΊΠ΅. ΠΠ°ΠΆΠ΅ Π΅ΡΠ»ΠΈ Π²ΠΎΠ΄ΠΈΡΠ΅Π»Ρ ΠΏΡΠΈΠΊΠ»Π°Π΄ΡΠ²Π°Π΅Ρ Π½Π΅Π±ΠΎΠ»ΡΡΠΎΠ΅ ΡΡΠΈΠ»ΠΈΠ΅, ΡΠΎΡΠΌΠΎΠ·Π½ΠΎΠΉ ΠΏΡΡΡ ΡΠΎΠΊΡΠ°ΡΠ°Π΅ΡΡΡ Π΄ΠΎ ΠΌΠΈΠ½ΠΈΠΌΡΠΌΠ°. ΠΠ²ΡΠΎΠΌΠ°ΡΠΈΡΠ΅ΡΠΊΠ°Ρ ΡΠΈΡΡΠ΅ΠΌΠ° ΡΡΠΈΡΡΠ²Π°Π΅Ρ ΠΈΠ½ΡΠΎΡΠΌΠ°ΡΠΈΡ ΠΎ ΡΠΊΠΎΡΠΎΡΡΠΈ ΠΏΠΎΠ²ΡΡΠ΅Π½ΠΈΡ Π΄Π°Π²Π»Π΅Π½ΠΈΡ ΠΈ ΡΡΠΈΠ»ΠΈΠΈ, ΠΊΠΎΡΠΎΡΠΎΠ΅ ΠΏΡΠΈΠΊΠ»Π°Π΄ΡΠ²Π°Π΅Ρ Π²ΠΎΠ΄ΠΈΡΠ΅Π»Ρ. Π’Π°ΠΊ ΠΊΠΎΠΌΠΏΡΡΡΠ΅Ρ ΠΎΠΏΡΠ΅Π΄Π΅Π»ΡΠ΅Ρ, ΡΠ²Π»ΡΠ΅ΡΡΡ Π»ΠΈ ΡΠΈΡΡΠ°ΡΠΈΡ ΠΎΠΏΠ°ΡΠ½ΠΎΠΉ. ΠΡΠ»ΠΈ Π΄Π°, Π½Π΅Π·Π°ΠΌΠ΅Π΄Π»ΠΈΡΠ΅Π»ΡΠ½ΠΎ Π΄Π°Π²Π»Π΅Π½ΠΈΠ΅ Π²ΠΎΠ·ΡΠ°ΡΡΠ°Π΅Ρ Π΄ΠΎ ΠΌΠ°ΠΊΡΠΈΠΌΡΠΌΠ°, ΡΡΠΎ ΠΈ ΠΏΠΎΠ·Π²ΠΎΠ»ΡΠ΅Ρ ΠΌΠ°ΡΠΈΠ½Π΅ Π·Π°ΡΠΎΡΠΌΠΎΠ·ΠΈΡΡ Π±ΡΡΡΡΠ΅Π΅.
ΠΠΎΠΏΠΎΠ»Π½ΠΈΡΠ΅Π»ΡΠ½ΠΎ Π±Π»ΠΎΠΊ ΡΠΏΡΠ°Π²Π»Π΅Π½ΠΈΠ΅ΠΌ ΡΡΠΈΡΡΠ²Π°Π΅Ρ Π΄Π°Π½Π½ΡΠ΅ ΠΎ ΡΠΊΠΎΡΠΎΡΡΠΈ Π΄Π²ΠΈΠΆΠ΅Π½ΠΈΡ ΠΎ ΡΡΠ΅ΠΏΠ΅Π½ΠΈ ΠΈΠ·Π½ΠΎΡΠ° ΡΠΎΡΠΌΠΎΠ·ΠΎΠ². DBC ΠΎΡΠ½ΠΎΠ²Π°Π½Π° Π½Π° ΠΏΡΠΈΠ½ΡΠΈΠΏΠ΅ Π³ΠΈΠ΄ΡΠ°Π²Π»ΠΈΡΠ΅ΡΠΊΠΎΠ³ΠΎ ΡΡΠΈΠ»Π΅Π½ΠΈΡ, Π² ΠΎΡΠ»ΠΈΡΠΈΠ΅ ΠΎΡ ΠΊΠΎΠ½ΠΊΡΡΠ΅Π½ΡΠΎΠ², Π³Π΄Π΅ ΠΏΡΠΈΠΌΠ΅Π½ΡΠ΅ΡΡΡ Π²Π°ΠΊΡΡΠΌΠ½ΡΠΉ ΠΏΡΠΈΠ½ΡΠΈΠΏ. ΠΡΠ°ΠΊΡΠΈΠΊΠ° ΠΏΠΎΠΊΠ°Π·ΡΠ²Π°Π΅Ρ, ΡΡΠΎ Π³ΠΈΠ΄ΡΠ°Π²Π»ΠΈΠΊΠ° ΡΠΏΠΎΡΠΎΠ±ΡΡΠ²ΡΠ΅Ρ Π»ΡΡΡΠ΅ΠΌΡ ΠΈ Π±ΠΎΠ»Π΅Π΅ ΡΠΎΡΠ½ΠΎ ΡΠ°ΡΠΏΡΠ΅Π΄Π΅Π»ΡΠ΅ΠΌΠΎΠΌΡ ΡΠΎΡΠΌΠΎΠ·Π½ΠΎΠΌΡ ΡΡΠΈΠ»ΠΈΡ ΠΏΡΠΈ ΡΠΊΡΡΡΠ΅Π½Π½ΡΡ ΠΈ Π°Π²Π°ΡΠΈΠΉΠ½ΡΡ ΠΎΡΡΠ°Π½ΠΎΠ²ΠΊΠ°Ρ Π°Π²ΡΠΎΡΡΠ°Π½ΡΠΏΠΎΡΡΠ°. ΠΠ»Π΅ΠΊΡΡΠΎΠ½ΠΈΠΊΠ° DBC Π½Π°ΠΏΡΡΠΌΡΡ ΡΠ²ΡΠ·Π°Π½Π° Ρ ΡΠΈΡΡΠ΅ΠΌΠΎΠΉ ΡΡΠ°Π±ΠΈΠ»ΠΈΠ·Π°ΡΠΈΠΈ ΠΈ ABS.
CBC
ΠΡΡ ΡΠΈΡΡΠ΅ΠΌΡ ΡΠ°Π·ΡΠ°Π±ΠΎΡΠ°Π»ΠΈ ΡΠ°ΠΊΠΆΠ΅ Π±Π°Π²Π°ΡΡΠΊΠΈΠ΅ ΡΠΏΠ΅ΡΠΈΠ°Π»ΠΈΡΡΡ ΠΈΠ· BMW Π΅ΡΡ Π² 1997 Π³ΠΎΠ΄Ρ. ΠΠΎΠ³Π΄Π° Π°Π²ΡΠΎ Π½Π°ΡΠΈΠ½Π°Π΅Ρ ΡΠΎΡΠΌΠΎΠ·ΠΈΡΡ, Π·Π°Π΄Π½ΠΈΠ΅ ΠΊΠΎΠ»ΡΡΠ° Π½Π° ΠΌΠ°ΡΠΈΠ½Π΅ ΡΠ°Π·Π³ΡΡΠΆΠ°ΡΡΡΡ. ΠΡΠ»ΠΈ ΡΡΠΎ ΡΠΎΡΠΌΠΎΠΆΠ΅Π½ΠΈΠ΅ ΠΏΡΠΎΠΈΡΡ ΠΎΠ΄ΠΈΡ Π² ΠΏΠΎΠ²ΠΎΡΠΎΡΠ΅, Π·Π°Π΄Π½ΡΡ ΠΎΡΡ ΠΌΠΎΠΆΠ΅Ρ Π·Π°Π½Π΅ΡΡΠΈ, ΠΏΠΎΡΠΊΠΎΠ»ΡΠΊΡ ΡΠ°ΡΡΡΡ Π½Π°Π³ΡΡΠ·ΠΊΠ° Π½Π° ΠΏΠ΅ΡΠ΅Π΄Π½ΡΡ ΡΠ°ΡΡΡ. CBC ΡΠ΅ΡΠ½ΠΎ ΡΠ²ΡΠ·Π°Π½Π° Ρ ABS. ΠΡ ΡΠΎΠ²ΠΌΠ΅ΡΡΠ½Π°Ρ ΡΠ°Π±ΠΎΡΠ° ΠΏΠΎΠ·Π²ΠΎΠ»ΡΠ΅Ρ ΠΏΡΠ΅Π΄ΠΎΡΠ²ΡΠ°ΡΠ°ΡΡ Π²ΠΎΠ·ΠΌΠΎΠΆΠ½ΡΠΉ ΡΠ½ΠΎΡ Π·Π°Π΄Π½Π΅ΠΉ ΠΎΡΠΈ, ΠΊΠΎΠ³Π΄Π° Π²ΠΎΠ΄ΠΈΡΠ΅Π»Ρ Π½Π°ΡΠΈΠ½Π°Π΅Ρ ΡΠΎΡΠΌΠΎΠ·ΠΈΡΡ Π½Π° Π²Ρ ΠΎΠ΄Π΅ Π² ΠΏΠΎΠ²ΠΎΡΠΎΡ. Π‘ΠΈΡΡΠ΅ΠΌΠ° ΠΎΠΏΡΠΈΠΌΠ°Π»ΡΠ½ΠΎ ΡΠ°ΡΠΏΡΠ΅Π΄Π΅Π»ΡΠ΅Ρ ΡΠΎΡΠΌΠΎΠ·Π½ΡΠ΅ ΡΡΠΈΠ»ΠΈΡ. Π ΠΈΡΠΎΠ³Π΅ Π·Π°Π½ΠΎΡ Π½Π΅ ΠΏΡΠΎΠΈΡΡ ΠΎΠ΄ΠΈΡ, Π΄Π°ΠΆΠ΅ Π΅ΡΠ»ΠΈ Π²ΠΎΠ΄ΠΈΡΠ΅Π»Ρ ΠΏΠ»ΠΎΡΠ½ΠΎ ΠΈ ΡΠ΅Π·ΠΊΠΎ Π·Π°ΠΆΠΈΠΌΠ°Π΅Ρ ΠΏΠ΅Π΄Π°Π»Ρ ΡΠΎΡΠΌΠΎΠ·Π°. Π‘ΠΈΠ³Π½Π°Π»Ρ, ΠΈΠ΄ΡΡΠΈΠ΅ ΠΎΡ Π΄Π°ΡΡΠΈΠΊΠΎΠ² ABS, ΠΏΠ΅ΡΠ΅Π΄Π°ΡΡΡΡ Π½Π° CBC. Π’Π°ΠΊΠΆΠ΅ ΠΎΠΏΡΠ΅Π΄Π΅Π»ΡΠ΅ΡΡΡ ΡΠΊΠΎΡΠΎΡΡΡ, Ρ ΠΊΠΎΡΠΎΡΠΎΠΉ Π²ΡΠ°ΡΠ°ΡΡΡΡ ΠΊΠΎΠ»ΡΡΠ°. ΠΡΠΈ Π΄Π°Π½Π½ΡΠ΅ ΠΏΠΎΠ·Π²ΠΎΠ»ΡΡΡ ΡΠ΅Π³ΡΠ»ΠΈΡΠΎΠ²Π°ΡΡ ΡΠΎΡΡ ΡΠΎΡΠΌΠΎΠ·Π½ΠΎΠ³ΠΎ ΡΡΠΈΠ»ΠΈΡ Π΄Π»Ρ ΠΊΠ°ΠΆΠ΄ΠΎΠ³ΠΎ ΠΈΠ· ΡΠΈΠ»ΠΈΠ½Π΄ΡΠΎΠ². ΠΡΠΎΠΈΡΡ ΠΎΠ΄ΠΈΡ ΡΡΠΎ ΡΠ°ΠΊ, ΡΡΠΎΠ±Ρ Π½Π°ΡΠ°ΡΡΠ°Π½ΠΈΠ΅ ΠΏΡΠΎΠΈΡΡ ΠΎΠ΄ΠΈΠ»ΠΎ ΠΈΠ½ΡΠ΅Π½ΡΠΈΠ²Π½Π΅Π΅ Π½Π° Π²Π½Π΅ΡΠ½Π΅ΠΌ ΠΏΠ΅ΡΠ΅Π΄Π½Π΅ΠΌ ΠΊΠΎΠ»Π΅ΡΠ΅, Π΅ΡΠ»ΠΈ ΡΠΌΠΎΡΡΠ΅ΡΡ ΠΎΡΠ½ΠΎΡΠΈΡΠ΅Π»ΡΠ½ΠΎ ΠΏΠΎΠ²ΠΎΡΠΎΡΠ°. Π’Π°ΠΊΠΎΠΉ ΠΏΡΠΈΠ½ΡΠΈΠΏ Π΄Π΅ΠΉΡΡΠ²ΠΈΡ ΠΏΠΎΠ·Π²ΠΎΠ»ΡΠ΅Ρ ΠΏΡΠ΅Π΄ΠΎΡΠ²ΡΠ°ΡΠ°ΡΡ Π·Π°Π½ΠΎΡΡ. ΠΠ° Π°Π²ΡΠΎΠΌΠΎΠ±ΠΈΠ»ΡΡ ΡΠΈΡΡΠ΅ΠΌΠ° ΡΠ°Π±ΠΎΡΠ°Π΅Ρ ΠΏΠΎΡΡΠΎΡΠ½Π½ΠΎ, Π½ΠΎ ΡΡΠΎ ΠΎΡΡΠ°ΡΡΡΡ Π½Π΅Π·Π°ΠΌΠ΅ΡΠ½ΡΠΌ Π΄Π»Ρ Π²ΠΎΠ΄ΠΈΡΠ΅Π»Π΅ΠΉ. Π₯ΠΎΡΡ ΠΏΠΎΠ»ΡΠ·Π° ΠΎΡ ΠΏΠΎΠ΄ΠΎΠ±Π½ΠΎΠ³ΠΎ ΡΠ΅ΡΠ΅Π½ΠΈΡ ΠΎΠ³ΡΠΎΠΌΠ½Π°Ρ.
EBD
ΠΠ½ΠΎΠ³ΠΎ Π³ΠΎΠ²ΠΎΡΠΈΡΡΡ ΠΎ ΡΠΈΡΡΠ΅ΠΌΠ΅ ΡΠ°ΡΠΏΡΠ΅Π΄Π΅Π»Π΅Π½ΠΈΡ ΡΠΎΡΠΌΠΎΠ·Π½ΡΡ ΡΡΠΈΠ»ΠΈΠΉ EBD, Π½ΠΎ Π½Π΅ ΠΊΠ°ΠΆΠ΄ΡΠΉ ΡΠΎΡΠ½ΠΎ ΠΏΠΎΠ½ΠΈΠΌΠ°Π΅Ρ, ΡΡΠΎ ΡΡΠΎ ΡΠ°ΠΊΠΎΠ΅. EBD ΡΠ°ΡΡΠΈΡΡΠΎΠ²ΡΠ²Π°Π΅ΡΡΡ ΠΊΠ°ΠΊ ΡΠ»Π΅ΠΊΡΡΠΎΠ½Π½Π°Ρ ΡΠΈΡΡΠ΅ΠΌΠ° ΡΠ°ΡΠΏΡΠ΅Π΄Π΅Π»Π΅Π½ΠΈΡ ΡΠΎΡΠΌΠΎΠ·Π½ΡΡ ΡΡΠΈΠ»ΠΈΠΉ. ΠΠ· ΡΡΠΎΠ³ΠΎ ΡΠΆΠ΅ ΡΡΠ°Π½ΠΎΠ²ΠΈΡΡΡ ΠΏΡΠΈΠΌΠ΅ΡΠ½ΠΎ ΠΏΠΎΠ½ΡΡΠ½ΠΎ, ΠΊΠ°ΠΊΠΈΠ΅ ΡΡΠ½ΠΊΡΠΈΠΈ ΠΈ Π·Π°Π΄Π°ΡΠΈ Π²ΡΠΏΠΎΠ»Π½ΡΠ΅Ρ ΡΠΈΡΡΠ΅ΠΌΠ°. Π Π°Π²ΡΠΎΠΌΠΎΠ±ΠΈΠ»ΡΡ ΡΡΠΎ ΡΠ΅ΡΠ΅Π½ΠΈΠ΅ ΠΈΡΠΏΠΎΠ»ΡΠ·ΡΠ΅ΡΡΡ Π΄Π»Ρ ΡΠΎΠ³ΠΎ, ΡΡΠΎΠ±Ρ ΠΏΠ΅ΡΠ΅ΡΠ°ΡΠΏΡΠ΅Π΄Π΅Π»ΡΡΡ ΡΡΠΈΠ»ΠΈΡ ΠΎΡ ΡΠΎΡΠΌΠΎΠ·ΠΎΠ² ΠΌΠ΅ΠΆΠ΄Ρ Π·Π°Π΄Π½ΠΈΠΌΠΈ ΠΈ ΠΏΠ΅ΡΠ΅Π΄Π½ΠΈΠΌΠΈ ΠΊΠΎΠ»ΡΡΠ°ΠΌΠΈ. ΠΠ»ΡΡ ΡΠΈΡΡΠ΅ΠΌΠ° ΡΠ°ΡΠΏΡΠ΅Π΄Π΅Π»Π΅Π½ΠΈΡ ΡΠΎΡΠΌΠΎΠ·Π½ΠΎΠ³ΠΎ ΡΡΠΈΠ»ΠΈΡ, ΠΈΠ»ΠΈ ΠΏΡΠΎΡΡΠΎ EBD, ΠΏΠΎΠΌΠΎΠ³Π°Π΅Ρ Π² Π³ΡΠ°ΠΌΠΎΡΠ½ΠΎΠΌ Π°Π²ΡΠΎΠΌΠ°ΡΠΈΡΠ΅ΡΠΊΠΎΠΌ ΠΏΠ΅ΡΠ΅Π½Π°ΠΏΡΠ°Π²Π»Π΅Π½ΠΈΠΈ ΠΌΠ΅ΠΆΠ΄Ρ Π»Π΅Π²ΠΎΠΉ ΠΈ ΠΏΡΠ°Π²ΠΎΠΉ ΡΡΠΎΡΠΎΠ½ΠΎΠΉ ΡΡΠ°Π½ΡΠΏΠΎΡΡΠ½ΠΎΠ³ΠΎ ΡΡΠ΅Π΄ΡΡΠ²Π°, ΠΎΠΏΠΈΡΠ°ΡΡΡ Π½Π΅ ΡΠ΅ΠΊΡΡΠΈΠ΅ ΡΡΠ»ΠΎΠ²ΠΈΡ ΠΏΠ΅ΡΠ΅Π΄Π²ΠΈΠΆΠ΅Π½ΠΈΡ. ΠΠΠ Π²Ρ ΠΎΠ΄ΠΈΡ Π² ΡΠΎΡΡΠ°Π² ΡΡΠ°Π΄ΠΈΡΠΈΠΎΠ½Π½ΠΎΠΉ ΡΠΈΡΡΠ΅ΠΌΡ ABS, ΠΎΡΠ½Π°ΡΡΠ½Π½ΠΎΠΉ ΡΠ»Π΅ΠΊΡΡΠΎΠ½Π½ΡΠΌ ΡΠΏΡΠ°Π²Π»Π΅Π½ΠΈΠ΅ΠΌ.
ΠΠΎΠ³Π΄Π° ΠΌΠ°ΡΠΈΠ½Π° Π΄Π²ΠΈΠΆΠ΅ΡΡΡ ΠΏΡΡΠΌΠΎΠ»ΠΈΠ½Π΅ΠΉΠ½ΠΎ ΠΈ Π½Π°ΡΠΈΠ½Π°Π΅Ρ ΡΠΎΡΠΌΠΎΠ·ΠΈΡΡ, Π½Π°Π³ΡΡΠ·ΠΊΠ° ΠΏΠ΅ΡΠ΅ΡΠ°ΡΠΏΡΠ΅Π΄Π΅Π»ΡΠ΅ΡΡΡ. Π ΠΈΠΌΠ΅Π½Π½ΠΎ Π½Π°Π³ΡΡΠΆΠ°ΡΡΡΡ ΠΏΠ΅ΡΠ΅Π΄Π½ΠΈΠ΅ ΠΊΠΎΠ»ΡΡΠ°, Π° Π·Π°Π΄Π½ΠΈΠ΅ Π½Π°ΠΎΠ±ΠΎΡΠΎΡ ΡΠ°Π·Π³ΡΡΠΆΠ°ΡΡΡΡ. ΠΡΠ»ΠΈ Ρ Π·Π°Π΄Π½ΠΈΡ ΡΠΎΡΠΌΠΎΠ·ΠΎΠ² Π±ΡΠ΄Π΅Ρ Π°Π½Π°Π»ΠΎΠ³ΠΈΡΠ½ΠΎΠ΅ ΡΡΠΈΠ»ΠΈΠ΅, ΠΊΠ°ΠΊ ΠΈ Π²ΠΏΠ΅ΡΠ΅Π΄ΠΈ, Π·Π½Π°ΡΠΈΡΠ΅Π»ΡΠ½ΠΎ Π²ΠΎΠ·ΡΠ°ΡΡΡΡ Π²Π΅ΡΠΎΡΡΠ½ΠΎΡΡΡ Π²ΠΎΠ·Π½ΠΈΠΊΠ½ΠΎΠ²Π΅Π½ΠΈΡ Π±Π»ΠΎΠΊΠΈΡΠΎΠ²ΠΊΠΈ Π½Π° Π·Π°Π΄Π½ΠΈΡ ΠΊΠΎΠ»ΡΡΠ°Ρ . ΠΡΠΏΠΎΠ»ΡΠ·ΡΡ ΡΠΏΠ΅ΡΠΈΠ°Π»ΡΠ½ΡΠ΅ Π΄Π°ΡΡΠΈΠΊΠΈ ΡΠΊΠΎΡΠΎΡΡΠΈ, ΡΠ»Π΅ΠΊΡΡΠΎΠ½Π½ΡΠΉ ΡΠΏΡΠ°Π²Π»ΡΡΡΠΈΠΉ Π±Π»ΠΎΠΊ ABS ΠΎΠΏΡΠ΅Π΄Π΅Π»ΡΠ΅Ρ Π½ΡΠΆΠ½ΡΠΉ ΠΌΠΎΠΌΠ΅Π½Ρ ΠΈ ΡΠ΅Π³ΡΠ»ΠΈΡΡΠ΅Ρ ΡΡΠΈΠ»ΠΈΠ΅. ΠΠΎ ΠΌΠ½ΠΎΠ³ΠΎΠΌ Π³ΡΠ°ΠΌΠΎΡΠ½ΠΎΠ΅ ΡΠ°ΡΠΏΡΠ΅Π΄Π΅Π»Π΅Π½ΠΈΠ΅ Π·Π°Π²ΠΈΡΠΈΡ ΠΎΡ ΡΠΎΠ³ΠΎ, ΠΊΠ°ΠΊΡΡ ΠΌΠ°ΡΡΡ ΠΈΠΌΠ΅Π΅Ρ ΠΏΠ΅ΡΠ΅Π²ΠΎΠ·ΠΈΠΌΡΠΉ Π³ΡΡΠ· ΠΈ ΠΊΠ°ΠΊ ΠΎΠ½ ΡΠ°ΡΠΏΠΎΠ»Π°Π³Π°Π΅ΡΡΡ.
Π’Π°ΠΊΠΆΠ΅ ΠΠΠ ΠΎΠΊΠ°Π·ΡΠ²Π°Π΅ΡΡΡ ΠΏΠΎΠ»Π΅Π·Π½ΠΎΠΉ ΠΏΡΠΈ ΡΠΎΡΠΌΠΎΠΆΠ΅Π½ΠΈΠΈ Π²ΠΎ Π²ΡΠ΅ΠΌΡ Π²Ρ ΠΎΠ΄Π° Π² ΠΏΠΎΠ²ΠΎΡΠΎΡΡ. Π’ΠΎΠ³Π΄Π° ΠΏΡΠΎΠΈΡΡ ΠΎΠ΄ΠΈΡ ΡΠ²Π΅Π»ΠΈΡΠ΅Π½ΠΈΠ΅ Π½Π°Π³ΡΡΠ·ΠΊΠΈ Π½Π° Π²Π½Π΅ΡΠ½ΠΈΠ΅ ΠΊΠΎΠ»ΡΡΠ° ΠΎΡΠ½ΠΎΡΠΈΡΠ΅Π»ΡΠ½ΠΎ ΠΏΠΎΠ²ΠΎΡΠΎΡΠ° ΠΈ ΡΠ°Π·Π³ΡΡΠ·ΠΊΠ° Π²Π½ΡΡΡΠ΅Π½Π½ΠΈΡ . Π’Π΅ΠΌ ΡΠ°ΠΌΡΠΌ Π³Π°ΡΠ°Π½ΡΠΈΡΡΠ΅ΡΡΡ Π·Π°ΡΠΈΡΠ° ΠΎΡ Π²ΠΎΠ·ΠΌΠΎΠΆΠ½ΠΎΠΉ Π±Π»ΠΎΠΊΠΈΡΠΎΠ²ΠΊΠΈ. ΠΠΠ ΠΎΡΠΈΠ΅Π½ΡΠΈΡΡΠ΅ΡΡΡ Π½Π° ΡΠΈΠ³Π½Π°Π»Ρ Π΄Π°ΡΡΠΈΠΊΠΎΠ², ΡΡΡΠ°Π½ΠΎΠ²Π»Π΅Π½Π½ΡΡ Π½Π° ΠΊΠΎΠ»ΡΡΠ°Ρ , Π° ΡΠ°ΠΊΠΆΠ΅ Π΄Π°ΡΡΠΈΠΊΠΎΠ² Π·Π°ΠΌΠ΅Π΄Π»Π΅Π½ΠΈΡ ΠΈΠ»ΠΈ ΡΡΠΊΠΎΡΠ΅Π½ΠΈΡ. ΠΡΠΎ ΠΏΠΎΠ·Π²ΠΎΠ»ΡΠ΅Ρ ΡΠΈΡΡΠ΅ΠΌΠ΅ ΠΎΠΏΡΠ΅Π΄Π΅Π»ΠΈΡΡ, ΠΊΠ°ΠΊΠΈΠ΅ ΡΡΠ»ΠΎΠ²ΠΈΡ Π½ΡΠΆΠ½ΠΎ ΡΠΎΠ·Π΄Π°ΡΡ Π΄Π»Ρ Π±Π΅Π·ΠΎΠΏΠ°ΡΠ½ΠΎΠ³ΠΎ ΡΠΎΡΠΌΠΎΠΆΠ΅Π½ΠΈΡ. ΠΠΎΠΌΠ±ΠΈΠ½ΠΈΡΡΡ ΡΠ°Π·Π½ΡΠ΅ ΠΊΠ»Π°ΠΏΠ°Π½Ρ, Π΄Π°Π²Π»Π΅Π½ΠΈΠ΅ ΡΠ°Π±ΠΎΡΠ΅ΠΉ ΠΆΠΈΠ΄ΠΊΠΎΡΡΠΈ ΠΏΠ΅ΡΠ΅ΡΠ°ΡΠΏΡΠ΅Π΄Π΅Π»ΡΠ΅ΡΡΡ. Π ΠΈΡΠΎΠ³Π΅ Π² ΠΊΠ°ΠΆΠ΄ΠΎΠΌ ΠΈΠ· ΠΊΠΎΠ»ΡΡ ΠΎΡΠΌΠ΅ΡΠ°Π΅ΡΡΡ ΡΠ°Π·Π½ΡΠΉ ΠΏΠΎΠΊΠ°Π·Π°ΡΠ΅Π»Ρ Π΄Π°Π²Π»Π΅Π½ΠΈΡ.
Π‘ΠΎΠ²ΡΠ΅ΠΌΠ΅Π½Π½ΡΠ΅ ΡΠΎΡΠΌΠΎΠ·Π½ΡΠ΅ ΠΌΠ΅Ρ Π°Π½ΠΈΠ·ΠΌΡ ΡΠΎΡ ΡΠ°Π½ΠΈΠ»ΠΈ ΡΠ²ΠΎΠΉ ΠΈΠ·Π½Π°ΡΠ°Π»ΡΠ½ΡΠΉ ΠΏΡΠΈΠ½ΡΠΈΠΏ ΡΠ°Π±ΠΎΡΡ. ΠΠΎ Π½ΠΎΠ²ΡΠ΅ ΡΠ°Π·ΡΠ°Π±ΠΎΡΠΊΠΈ ΡΡΠΌΠ΅Π»ΠΈ Π·Π½Π°ΡΠΈΡΠ΅Π»ΡΠ½ΠΎ ΠΏΠΎΠ²ΡΡΠΈΡΡ ΠΈΡ ΡΡΡΠ΅ΠΊΡΠΈΠ²Π½ΠΎΡΡΡ. Π’Π΅ΠΏΠ΅ΡΡ ΠΌΠ°ΡΠΈΠ½Π° Π½Π΅ ΠΏΡΠΎΡΡΠΎ ΠΌΠΎΠΆΠ΅Ρ Π·Π°ΡΠΎΡΠΌΠΎΠ·ΠΈΡΡ. ΠΠ½Π° Π΄Π΅Π»Π°Π΅Ρ ΡΡΠΎ Π°ΠΊΠΊΡΡΠ°ΡΠ½ΠΎ, ΠΈΠ·Π±Π΅Π³Π°Ρ Π±Π»ΠΎΠΊΠΈΡΠΎΠ²ΠΊΠΈ ΠΊΠΎΠ»ΡΡ, Π·Π°Π½ΠΎΡΠΎΠ² ΠΈ ΠΏΡΠΎΡΠΈΡ Π½Π΅ΠΏΡΠΈΡΡΠ½ΠΎΡΡΠ΅ΠΉ, ΠΊΠΎΡΠΎΡΡΠ΅ ΠΌΠΎΠ³ΡΡ Π²ΠΎΠ·Π½ΠΈΠΊΠ½ΡΡΡ ΠΏΡΠΈ Π½Π΅ΠΎΠ±Ρ ΠΎΠ΄ΠΈΠΌΠΎΡΡΠΈ ΡΠΊΡΡΡΠ΅Π½Π½ΠΎ ΡΠ±ΡΠΎΡΠΈΡΡ ΡΠΊΠΎΡΠΎΡΡΡ. ΠΠ½ΠΎΠ³ΠΈΠ΅ Π½Π΅Π΄ΠΎΠΎΡΠ΅Π½ΠΈΠ²Π°ΡΡ Π·Π½Π°ΡΠΈΠΌΠΎΡΡΡ ΡΠΎΠ²ΡΠ΅ΠΌΠ΅Π½Π½ΡΡ ΡΠΎΡΠΌΠΎΠ·Π½ΡΡ ΡΠΈΡΡΠ΅ΠΌ. Π₯ΠΎΡΡ ΠΈΠΌΠ΅Π½Π½ΠΎ ΠΎΠ½ΠΈ Π²ΠΎ ΠΌΠ½ΠΎΠ³ΠΎΠΌ ΠΏΠΎΠΌΠΎΠ³Π°ΡΡ ΡΠ²Π΅ΡΠ΅Π½Π½ΠΎ ΡΡΠ²ΡΡΠ²ΠΎΠ²Π°ΡΡ ΡΠ΅Π±Ρ Π½Π° Π΄ΠΎΡΠΎΠ³Π°Ρ , Π²Ρ ΠΎΠ΄ΠΈΡΡ Π² ΠΏΠΎΠ²ΠΎΡΠΎΡΡ Π½Π° ΡΠΎΠ»ΠΈΠ΄Π½ΡΡ ΡΠΊΠΎΡΠΎΡΡΡΡ ΠΈ ΡΠ²ΠΎΠ΅Π²ΡΠ΅ΠΌΠ΅Π½Π½ΠΎ ΠΎΡΡΠ°Π½Π°Π²Π»ΠΈΠ²Π°ΡΡΡΡ ΠΏΠ΅ΡΠ΅Π΄ Π²ΡΡΠΊΠΎΡΠΈΠ²ΡΠΈΠΌ Π²ΠΏΠ΅ΡΠ΅Π΄ΠΈ ΠΏΡΠ΅ΠΏΡΡΡΡΠ²ΠΈΠ΅ΠΌ. ΠΠ°Π»ΠΈΡΠΈΠ΅ Π²ΡΠ΅Ρ Π°ΡΡΠΈΡΡΠΎΠ² ΡΠΎΡΠΌΠΎΠ·Π½ΠΎΠΉ ΡΠΈΡΡΠ΅ΠΌΡ ΠΏΠΎΡΡΠ΅ΠΏΠ΅Π½Π½ΠΎ ΡΡΠ°Π½ΠΎΠ²ΠΈΡΡΡ ΠΎΠ±ΡΠ·Π°ΡΠ΅Π»ΡΠ½ΡΠΌ ΡΡΠ»ΠΎΠ²ΠΈΠ΅ΠΌ ΠΏΡΠΈ ΠΏΡΠΎΠΈΠ·Π²ΠΎΠ΄ΡΡΠ²Π΅ ΠΈ ΠΏΡΠΎΠ΄Π°ΠΆΠ΅ Π½ΠΎΠ²ΡΡ Π°Π²ΡΠΎΠΌΠΎΠ±ΠΈΠ»Π΅ΠΉ. Π ΡΡΠΎ Π°Π±ΡΠΎΠ»ΡΡΠ½ΠΎ ΠΏΡΠ°Π²ΠΈΠ»ΡΠ½ΠΎΠ΅ ΡΠ΅ΡΠ΅Π½ΠΈΠ΅, Π½Π°ΠΏΡΠ°Π²Π»Π΅Π½Π½ΠΎΠ΅ Π½Π° ΠΏΠΎΠ²ΡΡΠ΅Π½ΠΈΠ΅ Π±Π΅Π·ΠΎΠΏΠ°ΡΠ½ΠΎΡΡΠΈ Π½Π° Π΄ΠΎΡΠΎΠ³Π°Ρ ΠΈ ΡΠ½ΠΈΠΆΠ΅Π½ΠΈΠ΅ ΠΊΠΎΠ»ΠΈΡΠ΅ΡΡΠ²Π° Π°Π²Π°ΡΠΈΠΉΠ½ΡΡ ΡΠΈΡΡΠ°ΡΠΈΠΉ ΠΈΠ»ΠΈ Π΄ΠΎΡΠΎΠΆΠ½ΠΎ-ΡΡΠ°Π½ΡΠΏΠΎΡΡΠ½ΡΡ ΠΏΡΠΎΠΈΡΡΠ΅ΡΡΠ²ΠΈΠΉ.
ΠΡΡΡΠΈΠ΅ ΡΠ΅Π½Ρ ΠΈ ΡΡΠ»ΠΎΠ²ΠΈΡ Π½Π° ΠΏΠΎΠΊΡΠΏΠΊΡ Π½ΠΎΠ²ΡΡ Π°Π²ΡΠΎ
ΠΡΠ΅Π΄ΠΈΡ 6,5% / Π Π°ΡΡΡΠΎΡΠΊΠ° / Trade-in / 98% ΠΎΠ΄ΠΎΠ±ΡΠ΅Π½ΠΈΠΉ / ΠΠΎΠ΄Π°ΡΠΊΠΈ Π² ΡΠ°Π»ΠΎΠ½Π΅ ΠΠ°Ρ ΠΠΎΡΠΎΡΡdrivertip.ru
1.2. ΠΠΈΠ΄Ρ ΡΠΎΡΠΌΠΎΠ·Π½ΡΡ ΡΠΈΡΡΠ΅ΠΌ Π°Π²ΡΠΎΠΌΠΎΠ±ΠΈΠ»Ρ
Π’ΠΎΡΠΌΠΎΠ·Π½Π°Ρ ΡΠΈΡΡΠ΅ΠΌΠ° Π½Π΅ΠΎΠ±Ρ ΠΎΠ΄ΠΈΠΌΠ° Π΄Π»Ρ Π·Π°ΠΌΠ΅Π΄Π»Π΅Π½ΠΈΡ ΡΡΠ°Π½ΡΠΏΠΎΡΡΠ½ΠΎΠ³ΠΎ ΡΡΠ΅Π΄ΡΡΠ²Π° ΠΈ ΠΏΠΎΠ»Π½ΠΎΠΉ ΠΎΡΡΠ°Π½ΠΎΠ²ΠΊΠΈ Π°Π²ΡΠΎΠΌΠΎΠ±ΠΈΠ»Ρ, Π° ΡΠ°ΠΊΠΆΠ΅ Π΅Π³ΠΎ ΡΠ΄Π΅ΡΠΆΠ°Π½ΠΈΡ Π½Π° ΠΌΠ΅ΡΡΠ΅.
ΠΠ»Ρ ΡΡΠΎΠ³ΠΎ Π½Π° Π°Π²ΡΠΎΠΌΠΎΠ±ΠΈΠ»Π΅ ΠΈΡΠΏΠΎΠ»ΡΠ·ΡΡΡ Π½Π΅ΠΊΠΎΡΠΎΡΡΠ΅ ΡΠΎΡΠΌΠΎΠ·Π½ΡΠ΅ ΡΠΈΡΡΠ΅ΠΌΠ°, ΠΊΠ°ΠΊ — ΡΡΠΎΡΠ½ΠΎΡΠ½Π°Ρ, ΡΠ°Π±ΠΎΡΠ°Ρ, Π²ΡΠΏΠΎΠΌΠΎΠ³Π°ΡΠ΅Π»ΡΠ½Π°Ρ ΡΠΈΡΡΠ΅ΠΌΠ° ΠΈ Π·Π°ΠΏΠ°ΡΠ½Π°Ρ.
Π Π°Π±ΠΎΡΠ°Ρ ΡΠΎΡΠΌΠΎΠ·Π½Π°Ρ ΡΠΈΡΡΠ΅ΠΌΠ° ΠΈΡΠΏΠΎΠ»ΡΠ·ΡΠ΅ΡΡΡ ΠΏΠΎΡΡΠΎΡΠ½Π½ΠΎ, Π½Π° Π»ΡΠ±ΠΎΠΉ ΡΠΊΠΎΡΠΎΡΡΠΈ, Π΄Π»Ρ Π·Π°ΠΌΠ΅Π΄Π»Π΅Π½ΠΈΡ ΠΈ ΠΎΡΡΠ°Π½ΠΎΠ²ΠΊΠΈ Π°Π²ΡΠΎΠΌΠΎΠ±ΠΈΠ»Ρ. Π Π°Π±ΠΎΡΠ°Ρ ΡΠΎΡΠΌΠΎΠ·Π½Π°Ρ ΡΠΈΡΡΠ΅ΠΌΠ°, ΠΏΡΠΈΠ²ΠΎΠ΄ΠΈΡΡΡ Π² Π΄Π΅ΠΉΡΡΠ²ΠΈΠ΅, ΠΏΡΡΠ΅ΠΌ Π½Π°ΠΆΠ°ΡΠΈΡ Π½Π° ΠΏΠ΅Π΄Π°Π»Ρ ΡΠΎΡΠΌΠΎΠ·Π°. ΠΠ½Π° ΡΠ²Π»ΡΠ΅ΡΡΡ ΡΠ°ΠΌΠΎΠΉ ΡΡΡΠ΅ΠΊΡΠΈΠ²Π½ΠΎΠΉ ΡΠΈΡΡΠ΅ΠΌΠΎΠΉ ΠΈΠ· Π²ΡΠ΅Ρ ΠΎΡΡΠ°Π»ΡΠ½ΡΡ .
ΠΠ°ΠΏΠ°ΡΠ½Π°Ρ ΡΠΎΡΠΌΠΎΠ·Π½Π°Ρ ΡΠΈΡΡΠ΅ΠΌΠ° ΠΈΡΠΏΠΎΠ»ΡΠ·ΡΠ΅ΡΡΡ ΠΏΡΠΈ Π½Π΅ΠΈΡΠΏΡΠ°Π²Π½ΠΎΡΡΠΈ ΠΎΡΠ½ΠΎΠ²Π½ΠΎΠΉ. ΠΠ½Π° Π±ΡΠ²Π°Π΅Ρ Π² Π²ΠΈΠ΄Π΅ Π°Π²ΡΠΎΠ½ΠΎΠΌΠ½ΠΎΠΉ ΡΠΈΡΡΠ΅ΠΌΡ ΠΈΠ»ΠΈ Π΅Ρ ΡΡΠ½ΠΊΡΠΈΡ Π²ΡΠΏΠΎΠ»Π½ΡΠ΅Ρ ΡΠ°ΡΡΡ ΠΈΡΠΏΡΠ°Π²Π½ΠΎΠΉ ΡΠ°Π±ΠΎΡΠ΅ΠΉ ΡΠΎΡΠΌΠΎΠ·Π½ΠΎΠΉ ΡΠΈΡΡΠ΅ΠΌΡ.
Π‘ΡΠΎΡΠ½ΠΎΡΠ½Π°Ρ ΡΠΎΡΠΌΠΎΠ·Π½Π°Ρ ΡΠΈΡΡΠ΅ΠΌΠ°Β Π½ΡΠΆΠ½Π° Π΄Π»Ρ ΡΠ΄Π΅ΡΠΆΠ°Π½ΠΈΡ Π°Π²ΡΠΎΠΌΠΎΠ±ΠΈΠ»Ρ Π½Π° ΠΎΠ΄Π½ΠΎΠΌ ΠΌΠ΅ΡΡΠ΅. Π‘ΡΠΎΡΠ½ΠΎΡΠ½ΡΡ ΡΠΈΡΡΠ΅ΠΌΡ ΠΈΡΠΏΠΎΠ»ΡΠ·ΡΡ Π²ΠΎ ΠΈΠ·Π±Π΅ΠΆΠ°Π½ΠΈΠ΅ ΡΠ°ΠΌΠΎΠΏΡΠΎΠΈΠ·Π²ΠΎΠ»ΡΠ½ΠΎΠ³ΠΎ Π΄Π²ΠΈΠΆΠ΅Π½ΠΈΡ Π°Π²ΡΠΎΠΌΠΎΠ±ΠΈΠ»Ρ.
ΠΡΠΏΠΎΠΌΠΎΠ³Π°ΡΠ΅Π»ΡΠ½Π°Ρ ΡΠΎΡΠΌΠΎΠ·Π½Π°Ρ ΡΠΈΡΡΠ΅ΠΌΠ°Β ΠΏΡΠΈΠΌΠ΅Π½ΡΠ΅ΡΡΡ Π½Π° Π°Π²ΡΠΎ Ρ ΠΏΠΎΠ²ΡΡΠ΅Π½Π½ΠΎΠΉ ΠΌΠ°ΡΡΠΎΠΉ. ΠΡΠΏΠΎΠΌΠΎΠ³Π°ΡΠ΅Π»ΡΠ½ΡΡ ΡΠΈΡΡΠ΅ΠΌΡ ΠΈΡΠΏΠΎΠ»ΡΠ·ΡΡΡ Π΄Π»Ρ ΡΠΎΡΠΌΠΎΠΆΠ΅Π½ΠΈΡ Π½Π° ΡΠΊΠ»ΠΎΠ½Π°Ρ ΠΈ ΡΠΏΡΡΠΊΠ°Ρ . ΠΠ΅ ΡΠ΅Π΄ΠΊΠΎ Π±ΡΠ²Π°Π΅Ρ, ΡΡΠΎ Π½Π° Π°Π²ΡΠΎΠΌΠΎΠ±ΠΈΠ»ΡΡ ΡΠΎΠ»Ρ Π²ΡΠΏΠΎΠΌΠΎΠ³Π°ΡΠ΅Π»ΡΠ½ΠΎΠΉ ΡΠΈΡΡΠ΅ΠΌΡ ΠΈΠ³ΡΠ°Π΅Ρ Π΄Π²ΠΈΠ³Π°ΡΠ΅Π»Ρ, Π³Π΄Π΅ Π²ΡΠΏΡΡΠΊΠ½ΠΎΠΉ ΡΡΡΠ±ΠΎΠΏΡΠΎΠ²ΠΎΠ΄ ΠΏΠ΅ΡΠ΅ΠΊΡΡΠ²Π°Π΅Ρ Π·Π°ΡΠ»ΠΎΠ½ΠΊΠ°.
Π’ΠΎΡΠΌΠΎΠ·Π½Π°Ρ ΡΠΈΡΡΠ΅ΠΌΠ° — ΡΡΠΎ Π²Π°ΠΆΠ½Π΅ΠΉΡΠ°Ρ Π½Π΅ΠΎΡΡΠ΅ΠΌΠ»Π΅ΠΌΠ°Ρ ΡΠ°ΡΡΡ Π°Π²ΡΠΎΠΌΠΎΠ±ΠΈΠ»Ρ, ΡΠ»ΡΠΆΠ°ΡΠ°Ρ Π΄Π»Ρ ΠΎΠ±Π΅ΡΠΏΠ΅ΡΠ΅Π½ΠΈΡ Π°ΠΊΡΠΈΠ²Π½ΠΎΠΉ Π±Π΅Π·ΠΎΠΏΠ°ΡΠ½ΠΎΡΡΠΈ Π²ΠΎΠ΄ΠΈΡΠ΅Π»Π΅ΠΉ ΠΈ ΠΏΠ΅ΡΠ΅Ρ ΠΎΠ΄ΠΎΠ². ΠΠ° ΠΌΠ½ΠΎΠ³ΠΈΡ Π°Π²ΡΠΎΠΌΠΎΠ±ΠΈΠ»ΡΡ ΠΏΡΠΈΠΌΠ΅Π½ΡΡΡ ΡΠ°Π·Π»ΠΈΡΠ½ΡΠ΅ ΡΡΡΡΠΎΠΉΡΡΠ²Π° ΠΈ ΡΠΈΡΡΠ΅ΠΌΡ, ΠΏΠΎΠ²ΡΡΠ°ΡΡΠΈΠ΅ ΡΡΡΠ΅ΠΊΡΠΈΠ²Π½ΠΎΡΡΡ ΡΠΈΡΡΠ΅ΠΌΡ ΠΏΡΠΈ ΡΠΎΡΠΌΠΎΠΆΠ΅Π½ΠΈΠΈ β ΡΡΠΎ Π°Π½ΡΠΈΠ±Π»ΠΎΠΊΠΈΡΠΎΠ²ΠΎΡΠ½Π°Ρ ΡΠΈΡΡΠ΅ΠΌΠ° (ABS), ΡΡΠΈΠ»ΠΈΡΠ΅Π»Ρ ΡΠΊΡΡΡΠ΅Π½Π½ΠΎΠ³ΠΎ ΡΠΎΡΠΌΠΎΠΆΠ΅Π½ΠΈΡ (BAS), ΡΡΠΈΠ»ΠΈΡΠ΅Π»Ρ ΡΠΎΡΠΌΠΎΠ·ΠΎΠ² [3].
1.3. ΠΡΠ½ΠΎΠ²Π½ΡΠ΅ ΡΠ»Π΅ΠΌΠ΅Π½ΡΡ ΡΠΎΡΠΌΠΎΠ·Π½ΠΎΠΉ ΡΠΈΡΡΠ΅ΠΌΡ Π°Π²ΡΠΎΠΌΠΎΠ±ΠΈΠ»Ρ
Π’ΠΎΡΠΌΠΎΠ·Π½Π°Ρ ΡΠΈΡΡΠ΅ΠΌΠ° Π°Π²ΡΠΎΠΌΠΎΠ±ΠΈΠ»Ρ ΡΠΎΡΡΠΎΠΈΡ ΠΈΠ· ΡΠΎΡΠΌΠΎΠ·Π½ΠΎΠ³ΠΎ ΠΏΡΠΈΠ²ΠΎΠ΄Π° ΠΈ ΡΠΎΡΠΌΠΎΠ·Π½ΠΎΠ³ΠΎ ΠΌΠ΅Ρ Π°Π½ΠΈΠ·ΠΌΠ° [5].
Π ΠΈΡ.1.3. Π‘Ρ Π΅ΠΌΠ° Π³ΠΈΠ΄ΡΠΎΠΏΡΠΈΠ²ΠΎΠ΄Π° ΡΠΎΡΠΌΠΎΠ·ΠΎΠ²: 1 β ΡΡΡΠ±ΠΎΠΏΡΠΎΠ²ΠΎΠ΄ ΠΊΠΎΠ½ΡΡΡΠ° Β«Π»Π΅Π²ΡΠΉ ΠΏΠ΅ΡΠ΅Π΄Π½ΠΈΠΉ-ΠΏΡΠ°Π²ΡΠΉ Π·Π°Π΄Π½ΠΈΠΉ ΡΠΎΡΠΌΠΎΠ·Β»; 2-ΡΠΈΠ³Π½Π°Π»ΡΠ½ΠΎΠ΅ ΡΡΡΡΠΎΠΉΡΡΠ²ΠΎ; 3 β ΡΡΡΠ±ΠΎΠΏΡΠΎΠ²ΠΎΠ΄ ΠΊΠΎΠ½ΡΡΡΠ° Β«ΠΏΡΠ°Π²ΡΠΉ ΠΏΠ΅ΡΠ΅Π΄Π½ΠΈΠΉ β Π»Π΅Π²ΡΠΉ Π·Π°Π΄Π½ΠΈΠΉ ΡΠΎΡΠΌΠΎΠ·Β»; 4 β Π±Π°ΡΠΎΠΊ Π³Π»Π°Π²Π½ΠΎΠ³ΠΎ ΡΠΈΠ»ΠΈΠ½Π΄ΡΠ°; 5 β Π³Π»Π°Π²Π½ΡΠΉ ΡΠΈΠ»ΠΈΠ½Π΄Ρ Π³ΠΈΠ΄ΡΠΎΠΏΡΠΈΠ²ΠΎΠ΄Π° ΡΠΎΡΠΌΠΎΠ·ΠΎΠ²; 6 β Π²Π°ΠΊΡΡΠΌΠ½ΡΠΉ ΡΡΠΈΠ»ΠΈΡΠ΅Π»Ρ; 7 β ΠΏΠ΅Π΄Π°Π»Ρ ΡΠΎΡΠΌΠΎΠ·Π°; 8 β ΡΠ΅Π³ΡΠ»ΡΡΠΎΡ Π΄Π°Π²Π»Π΅Π½ΠΈΡ Π·Π°Π΄Π½ΠΈΡ ΡΠΎΡΠΌΠΎΠ·ΠΎΠ²; 9 β ΡΡΠΎΡ ΡΡΠΎΡΠ½ΠΎΡΠ½ΠΎΠ³ΠΎ ΡΠΎΡΠΌΠΎΠ·Π°; 10 β ΡΠΎΡΠΌΠΎΠ·Π½ΠΎΠΉ ΠΌΠ΅Ρ Π°Π½ΠΈΠ·ΠΌ Π·Π°Π΄Π½Π΅Π³ΠΎ ΠΊΠΎΠ»Π΅ΡΠ°; 11 β ΡΠ΅Π³ΡΠ»ΠΈΡΠΎΠ²ΠΎΡΠ½ΡΠΉ Π½Π°ΠΊΠΎΠ½Π΅ΡΠ½ΠΈΠΊ ΡΡΠΎΡΠ½ΠΎΡΠ½ΠΎΠ³ΠΎ ΡΠΎΡΠΌΠΎΠ·Π°; 12 β ΡΡΡΠ°Π³ ΠΏΡΠΈΠ²ΠΎΠ΄Π° ΡΡΠΎΡΠ½ΠΎΡΠ½ΠΎΠ³ΠΎ ΡΠΎΡΠΌΠΎΠ·Π°; 13 β ΡΠΎΡΠΌΠΎΠ·Π½ΠΎΠΉ ΠΌΠ΅Ρ Π°Π½ΠΈΠ·ΠΌ ΠΏΠ΅ΡΠ΅Π΄Π½Π΅Π³ΠΎ ΠΊΠΎΠ»Π΅ΡΠ°.
Π’ΠΎΡΠΌΠΎΠ·Π½ΡΠΌ ΠΌΠ΅Ρ Π°Π½ΠΈΠ·ΠΌΠΎΠΌΒ Π±Π»ΠΎΠΊΠΈΡΡΡΡΡΡ Π²ΡΠ°ΡΠ΅Π½ΠΈΡ ΠΊΠΎΠ»Π΅Ρ Π°Π²ΡΠΎΠΌΠΎΠ±ΠΈΠ»Ρ ΠΈ Π² ΡΠ»Π΅Π΄ΡΡΠ²ΠΈΠΈ ΡΠ΅Π³ΠΎ, ΠΏΠΎΡΠ²Π»ΡΠ΅ΡΡΡ ΡΠΎΡΠΌΠΎΠ·Π½Π°Ρ ΡΠΈΠ»Π°, ΠΊΠΎΡΠΎΡΠ°Ρ ΡΠ²Π»ΡΠ΅ΡΡΡ ΠΏΡΠΈΡΠΈΠ½ΠΎΠΉ ΠΎΡΡΠ°Π½ΠΎΠ²ΠΊΠΈ Π°Π²ΡΠΎΠΌΠΎΠ±ΠΈΠ»Ρ. Π’ΠΎΡΠΌΠΎΠ·Π½ΡΠ΅ ΠΌΠ΅Ρ Π°Π½ΠΈΠ·ΠΌΡ Π½Π°Ρ ΠΎΠ΄ΡΡΡΡ Π½Π° ΠΏΠ΅ΡΠ΅Π΄Π½ΠΈΡ ΠΈ Π·Π°Π΄Π½ΠΈΡ ΠΊΠΎΠ»Π΅ΡΠ°Ρ Π°Π²ΡΠΎΠΌΠΎΠ±ΠΈΠ»Ρ.
ΠΡΠΎΡΠ΅ Π³ΠΎΠ²ΠΎΡΡ, Π²ΡΠ΅ ΡΠΎΡΠΌΠΎΠ·Π½ΡΠ΅ ΠΌΠ΅Ρ Π°Π½ΠΈΠ·ΠΌΡ ΠΌΠΎΠΆΠ½ΠΎ Π½Π°Π·Π²Π°ΡΡ ΠΊΠΎΠ»ΠΎΠ΄ΠΎΡΠ½ΡΠΌΠΈ. Π ΡΠΆΠ΅ Π² ΡΠ²ΠΎΡ ΠΎΡΠ΅ΡΠ΅Π΄Ρ, ΠΈΡ ΠΌΠΎΠΆΠ½ΠΎ ΡΠ°Π·Π΄Π΅Π»ΡΡΡ ΠΏΠΎ ΡΡΠ΅Π½ΠΈΡ — Π±Π°ΡΠ°Π±Π°Π½Π½ΡΠ΅ ΠΈ Π΄ΠΈΡΠΊΠΎΠ²ΡΠ΅. Π’ΠΎΡΠΌΠΎΠ·Π½ΠΎΠΉ ΠΌΠ΅Ρ Π°Π½ΠΈΠ·ΠΌ ΠΎΡΠ½ΠΎΠ²Π½ΠΎΠΉ ΡΠΈΡΡΠ΅ΠΌΡ ΠΌΠΎΠ½ΡΠΈΡΡΠ΅ΡΡΡ Π² ΠΊΠΎΠ»Π΅ΡΠΎ, Π° Π·Π° ΡΠ°Π·Π΄Π°ΡΠΎΡΠ½ΠΎΠΉ ΠΊΠΎΡΠΎΠ±ΠΊΠΎΠΉ ΠΈΠ»ΠΈ ΠΊΠΎΡΠΎΠ±ΠΊΠΎΠΉ ΠΏΠ΅ΡΠ΅Π΄Π°Ρ Π½Π°Ρ ΠΎΠ΄ΠΈΡΡΡ ΠΌΠ΅Ρ Π°Π½ΠΈΠ·ΠΌ ΡΡΠΎΡΠ½ΠΎΡΠ½ΠΎΠΉ ΡΠΈΡΡΠ΅ΠΌΡ.
Π’ΠΎΡΠΌΠΎΠ·Π½ΡΠ΅ ΠΌΠ΅Ρ Π°Π½ΠΈΠ·ΠΌΡ, ΠΊΠ°ΠΊ ΠΏΡΠ°Π²ΠΈΠ»ΠΎ ΡΠΎΡΡΠΎΡΡ ΠΈΠ· Π΄Π²ΡΡ ΡΠ°ΡΡΠ΅ΠΉ, ΠΈΠ· Π½Π΅ΠΏΠΎΠ΄Π²ΠΈΠΆΠ½ΠΎΠΉ ΠΈ Π²ΡΠ°ΡΠ°ΡΡΠ΅ΠΉΡΡ. ΠΠ΅ΠΏΠΎΠ΄Π²ΠΈΠΆΠ½Π°Ρ ΡΠ°ΡΡΡ β ΡΡΠΎ ΡΠΎΡΠΌΠΎΠ·Π½ΡΠ΅ ΠΊΠΎΠ»ΠΎΠ΄ΠΊΠΈ, Π° Π²ΡΠ°ΡΠ°ΡΡΠ°ΡΡΡ ΡΠ°ΡΡΡ Π±Π°ΡΠ°Π±Π°Π½Π½ΠΎΠ³ΠΎ ΠΌΠ΅Ρ Π°Π½ΠΈΠ·ΠΌΠ° — ΡΡΠΎ ΡΠΎΡΠΌΠΎΠ·Π½ΠΎΠΉ Π±Π°ΡΠ°Π±Π°Π½.
ΠΠ°ΡΠ°Π±Π°Π½Π½ΡΠ΅ ΡΠΎΡΠΌΠΎΠ·Π½ΡΠ΅ ΠΌΠ΅Ρ Π°Π½ΠΈΠ·ΠΌΡ (ΡΠΈΡ. 1.4.) ΡΠ°ΡΠ΅ Π²ΡΠ΅Π³ΠΎ ΡΡΠΎΡΡ Π½Π° Π·Π°Π΄Π½ΠΈΡ ΠΊΠΎΠ»Π΅ΡΠ°Ρ Π°Π²ΡΠΎΠΌΠΎΠ±ΠΈΠ»Ρ. Π ΠΏΡΠΎΡΠ΅ΡΡΠ΅ ΡΠΊΡΠΏΠ»ΡΠ°ΡΠ°ΡΠΈΠΈ ΠΈΠ·-Π·Π° ΠΈΠ·Π½ΠΎΡΠ°, Π·Π°Π·ΠΎΡ ΠΌΠ΅ΠΆΠ΄Ρ ΠΊΠΎΠ»ΠΎΠ΄ΠΊΠΎΠΉ ΠΈ Π±Π°ΡΠ°Π±Π°Π½ΠΎΠΌ ΡΠ²Π΅Π»ΠΈΡΠΈΠ²Π°Π΅ΡΡΡ ΠΈ Π΄Π»Ρ Π΅Π³ΠΎ ΡΡΡΡΠ°Π½Π΅Π½ΠΈΡ ΠΈΡΠΏΠΎΠ»ΡΠ·ΡΡΡ ΠΌΠ΅Ρ Π°Π½ΠΈΡΠ΅ΡΠΊΠΈΠ΅ ΡΠ΅Π³ΡΠ»ΡΡΠΎΡΡ.
Π ΠΈΡ. 1.4. ΠΠ°ΡΠ°Π±Π°Π½Π½ΡΠΉ ΡΠΎΡΠΌΠΎΠ·Π½ΠΎΠΉ ΠΌΠ΅Ρ Π°Π½ΠΈΠ·ΠΌ Π·Π°Π΄Π½Π΅Π³ΠΎ ΠΊΠΎΠ»Π΅ΡΠ°: 1 β ΡΠ°ΡΠΊΠ°; 2 β ΠΏΡΠΈΠΆΠΈΠΌΠ½Π°Ρ ΠΏΡΡΠΆΠΈΠ½Π°; 3 β ΠΏΡΠΈΠ²ΠΎΠ΄Π½ΠΎΠΉ ΡΡΡΠ°Π³; 4 β ΡΠΎΡΠΌΠΎΠ·Π½Π°Ρ ΠΊΠΎΠ»ΠΎΠ΄ΠΊΠ°; 5 β Π²Π΅ΡΡ Π½ΡΡ ΡΡΡΠΆΠ½Π°Ρ ΠΏΡΡΠΆΠΈΠ½Π°; 6 β ΡΠ°ΡΠΏΠΎΡΠ½Π°Ρ ΠΏΠ»Π°Π½ΠΊΠ°; 7 β ΡΠ΅Π³ΡΠ»ΠΈΡΠΎΠ²ΠΎΡΠ½ΡΠΉ ΠΊΠ»ΠΈΠ½; 8 β ΠΊΠΎΠ»Π΅ΡΠ½ΡΠΉ ΡΠΎΡΠΌΠΎΠ·Π½ΠΎΠΉ ΡΠΈΠ»ΠΈΠ½Π΄Ρ; 9 β ΡΠΎΡΠΌΠΎΠ·Π½ΠΎΠΉ ΡΠΈΡ; 10 β Π±ΠΎΠ»Ρ; 11 β ΡΡΠ΅ΡΠΆΠ΅Π½Ρ; 12 β ΡΠΊΡΡΠ΅Π½ΡΡΠΈΠΊ; 13 β Π½Π°ΠΆΠΈΠΌΠ½Π°Ρ ΠΏΡΡΠΆΠΈΠ½Π°; 14 β Π½ΠΈΠΆΠ½ΡΡ ΡΡΡΠΆΠ½Π°Ρ ΠΏΡΡΠΆΠΈΠ½Π°; 15 β ΠΏΡΠΈΠΆΠΈΠΌΠ½Π°Ρ ΠΏΡΡΠΆΠΈΠ½Π° ΡΠ°ΡΠΏΠΎΡΠ½ΠΎΠΉ ΠΏΠ»Π°Π½ΠΊΠΈ.
ΠΠ° Π°Π²ΡΠΎΠΌΠΎΠ±ΠΈΠ»ΡΡ ΠΌΠΎΠ³ΡΡ ΠΏΡΠΈΠΌΠ΅Π½ΡΡΡ ΡΠ°Π·Π»ΠΈΡΠ½ΡΠ΅ ΠΊΠΎΠΌΠ±ΠΈΠ½Π°ΡΠΈΠΈ ΡΠΎΡΠΌΠΎΠ·Π½ΡΡ ΠΌΠ΅Ρ Π°Π½ΠΈΠ·ΠΌΠΎΠ²:
Π΄Π²Π° Π±Π°ΡΠ°Π±Π°Π½Π½ΡΡ Π·Π°Π΄Π½ΠΈΡ , Π΄Π²Π° Π΄ΠΈΡΠΊΠΎΠ²ΡΡ ΠΏΠ΅ΡΠ΅Π΄Π½ΠΈΡ ;
ΡΠ΅ΡΡΡΠ΅ Π±Π°ΡΠ°Π±Π°Π½Π½ΡΡ ;
ΡΠ΅ΡΡΡΠ΅ Π΄ΠΈΡΠΊΠΎΠ²ΡΡ .
Π ΡΠΎΡΠΌΠΎΠ·Π½ΠΎΠΌ Π΄ΠΈΡΠΊΠΎΠ²ΠΎΠΌ ΠΌΠ΅Ρ Π°Π½ΠΈΠ·ΠΌΠ΅ (ΡΠΈΡ. 1.5.)Β — Π΄ΠΈΡΠΊ Π²ΡΠ°ΡΠ°Π΅ΡΡΡ, Π° Π²Π½ΡΡΡΠΈ ΡΡΠΏΠΏΠΎΡΡΠ° ΡΡΡΠ°Π½ΠΎΠ²Π»Π΅Π½Ρ, Π΄Π²Π΅ Π½Π΅ΠΏΠΎΠ΄Π²ΠΈΠΆΠ½ΡΠ΅ ΠΊΠΎΠ»ΠΎΠ΄ΠΊΠΈ. Π ΡΡΠΏΠΏΠΎΡΡΠ΅ ΡΡΡΠ°Π½ΠΎΠ²Π»Π΅Π½Ρ ΡΠ°Π±ΠΎΡΠΈΠ΅ ΡΠΈΠ»ΠΈΠ½Π΄ΡΡ, ΠΏΡΠΈ ΡΠΎΡΠΌΠΎΠΆΠ΅Π½ΠΈΠΈ ΠΎΠ½ΠΈ ΠΏΡΠΈΠΆΠΈΠΌΠ°ΡΡ ΡΠΎΡΠΌΠΎΠ·Π½ΡΠ΅ ΠΊΠΎΠ»ΠΎΠ΄ΠΊΠΈ ΠΊ Π΄ΠΈΡΠΊΡ, Π° ΡΠ°ΠΌ ΡΡΠΏΠΏΠΎΡΡ Π½Π°Π΄Π΅ΠΆΠ½ΠΎ Π·Π°ΠΊΡΠ΅ΠΏΠ»Π΅Π½ Π½Π° ΠΊΡΠΎΠ½ΡΡΠ΅ΠΉΠ½Π΅. ΠΠ»Ρ ΡΠ²Π΅Π»ΠΈΡΠ΅Π½ΠΈΡ ΠΎΡΠ²ΠΎΠ΄Π° ΡΠ΅ΠΏΠ»Π° ΠΎΡ ΡΠ°Π±ΠΎΡΠ΅ΠΉ Π·ΠΎΠ½Ρ ΡΠ°ΡΡΠΎ ΠΈΡΠΏΠΎΠ»ΡΠ·ΡΡΡΡΡ Π²Π΅Π½ΡΠΈΠ»ΠΈΡΡΠ΅ΠΌΡΠ΅ Π΄ΠΈΡΠΊΠΈ [8].
Π ΠΈΡ. 1.5. Π‘Ρ Π΅ΠΌΠ° Π΄ΠΈΡΠΊΠΎΠ²ΠΎΠ³ΠΎ ΡΠΎΡΠΌΠΎΠ·Π½ΠΎΠ³ΠΎ ΠΌΠ΅Ρ Π°Π½ΠΈΠ·ΠΌΠ°: 1 β ΠΊΠΎΠ»Π΅ΡΠ½Π°Ρ ΡΠΏΠΈΠ»ΡΠΊΠ°; 2 β Π½Π°ΠΏΡΠ°Π²Π»ΡΡΡΠΈΠΉ ΠΏΠ°Π»Π΅Ρ; 3 β ΡΠΌΠΎΡΡΠΎΠ²ΠΎΠ΅ ΠΎΡΠ²Π΅ΡΡΡΠΈΠ΅; 4 β ΡΡΠΏΠΏΠΎΡΡ; 5 β ΠΊΠ»Π°ΠΏΠ°Π½; 6 β ΡΠ°Π±ΠΎΡΠΈΠΉ ΡΠΈΠ»ΠΈΠ½Π΄Ρ; 7 β ΡΠΎΡΠΌΠΎΠ·Π½ΠΎΠΉ ΡΠ»Π°Π½Π³; 8 β ΡΠΎΡΠΌΠΎΠ·Π½Π°Ρ ΠΊΠΎΠ»ΠΎΠ΄ΠΊΠ°; 9 β Π²Π΅Π½ΡΠΈΠ»ΡΡΠΈΠΎΠ½Π½ΠΎΠ΅ ΠΎΡΠ²Π΅ΡΡΡΠΈΠ΅; 10 β ΡΠΎΡΠΌΠΎΠ·Π½ΠΎΠΉ Π΄ΠΈΡΠΊ; 11 β ΡΡΡΠΏΠΈΡΠ° ΠΊΠΎΠ»Π΅ΡΠ°; 12 β Π³ΡΡΠ·Π΅Π·Π°ΡΠΈΡΠ½ΡΠΉ ΠΊΠΎΠ»ΠΏΠ°ΡΠΎΠΊ.
studfiles.net
ΠΠΈΠ΄Ρ ΡΠΎΡΠΌΠΎΠ·Π½ΡΡ ΠΌΠ΅Ρ Π°Π½ΠΈΠ·ΠΌΠΎΠ² Π°Π²ΡΠΎΠΌΠΎΠ±ΠΈΠ»Ρ: ΠΏΡΠ΅ΠΈΠΌΡΡΠ΅ΡΡΠ²Π° ΠΈ Π½Π΅Π΄ΠΎΡΡΠ°ΡΠΊΠΈ
- ΠΠ»Π°Π²Π½Π°Ρ
- ΠΠΎΠ²ΠΎΡΡΠΈ
- ΠΠ°Π΄ΡΡ
- ΠΡΠ²ΠΈ
- ΠΡΡΠ»ΠΈ
- Π Π΅ΠΊΠ»Π°ΠΌΠ°
- Π Π½Π°Ρ
27
ΠΈΡΠ»
Π Π΅ΠΊΠ»Π°ΠΌΠ½ΡΠΉ ΠΏΠΎΡΡ Π² Instagram-Π°ΠΊΠΊΠ°ΡΠ½ΡΠ΅ ΠΠ°ΠΊΠ°ΡΡΡΠΊΠ° ΠΌΠΎΠ³ Π±Ρ ΡΡΠΎΠΈΡΡ $225 20:35 Π ΠΎΠ΄ΡΡΠ²Π΅Π½Π½ΠΈΠΊΠ°ΠΌ ΠΏΠΎΠ³ΠΈΠ±ΡΠΈΡ Π² Π‘ΠΊΠ½ΠΈΠ»ΠΎΠ²ΡΠΊΠΎΠΉ Π°Π²ΠΈΠ°ΠΊΠ°ΡΠ°ΡΡΡΠΎΡΠ΅ Π²ΡΠΏΠ»Π°ΡΡΡ ΠΏΠΎ 2 ΡΡΡ. Π³ΡΠ½ 20:14 ΠΡΠ²ΠΈ
Π€ΠΠ€Π ΡΠ½ΡΠ»Π° ΡΠΈΠ»ΡΠΌ ΠΎ ΠΏΠΎΠ±Π΅Π΄Π½ΠΎΠΌ Π΄Π»Ρ Π£ΠΊΡΠ°ΠΈΠ½Ρ Π§Π U-20 19:51 ΠΠ¦Π£ ΡΠΎΠ·Π΄Π°Π»Π° ΡΡΠΌΡΠ½ΡΠΊΠΈΠΉ Π²ΠΈΠΊΠ°ΡΠΈΠ°Ρ 19:29 Π‘Π΅ΡΠΈΠ°Π» Β«Π Π°ΡΡΠΊΠ°Π· ΡΠ»ΡΠΆΠ°Π½ΠΊΠΈΒ» ΠΏΡΠΎΠ΄Π»ΠΈΠ»ΠΈ Π½Π° ΡΠ΅ΡΠ²Π΅ΡΡΡΠΉ ΡΠ΅Π·ΠΎΠ½ 19:08 Π‘Π°Π²ΠΈΠΊ Π¨ΡΡΡΠ΅Ρ Π²ΠΎΠ·Π²ΡΠ°ΡΠ°Π΅ΡΡΡ: Π±ΡΠ΄Π΅Ρ Π²Π΅ΡΡΠΈ ΡΠΎΠΊ-ΡΠΎΡ Π½Π° ΡΠ΅Π»Π΅ΠΊΠ°Π½Π°Π»Π΅ ΠΡ ΠΌΠ΅ΡΠΎΠ²Π° 18:50 ΠΠΎΡΠΊΡΠ΅ΡΠ΅Π½ΡΠ΅ Π² Π£ΠΊΡΠ°ΠΈΠ½Π΅ Π±ΡΠ΄Π΅Ρ ΠΆΠ°ΡΠΊΠΈΠΌ 18:27 ΠΠΊΡΠΊΠ»ΡΠ·ΠΈΠ²
ΠΡΠ»ΠΈ Π±Ρ Π’ΠΈΠΌΠΎΡΠ΅Π½ΠΊΠΎ Π±ΡΠ»Π° Π±Π»ΠΎΠ³Π΅ΡΠΎΠΌ — ΠΎΠ½Π° Π±Ρ ΡΠ°ΡΡΠΊΠ°Π·ΡΠ²Π°Π»Π° ΠΎ ΠΌΠΎΠ΄Π΅, — ΠΈΡΡΠ»Π΅Π΄ΠΎΠ²Π°Π½ΠΈΠ΅ 18:18 Bellingcat ΠΏΠΎΠ΄Π²Π΅ΡΠ³Π»Π°ΡΡ ΠΊΠΈΠ±Π΅ΡΠ°ΡΠ°ΠΊΠ΅ ΠΈΠ·-Π·Π° ΡΠ°ΡΡΠ»Π΅Π΄ΠΎΠ²Π°Π½ΠΈΡ Π΄Π΅ΠΉΡΡΠ²ΠΈΠΉ Π ΠΎΡΡΠΈΠΈ 17:59 Π£ΠΌΠ΅Ρ ΡΠΊΡΠ°ΠΈΠ½ΡΠΊΠΈΠΉ Π»Π΅Π³ΠΊΠΎΠ°ΡΠ»Π΅Ρ Π ΠΎΠΌΠ°Π½ ΠΠΈΡΠ°ΡΡΡΠΊ 17:42 ΠΠ°Π΄ΡΡ
ΠΠΊΡΠΈΡ ΠΏΡΠΎΡΠ΅ΡΡΠ° Π² ΠΠΎΡΠΊΠ²Π΅: Π·Π°Π΄Π΅ΡΠΆΠ°Π½Ρ Π±ΠΎΠ»Π΅Π΅ 500 ΡΠ΅Π»ΠΎΠ²Π΅ΠΊ 17:39 ΠΠΊΡΠΊΠ»ΡΠ·ΠΈΠ²
ΠΠ΄ΠΈΠ½ ΠΏΠΎΡΡ Π² Instagram ΠΠΎΡΠΎΡΠ΅Π½ΠΊΠΎ ΠΌΠΎΠ³ Π±Ρ ΡΡΠΎΠΈΡΡ ΠΎΠΊΠΎΠ»ΠΎ $600, — ΠΈΡΡΠ»Π΅Π΄ΠΎΠ²Π°Π½ΠΈΠ΅ 17:25 Π‘Π°Π°ΠΊΠ°ΡΠ²ΠΈΠ»ΠΈ ΡΠΎΠ±ΠΈΡΠ°Π΅ΡΡΡ ΠΏΠ΅ΡΠ΅Π΅Ρ Π°ΡΡ Π² ΠΠ΄Π΅ΡΡΡ ΠΈ ΠΎΡΠ²ΠΎΠ±ΠΎΠ΄ΠΈΡΡ Π³ΠΎΡΠΎΠ΄ ΠΎΡ Π±Π°Π½Π΄ΠΈΡΠΎΠ² 17:20 17 Π»Π΅Ρ Π‘ΠΊΠ½ΠΈΠ»ΠΎΠ²ΡΠΊΠΎΠΉ ΡΡΠ°Π³Π΅Π΄ΠΈΠΈ: ΠΊΠ°ΠΊ Π²ΡΠ΅ Π±ΡΠ»ΠΎ 16:51 ΠΠ΅Π»Π΅Π½ΡΠΊΠΈΠΉ ΠΏΠΎΡΡΠ΅Π±ΠΎΠ²Π°Π» ΡΠ²ΠΎΠ»ΡΠ½Π΅Π½ΠΈΡ Π³Π»Π°Π²Ρ ΠΠ°ΡΠΏΠΎΠ»ΠΈΡΠΈΠΈ ΠΠ½Π΅ΠΏΡΠΎΠΏΠ΅ΡΡΠΎΠ²ΡΠΊΠΎΠΉ ΠΎΠ±Π»Π°ΡΡΠΈ
bykvu.com
ΠΠ²ΡΠΎΠΌΠΎΠ±ΠΈΠ»ΡΠ½ΡΠ΅ ΡΠΎΡΠΌΠΎΠ·Π½ΡΠ΅ ΡΠΈΡΡΠ΅ΠΌΡ, Π²ΠΈΠ΄Ρ, ΡΡΡΡΠΎΠΉΡΡΠ²ΠΎ, ΠΊΠ°ΠΊ ΡΠ°Π±ΠΎΡΠ°ΡΡ
Π’ΠΎΡΠΌΠΎΠ·Π½Π°Ρ ΡΠΈΡΡΠ΅ΠΌΠ° Π½Π΅ΠΎΠ±Ρ ΠΎΠ΄ΠΈΠΌΠ° Π΄Π»Ρ Π±ΡΡΡΡΠΎΠ³ΠΎ ΠΈΠ·ΠΌΠ΅Π½Π΅Π½ΠΈΡ ΡΠΊΠΎΡΠΎΡΡΠΈ ΠΈΠ»ΠΈ ΠΏΠΎΠ»Π½ΠΎΠΉ ΠΎΡΡΠ°Π½ΠΎΠ²ΠΊΠΈ Π°Π²ΡΠΎΠΌΠΎΠ±ΠΈΠ»Ρ ΠΈ ΡΠ΄Π΅ΡΠΆΠ°Π½ΠΈΡ Π΅Π³ΠΎ Π½Π° ΠΌΠ΅ΡΡΠ΅ ΠΏΡΠΈ ΡΡΠΎΡΠ½ΠΊΠ΅.
ΠΠ»Ρ ΡΡΠΎΠ³ΠΎ Π½Π° Π°Π²ΡΠΎΠΌΠΎΠ±ΠΈΠ»Π΅ Π΅ΡΡΡ ΡΠ°ΠΊΠΈΠ΅ Π²ΠΈΠ΄Ρ ΡΠΎΡΠΌΠΎΠ·Π½ΡΡ ΡΠΈΡΡΠ΅ΠΌ, ΠΊΠ°ΠΊ β ΡΠ°Π±ΠΎΡΠ°Ρ, ΡΡΠΎΡΠ½ΠΎΡΠ½Π°Ρ, Π·Π°ΠΏΠ°ΡΠ½Π°Ρ ΠΈ Π²ΡΠΏΠΎΠΌΠΎΠ³Π°ΡΠ΅Π»ΡΠ½Π°Ρ ΡΠΈΡΡΠ΅ΠΌΠ° (ΡΠΎΡΠΌΠΎΠ·-Π·Π°ΠΌΠ΅Π΄Π»ΠΈΡΠ΅Π»Ρ).
Π Π°Π±ΠΎΡΠ°Ρ ΡΠΎΡΠΌΠΎΠ·Π½Π°Ρ ΡΠΈΡΡΠ΅ΠΌΠ° Π²ΡΠ΅Π³Π΄Π° ΠΈΡΠΏΠΎΠ»ΡΠ·ΡΠ΅ΡΡΡ ΠΏΡΠΈ Π»ΡΠ±ΠΎΠΉ ΡΠΊΠΎΡΠΎΡΡΠΈ Π°Π²ΡΠΎΠΌΠΎΠ±ΠΈΠ»Ρ Π΄Π»Ρ ΠΏΠΎΠ»Π½ΠΎΠΉ ΠΎΡΡΠ°Π½ΠΎΠ²ΠΊΠΈ ΠΈΠ»ΠΈ Π΄Π»Ρ ΡΠ½ΠΈΠΆΠ΅Π½ΠΈΡ ΡΠΊΠΎΡΠΎΡΡΠΈ. Π Π°Π±ΠΎΡΠ°Ρ ΡΠΎΡΠΌΠΎΠ·Π½Π°Ρ ΡΠΈΡΡΠ΅ΠΌΠ° Π½Π°ΡΠΈΠ½Π°Π΅Ρ ΡΠ°Π±ΠΎΡΠ°ΡΡ ΠΏΡΠΈ Π½Π°ΠΆΠ°ΡΠΈΠΈ Π½Π° ΠΏΠ΅Π΄Π°Π»Ρ ΡΠΎΡΠΌΠΎΠ·Π°. ΠΡΠ° ΡΠΈΡΡΠ΅ΠΌΠ° ΡΠ°ΠΌΠ°Ρ ΡΡΡΠ΅ΠΊΡΠΈΠ²Π½Π°Ρ ΠΏΡΠΈ ΡΡΠ°Π²Π½Π΅Π½ΠΈΠΈ Ρ Π΄ΡΡΠ³ΠΈΠΌΠΈ Π²ΠΈΠ΄Π°ΠΌΠΈ.
ΠΠ°ΠΏΠ°ΡΠ½Π°Ρ ΡΠΎΡΠΌΠΎΠ·Π½Π°Ρ ΡΠΈΡΡΠ΅ΠΌΠ° ΠΏΡΠΈΠΌΠ΅Π½ΡΠ΅ΡΡΡ ΠΏΡΠΈ Π½Π΅ΠΈΡΠΏΡΠ°Π²Π½ΠΎΡΡΠΈ ΠΎΡΠ½ΠΎΠ²Π½ΠΎΠΉ ΡΠΈΡΡΠ΅ΠΌΡ. ΠΠ°ΠΏΠ°ΡΠ½Π°Ρ ΡΠΎΡΠΌΠΎΠ·Π½Π°Ρ ΡΠΈΡΡΠ΅ΠΌΠ° Π±ΡΠ²Π°Π΅Ρ Π² Π²ΠΈΠ΄Π΅ Π°Π²ΡΠΎΠ½ΠΎΠΌΠ½ΠΎΠΉ ΡΠΈΡΡΠ΅ΠΌΡ ΠΈΠ»ΠΈ Π΅Ρ ΡΡΠ½ΠΊΡΠΈΠΈ Π²ΡΠΏΠΎΠ»Π½ΡΠ΅Ρ ΡΠ°ΡΡΡ ΠΈΡΠΏΡΠ°Π²Π½ΠΎΠΉ ΡΠ°Π±ΠΎΡΠ΅ΠΉ ΡΠΎΡΠΌΠΎΠ·Π½ΠΎΠΉ ΡΠΈΡΡΠ΅ΠΌΡ.
Π‘ΡΠΎΡΠ½ΠΎΡΠ½Π°Ρ ΡΠΎΡΠΌΠΎΠ·Π½Π°Ρ ΡΠΈΡΡΠ΅ΠΌΠ° Π½Π΅ΠΎΠ±Ρ ΠΎΠ΄ΠΈΠΌΠ° Π΄Π»Ρ ΡΠ΄Π΅ΡΠΆΠ°Π½ΠΈΡ Π°Π²ΡΠΎΠΌΠΎΠ±ΠΈΠ»Ρ ΠΎΠΏΡΠ΅Π΄Π΅Π»Π΅Π½Π½ΠΎΠ΅ Π²ΡΠ΅ΠΌΡ Π½Π° ΠΎΠ΄Π½ΠΎΠΌ ΠΌΠ΅ΡΡΠ΅. Π‘ΡΠΎΡΠ½ΠΎΡΠ½Π°Ρ ΡΠΈΡΡΠ΅ΠΌΠ° ΠΏΠΎΠ»Π½ΠΎΡΡΡΡ ΠΈΡΠΊΠ»ΡΡΠ°Π΅Ρ Π΄Π²ΠΈΠΆΠ΅Π½ΠΈΠ΅ Π°Π²ΡΠΎΠΌΠΎΠ±ΠΈΠ»Ρ ΡΠ°ΠΌΠΎΠΏΡΠΎΠΈΠ·Π²ΠΎΠ»ΡΠ½ΠΎ.
ΠΡΠΏΠΎΠΌΠΎΠ³Π°ΡΠ΅Π»ΡΠ½Π°Ρ ΡΠΎΡΠΌΠΎΠ·Π½Π°Ρ ΡΠΈΡΡΠ΅ΠΌΠ° ΠΏΡΠΈΠΌΠ΅Π½ΡΠ΅ΡΡΡ Π½Π° Π°Π²ΡΠΎΠΌΠΎΠ±ΠΈΠ»ΡΡ Ρ ΠΏΠΎΠ²ΡΡΠ΅Π½Π½ΠΎΠΉ ΠΌΠ°ΡΡΠΎΠΉ. ΠΡΠΏΠΎΠΌΠΎΠ³Π°ΡΠ΅Π»ΡΠ½Π°Ρ ΡΠΈΡΡΠ΅ΠΌΠ° ΠΈΡΠΏΠΎΠ»ΡΠ·ΡΠ΅ΡΡΡ Π΄Π»Ρ ΡΠΎΡΠΌΠΎΠΆΠ΅Π½ΠΈΡ Π½Π° ΡΠΏΡΡΠΊΠ°Ρ . Π§Π°ΡΡΠΎ Π±ΡΠ²Π°Π΅Ρ, ΡΡΠΎ Π½Π° Π°Π²ΡΠΎΠΌΠΎΠ±ΠΈΠ»ΡΡ ΡΠΎΠ»Ρ Π²ΡΠΏΠΎΠΌΠΎΠ³Π°ΡΠ΅Π»ΡΠ½ΠΎΠΉ ΡΠΈΡΡΠ΅ΠΌΡ Π²ΡΠΏΠΎΠ»Π½ΡΠ΅Ρ Π΄Π²ΠΈΠ³Π°ΡΠ΅Π»Ρ, Π³Π΄Π΅ Π²ΡΠΏΡΡΠΊΠ½ΠΎΠΉ ΡΡΡΠ±ΠΎΠΏΡΠΎΠ²ΠΎΠ΄ ΠΏΠ΅ΡΠ΅ΠΊΡΡΠ²Π°Π΅ΡΡΡ Π·Π°ΡΠ»ΠΎΠ½ΠΊΠΎΠΉ.
Π’ΠΎΡΠΌΠΎΠ·Π½Π°Ρ ΡΠΈΡΡΠ΅ΠΌΠ° β ΡΡΠΎ Π²Π°ΠΆΠ½ΠΎΠ΅ ΡΡΠ΅Π΄ΡΡΠ²ΠΎ Π°Π²ΡΠΎΠΌΠΎΠ±ΠΈΠ»Ρ Π΄Π»Ρ ΠΎΠ±Π΅ΡΠΏΠ΅ΡΠ΅Π½ΠΈΡ Π°ΠΊΡΠΈΠ²Π½ΠΎΠΉ Π±Π΅Π·ΠΎΠΏΠ°ΡΠ½ΠΎΡΡΠΈ. ΠΠ° Π°Π²ΡΠΎΠΌΠΎΠ±ΠΈΠ»ΡΡ ΠΏΡΠΈΠΌΠ΅Π½ΡΡΡΡΡ ΡΠ°Π·Π½ΡΠ΅ ΡΠΈΡΡΠ΅ΠΌΡ ΠΈ ΡΡΡΡΠΎΠΉΡΡΠ²Π°, ΠΏΠΎΠ²ΡΡΠ°ΡΡΠΈΠ΅ ΡΡΡΠ΅ΠΊΡΠΈΠ²Π½ΠΎΡΡΡ ΡΠΈΡΡΠ΅ΠΌΡ ΠΏΡΠΈ ΡΠΎΡΠΌΠΎΠΆΠ΅Π½ΠΈΠΈ β ΡΡΠΎ Π°Π½ΡΠΈΠ±Π»ΠΎΠΊΠΈΡΠΎΠ²ΠΎΡΠ½Π°Ρ ΡΠΈΡΡΠ΅ΠΌΠ°, ΡΡΠΈΠ»ΠΈΡΠ΅Π»Ρ ΡΠΊΡΡΡΠ΅Π½Π½ΠΎΠ³ΠΎ ΡΠΎΡΠΌΠΎΠΆΠ΅Π½ΠΈΡ, ΡΡΠΈΠ»ΠΈΡΠ΅Π»Ρ ΡΠΎΡΠΌΠΎΠ·ΠΎΠ².
Π’ΠΎΡΠΌΠΎΠ·Π½Π°Ρ ΡΠΈΡΡΠ΅ΠΌΠ° Π²ΠΊΠ»ΡΡΠ°Π΅Ρ Π² ΡΠ΅Π±Ρ ΡΠΎΡΠΌΠΎΠ·Π½ΠΎΠΉ ΠΏΡΠΈΠ²ΠΎΠ΄ ΠΈ ΡΠΎΡΠΌΠΎΠ·Π½ΠΎΠΉ ΠΌΠ΅Ρ Π°Π½ΠΈΠ·ΠΌ.
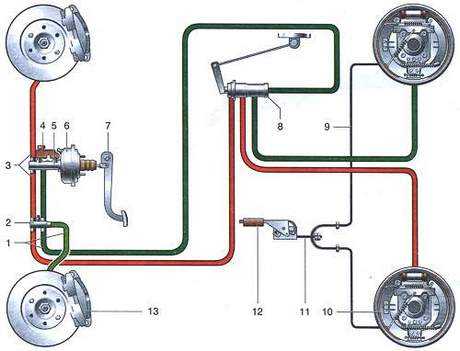
Π‘Ρ
Π΅ΠΌΠ° Π³ΠΈΠ΄ΡΠΎΠΏΡΠΈΠ²ΠΎΠ΄Π° ΡΠΎΡΠΌΠΎΠ·ΠΎΠ²:
1 β ΡΡΡΠ±ΠΎΠΏΡΠΎΠ²ΠΎΠ΄ ΠΊΠΎΠ½ΡΡΡΠ° Β«Π»Π΅Π²ΡΠΉ ΠΏΠ΅ΡΠ΅Π΄Π½ΠΈΠΉ-ΠΏΡΠ°Π²ΡΠΉ Π·Π°Π΄Π½ΠΈΠΉ ΡΠΎΡΠΌΠΎΠ·Β»; 2-ΡΠΈΠ³Π½Π°Π»ΡΠ½ΠΎΠ΅ ΡΡΡΡΠΎΠΉΡΡΠ²ΠΎ; 3 β ΡΡΡΠ±ΠΎΠΏΡΠΎΠ²ΠΎΠ΄ ΠΊΠΎΠ½ΡΡΡΠ° Β«ΠΏΡΠ°Π²ΡΠΉ ΠΏΠ΅ΡΠ΅Π΄Π½ΠΈΠΉ β Π»Π΅Π²ΡΠΉ Π·Π°Π΄Π½ΠΈΠΉ ΡΠΎΡΠΌΠΎΠ·Β»; 4 β Π±Π°ΡΠΎΠΊ Π³Π»Π°Π²Π½ΠΎΠ³ΠΎ ΡΠΈΠ»ΠΈΠ½Π΄ΡΠ°; 5 β Π³Π»Π°Π²Π½ΡΠΉ ΡΠΈΠ»ΠΈΠ½Π΄Ρ Π³ΠΈΠ΄ΡΠΎΠΏΡΠΈΠ²ΠΎΠ΄Π° ΡΠΎΡΠΌΠΎΠ·ΠΎΠ²; 6 β Π²Π°ΠΊΡΡΠΌΠ½ΡΠΉ ΡΡΠΈΠ»ΠΈΡΠ΅Π»Ρ; 7 β ΠΏΠ΅Π΄Π°Π»Ρ ΡΠΎΡΠΌΠΎΠ·Π°; 8 β ΡΠ΅Π³ΡΠ»ΡΡΠΎΡ Π΄Π°Π²Π»Π΅Π½ΠΈΡ Π·Π°Π΄Π½ΠΈΡ
ΡΠΎΡΠΌΠΎΠ·ΠΎΠ²; 9 β ΡΡΠΎΡ ΡΡΠΎΡΠ½ΠΎΡΠ½ΠΎΠ³ΠΎ ΡΠΎΡΠΌΠΎΠ·Π°; 10 β ΡΠΎΡΠΌΠΎΠ·Π½ΠΎΠΉ ΠΌΠ΅Ρ
Π°Π½ΠΈΠ·ΠΌ Π·Π°Π΄Π½Π΅Π³ΠΎ ΠΊΠΎΠ»Π΅ΡΠ°; 11 β ΡΠ΅Π³ΡΠ»ΠΈΡΠΎΠ²ΠΎΡΠ½ΡΠΉ Π½Π°ΠΊΠΎΠ½Π΅ΡΠ½ΠΈΠΊ ΡΡΠΎΡΠ½ΠΎΡΠ½ΠΎΠ³ΠΎ ΡΠΎΡΠΌΠΎΠ·Π°; 12 β ΡΡΡΠ°Π³ ΠΏΡΠΈΠ²ΠΎΠ΄Π° ΡΡΠΎΡΠ½ΠΎΡΠ½ΠΎΠ³ΠΎ ΡΠΎΡΠΌΠΎΠ·Π°; 13 β ΡΠΎΡΠΌΠΎΠ·Π½ΠΎΠΉ ΠΌΠ΅Ρ
Π°Π½ΠΈΠ·ΠΌ ΠΏΠ΅ΡΠ΅Π΄Π½Π΅Π³ΠΎ ΠΊΠΎΠ»Π΅ΡΠ°.
Π’ΠΎΡΠΌΠΎΠ·Π½ΠΎΠΉ ΠΌΠ΅Ρ Π°Π½ΠΈΠ·ΠΌ Π±Π»ΠΎΠΊΠΈΡΡΠ΅Ρ Π²ΡΠ°ΡΠ΅Π½ΠΈΠ΅ ΠΊΠΎΠ»Π΅Ρ ΠΈ ΠΊΠ°ΠΊ ΡΠ΅Π·ΡΠ»ΡΡΠ°Ρ ΠΏΠΎΡΠ²Π»Π΅Π½ΠΈΠ΅ ΡΠΎΡΠΌΠΎΠ·Π½ΠΎΠΉ ΡΠΈΠ»Ρ, ΠΊΠΎΡΠΎΡΠ°Ρ ΠΎΡΡΠ°Π½Π°Π²Π»ΠΈΠ²Π°Π΅Ρ ΡΡΠ°Π½ΡΠΏΠΎΡΡΠ½ΠΎΠ΅ ΡΡΠ΅Π΄ΡΡΠ²ΠΎ. Π’ΠΎΡΠΌΠΎΠ·Π½ΡΠ΅ ΠΌΠ΅Ρ Π°Π½ΠΈΠ·ΠΌΡ Π½Π°Ρ ΠΎΠ΄ΡΡΡΡ Π½Π° Π·Π°Π΄Π½ΠΈΡ ΠΈ ΠΏΠ΅ΡΠ΅Π΄Π½ΠΈΡ ΠΊΠΎΠ»Π΅ΡΠ°Ρ .
ΠΠΎ ΠΈΠ΄Π΅Π΅ β Π²ΡΠ΅ ΡΠΎΡΠΌΠΎΠ·Π½ΡΠ΅ ΠΌΠ΅Ρ Π°Π½ΠΈΠ·ΠΌΡ Π»ΠΎΠ³ΠΈΡΠ½ΠΎ Π½Π°Π·ΡΠ²Π°ΡΡ ΠΊΠΎΠ»ΠΎΠ΄ΠΎΡΠ½ΡΠΌΠΈ. Π ΡΠΆΠ΅ Π² ΡΠ²ΠΎΡ ΠΎΡΠ΅ΡΠ΅Π΄Ρ, ΠΈΡ ΠΌΠΎΠΆΠ½ΠΎ ΡΠ°Π·Π΄Π΅Π»ΠΈΡΡ ΠΏΠΎ ΡΡΠ΅Π½ΠΈΡ β Π΄ΠΈΡΠΊΠΎΠ²ΡΠ΅ ΠΈ Π±Π°ΡΠ°Π±Π°Π½Π½ΡΠ΅. Π’ΠΎΡΠΌΠΎΠ·Π½ΡΠ΅ ΠΌΠ΅Ρ Π°Π½ΠΈΠ·ΠΌΡ ΠΎΡΠ½ΠΎΠ²Π½ΠΎΠΉ ΡΠΈΡΡΠ΅ΠΌΡ ΠΌΠΎΠ½ΡΠΈΡΡΡΡΡΡ Π² ΠΊΠΎΠ»Π΅ΡΠ΅, Π° ΠΌΠ΅Ρ Π°Π½ΠΈΠ·ΠΌ ΡΡΠΎΡΠ½ΠΎΡΠ½ΠΎΠΉ ΡΠΈΡΡΠ΅ΠΌΡ Π½Π°Ρ ΠΎΠ΄ΠΈΡΡΡ Π·Π° ΡΠ°Π·Π΄Π°ΡΠΎΡΠ½ΠΎΠΉ ΠΊΠΎΡΠΎΠ±ΠΊΠΎΠΉ ΠΈΠ»ΠΈ ΠΊΠΎΡΠΎΠ±ΠΊΠΎΠΉ ΠΏΠ΅ΡΠ΅Π΄Π°Ρ.
Π Π±Π°ΡΠ°Π±Π°Π½Π½ΡΡ ΠΈ Π΄ΠΈΡΠΊΠΎΠ²ΡΡ ΡΠΎΡΠΌΠΎΠ·Π½ΡΡ ΠΌΠ΅Ρ Π°Π½ΠΈΠ·ΠΌΠ°Ρ
Π’ΠΎΡΠΌΠΎΠ·Π½ΠΎΠΉ ΠΌΠ΅Ρ Π°Π½ΠΈΠ·ΠΌ ΠΎΠ±ΡΡΠ½ΠΎ ΡΠΎΡΡΠΎΠΈΡ ΠΈΠ· Π΄Π²ΡΡ ΡΠ°ΡΡΠ΅ΠΉ, ΠΈΠ· Π²ΡΠ°ΡΠ°ΡΡΠ΅ΠΉΡΡ ΠΈ Π½Π΅ΠΏΠΎΠ΄Π²ΠΈΠΆΠ½ΠΎΠΉ. ΠΡΠ°ΡΠ°ΡΡΠ°ΡΡΡ ΡΠ°ΡΡΡ Π±Π°ΡΠ°Π±Π°Π½Π½ΠΎΠ³ΠΎ ΠΌΠ΅Ρ Π°Π½ΠΈΠ·ΠΌΠ° β ΡΡΠΎ ΡΠΎΡΠΌΠΎΠ·Π½ΠΎΠΉ Π±Π°ΡΠ°Π±Π°Π½, Π° Π½Π΅ΠΏΠΎΠ΄Π²ΠΈΠΆΠ½Π°Ρ ΡΠ°ΡΡΡ β ΡΠΎΡΠΌΠΎΠ·Π½ΡΠ΅ ΠΊΠΎΠ»ΠΎΠ΄ΠΊΠΈ.
ΠΠ°ΡΠ°Π±Π°Π½Π½ΡΠ΅ ΡΠΎΡΠΌΠΎΠ·Π½ΡΠ΅ ΠΌΠ΅Ρ Π°Π½ΠΈΠ·ΠΌΡ ΠΎΠ±ΡΡΠ½ΠΎ ΡΡΠΎΡΡ Π½Π° Π·Π°Π΄Π½ΠΈΡ ΠΊΠΎΠ»Π΅ΡΠ°Ρ . Π ΠΏΡΠΎΡΠ΅ΡΡΠ΅ ΠΈΠ·Π½ΠΎΡΠ° Π·Π°Π·ΠΎΡ ΠΌΠ΅ΠΆΠ΄Ρ Π±Π°ΡΠ°Π±Π°Π½ΠΎΠΌ ΠΈ ΠΊΠΎΠ»ΠΎΠ΄ΠΊΠΎΠΉ ΡΠ²Π΅Π»ΠΈΡΠΈΠ²Π°Π΅ΡΡΡ ΠΈ Π΄Π»Ρ Π΅Π³ΠΎ ΡΡΡΡΠ°Π½Π΅Π½ΠΈΡ Π΅ΡΡΡ ΠΌΠ΅Ρ Π°Π½ΠΈΡΠ΅ΡΠΊΠΈΠ΅ ΡΠ΅Π³ΡΠ»ΡΡΠΎΡΡ.
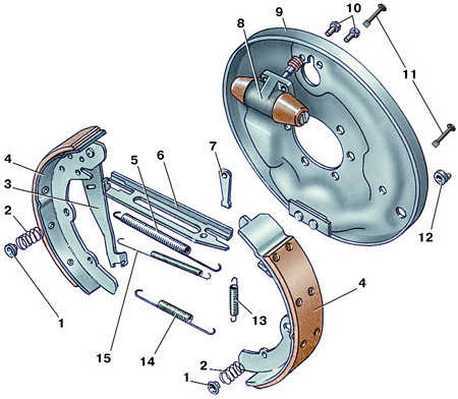
ΠΠ°ΡΠ°Π±Π°Π½Π½ΡΠΉ ΡΠΎΡΠΌΠΎΠ·Π½ΠΎΠΉ ΠΌΠ΅Ρ
Π°Π½ΠΈΠ·ΠΌ Π·Π°Π΄Π½Π΅Π³ΠΎ ΠΊΠΎΠ»Π΅ΡΠ°:
1 β ΡΠ°ΡΠΊΠ°; 2 β ΠΏΡΠΈΠΆΠΈΠΌΠ½Π°Ρ ΠΏΡΡΠΆΠΈΠ½Π°; 3 β ΠΏΡΠΈΠ²ΠΎΠ΄Π½ΠΎΠΉ ΡΡΡΠ°Π³; 4 β ΡΠΎΡΠΌΠΎΠ·Π½Π°Ρ ΠΊΠΎΠ»ΠΎΠ΄ΠΊΠ°; 5 β Π²Π΅ΡΡ
Π½ΡΡ ΡΡΡΠΆΠ½Π°Ρ ΠΏΡΡΠΆΠΈΠ½Π°; 6 β ΡΠ°ΡΠΏΠΎΡΠ½Π°Ρ ΠΏΠ»Π°Π½ΠΊΠ°; 7 β ΡΠ΅Π³ΡΠ»ΠΈΡΠΎΠ²ΠΎΡΠ½ΡΠΉ ΠΊΠ»ΠΈΠ½; 8 β ΠΊΠΎΠ»Π΅ΡΠ½ΡΠΉ ΡΠΎΡΠΌΠΎΠ·Π½ΠΎΠΉ ΡΠΈΠ»ΠΈΠ½Π΄Ρ; 9 β ΡΠΎΡΠΌΠΎΠ·Π½ΠΎΠΉ ΡΠΈΡ; 10 β Π±ΠΎΠ»Ρ; 11 β ΡΡΠ΅ΡΠΆΠ΅Π½Ρ; 12 β ΡΠΊΡΡΠ΅Π½ΡΡΠΈΠΊ; 13 β Π½Π°ΠΆΠΈΠΌΠ½Π°Ρ ΠΏΡΡΠΆΠΈΠ½Π°; 14 β Π½ΠΈΠΆΠ½ΡΡ ΡΡΡΠΆΠ½Π°Ρ ΠΏΡΡΠΆΠΈΠ½Π°; 15 β ΠΏΡΠΈΠΆΠΈΠΌΠ½Π°Ρ ΠΏΡΡΠΆΠΈΠ½Π° ΡΠ°ΡΠΏΠΎΡΠ½ΠΎΠΉ ΠΏΠ»Π°Π½ΠΊΠΈ.
ΠΠ° Π°Π²ΡΠΎΠΌΠΎΠ±ΠΈΠ»ΡΡ ΡΠΎΡΠΌΠΎΠ·Π½ΡΠ΅ ΠΌΠ΅Ρ Π°Π½ΠΈΠ·ΠΌΡ ΠΌΠΎΠ³ΡΡ ΠΈΠΌΠ΅ΡΡ ΡΠ°Π·Π½ΡΠ΅ ΡΠΎΡΠ΅ΡΠ°Π½ΠΈΡ:
- Π΄Π²Π° Π΄ΠΈΡΠΊΠΎΠ²ΡΡ ΠΏΠ΅ΡΠ΅Π΄Π½ΠΈΡ , Π΄Π²Π° Π±Π°ΡΠ°Π±Π°Π½Π½ΡΡ Π·Π°Π΄Π½ΠΈΡ ;
- ΡΠ΅ΡΡΡΠ΅ Π΄ΠΈΡΠΊΠΎΠ²ΡΡ ;
- ΡΠ΅ΡΡΡΠ΅ Π±Π°ΡΠ°Π±Π°Π½Π½ΡΡ .
Π ΡΠΎΡΠΌΠΎΠ·Π½ΠΎΠΌ Π΄ΠΈΡΠΊΠΎΠ²ΠΎΠΌ ΠΌΠ΅Ρ Π°Π½ΠΈΠ·ΠΌΠ΅ β Π΄ΠΈΡΠΊ Π²ΡΠ°ΡΠ°Π΅ΡΡΡ, Π° Π΄Π²Π΅ ΠΊΠΎΠ»ΠΎΠ΄ΠΊΠΈ ΡΡΠΎΡΡ Π½Π΅ΠΏΠΎΠ΄Π²ΠΈΠΆΠ½ΠΎ, ΠΎΠ½ΠΈ ΡΡΡΠ°Π½ΠΎΠ²Π»Π΅Π½Ρ Π²Π½ΡΡΡΠΈ ΡΡΠΏΠΏΠΎΡΡΠ°. Π ΡΡΠΏΠΏΠΎΡΡΠ΅ ΡΡΠΎΡΡ ΡΠ°Π±ΠΎΡΠΈΠ΅ ΡΠΈΠ»ΠΈΠ½Π΄ΡΡ, ΠΎΠ½ΠΈ ΠΏΡΠΈ ΡΠΎΡΠΌΠΎΠΆΠ΅Π½ΠΈΠΈ ΠΏΡΠΈΠΆΠΈΠΌΠ°ΡΡ ΠΊ Π΄ΠΈΡΠΊΡ ΡΠΎΡΠΌΠΎΠ·Π½ΡΠ΅ ΠΊΠΎΠ»ΠΎΠ΄ΠΊΠΈ, Π° ΡΠ°ΠΌ ΡΡΠΏΠΏΠΎΡΡ Ρ ΠΎΡΠΎΡΠΎ Π·Π°ΠΊΡΠ΅ΠΏΠ»Π΅Π½ Π½Π° ΠΊΡΠΎΠ½ΡΡΠ΅ΠΉΠ½Π΅. ΠΠ»Ρ ΡΠ»ΡΡΡΠ΅Π½ΠΈΡ ΠΎΡΠ²ΠΎΠ΄Π° ΡΠ΅ΠΏΠ»Π° ΠΈΠ· ΡΠ°Π±ΠΎΡΠ΅ΠΉ Π·ΠΎΠ½Ρ ΡΠ°ΡΡΠΎ ΠΏΡΠΈΠΌΠ΅Π½ΡΡΡ Π²Π΅Π½ΡΠΈΠ»ΠΈΡΡΠ΅ΠΌΡΠ΅ Π΄ΠΈΡΠΊΠΈ.
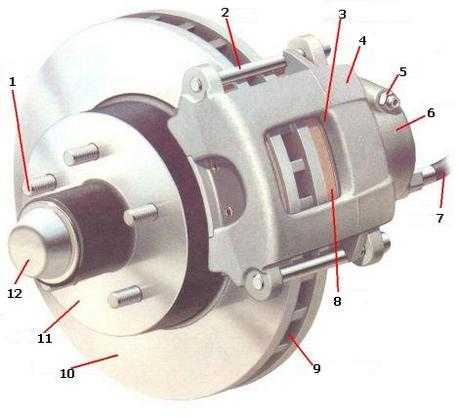
Π‘Ρ
Π΅ΠΌΠ° Π΄ΠΈΡΠΊΠΎΠ²ΠΎΠ³ΠΎ ΡΠΎΡΠΌΠΎΠ·Π½ΠΎΠ³ΠΎ ΠΌΠ΅Ρ
Π°Π½ΠΈΠ·ΠΌΠ°:
1 β ΠΊΠΎΠ»Π΅ΡΠ½Π°Ρ ΡΠΏΠΈΠ»ΡΠΊΠ°; 2 β Π½Π°ΠΏΡΠ°Π²Π»ΡΡΡΠΈΠΉ ΠΏΠ°Π»Π΅Ρ; 3 β ΡΠΌΠΎΡΡΠΎΠ²ΠΎΠ΅ ΠΎΡΠ²Π΅ΡΡΡΠΈΠ΅; 4 β ΡΡΠΏΠΏΠΎΡΡ; 5 β ΠΊΠ»Π°ΠΏΠ°Π½; 6 β ΡΠ°Π±ΠΎΡΠΈΠΉ ΡΠΈΠ»ΠΈΠ½Π΄Ρ; 7 β ΡΠΎΡΠΌΠΎΠ·Π½ΠΎΠΉ ΡΠ»Π°Π½Π³; 8 β ΡΠΎΡΠΌΠΎΠ·Π½Π°Ρ ΠΊΠΎΠ»ΠΎΠ΄ΠΊΠ°; 9 β Π²Π΅Π½ΡΠΈΠ»ΡΡΠΈΠΎΠ½Π½ΠΎΠ΅ ΠΎΡΠ²Π΅ΡΡΡΠΈΠ΅; 10 β ΡΠΎΡΠΌΠΎΠ·Π½ΠΎΠΉ Π΄ΠΈΡΠΊ; 11 β ΡΡΡΠΏΠΈΡΠ° ΠΊΠΎΠ»Π΅ΡΠ°; 12 β Π³ΡΡΠ·Π΅Π·Π°ΡΠΈΡΠ½ΡΠΉ ΠΊΠΎΠ»ΠΏΠ°ΡΠΎΠΊ.
Π ΡΠΎΡΠΌΠΎΠ·Π½ΡΡ ΠΏΡΠΈΠ²ΠΎΠ΄Π°Ρ
Π Π°Π²ΡΠΎΠΌΠΎΠ±ΠΈΠ»ΡΠ½ΡΡ ΡΠΎΡΠΌΠΎΠ·Π½ΡΡ ΡΠΈΡΡΠ΅ΠΌΠ°Ρ Π½Π°ΡΠ»ΠΈ ΠΏΡΠΈΠΌΠ΅Π½Π΅Π½ΠΈΠ΅ Π²ΠΎΡ ΡΡΠΈ ΡΠΈΠΏΡ ΡΠΎΡΠΌΠΎΠ·Π½ΡΡ ΠΏΡΠΈΠ²ΠΎΠ΄ΠΎΠ²:
- Π³ΠΈΠ΄ΡΠ°Π²Π»ΠΈΡΠ΅ΡΠΊΠΈΠΉ;
- ΠΏΠ½Π΅Π²ΠΌΠ°ΡΠΈΡΠ΅ΡΠΊΠΈΠΉ;
- ΠΊΠΎΠΌΠ±ΠΈΠ½ΠΈΡΠΎΠ²Π°Π½Π½ΡΠΉ.
- ΠΌΠ΅Ρ Π°Π½ΠΈΡΠ΅ΡΠΊΠΈΠΉ;
ΠΠΈΠ΄ΡΠ°Π²Π»ΠΈΡΠ΅ΡΠΊΠΈΠΉ ΠΏΡΠΈΠ²ΠΎΠ΄ ΠΏΠΎΠ»ΡΡΠΈΠ» ΡΠ°ΠΌΠΎΠ΅ ΡΠΈΡΠΎΠΊΠΎΠ΅ ΡΠ°ΡΠΏΡΠΎΡΡΡΠ°Π½Π΅Π½ΠΈΠ΅ Π² ΡΠ°Π±ΠΎΡΠ΅ΠΉ ΡΠΎΡΠΌΠΎΠ·Π½ΠΎΠΉ ΡΠΈΡΡΠ΅ΠΌΠ΅ Π°Π²ΡΠΎΠΌΠΎΠ±ΠΈΠ»Ρ. Π Π½Π΅Π³ΠΎ Π²Ρ ΠΎΠ΄ΡΡ:
- Π³Π»Π°Π²Π½ΡΠΉ ΡΠΎΡΠΌΠΎΠ·Π½ΠΎΠΉ ΡΠΈΠ»ΠΈΠ½Π΄Ρ;
- ΡΠΎΡΠΌΠΎΠ·Π½Π°Ρ ΠΏΠ΅Π΄Π°Π»Ρ;
- ΠΊΠΎΠ»Π΅ΡΠ½ΡΠ΅ ΡΠΈΠ»ΠΈΠ½Π΄ΡΡ;
- ΡΡΠΈΠ»ΠΈΡΠ΅Π»Ρ ΡΠΎΡΠΌΠΎΠ·ΠΎΠ²
- ΡΠ»Π°Π½Π³ΠΈ ΠΈ ΡΡΡΠ±ΠΎΠΏΡΠΎΠ²ΠΎΠ΄Ρ (ΡΠ°Π±ΠΎΡΠΈΠ΅ ΠΊΠΎΠ½ΡΡΡΠ°).
ΠΡΠΈ ΡΡΠΈΠ»ΠΈΠΈ Π½Π° ΡΠΎΡΠΌΠΎΠ·Π½ΡΡ ΠΏΠ΅Π΄Π°Π»Ρ Π²ΠΎΠ΄ΠΈΡΠ΅Π»Π΅ΠΌ, ΡΠ° ΠΏΠ΅ΡΠ΅Π΄Π°Π΅Ρ ΡΡΠΈΠ»ΠΈΠ΅ ΠΎΡ Π½ΠΎΠ³ΠΈ Π½Π° Π³Π»Π°Π²Π½ΡΠΉ ΡΠΎΡΠΌΠΎΠ·Π½ΠΎΠΉ ΡΠΈΠ»ΠΈΠ½Π΄Ρ. Π£ΡΠΈΠ»ΠΈΡΠ΅Π»Ρ ΡΠΎΡΠΌΠΎΠ·ΠΎΠ² Π΄ΠΎΠΏΠΎΠ»Π½ΠΈΡΠ΅Π»ΡΠ½ΠΎ ΡΠΎΠ·Π΄Π°Π΅Ρ ΡΡΠΈΠ»ΠΈΠ΅, ΠΎΠ±Π»Π΅Π³ΡΠ°Ρ ΡΠ΅ΠΌ ΡΠ°ΠΌΡΠΌ ΠΆΠΈΠ·Π½Ρ Π²ΠΎΠ΄ΠΈΡΠ΅Π»Ρ. Π¨ΠΈΡΠΎΠΊΠΎΠ΅ ΠΏΡΠΈΠΌΠ΅Π½Π΅Π½ΠΈΠ΅ Π½Π° ΠΌΠ°ΡΠΈΠ½Π°Ρ ΠΏΡΠΈΠΎΠ±ΡΠ΅Π» Π²Π°ΠΊΡΡΠΌΠ½ΡΠΉ ΡΡΠΈΠ»ΠΈΡΠ΅Π»Ρ ΡΠΎΡΠΌΠΎΠ·ΠΎΠ².
ΠΠ»Π°Π²Π½ΡΠΉ ΡΠΎΡΠΌΠΎΠ·Π½ΠΎΠΉ ΡΠΈΠ»ΠΈΠ½Π΄Ρ Π½Π°Π³Π½Π΅ΡΠ°Π΅Ρ ΡΠΎΡΠΌΠΎΠ·Π½ΡΡ ΠΆΠΈΠ΄ΠΊΠΎΡΡΡ ΠΊ ΡΠΎΡΠΌΠΎΠ·Π½ΡΠΌ ΡΠΈΠ»ΠΈΠ½Π΄ΡΠ°ΠΌ. ΠΠ±ΡΡΠ½ΠΎ Π½Π°Π΄ Π³Π»Π°Π²Π½ΡΠΌ ΡΠΈΠ»ΠΈΠ½Π΄ΡΠΎΠΌ ΡΡΠΎΠΈΡ ΡΠ°ΡΡΠΈΡΠΈΡΠ΅Π»ΡΠ½ΡΠΉ Π±Π°ΡΠΎΠΊ, Π² Π½Π΅ΠΌ ΡΠΎΠ΄Π΅ΡΠΆΠΈΡΡΡ ΡΠΎΡΠΌΠΎΠ·Π½Π°Ρ ΠΆΠΈΠ΄ΠΊΠΎΡΡΡ.
ΠΠΎΠ»Π΅ΡΠ½ΡΠΉ ΡΠΈΠ»ΠΈΠ½Π΄Ρ ΠΏΡΠΈΠΆΠΈΠΌΠ°Π΅Ρ ΡΠΎΡΠΌΠΎΠ·Π½ΡΠ΅ ΠΊΠΎΠ»ΠΎΠ΄ΠΊΠΈ ΠΊ ΡΠΎΡΠΌΠΎΠ·Π½ΠΎΠΌΡ Π±Π°ΡΠ°Π±Π°Π½Ρ ΠΈΠ»ΠΈ Π΄ΠΈΡΠΊΡ.
Π Π°Π±ΠΎΡΠΈΠΉ ΠΊΠΎΠ½ΡΡΡ ΡΠ΅ΠΉΡΠ°Ρ ΠΏΡΠ΅Π΄ΡΡΠ°Π²Π»ΡΠ΅Ρ ΠΈΠ· ΡΠ΅Π±Ρ ΠΎΡΠ½ΠΎΠ²Π½ΠΎΠΉ ΠΈ Π²ΡΠΏΠΎΠΌΠΎΠ³Π°ΡΠ΅Π»ΡΠ½ΡΠΉ. ΠΠ°ΠΏΡΠΈΠΌΠ΅Ρ, Π²ΡΡ ΡΠΈΡΡΠ΅ΠΌΠ° ΠΈΡΠΏΡΠ°Π²Π½Π°, ΡΠΎ Π·Π½Π°ΡΠΈΡ ΡΠ°Π±ΠΎΡΠ°ΡΡ ΠΎΠ±Π°, Π½ΠΎ ΠΏΡΠΈ Π½Π΅ΠΈΡΠΏΡΠ°Π²Π½ΠΎΡΡΠΈ ΠΎΠ΄Π½ΠΎΠ³ΠΎ ΠΈΠ· Π½ΠΈΡ β Π΄ΡΡΠ³ΠΎΠΉ Π±ΡΠ΄Π΅Ρ ΡΠ°Π±ΠΎΡΠ°ΡΡ.
Π¨ΠΈΡΠΎΠΊΠΎ ΡΠ°ΡΠΏΡΠΎΡΡΡΠ°Π½Π΅Π½Ρ ΡΡΠΈ ΠΎΡΠ½ΠΎΠ²Π½ΡΠ΅ ΠΊΠΎΠΌΠΏΠΎΠ½ΠΎΠ²ΠΊΠΈ ΡΠ°Π·Π΄Π΅Π»Π΅Π½ΠΈΡ ΡΠ°Π±ΠΎΡΠΈΡ ΠΊΠΎΠ½ΡΡΡΠΎΠ²:
- 2 + 2 ΠΏΠΎΠ΄ΠΊΠ»ΡΡΠ΅Π½Π½ΡΡ ΠΏΠ°ΡΠ°Π»Π»Π΅Π»ΡΠ½ΠΎ β Π·Π°Π΄Π½ΠΈΠ΅ + ΠΏΠ΅ΡΠ΅Π΄Π½ΠΈΠ΅;
- 2 + 2 ΠΏΠΎΠ΄ΠΊΠ»ΡΡΠ΅Π½Π½ΡΡ Π΄ΠΈΠ°Π³ΠΎΠ½Π°Π»ΡΠ½ΠΎ β ΠΏΡΠ°Π²ΡΠΉ ΠΏΠ΅ΡΠ΅Π΄Π½ΠΈΠΉ + Π»Π΅Π²ΡΠΉ Π·Π°Π΄Π½ΠΈΠΉ ΠΈ ΡΠ°ΠΊ Π΄Π°Π»Π΅Π΅;
- 4 + 2 Π² ΠΎΠ΄ΠΈΠ½ ΠΊΠΎΠ½ΡΡΡ ΠΏΠΎΠ΄ΠΊΠ»ΡΡΠ΅Π½Ρ Π΄Π²Π° ΠΏΠ΅ΡΠ΅Π΄Π½ΠΈΡ , Π° Π² Π΄ΡΡΠ³ΠΎΠΉ ΡΠΎΡΠΌΠΎΠ·Π½ΡΠ΅ ΠΌΠ΅Ρ Π°Π½ΠΈΠ·ΠΌΡ Π²ΡΠ΅Ρ ΠΊΠΎΠ»Π΅Ρ.
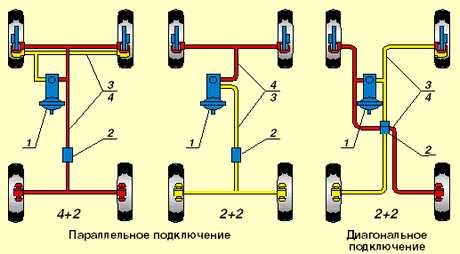
Π‘Ρ
Π΅ΠΌΠ° ΠΊΠΎΠΌΠΏΠΎΠ½ΠΎΠ²ΠΊΠΈ Π³ΠΈΠ΄ΡΠΎΠΏΡΠΈΠ²ΠΎΠ΄Π°:
1 β Π³Π»Π°Π²Π½ΡΠΉ ΡΠΎΡΠΌΠΎΠ·Π½ΠΎΠΉ ΡΠΈΠ»ΠΈΠ½Π΄Ρ Ρ Π²Π°ΠΊΡΡΠΌΠ½ΡΠΌ ΡΡΠΈΠ»ΠΈΡΠ΅Π»Π΅ΠΌ; 2 β ΡΠ΅Π³ΡΠ»ΡΡΠΎΡ Π΄Π°Π²Π»Π΅Π½ΠΈΡ ΠΆΠΈΠ΄ΠΊΠΎΡΡΠΈ Π² Π·Π°Π΄Π½ΠΈΡ
ΡΠΎΡΠΌΠΎΠ·Π½ΡΡ
ΠΌΠ΅Ρ
Π°Π½ΠΈΠ·ΠΌΠ°Ρ
; 3-4 β ΡΠ°Π±ΠΎΡΠΈΠ΅ ΠΊΠΎΠ½ΡΡΡΡ.
ΠΡΠΎΠ³ΡΠ΅ΡΡ Π½Π΅ ΡΡΠΎΠΈΡ Π½Π° ΠΌΠ΅ΡΡΠ΅ ΠΈ ΡΠ΅ΠΉΡΠ°Ρ Π² ΡΠΎΡΡΠ°Π² Π³ΠΈΠ΄ΡΠ°Π²Π»ΠΈΡΠ΅ΡΠΊΠΎΠ³ΠΎ ΡΠΎΡΠΌΠΎΠ·Π½ΠΎΠ³ΠΎ ΠΏΡΠΈΠ²ΠΎΠ΄Π° Π΄ΠΎΠ±Π°Π²Π»ΡΡΡΡΡ ΡΠ°Π·Π½ΡΠ΅ ΡΠ»Π΅ΠΊΡΡΠΎΠ½Π½ΡΠ΅ ΠΊΠΎΠΌΠΏΠΎΠ½Π΅Π½ΡΡ:
- ΡΡΠΈΠ»ΠΈΡΠ΅Π»Ρ ΡΠΊΡΡΡΠ΅Π½Π½ΠΎΠ³ΠΎ ΡΠΎΡΠΌΠΎΠΆΠ΅Π½ΠΈΡ
- Π°Π½ΡΠΈΠ±Π»ΠΎΠΊΠΈΡΠΎΠ²ΠΎΡΠ½Π°Ρ ΡΠΈΡΡΠ΅ΠΌΠ° ΡΠΎΡΠΌΠΎΠ·ΠΎΠ²;
- Π°Π½ΡΠΈΠΏΡΠΎΠ±ΡΠΊΡΠΎΠ²ΠΎΡΠ½Π°Ρ ΡΠΈΡΡΠ΅ΠΌΠ°;
- ΡΠΈΡΡΠ΅ΠΌΠ° ΡΠ°ΡΠΏΡΠ΅Π΄Π΅Π»Π΅Π½ΠΈΡ ΡΠΎΡΠΌΠΎΠ·Π½ΡΡ ΡΡΠΈΠ»ΠΈΠΉ;
- ΡΠ»Π΅ΠΊΡΡΠΎΠ½Π½Π°Ρ Π±Π»ΠΎΠΊΠΈΡΠΎΠ²ΠΊΠ° Π΄ΠΈΡΡΠ΅ΡΠ΅Π½ΡΠΈΠ°Π»Π°.
ΠΠ½Π΅Π²ΠΌΠ°ΡΠΈΡΠ΅ΡΠΊΠΈΠΉ ΠΏΡΠΈΠ²ΠΎΠ΄ ΠΏΡΠΈΠΌΠ΅Π½ΡΠ΅ΡΡΡ Π² ΡΠΎΡΠΌΠΎΠ·Π½ΠΎΠΉ ΡΠΈΡΡΠ΅ΠΌΠ΅ Π±ΠΎΠ»ΡΡΠ΅Π³ΡΡΠ·Π½ΡΡ Π°Π²ΡΠΎΠΌΠΎΠ±ΠΈΠ»Π΅ΠΉ.
ΠΠΎΠΌΠ±ΠΈΠ½ΠΈΡΠΎΠ²Π°Π½Π½ΡΠΉ ΡΠΎΡΠΌΠΎΠ·Π½ΠΎΠΉ ΠΏΡΠΈΠ²ΠΎΠ΄ β ΡΡΠΎ ΠΊΠΎΠΌΠ±ΠΈΠ½Π°ΡΠΈΡ ΡΠ°Π·Π½ΡΡ ΡΠΈΠΏΠΎΠ² ΠΏΡΠΈΠ²ΠΎΠ΄Π°.
ΠΠ΅Ρ Π°Π½ΠΈΡΠ΅ΡΠΊΠΈΠΉ ΠΏΡΠΈΠ²ΠΎΠ΄ ΠΏΡΠΈΠΌΠ΅Π½ΡΠ΅ΡΡΡ Π² ΡΡΠΎΡΠ½ΠΎΡΠ½ΠΎΠΉ ΡΠΎΡΠΌΠΎΠ·Π½ΠΎΠΉ ΡΠΈΡΡΠ΅ΠΌΠ΅. ΠΠ½ Π²ΠΊΠ»ΡΡΠ°Π΅Ρ Π² ΡΠ΅Π±Ρ ΡΠΈΡΡΠ΅ΠΌΡ ΡΡΠ³ ΠΈ ΡΡΠΎΡΠΎΠ², Ρ ΠΏΠΎΠΌΠΎΡΡΡ ΠΊΠΎΡΠΎΡΡΡ ΠΎΠ±ΡΠ΅Π΄ΠΈΠ½ΡΠ΅Ρ ΡΠΈΡΡΠ΅ΠΌΡ Π² ΠΎΠ΄Π½ΠΎ ΡΠ΅Π»ΠΎΠ΅, ΠΎΠ±ΡΡΠ½ΠΎ Π½Π° Π·Π°Π΄Π½ΠΈΠ΅ ΠΊΠΎΠ»Π΅ΡΠ° ΠΈΠΌΠ΅Π΅Ρ ΠΏΡΠΈΠ²ΠΎΠ΄. Π ΡΡΠ°Π³ ΡΠΎΡΠΌΠΎΠ·Π° ΡΠΎΠ΅Π΄ΠΈΠ½Π΅Π½ ΠΏΡΠΈ ΠΏΠΎΠΌΠΎΡΠΈ ΡΠΎΠ½ΠΊΠΎΠ³ΠΎ ΡΡΠΎΡΠ° Ρ ΡΠΎΡΠΌΠΎΠ·Π½ΡΠΌΠΈ ΠΌΠ΅Ρ Π°Π½ΠΈΠ·ΠΌΠ°ΠΌΠΈ, Π³Π΄Π΅ Π΅ΡΡΡ ΡΡΡΡΠΎΠΉΡΡΠ²ΠΎ, ΠΊΠΎΡΠΎΡΠΎΠ΅ ΠΏΡΠΈΠ²ΠΎΠ΄ΠΈΡ Π² Π΄Π΅ΠΉΡΡΠ²ΠΈΠ΅ ΠΎΡΠ½ΠΎΠ²Π½ΡΠ΅ ΠΈΠ»ΠΈ ΡΡΠΎΡΠ½ΠΎΡΠ½ΡΠ΅ ΠΊΠΎΠ»ΠΎΠ΄ΠΊΠΈ.
ΠΡΡΡ Π°Π²ΡΠΎΠΌΠΎΠ±ΠΈΠ»ΠΈ, Π³Π΄Π΅ ΡΡΠΎΡΠ½ΠΎΡΠ½Π°Ρ ΡΠΈΡΡΠ΅ΠΌΠ° ΡΠ°Π±ΠΎΡΠ°Π΅Ρ ΠΎΡ Π½ΠΎΠΆΠ½ΠΎΠΉ ΠΏΠ΅Π΄Π°Π»ΠΈ. Π‘Π΅ΠΉΡΠ°Ρ Π²ΡΡ ΡΠ°ΡΠ΅ ΡΡΠ°Π»ΠΈ ΠΏΡΠΈΠΌΠ΅Π½ΡΡΡ Π² ΡΡΠΎΡΠ½ΠΎΡΠ½ΠΎΠΉ ΡΠΈΡΡΠ΅ΠΌΠ΅ ΡΠ»Π΅ΠΊΡΡΠΎΠΏΡΠΈΠ²ΠΎΠ΄, ΠΊΠΎΡΠΎΡΡΠΉ ΠΏΠΎΠ»ΡΡΠΈΠ» Π½Π°Π·Π²Π°Π½ΠΈΠ΅ β ΡΠ»Π΅ΠΊΡΡΠΎΠΌΠ΅Ρ Π°Π½ΠΈΡΠ΅ΡΠΊΠΈΠΉ ΡΡΠΎΡΠ½ΠΎΡΠ½ΡΠΉ ΡΠΎΡΠΌΠΎΠ·.
ΠΡΠ°ΠΊ, ΠΊΠ°ΠΊ ΡΠ°Π±ΠΎΡΠ°Π΅Ρ Π³ΠΈΠ΄ΡΠ°Π²Π»ΠΈΡΠ΅ΡΠΊΠ°Ρ ΡΠΎΡΠΌΠΎΠ·Π½Π°Ρ ΡΠΈΡΡΠ΅ΠΌΠ°
ΠΡΡΠ°Π»ΠΎΡΡ ΡΠ°ΡΡΠΌΠΎΡΡΠ΅ΡΡ ΡΠ°Π±ΠΎΡΡ ΡΠΎΡΠΌΠΎΠ·Π½ΠΎΠΉ ΡΠΈΡΡΠ΅ΠΌΡ, ΡΡΠΎ ΠΌΡ ΡΠ΄Π΅Π»Π°Π΅ΠΌ Π½Π° ΠΏΡΠΈΠΌΠ΅ΡΠ΅ Π³ΠΈΠ΄ΡΠ°Π²Π»ΠΈΡΠ΅ΡΠΊΠΎΠΉ ΡΠΈΡΡΠ΅ΠΌΡ.
ΠΠΎΠ³Π΄Π° Π²ΠΎΠ΄ΠΈΡΠ΅Π»Ρ Π½Π°ΠΆΠΈΠΌΠ°Π΅Ρ Π½Π° ΠΏΠ΅Π΄Π°Π»Ρ ΡΠΎΡΠΌΠΎΠ·Π°, ΡΠΎ ΠΏΠ΅ΡΠ΅Π΄Π°Π΅ΡΡΡ Π½Π°Π³ΡΡΠ·ΠΊΠ° ΠΊ ΡΡΠΈΠ»ΠΈΡΠ΅Π»Ρ ΠΈ ΡΠΎΡ ΡΠΎΠ·Π΄Π°Π΅Ρ ΡΡΠΈΠ»ΠΈΠ΅ Π½Π° Π³Π»Π°Π²Π½ΠΎΠΌ ΡΠΎΡΠΌΠΎΠ·Π½ΠΎΠΌ ΡΠΈΠ»ΠΈΠ½Π΄ΡΠ΅. Π Π² ΡΠ²ΠΎΡ ΠΎΡΠ΅ΡΠ΅Π΄Ρ ΠΏΠΎΡΡΠ΅Π½Ρ Π³Π»Π°Π²Π½ΠΎΠ³ΠΎ ΡΠΎΡΠΌΠΎΠ·Π½ΠΎΠ³ΠΎ ΡΠΈΠ»ΠΈΠ½Π΄ΡΠ° ΡΠ΅ΡΠ΅Π· ΡΡΡΠ±ΠΎΠΏΡΠΎΠ²ΠΎΠ΄Ρ Π½Π°Π³Π½Π΅ΡΠ°Π΅Ρ ΠΆΠΈΠ΄ΠΊΠΎΡΡΡ ΠΊ ΠΊΠΎΠ»Π΅ΡΠ½ΡΠΌ ΡΠΈΠ»ΠΈΠ½Π΄ΡΠ°ΠΌ. ΠΠΎΡΡΠ½ΠΈ ΠΊΠΎΠ»Π΅ΡΠ½ΡΡ ΡΠΈΠ»ΠΈΠ½Π΄ΡΠΎΠ² ΠΎΡ Π΄Π°Π²Π»Π΅Π½ΠΈΡ ΠΆΠΈΠ΄ΠΊΠΎΡΡΠΈ ΠΏΠ΅ΡΠ΅Π΄Π²ΠΈΠ³Π°ΡΡ ΡΠΎΡΠΌΠΎΠ·Π½ΡΠ΅ ΠΊΠΎΠ»ΠΎΠ΄ΠΊΠΈ ΠΊ Π΄ΠΈΡΠΊΠ°ΠΌ ΠΈΠ»ΠΈ Π±Π°ΡΠ°Π±Π°Π½Π°ΠΌ ΠΈ ΠΏΡΠΎΠΈΡΡ ΠΎΠ΄ΠΈΡ ΡΠΎΡΠΌΠΎΠΆΠ΅Π½ΠΈΠ΅ Π°Π²ΡΠΎΠΌΠΎΠ±ΠΈΠ»Ρ.
ΠΠΎΠ³Π΄Π° Π²ΠΎΠ΄ΠΈΡΠ΅Π»Ρ ΡΠ±ΠΈΡΠ°Π΅Ρ Π½ΠΎΠ³Ρ Ρ ΠΏΠ΅Π΄Π°Π»ΠΈ ΡΠΎΡΠΌΠΎΠ·Π°, ΡΠΎ ΠΏΠ΅Π΄Π°Π»Ρ ΠΎΡ Π΄Π΅ΠΉΡΡΠ²ΠΈΡ Π²ΠΎΠ·Π²ΡΠ°ΡΠ½ΠΎΠΉ ΠΏΡΡΠΆΠΈΠ½Ρ Π²ΠΎΠ·Π²ΡΠ°ΡΠ°Π΅ΡΡΡ Π² Π½Π°ΡΠ°Π»ΡΠ½ΠΎΠ΅ ΠΏΠΎΠ»ΠΎΠΆΠ΅Π½ΠΈΠ΅. Π’Π°ΠΊΠΆΠ΅, Π² ΡΠ²ΠΎΠ΅ ΠΏΠΎΠ»ΠΎΠΆΠ΅Π½ΠΈΠ΅ Π²ΠΎΠ·Π²ΡΠ°ΡΠ°Π΅ΡΡΡ ΠΈ ΠΏΠΎΡΡΠ΅Π½Ρ Π³Π»Π°Π²Π½ΠΎΠ³ΠΎ ΡΠΎΡΠΌΠΎΠ·Π½ΠΎΠ³ΠΎ ΡΠΈΠ»ΠΈΠ½Π΄ΡΠ°, Π° ΠΏΡΡΠΆΠΈΠ½Ρ ΠΎΡΠ²ΠΎΠ΄ΡΡ ΠΊΠΎΠ»ΠΎΠ΄ΠΊΠΈ ΠΎΡ Π±Π°ΡΠ°Π±Π°Π½ΠΎΠ² ΠΈΠ»ΠΈ Π΄ΠΈΡΠΊΠΎΠ². Π’ΠΎΡΠΌΠΎΠ·Π½Π°Ρ ΠΆΠΈΠ΄ΠΊΠΎΡΡΡ Π²ΠΎΠ·Π²ΡΠ°ΡΠ°Π΅ΡΡΡ ΠΎΠ±ΡΠ°ΡΠ½ΠΎ Π² Π³Π»Π°Π²Π½ΡΠΉ ΡΠΎΡΠΌΠΎΠ·Π½ΠΎΠΉ ΡΠΈΠ»ΠΈΠ½Π΄Ρ ΠΈ ΠΏΠ°Π΄Π°Π΅Ρ Π΄Π°Π²Π»Π΅Π½ΠΈΠ΅ Π² ΡΠΈΡΡΠ΅ΠΌΠ΅.
ΠΠΈΠ΄Π΅ΠΎ: ΠΏΡΠΈΠ½ΡΠΈΠΏ ΡΠ°Π±ΠΎΡΡ ΡΠΎΡΠΌΠΎΠ·Π½ΠΎΠΉ ΡΠΈΡΡΠ΅ΠΌΡ.
ΠΠΎΡ Π½Π° ΡΡΠΎΠΌ ΠΏΠΎΠΆΠ°Π»ΡΠΉ ΠΈ Π·Π°Π²Π΅ΡΡΡ ΡΠ²ΠΎΡ Π½Π΅ ΠΌΠ°Π»Π΅Π½ΡΠΊΡΡ ΡΡΠ°ΡΡΡ. ΠΡΠ΅ΠΌ ΡΠ΄Π°ΡΠΈ Π½Π° Π΄ΠΎΡΠΎΠ³Π°Ρ !
ΠΠ°Π³ΡΡΠ·ΠΊΠ°…avto-i-avto.ru
ΠΠ»Π°ΡΡΠΈΡΠΈΠΊΠ°ΡΠΈΡ ΡΠΎΡΠΌΠΎΠ·Π½ΡΡ ΠΌΠ΅Ρ Π°Π½ΠΈΠ·ΠΌΠΎΠ²
β ΠΡΠ΅Π΄ΡΠ΄ΡΡΠ°ΡΠ‘ΡΡ 44 ΠΈΠ· 48Π‘Π»Π΅Π΄ΡΡΡΠ°Ρ β
Β
Π‘ΠΎΠ²ΡΠ΅ΠΌΠ΅Π½Π½ΡΠ΅ Π°Π²ΡΠΎΠΌΠΎΠ±ΠΈΠ»ΠΈ ΠΎΠ±ΠΎΡΡΠ΄ΡΡΡΡΡ ΡΠ°Π·Π»ΠΈΡΠ½ΡΠΌΠΈ ΡΠΈΠΏΠ°ΠΌΠΈ ΡΠΎΡΠΌΠΎΠ·Π½ΡΡ ΠΌΠ΅Ρ Π°Π½ΠΈΠ·ΠΌΠΎΠ² (ΡΠΈΡ. 10.1). Π’ΠΎΡΠΌΠΎΠ·Π½ΡΠ΅ ΠΌΠ΅Ρ Π°Π½ΠΈΠ·ΠΌΡ ΠΌΠΎΠ³ΡΡ ΠΎΡΡΡΠ΅ΡΡΠ²Π»ΡΡΡ ΠΏΡΠΈΠ½ΡΠ΄ΠΈΡΠ΅Π»ΡΠ½ΠΎΠ΅ Π·Π°ΠΌΠ΅Π΄Π»Π΅Π½ΠΈΠ΅ Π°Π²ΡΠΎΠΌΠΎΠ±ΠΈΠ»Ρ ΡΠ°Π·Π»ΠΈΡΠ½ΡΠΌΠΈ ΡΠΏΠΎΡΠΎΠ±Π°ΠΌΠΈ: ΠΌΠ΅Ρ Π°Π½ΠΈΡΠ΅ΡΠΊΠΈΠΌ (ΡΡΠΈΠΊΡΠΈΠΎΠ½Π½ΡΠΌ), Π³ΠΈΠ΄ΡΠ°Π²Π»ΠΈΡΠ΅ΡΠΊΠΈΠΌ, ΡΠ»Π΅ΠΊΡΡΠΈΡΠ΅ΡΠΊΠΈΠΌ ΠΈ Π²Π½Π΅ΠΊΠΎΠ»Π΅ΡΠ½ΡΠΌ ΡΠΎΡΠΌΠΎΠΆΠ΅Π½ΠΈΠ΅ΠΌ.
Π ΠΈΡ. 10.1. Π’ΠΈΠΏΡ ΡΠΎΡΠΌΠΎΠ·Π½ΡΡ ΠΌΠ΅Ρ Π°Π½ΠΈΠ·ΠΌΠΎΠ², ΠΊΠ»Π°ΡΡΠΈΡΠΈΡΠΈΡΠΎΠ²Π°Π½Π½ΡΠ΅ ΠΏΠΎ ΡΠ°Π·Π»ΠΈΡΠ½ΡΠΌ ΠΏΡΠΈΠ·Π½Π°ΠΊΠ°ΠΌ
Β
Π€ΡΠΈΠΊΡΠΈΠΎΠ½Π½ΡΠ΅ ΡΠΎΡΠΌΠΎΠ·Π½ΡΠ΅ ΠΌΠ΅Ρ Π°Π½ΠΈΠ·ΠΌΡ (Π΄ΠΈΡΠΊΠΎΠ²ΡΠ΅ ΠΈ Π±Π°ΡΠ°Π±Π°Π½Π½ΡΠ΅) ΠΏΠΎΠ»ΡΡΠΈΠ»ΠΈ Π½Π°ΠΈΠ±ΠΎΠ»Π΅Π΅ ΡΠΈΡΠΎΠΊΠΎΠ΅ ΡΠ°ΡΠΏΡΠΎΡΡΡΠ°Π½Π΅Π½ΠΈΠ΅ Π½Π° Π°Π²ΡΠΎΠΌΠΎΠ±ΠΈΠ»ΡΡ .
ΠΠΈΡΠΊΠΎΠ²ΡΠ΅ ΡΠΎΡΠΌΠΎΠ·Π½ΡΠ΅ ΠΌΠ΅Ρ Π°Π½ΠΈΠ·ΠΌΡ ΠΏΡΠΈΠΌΠ΅Π½ΡΡΡΡΡ Π΄Π»Ρ ΠΏΠ΅ΡΠ΅Π΄Π½ΠΈΡ ΠΈ Π·Π°Π΄Π½ΠΈΡ ΠΊΠΎΠ»Π΅Ρ Π»Π΅Π³ΠΊΠΎΠ²ΡΡ Π°Π²ΡΠΎΠΌΠΎΠ±ΠΈΠ»Π΅ΠΉ Π±ΠΎΠ»ΡΡΠΎΠ³ΠΎ ΠΊΠ»Π°ΡΡΠ° ΠΈ Π΄Π»Ρ ΠΏΠ΅ΡΠ΅Π΄Π½ΠΈΡ ΠΊΠΎΠ»Π΅Ρ Π»Π΅Π³ΠΊΠΎΠ²ΡΡ Π°Π²ΡΠΎΠΌΠΎΠ±ΠΈΠ»Π΅ΠΉ ΠΌΠ°Π»ΠΎΠ³ΠΎ ΠΈ ΡΡΠ΅Π΄Π½Π΅Π³ΠΎ ΠΊΠ»Π°ΡΡΠΎΠ².
ΠΠ°ΡΠ°Π±Π°Π½Π½ΡΠ΅ ΡΠΎΡΠΌΠΎΠ·Π½ΡΠ΅ ΠΌΠ΅Ρ Π°Π½ΠΈΠ·ΠΌΡ ΠΈΡΠΏΠΎΠ»ΡΠ·ΡΡΡ Π½Π° Π³ΡΡΠ·ΠΎΠ²ΡΡ Π°Π²ΡΠΎΠΌΠΎΠ±ΠΈΠ»ΡΡ , Π½Π΅Π·Π°Π²ΠΈΡΠΈΠΌΠΎ ΠΎΡ ΠΈΡ Π³ΡΡΠ·ΠΎΠΏΠΎΠ΄ΡΠ΅ΠΌΠ½ΠΎΡΡΠΈ, Π² ΠΊΠ°ΡΠ΅ΡΡΠ²Π΅ ΠΊΠΎΠ»Π΅ΡΠ½ΡΡ ΠΈ ΡΡΠ°Π½ΡΠΌΠΈΡΡΠΈΠΎΠ½Π½ΡΡ ΠΈ Π½Π° Π»Π΅Π³ΠΊΠΎΠ²ΡΡ Π°Π²ΡΠΎΠΌΠΎΠ±ΠΈΠ»ΡΡ ΠΌΠ°Π»ΠΎΠ³ΠΎ ΠΈ ΡΡΠ΅Π΄Π½Π΅Π³ΠΎ ΠΊΠ»Π°ΡΡΠΎΠ² Π΄Π»Ρ Π·Π°Π΄Π½ΠΈΡ ΠΊΠΎΠ»Π΅Ρ.
Π€ΡΠΈΠΊΡΠΈΠΎΠ½Π½ΡΠΉ ΡΠΎΡΠΌΠΎΠ·Π½ΠΎΠΉ ΠΌΠ΅Ρ Π°Π½ΠΈΠ·ΠΌ Π²ΠΊΠ»ΡΡΠ°Π΅Ρ Π² ΡΠ΅Π±Ρ Π²ΡΠ°ΡΠ°ΡΡΡΡΡΡ ΡΠ°ΡΡΡ (Π±Π°ΡΠ°Π±Π°Π½, Π΄ΠΈΡΠΊ), ΡΠΎΡΠΌΠΎΠ·Π½ΠΎΠΉ ΡΠ»Π΅ΠΌΠ΅Π½Ρ (ΠΊΠΎΠ»ΠΎΠ΄ΠΊΠΈ), ΡΠ°Π·ΠΆΠΈΠΌΠ½ΠΎΠ΅ ΡΡΡΡΠΎΠΉΡΡΠ²ΠΎ (ΠΊΡΠ»Π°ΡΠΊΠΎΠ²ΠΎΠ΅, ΠΏΠΎΡΡΠ½Π΅Π²ΠΎΠ΅), ΡΠ΅Π³ΡΠ»ΠΈΡΠΎΠ²ΠΎΡΠ½ΠΎΠ΅ ΡΡΡΡΠΎΠΉΡΡΠ²ΠΎ (ΡΠΊΡΡΠ΅Π½ΡΡΠΈΠΊΠΈ) ΠΈ ΠΎΡ Π»Π°ΠΆΠ΄Π°ΡΡΠ΅Π΅ ΡΡΡΡΠΎΠΉΡΡΠ²ΠΎ (ΡΠ΅Π±ΡΠ°, ΠΊΠ°Π½Π°Π»Ρ).
Π Π±Π°ΡΠ°Π±Π°Π½Π½ΠΎΠΌ ΡΠΎΡΠΌΠΎΠ·Π½ΠΎΠΌ ΠΌΠ΅Ρ Π°Π½ΠΈΠ·ΠΌΠ΅ (ΡΠΈΡ. 10.2, Π°) ΡΠΎΡΠΌΠΎΠ·Π½ΠΎΠΉ Π±Π°ΡΠ°Π±Π°Π½ 5 ΡΠΎΠ΅Π΄ΠΈΠ½Π΅Π½ Ρ ΠΊΠΎΠ»Π΅ΡΠΎΠΌ Π°Π²ΡΠΎΠΌΠΎΠ±ΠΈΠ»Ρ ΠΈ Π²ΡΠ°ΡΠ°Π΅ΡΡΡ Π²ΠΌΠ΅ΡΡΠ΅ Ρ Π½ΠΈΠΌ.
Π ΠΈΡ. 10.2. Π€ΡΠΈΠΊΡΠΈΠΎΠ½Π½ΡΠ΅ ΡΠΎΡΠΌΠΎΠ·Π½ΡΠ΅ ΠΌΠ΅Ρ Π°Π½ΠΈΠ·ΠΌΡ: Π° β Π±Π°ΡΠ°Π±Π°Π½Π½ΡΠΉ; Π± β Π΄ΠΈΡΠΊΠΎΠ²ΡΠΉ; 1 β ΠΎΡΡ; 2, 6, 8, 9 β ΠΊΠΎΠ»ΠΎΠ΄ΠΊΠΈ; 3, 7 β Π΄ΠΈΡΠΊΠΈ; 4 β ΡΠ°Π·ΠΆΠΈΠΌΠ½ΠΎΠΉ ΠΊΡΠ»Π°ΠΊ; 5 β ΡΠΎΡΠΌΠΎΠ·Π½ΠΎΠΉ Π±Π°ΡΠ°Π±Π°Π½
Π’ΠΎΡΠΌΠΎΠ·Π½ΡΠ΅ ΠΊΠΎΠ»ΠΎΠ΄ΠΊΠΈ 2 ΠΈ 6 Ρ ΡΡΠΈΠΊΡΠΈΠΎΠ½Π½ΡΠΌΠΈ Π½Π°ΠΊΠ»Π°Π΄ΠΊΠ°ΠΌΠΈ ΡΡΡΠ°Π½ΠΎΠ²Π»Π΅Π½Ρ Π½ΠΈΠΆΠ½ΠΈΠΌΠΈ ΠΊΠΎΠ½ΡΠ°ΠΌΠΈ Π½Π° ΠΎΡΠΈ 1, Π·Π°ΠΊΡΠ΅ΠΏΠ»Π΅Π½Π½ΠΎΠΉ Π½Π° Π½Π΅ΠΏΠΎΠ΄Π²ΠΈΠΆΠ½ΠΎΠΌ ΡΠΎΡΠΌΠΎΠ·Π½ΠΎΠΌ Π΄ΠΈΡΠΊΠ΅ 3. ΠΠΎΠ»ΠΎΠ΄ΠΊΠΈ ΠΌΠΎΠ³ΡΡ ΠΏΠΎΠ²ΠΎΡΠ°ΡΠΈΠ²Π°ΡΡΡΡ Π½Π° ΠΎΡΠΈ 1. ΠΠ΅ΠΆΠ΄Ρ Π²Π΅ΡΡ Π½ΠΈΠΌΠΈ ΠΊΠΎΠ½ΡΠ°ΠΌΠΈ ΠΊΠΎΠ»ΠΎΠ΄ΠΎΠΊ Π½Π°Ρ ΠΎΠ΄ΠΈΡΡΡ ΡΠ°Π·ΠΆΠΈΠΌΠ½ΠΎΠΉ ΠΊΡΠ»Π°ΠΊ 4.
ΠΡΠΈ ΡΠΎΡΠΌΠΎΠΆΠ΅Π½ΠΈΠΈ ΠΊΡΠ»Π°ΠΊ 4 ΡΠ°Π·Π²ΠΎΠ΄ΠΈΡ ΠΊΠΎΠ»ΠΎΠ΄ΠΊΠΈ 2 ΠΈ 6, ΠΏΡΠΈΠΆΠΈΠΌΠ°Ρ ΠΈΡ ΠΊ Π²ΡΠ°ΡΠ°ΡΡΠ΅ΠΌΡΡΡ Ρ ΠΊΠΎΠ»Π΅ΡΠΎΠΌ Π±Π°ΡΠ°Π±Π°Π½Ρ 5. Π’ΠΎΡΠΌΠΎΠΆΠ΅Π½ΠΈΠ΅ ΠΊΠΎΠ»Π΅ΡΠ° ΠΏΡΠΎΠΈΡΒΡ ΠΎΠ΄ΠΈΡ Π·Π° ΡΡΠ΅Ρ ΡΠΈΠ» ΡΡΠ΅Π½ΠΈΡ, Π²ΠΎΠ·Π½ΠΈΠΊΠ°ΡΡΠΈΡ ΠΌΠ΅ΠΆΠ΄Ρ ΡΡΠΈΠΊΡΠΈΠΎΠ½Π½ΡΠΌΠΈ Π½Π°ΠΊΠ»Π°Π΄ΠΊΠ°ΠΌΠΈ ΠΊΠΎΠ»ΠΎΠ΄ΠΎΠΊ ΠΈ ΡΠΎΡΠΌΠΎΠ·Π½ΡΠΌ Π±Π°ΡΠ°Π±Π°Π½ΠΎΠΌ.
Π Π΄ΠΈΡΠΊΠΎΠ²ΠΎΠΌ ΡΠΎΡΠΌΠΎΠ·Π½ΠΎΠΌ ΠΌΠ΅Ρ Π°Π½ΠΈΠ·ΠΌΠ΅ (ΡΠΈΡ. 10.2, Π±) ΡΠΎΡΠΌΠΎΠ·Π½ΠΎΠΉ Π΄ΠΈΡΠΊ 7 ΡΠ²ΡΠ·Π°Π½ Ρ ΠΊΠΎΠ»Π΅ΡΠΎΠΌ Π°Π²ΡΠΎΠΌΠΎΠ±ΠΈΠ»Ρ ΠΈ Π²ΡΠ°ΡΠ°Π΅ΡΡΡ Π²ΠΌΠ΅ΡΡΠ΅ Ρ Π½ΠΈΠΌ. Π‘ ΠΎΠ±Π΅ΠΈΡ ΡΡΠΎΡΠΎΠ½ ΡΠΎΡΠΌΠΎΠ·Π½ΠΎΠ³ΠΎ Π΄ΠΈΡΠΊΠ° ΡΡΡΠ°Π½ΠΎΠ²Π»Π΅Π½Ρ Π΄Π²Π΅ Π½Π΅Π²ΡΠ°ΡΠ°ΡΡΠΈΠ΅ΡΡ ΠΊΠΎΠ»ΠΎΠ΄ΠΊΠΈ 5 ΠΈ 9 Ρ ΡΡΠΈΠΊΡΠΈΠΎΠ½Π½ΡΠΌΠΈ Π½Π°ΠΊΠ»Π°Π΄ΠΊΠ°ΠΌΠΈ. ΠΡΠΈ ΡΠΎΡΠΌΠΎΠΆΠ΅Π½ΠΈΠΈ ΠΊΠΎΠ»Π΅ΡΠ° ΠΊΠΎΠ»ΠΎΠ΄ΠΊΠΈ ΠΏΡΠΈΠΆΠΈΠΌΠ°ΡΡΡΡ ΠΊ Π΄ΠΈΡΠΊΡ, ΡΠΎΠ·Π΄Π°Π²Π°Ρ ΡΠΎΡΠΌΠΎΠ·Π½ΠΎΠΉ ΠΌΠΎΠΌΠ΅Π½Ρ, ΠΏΡΠ΅ΠΏΡΡΡΡΠ²ΡΡΡΠΈΠΉ Π²ΡΠ°ΡΠ΅Π½ΠΈΡ ΠΊΠΎΠ»Π΅ΡΠ°.
ΠΠΈΡΠΊΠΎΠ²ΡΠ΅ ΡΠΎΡΠΌΠΎΠ·Π½ΡΠ΅ ΠΌΠ΅Ρ Π°Π½ΠΈΠ·ΠΌΡ ΠΏΠΎ ΡΡΠ°Π²Π½Π΅Π½ΠΈΡ Ρ Π±Π°ΡΠ°Π±Π°Π½Π½ΡΠΌΠΈ ΠΈΠΌΠ΅ΡΡ ΠΌΠ΅Π½ΡΡΡΡ ΠΌΠ°ΡΡΡ, Π±ΠΎΠ»Π΅Π΅ ΠΊΠΎΠΌΠΏΠ°ΠΊΡΠ½Ρ, Π±ΠΎΠ»Π΅Π΅ ΡΡΠ°Π±ΠΈΠ»ΡΠ½Ρ ΠΈ Π»ΡΡΡΠ΅ ΠΎΡ Π»Π°ΠΆΠ΄Π°ΡΡΡΡ. ΠΠ΄Π½Π°ΠΊΠΎ ΠΎΠ½ΠΈ ΠΌΠ΅Π½Π΅Π΅ ΡΡΡΠ΅ΠΊΡΠΈΠ²Π½Ρ, ΠΈΠΌΠ΅ΡΡ Π±ΠΎΠ»Π΅Π΅ Π±ΡΡΡΡΡΠΉ ΠΈΠ·Π½ΠΎΡ ΡΡΠΈΠΊΡΠΈΠΎΠ½Π½ΡΡ Π½Π°ΠΊΠ»Π°Π΄ΠΎΠΊ ΠΈ Ρ ΡΠΆΠ΅ Π·Π°ΡΠΈΡΠ΅Π½Ρ ΠΎΡ Π·Π°Π³ΡΡΠ·Π½Π΅Π½ΠΈΡ.
ΠΠΈΠ΄ΡΠ°Π²Π»ΠΈΡΠ΅ΡΠΊΠΈΠ΅, ΡΠ»Π΅ΠΊΡΡΠΈΡΠ΅ΡΠΊΠΈΠ΅, ΠΊΠΎΠΌΠΏΡΠ΅ΡΡΠΎΡΠ½ΡΠ΅ ΠΈ Π°ΡΡΠΎΠ΄ΠΈΠ½Π°ΠΌΠΈΡΠ΅ΡΠΊΠΈΠ΅ ΡΠΎΡΠΌΠΎΠ·Π½ΡΠ΅ ΠΌΠ΅Ρ Π°Π½ΠΈΠ·ΠΌΡ ΠΈΡΠΏΠΎΠ»ΡΠ·ΡΡΡΡΡ Π½Π° Π°Π²ΡΠΎΠΌΠΎΠ±ΠΈΠ»ΡΡ Π² ΠΊΠ°ΡΠ΅ΡΡΠ²Π΅ ΡΠΎΡΠΌΠΎΠ·ΠΎΠ²-Π·Π°ΠΌΠ΅Π΄Π»ΠΈΡΠ΅Π»Π΅ΠΉ.
ΠΠΈΠ΄ΡΠ°Π²Π»ΠΈΡΠ΅ΡΠΊΠΈΠΉ ΡΠΎΡΠΌΠΎΠ·-Π·Π°ΠΌΠ΅Π΄Π»ΠΈΡΠ΅Π»Ρ ΠΏΡΠ΅Π΄ΡΡΠ°Π²Π»ΡΠ΅Ρ ΡΠΎΠ±ΠΎΠΉ ΠΎΠ±ΡΡΠ½ΡΡ Π³ΠΈΠ΄ΡΠΎΠΌΡΡΡΡ, ΠΎΠ΄Π½ΠΎ ΠΈΠ· ΠΊΠΎΠ»Π΅Ρ ΠΊΠΎΡΠΎΡΠΎΠΉ Π·Π°ΠΊΡΠ΅ΠΏΠ»Π΅Π½ΠΎ Π½Π΅ΠΏΠΎΠ΄Π²ΠΈΠΆΠ½ΠΎ, Π° Π΄ΡΡΠ³ΠΎΠ΅ ΡΡΡΠ°Π½ΠΎΠ²Π»Π΅Π½ΠΎ Π½Π° Π²Π°Π»Ρ ΡΡΠ°Π½ΡΠΌΠΈΡΡΠΈΠΈ (Π·Π° ΠΊΠΎΡΠΎΠ±ΠΊΠΎΠΉ ΠΏΠ΅ΡΠ΅Π΄Π°Ρ) ΠΈ Π²ΡΠ°ΡΠ°Π΅ΡΡΡ Π²ΠΌΠ΅ΡΡΠ΅ Ρ Π²Π°Π»ΠΎΠΌ. Π’ΠΎΡΠΌΠΎΠ·Π½ΠΎΠΉ ΠΌΠΎΠΌΠ΅Π½Ρ Π³ΠΈΠ΄ΡΠ°Π²Π»ΠΈΡΠ΅ΡΠΊΠΎΠ³ΠΎ ΡΠΎΡΠΌΠΎΠ·Π°-Π·Π°ΠΌΠ΅Π΄Π»ΠΈΡΠ΅Π»Ρ Π·Π°Π²ΠΈΡΠΈΡ ΠΎΡ ΡΠΊΠΎΡΠΎΡΡΠΈ Π²ΡΠ°ΡΠ΅Π½ΠΈΡ ΡΠ°Π±ΠΎΡΠ΅Π³ΠΎ ΠΊΠΎΠ»Π΅ΡΠ° ΠΈ ΠΊΠΎΠ»ΠΈΡΠ΅ΡΡΠ²Π° ΠΏΠΎΠ΄Π°Π²Π°Π΅ΠΌΠΎΠΉ ΠΆΠΈΠ΄ΠΊΠΎΡΡΠΈ.
ΠΠ»Π΅ΠΊΡΡΠΈΡΠ΅ΡΠΊΠΈΠΉ ΡΠΎΡΠΌΠΎΠ·-Π·Π°ΠΌΠ΅Π΄Π»ΠΈΡΠ΅Π»Ρ ΠΎΠ±ΡΡΠ½ΠΎ ΡΠ°ΡΠΏΠΎΠ»Π°Π³Π°ΡΡ Π·Π° ΠΊΠΎΡΠΎΠ±ΠΊΠΎΠΉ ΠΏΠ΅ΡΠ΅Π΄Π°Ρ. ΠΠ½ ΠΏΡΠ΅Π΄ΡΡΠ°Π²Π»ΡΠ΅Ρ ΡΠΎΠ±ΠΎΠΉ ΠΌΠ°ΡΡΠΈΠ²Π½ΡΠΉ ΡΡΠ°Π»ΡΠ½ΠΎΠΉ Π΄ΠΈΡΠΊ, Π·Π°ΠΊΡΠ΅ΠΏΠ»Π΅Π½Π½ΡΠΉ Π½Π° Π²Π°Π»Ρ ΡΡΠ°Π½ΡΠΌΠΈΡΡΠΈΠΈ ΠΈ Π²ΡΠ°ΡΠ°ΡΡΠΈΠΉΡΡ Ρ Π²Π°Π»ΠΎΠΌ ΠΎΡΠ½ΠΎΡΠΈΡΠ΅Π»ΡΠ½ΠΎ Π½Π΅ΠΏΠΎΠ΄Π²ΠΈΠΆΠ½ΡΡ ΡΠ»Π΅ΠΊΡΡΠΎΠΌΠ°Π³Π½ΠΈΡΠΎΠ². Π’ΠΎΡΠΌΠΎΠΆΠ΅Π½ΠΈΠ΅ Π°Π²ΡΠΎΠΌΠΎΠ±ΠΈΠ»Ρ ΠΏΡΠΎΠΈΡΡ ΠΎΠ΄ΠΈΡ Π·Π° ΡΡΠ΅Ρ ΡΠ°Π±ΠΎΡΡ, ΠΊΠΎΡΠΎΡΠ°Ρ Π·Π°ΡΡΠ°ΡΠΈΠ²Π°Π΅ΡΡΡ Π½Π° ΠΏΡΠ΅ΠΎΠ΄ΠΎΠ»Π΅Π½ΠΈΠ΅ ΠΌΠ°Π³Π½ΠΈΡΠ½ΠΎΠ³ΠΎ Π²Π·Π°ΠΈΠΌΠΎΠ΄Π΅ΠΉΡΡΠ²ΠΈΡ ΠΌΠ΅ΠΆΠ΄Ρ Π²ΡΠ°ΡΠ°ΡΡΠΈΠΌΡΡ Π΄ΠΈΡΒΠΊΠΎΠΌ ΠΈ ΡΠ»Π΅ΠΊΡΡΠΎΠΌΠ°Π³Π½ΠΈΡΠ°ΠΌΠΈ.
ΠΠΎΠΌΠΏΡΠ΅ΡΡΠΎΡΠ½ΡΠΉ ΡΠΎΡΠΌΠΎΠ·-Π·Π°ΠΌΠ΅Π΄Π»ΠΈΡΠ΅Π»Ρ ΠΏΡΠ΅Π΄ΡΡΠ°Π²Π»ΡΠ΅Ρ ΡΠΎΠ±ΠΎΠΉ ΠΌΠΎΡΠΎΡΒΠ½ΡΠΉ ΡΠΎΡΠΌΠΎΠ·, ΠΈΡΠΏΠΎΠ»ΡΠ·ΡΡΡΠΈΠΉ ΠΏΡΠΎΡΠΈΠ²ΠΎΠ΄Π°Π²Π»Π΅Π½ΠΈΠ΅ Π½Π° Π²ΡΠΏΡΡΠΊΠ΅ ΠΏΡΠΈ ΡΠ°Π±ΠΎΡΠ΅ Π΄Π²ΠΈΠ³Π°ΡΠ΅Π»Ρ Π½Π° ΠΊΠΎΠΌΠΏΡΠ΅ΡΡΠΎΡΠ½ΠΎΠΌ ΡΠ΅ΠΆΠΈΠΌΠ΅. ΠΠ΅Ρ Π°Π½ΠΈΠ·ΠΌ ΠΌΠΎΡΠΎΡΠ½ΠΎΠ³ΠΎ ΡΠΎΡΠΌΠΎΠ·Π° (ΡΠΈΡ. 10.3) ΡΡΡΠ°Π½Π°Π²Π»ΠΈΠ²Π°ΡΡ Π² ΠΏΡΠΈΠ΅ΠΌΠ½ΠΎΠΉ ΡΡΡΠ±Π΅ Π³Π»ΡΡΠΈΡΠ΅Π»Ρ.
Π ΠΈΡ. 10.3. ΠΠΎΡΠΎΡΠ½ΡΠΉ ΡΠΎΡΠΌΠΎΠ·Π½ΠΎΠΉ ΠΌΠ΅Ρ Π°Π½ΠΈΠ·ΠΌ:1 β ΠΊΠΎΡΠΏΡΡ; 2 β ΡΡΡΠ°Π³; 3 β Π·Π°ΡΠ»ΠΎΠ½ΠΊΠ°; 4 β Π²Π°Π»
ΠΠ»Ρ ΡΠΎΠ·Π΄Π°Π½ΠΈΡ ΠΏΡΠΎΡΠΈΠ²ΠΎΠ΄Π°Π²Π»Π΅Π½ΠΈΡ ΠΏΡΠΈ ΡΠΎΡΠΌΠΎΠΆΠ΅Π½ΠΈΠΈ Π°Π²ΡΠΎΠΌΠΎΠ±ΠΈΠ»Ρ ΠΏΡΠΈΠ΅ΠΌΠ½Π°Ρ ΡΡΡΠ±Π° Π³Π»ΡΡΠΈΡΠ΅Π»Ρ ΠΏΠ΅ΡΠ΅ΠΊΡΡΠ²Π°Π΅ΡΡΡ Π·Π°ΡΠ»ΠΎΠ½ΠΊΠΎΠΉ 3. ΠΠ΄Π½ΠΎΠ²ΡΠ΅ΠΌΠ΅Π½Π½ΠΎ Ρ ΡΡΠΈΠΌ ΠΏΡΠ΅ΠΊΡΠ°ΡΠ°Π΅ΡΡΡ ΠΏΠΎΠ΄Π°ΡΠ° ΡΠΎΠΏΠ»ΠΈΠ²Π° Π² ΡΠΈΠ»ΠΈΠ½Π΄ΡΡ Π΄Π²ΠΈΠ³Π°ΡΠ΅Π»Ρ, ΠΈ Π΄Π²ΠΈΠ³Π°ΡΠ΅Π»Ρ ΡΠ°Π±ΠΎΡΠ°Π΅Ρ ΠΊΠ°ΠΊ ΠΊΠΎΠΌΠΏΡΠ΅ΡΡΠΎΡ. Π ΡΠ΅Π·ΡΠ»ΡΡΠ°ΡΠ΅ ΡΠΎΡΠΌΠΎΠ·Π½ΠΎΠΉ ΠΌΠΎΠΌΠ΅Π½Ρ Π΄Π²ΠΈΠ³Π°ΡΠ΅Π»Ρ Π²ΠΎΠ·ΡΠ°ΡΡΠ°Π΅Ρ ΠΏΠΎΡΡΠΈ Π² Π΄Π²Π° ΡΠ°Π·Π° ΠΏΠΎ ΡΡΠ°Π²Π½Π΅Π½ΠΈΡ Ρ ΠΌΠΎΠΌΠ΅Π½ΡΠΎΠΌ ΠΏΡΠΈ ΠΎΠ±ΡΡΠ½ΠΎΠΌ ΡΠΎΡΠΌΠΎΠΆΠ΅Π½ΠΈΠΈ Π΄Π²ΠΈΠ³Π°ΡΠ΅Π»Π΅ΠΌ.
ΠΡΡΠΎΠ΄ΠΈΠ½Π°ΠΌΠΈΡΠ΅ΡΠΊΠΈΠ΅ ΡΠΎΡΠΌΠΎΠ·Π°-Π·Π°ΠΌΠ΅Π΄Π»ΠΈΡΠ΅Π»ΠΈ Π²ΡΠΏΠΎΠ»Π½ΡΡΡΡΡ Π² Π²ΠΈΠ΄Π΅ ΡΠΏΠ΅ΡΠΈΠ°Π»ΡΠ½ΡΡ ΡΠΈΡΠΎΠ², Π·Π°ΠΊΡΡΠ»ΠΎΠΊ ΠΈ ΠΏΠ°ΡΠ°ΡΡΡΠΎΠ². ΠΠΌΠΈ ΠΎΠ±ΠΎΡΡΠ΄ΡΡΡΡΡ ΡΠΊΠΎΡΠΎΡΡΠ½ΡΠ΅ ΠΈ Π³ΠΎΠ½ΠΎΡΠ½ΡΠ΅ Π°Π²ΡΠΎΠΌΠΎΠ±ΠΈΠ»ΠΈ, Π΄Π²ΠΈΠΆΡΡΠΈΠ΅ΡΡ Ρ Π²ΡΡΠΎΠΊΠΈΠΌΠΈ ΡΠΊΠΎΡΠΎΡΡΡΠΌΠΈ. ΠΡΡΠΎΠ΄ΠΈΠ½Π°ΠΌΠΈΡΠ΅ΡΠΊΠΈΠ΅ ΡΠΎΡΠΌΠΎΠ·Π½ΡΠ΅ ΠΌΠ΅Ρ Π°Π½ΠΈΠ·ΠΌΡ ΡΠ²Π΅Π»ΠΈΡΠΈΠ²Π°ΡΡ ΡΠΎΠΏΡΠΎΡΠΈΠ²Π»Π΅Π½ΠΈΠ΅ Π²ΠΎΠ·Π΄ΡΡ Π° ΠΈ ΠΈΡΠΏΠΎΠ»ΡΠ·ΡΡΡΡΡ Π΄Π»Ρ ΡΠΊΡΡΡΠ΅Π½Π½ΠΎΠ³ΠΎ Π²Π½Π΅ΠΊΠΎΠ»Π΅ΡΠ½ΠΎΠ³ΠΎ ΡΠΎΡΠΌΠΎΠΆΠ΅Π½ΠΈΡ Π°Π²ΡΠΎΠΌΠΎΠ±ΠΈΠ»Π΅ΠΉ.
Π Π΅ΠΊΠΎΠΌΠ΅Π½Π΄ΡΠ΅ΠΌΡΠ΅ ΡΡΡΠ°Π½ΠΈΡΡ:
lektsia.com
ΠΡΠ½ΠΎΠ²Π½ΡΠ΅ ΡΠΈΠΏΡ ΠΊΠΎΠ»Π΅ΡΠ½ΡΡ ΡΠΎΡΠΌΠΎΠ·Π½ΡΡ ΠΌΠ΅Ρ Π°Π½ΠΈΠ·ΠΌΠΎΠ²
Β
Π ΡΠΎΡΠΌΠΎΠ·Π½ΡΡ ΡΠΈΡΡΠ΅ΠΌΠ°Ρ Π°Π²ΡΠΎΠΌΠΎΠ±ΠΈΠ»Π΅ΠΉ Π½Π°ΠΈΠ±ΠΎΠ»Π΅Π΅ ΡΠ°ΡΠΏΡΠΎΡΡΡΠ°Π½Π΅Π½Ρ ΡΡΠΈΠΊΡΠΈΠΎΠ½Π½ΡΠ΅ ΡΠΎΡΠΌΠΎΠ·Π½ΡΠ΅ ΠΌΠ΅Ρ Π°Π½ΠΈΠ·ΠΌΡ, ΠΏΡΠΈΠ½ΡΠΈΠΏ Π΄Π΅ΠΉΡΡΠ²ΠΈΡ ΠΊΠΎΡΠΎΡΡΡ ΠΎΡΠ½ΠΎΠ²Π°Π½ Π½Π° ΡΠΈΠ»Π°Ρ ΡΡΠ΅Π½ΠΈΡ Π²ΡΠ°ΡΠ°ΡΡΠΈΡ ΡΡ Π΄Π΅ΡΠ°Π»Π΅ΠΉ ΠΎ Π½Π΅Π²ΡΠ°ΡΠ°ΡΡΠΈΠ΅ΡΡ. ΠΠΎ ΡΠΎΡΠΌΠ΅ Π²ΡΠ°ΡΠ°ΡΡΠ΅ΠΉΡΡ Π΄Π΅ΡΠ°Π»ΠΈ ΠΊΠΎΠ»Π΅ΡΠ½ΡΠ΅ ΡΠΎΡΠΌΠΎΠ·Π½ΡΠ΅ ΠΌΠ΅Ρ Π°Π½ΠΈΠ·ΠΌΡ Π΄Π΅Π»ΡΡ Π½Π° Π±Π°ΡΠ°Π±Π°Π½Π½ΡΠ΅ ΠΈ Π΄ΠΈΡΠΊΠΎΠ²ΡΠ΅.
ΠΠ°ΡΠ°Π±Π°Π½Π½ΡΠΉ ΡΠΎΡΠΌΠΎΠ·Π½ΠΎΠΉ ΠΌΠ΅Ρ Π°Π½ΠΈΠ·ΠΌ Ρ Π³ΠΈΠ΄ΡΠ°Π²Π»ΠΈΡΠ΅ΡΠΊΠΈΠΌ ΠΏΡΠΈΠ²ΠΎΠ΄ΠΎΠΌ (ΡΠΈΡ. Π°) ΡΠΎΡΡΠΎΠΈΡ ΠΈΠ· Π΄Π²ΡΡ ΠΊΠΎΠ»ΠΎΠ΄ΠΎΠΊ 2 Ρ ΡΡΠΈΠΊΡΠΈΠΎΠ½Π½ΡΠΌΠΈ Π½Π°ΠΊΠ»Π°Π΄ΠΊΠ°ΠΌΠΈ, ΡΡΡΠ°Π½ΠΎΠ²Π»Π΅Π½Π½ΡΡ Π½Π° ΠΎΠΏΠΎΡΠ½ΠΎΠΌ Π΄ΠΈΡΠΊΠ΅ 3. ΠΠΈΠΆΠ½ΠΈΠ΅ ΠΊΠΎΠ½ΡΡ ΠΊΠΎΠ»ΠΎΠ΄ΠΎΠΊ Π·Π°ΠΊΡΠ΅ΠΏΠ»Π΅Π½Ρ ΡΠ°ΡΠ½ΠΈΡΠ½ΠΎ Π½Π° ΠΎΠΏΠΎΡΠ°Ρ 5, Π° Π²Π΅ΡΡ Π½ΠΈΠ΅ ΡΠΏΠΈΡΠ°ΡΡΡΡ ΡΠ΅ΡΠ΅Π· ΡΡΠ°Π»ΡΠ½ΡΠ΅ ΡΡΡ Π°ΡΠΈ Π² ΠΏΠΎΡΡΠ½ΠΈ ΡΠ°Π·ΠΆΠΈΠΌΠ½ΠΎΠ³ΠΎ ΠΊΠΎΠ»Π΅ΡΠ½ΠΎΠ³ΠΎ ΡΠΈΠ»ΠΈΠ½Π΄ΡΠ° 1. Π‘ΡΡΠΆΠ½Π°Ρ ΠΏΡΡΠΆΠΈΠ½Π° 6 ΠΏΡΠΈΠΆΠΈΠΌΠ°Π΅Ρ ΠΊΠΎΠ»ΠΎΠ΄ΠΊΠΈ ΠΊ ΠΏΠΎΡΡΠ½ΡΠΌ ΡΠΈΠ»ΠΈΠ½Π΄ΡΠ° 1, ΠΎΠ±Π΅ΡΠΏΠ΅ΡΠΈΠ²Π°Ρ Π·Π°Π·ΠΎΡ ΠΌΠ΅ΠΆΠ΄Ρ ΠΊΠΎΠ»ΠΎΠ΄ΠΊΠ°ΠΌΠΈ ΠΈ ΡΠΎΡΠΌΠΎΠ·Π½ΡΠΌ Π±Π°ΡΠ°Π±Π°Π½ΠΎΠΌ 4 Π² Π½Π΅ΡΠ°Π±ΠΎΡΠ΅ΠΌ ΠΏΠΎΠ»ΠΎΠΆΠ΅Π½ΠΈΠΈ ΡΠΎΡΠΌΠΎΠ·Π°. ΠΡΠΈ ΠΏΠΎΡΡΡΠΏΠ»Π΅Π½ΠΈΠΈ ΠΆΠΈΠ΄ΠΊΠΎΡΡΠΈ ΠΈΠ· ΠΏΡΠΈΠ²ΠΎΠ΄Π° Π² ΠΊΠΎΠ»Π΅ΡΠ½ΡΠΉ ΡΠΈΠ»ΠΈΠ½Π΄Ρ 1 Π΅Π³ΠΎ ΠΏΠΎΡΡΠ½ΠΈ ΡΠ°ΡΡ ΠΎΠ΄ΡΡΡΡ ΠΈ ΡΠ°Π·Π΄Π²ΠΈΠ³Π°ΡΡ ΠΊΠΎΠ»ΠΎΠ΄ΠΊΠΈ Π΄ΠΎ ΡΠΎΠΏΡΠΈΠΊΠΎΡΠ½ΠΎΠ²Π΅Π½ΠΈΡ Ρ ΡΠΎΡΠΌΠΎΠ·Π½ΡΠΌ Π±Π°ΡΠ°Π±Π°Π½ΠΎΠΌ, ΠΊΠΎΡΠΎΡΡΠΉ Π²ΡΠ°ΡΠ°Π΅ΡΡΡ Π²ΠΌΠ΅ΡΡΠ΅ ΡΠΎ ΡΡΡΠΏΠΈΡΠ΅ΠΉ ΠΊΠΎΠ»Π΅ΡΠ°. ΠΠΎΠ·Π½ΠΈΠΊΠ°ΡΡΠ°Ρ ΡΠΈΠ»Π° ΡΡΠ΅Π½ΠΈΡ ΠΊΠΎΠ»ΠΎΠ΄ΠΎΠΊ ΠΎ Π±Π°ΡΠ°Π±Π°Π½ Π²ΡΠ·ΡΠ²Π°Π΅Ρ Π·Π°ΡΠΎΡΠΌΠ°ΠΆΠΈΠ²Π°Π½ΠΈΠ΅ ΠΊΠΎΠ»Π΅ΡΠ°. ΠΠΎΡΠ»Π΅ ΠΏΡΠ΅ΠΊΡΠ°ΡΠ΅Π½ΠΈΡ Π΄Π°Π²Π»Π΅Π½ΠΈΡ ΠΆΠΈΠ΄ΠΊΠΎΡΡΠΈ Π½Π° ΠΏΠΎΡΡΠ½ΠΈ ΠΊΠΎΠ»Π΅ΡΠ½ΠΎΠ³ΠΎ ΡΠΈΠ»ΠΈΠ½Π΄ΡΠ° ΡΡΡΠΆΠ½Π°Ρ ΠΏΡΡΠΆΠΈΠ½Π° 11 Π²ΠΎΠ·Π²ΡΠ°ΡΠ°Π΅Ρ ΠΊΠΎΠ»ΠΎΠ΄ΠΊΠΈ Π² ΠΈΡΡ ΠΎΠ΄Π½ΠΎΠ΅ ΠΏΠΎΠ»ΠΎΠΆΠ΅Π½ΠΈΠ΅ ΠΈ ΡΠΎΡΠΌΠΎΠΆΠ΅Π½ΠΈΠ΅ ΠΏΡΠ΅ΠΊΡΠ°ΡΠ°Π΅ΡΡΡ.
Π Π°ΡΡΠΌΠΎΡΡΠ΅Π½Π½Π°Ρ ΠΊΠΎΠ½ΡΡΡΡΠΊΡΠΈΡ Π±Π°ΡΠ°Π±Π°Π½Π½ΠΎΠ³ΠΎ ΡΠΎΡΠΌΠΎΠ·Π° ΡΠΏΠΎΡΠΎΠ±ΡΡΠ²ΡΠ΅Ρ Π½Π΅ΡΠ°Π²Π½ΠΎΠΌΠ΅ΡΠ½ΠΎΠΌΡ ΠΈΠ·Π½ΠΎΡΡ ΠΏΠ΅ΡΠ΅Π΄Π½Π΅ΠΉ ΠΈ Π·Π°Π΄Π½Π΅ΠΉ ΠΏΠΎ Ρ ΠΎΠ΄Ρ Π΄Π²ΠΈΠΆΠ΅Π½ΠΈΡ ΠΊΠΎΠ»ΠΎΠ΄ΠΎΠΊ. ΠΡΠΎ ΠΏΡΠΎΠΈΡΡ ΠΎΠ΄ΠΈΡ Π² ΡΠ΅Π·ΡΠ»ΡΡΠ°ΡΠ΅ ΡΠΎΠ³ΠΎ, ΡΡΠΎ ΠΏΡΠΈ Π΄Π²ΠΈΠΆΠ΅Π½ΠΈΠΈ Π²ΠΏΠ΅ΡΠ΅Π΄ Π² ΠΌΠΎΠΌΠ΅Π½Ρ ΡΠΎΡΠΌΠΎΠΆΠ΅Π½ΠΈΡ ΠΏΠ΅ΡΠ΅Π΄Π½ΡΡ ΠΊΠΎΠ»ΠΎΠ΄ΠΊΠ° ΡΠ°Π±ΠΎΡΠ°Π΅Ρ ΠΏΡΠΎΡΠΈΠ² Π²ΡΠ°ΡΠ΅Π½ΠΈΡ ΠΊΠΎΠ»Π΅ΡΠ° ΠΈ ΠΏΡΠΈΠΆΠΈΠΌΠ°Π΅ΡΡΡ ΠΊ Π±Π°ΡΠ°Π±Π°Π½Ρ Ρ Π±ΠΎΠ»ΡΡΠ΅ΠΉ ΡΠΈΠ»ΠΎΠΉ, ΡΠ΅ΠΌ Π·Π°Π΄Π½ΡΡ. ΠΠΎΡΡΠΎΠΌΡ, ΡΡΠΎΠ±Ρ ΡΡΠ°Π²Π½ΡΡΡ ΠΈΠ·Π½ΠΎΡ ΠΏΠ΅ΡΠ΅Π΄Π½Π΅ΠΉ ΠΈ Π·Π°Π΄Π½Π΅ΠΉ ΠΊΠΎΠ»ΠΎΠ΄ΠΎΠΊ, Π΄Π»ΠΈΠ½Ρ ΠΏΠ΅ΡΠ΅Π΄Π½Π΅ΠΉ Π½Π°ΠΊΠ»Π°Π΄ΠΊΠΈ Π΄Π΅Π»Π°ΡΡ Π±ΠΎΠ»ΡΡΠ΅, ΡΠ΅ΠΌ Π·Π°Π΄Π½Π΅ΠΉ, ΠΈΠ»ΠΈ ΡΠ΅ΠΊΠΎΠΌΠ΅Π½Π΄ΡΡΡ ΠΌΠ΅Π½ΡΡΡ ΠΌΠ΅ΡΡΠ°ΠΌΠΈ ΠΊΠΎΠ»ΠΎΠ΄ΠΊΠΈ ΡΠ΅ΡΠ΅Π· ΠΎΠΏΡΠ΅Π΄Π΅Π»Π΅Π½Π½ΡΠΉ ΡΡΠΎΠΊ.
Β
ΠΠΎΠ»Π΅ΡΠ½ΡΠΉ Π±Π°ΡΠ°Π±Π°Π½Π½ΡΠΉ ΡΠΎΡΠΌΠΎΠ·Π½ΠΎΠΉ ΠΌΠ΅Ρ Π°Π½ΠΈΠ·ΠΌ
Π Π΄ΡΡΠ³ΠΎΠΉ ΠΊΠΎΠ½ΡΡΡΡΠΊΡΠΈΠΈ Π±Π°ΡΠ°Π±Π°Π½Π½ΠΎΠ³ΠΎ ΠΌΠ΅Ρ Π°Π½ΠΈΠ·ΠΌΠ° ΠΎΠΏΠΎΡΡ ΠΊΠΎΠ»ΠΎΠ΄ΠΎΠΊ ΡΠ°ΡΠΏΠΎΠ»Π°Π³Π°ΡΡ Π½Π° ΠΏΡΠΎΡΠΈΠ²ΠΎΠΏΠΎΠ»ΠΎΠΆΠ½ΡΡ ΡΡΠΎΡΠΎΠ½Π°Ρ ΡΠΎΡΠΌΠΎΠ·Π½ΠΎΠ³ΠΎ Π΄ΠΈΡΠΊΠ° ΠΈ ΠΏΡΠΈΠ²ΠΎΠ΄ ΠΊΠ°ΠΆΠ΄ΠΎΠΉ ΠΊΠΎΠ»ΠΎΠ΄ΠΊΠΈ Π²ΡΠΏΠΎΠ»Π½ΡΡΡ ΠΎΡ ΠΎΡΠ΄Π΅Π»ΡΠ½ΠΎΠ³ΠΎ Π³ΠΈΠ΄ΡΠΎΡΠΈΠ»ΠΈΠ½Π΄ΡΠ°. ΠΡΠΈΠΌ Π΄ΠΎΡΡΠΈΠ³Π°Π΅ΡΡΡ Π±ΠΎΠ»ΡΡΠΈΠΉ ΡΠΎΡΠΌΠΎΠ·Π½ΠΎΠΉ ΠΌΠΎΠΌΠ΅Π½Ρ ΠΈ ΡΠ°Π²Π½ΠΎΠΌΠ΅ΡΠ½ΠΎΡΡΡ ΠΈΠ·Π½Π°ΡΠΈΠ²Π°Π½ΠΈΡ ΠΊΠΎΠ»ΠΎΠ΄ΠΎΠΊ Π½Π° ΠΊΠ°ΠΆΠ΄ΠΎΠΌ ΠΊΠΎΠ»Π΅ΡΠ΅, ΠΎΠ±ΠΎΡΡΠ΄ΠΎΠ²Π°Π½Π½ΠΎΠΌ ΠΏΠΎ ΡΠ°ΠΊΠΎΠΉ ΡΡ Π΅ΠΌΠ΅.
ΠΠ°ΡΠ°Π±Π°Π½Π½ΡΠΉ ΡΠΎΡΠΌΠΎΠ·Π½ΠΎΠΉ ΠΌΠ΅Ρ Π°Π½ΠΈΠ·ΠΌ Ρ ΠΏΠ½Π΅Π²ΠΌΠ°ΡΠΈΡΠ΅ΡΠΊΠΈΠΌ ΠΏΡΠΈΠ²ΠΎΠ΄ΠΎΠΌ (ΡΠΈΡ. Π±) ΠΎΡΠ»ΠΈΡΠ°Π΅ΡΡΡ ΠΎΡ ΠΌΠ΅Ρ Π°Π½ΠΈΠ·ΠΌΠ° Ρ Π³ΠΈΠ΄ΡΠ°Π²Π»ΠΈΡΠ΅ΡΠΊΠΈΠΌ ΠΏΡΠΈΠ²ΠΎΠ΄ΠΎΠΌ ΠΊΠΎΠ½ΡΡΡΡΠΊΡΠΈΠ΅ΠΉ ΡΠ°Π·ΠΆΠΈΠΌΠ½ΠΎΠ³ΠΎ ΡΡΡΡΠΎΠΉΡΡΠ²Π° ΠΊΠΎΠ»ΠΎΠ΄ΠΎΠΊ. Π Π½Π΅ΠΌ ΠΈΡΠΏΠΎΠ»ΡΠ·ΡΠ΅ΡΡΡ Π΄Π»Ρ ΡΠ°Π·Π²Π΅Π΄Π΅Π½ΠΈΡ ΠΊΠΎΠ»ΠΎΠ΄ΠΎΠΊ ΡΠ°Π·ΠΆΠΈΠΌΠ½ΡΠΉ ΠΊΡΠ»Π°ΠΊ 7, ΠΏΡΠΈΠ²ΠΎΠ΄ΠΈΠΌΡΠΉ Π² Π΄Π²ΠΈΠΆΠ΅Π½ΠΈΠ΅ ΡΡΡΠ°Π³ΠΎΠΌ 8, ΠΏΠΎΡΠ°ΠΆΠ΅Π½Π½ΡΠΌ Π½Π° ΠΎΡΡ ΡΠ°Π·ΠΆΠΈΠΌΠ½ΠΎΠ³ΠΎ ΠΊΡΠ»Π°ΠΊΠ°. Π ΡΡΠ°Π³ ΠΎΡΠΊΠ»ΠΎΠ½ΡΠ΅ΡΡΡ ΡΡΠΈΠ»ΠΈΠ΅ΠΌ, Π²ΠΎΠ·Π½ΠΈΠΊΠ°ΡΡΠ΅ΠΌ Π² ΠΏΠ½Π΅Π²ΠΌΠ°ΡΠΈΡΠ΅ΡΠΊΠΎΠΉ ΡΠΎΡΠΌΠΎΠ·Π½ΠΎΠΉ ΠΊΠ°ΠΌΠ΅ΡΠ΅ 9, ΠΊΠΎΡΠΎΡΠ°Ρ ΡΠ°Π±ΠΎΡΠ°Π΅Ρ ΠΎΡ Π΄Π°Π²Π»Π΅Π½ΠΈΡ ΡΠΆΠ°ΡΠΎΠ³ΠΎ Π²ΠΎΠ·Π΄ΡΡ Π°. ΠΠΎΠ·Π²ΡΠ°Ρ ΠΊΠΎΠ»ΠΎΠ΄ΠΎΠΊ Π² ΠΈΡΡ ΠΎΠ΄Π½ΠΎΠ΅ ΠΏΠΎΠ»ΠΎΠΆΠ΅Π½ΠΈΠ΅ ΠΏΡΠΈ ΠΎΡΡΠΎΡΠΌΠ°ΠΆΠΈΠ²Π°Π½ΠΈΠΈ ΠΏΡΠΎΠΈΡΡ ΠΎΠ΄ΠΈΡ ΠΏΠΎΠ΄ Π΄Π΅ΠΉΡΡΠ²ΠΈΠ΅ΠΌ ΡΡΡΠΆΠ½ΠΎΠΉ ΠΏΡΡΠΆΠΈΠ½Ρ 11. ΠΠΈΠΆΠ½ΠΈΠ΅ ΠΊΠΎΠ½ΡΡ ΠΊΠΎΠ»ΠΎΠ΄ΠΎΠΊ Π·Π°ΠΊΡΠ΅ΠΏΠ»Π΅Π½Ρ Π½Π° ΡΠΊΡΡΠ΅Π½ΡΡΠΈΠΊΠΎΠ²ΡΡ ΠΏΠ°Π»ΡΡΠ°Ρ 10, ΠΊΠΎΡΠΎΡΡΠ΅ ΠΎΠ±Π΅ΡΠΏΠ΅ΡΠΈΠ²Π°ΡΡ ΡΠ΅Π³ΡΠ»ΠΈΡΠΎΠ²ΠΊΡ Π·Π°Π·ΠΎΡΠ° ΠΌΠ΅ΠΆΠ΄Ρ Π½ΠΈΠΆΠ½ΠΈΠΌΠΈ ΡΠ°ΡΡΡΠΌΠΈ ΠΊΠΎΠ»ΠΎΠ΄ΠΎΠΊ ΠΈ Π±Π°ΡΠ°Π±Π°Π½ΠΎΠΌ. ΠΠ΅ΡΡ Π½ΠΈΠ΅ ΡΠ°ΡΡΠΈ ΠΊΠΎΠ»ΠΎΠ΄ΠΎΠΊ ΠΏΠΎΠ΄Π²ΠΎΠ΄ΡΡΡΡ ΠΊ Π±Π°ΡΠ°Π±Π°Π½Ρ ΠΏΡΠΈ ΡΠ΅Π³ΡΠ»ΠΈΡΠΎΠ²ΠΊΠ΅ Π·Π°Π·ΠΎΡΠ° Ρ ΠΏΠΎΠΌΠΎΡΡΡ ΡΠ΅ΡΠ²ΡΡΠ½ΠΎΠ³ΠΎ ΠΌΠ΅Ρ Π°Π½ΠΈΠ·ΠΌΠ°.
Β
ΠΠΎΠ»Π΅ΡΠ½ΡΠΉ Π΄ΠΈΡΠΊΠΎΠ²ΡΠΉ ΡΠΎΡΠΌΠΎΠ·Π½ΠΎΠΉ ΠΌΠ΅Ρ Π°Π½ΠΈΠ·ΠΌ Ρ Π³ΠΈΠ΄ΡΠΎΠΏΡΠΈΠ²ΠΎΠ΄ΠΎΠΌ ΡΠΎΡΡΠΎΠΈΡ ΠΈΠ· ΡΠΎΡΠΌΠΎΠ·Π½ΠΎΠ³ΠΎ Π΄ΠΈΡΠΊΠ° 1, Π·Π°ΠΊΡΠ΅ΠΏΠ»Π΅Π½Π½ΠΎΠ³ΠΎ Π½Π° ΡΡΡΠΏΠΈΡΠ΅ ΠΊΠΎΠ»Π΅ΡΠ°. Π’ΠΎΡΠΌΠΎΠ·Π½ΠΎΠΉ Π΄ΠΈΡΠΊ Π²ΡΠ°ΡΠ°Π΅ΡΡΡ ΠΌΠ΅ΠΆΠ΄Ρ ΠΏΠΎΠ»ΠΎΠ²ΠΈΠ½ΠΊΠ°ΠΌΠΈ 8 ΠΈ 9 ΡΠΊΠΎΠ±Ρ, ΠΏΡΠΈΠΊΡΠ΅ΠΏΠ»Π΅Π½Π½ΠΎΠΉ ΠΊ ΡΡΠΎΠΉΠΊΠ΅ 4 ΠΏΠ΅ΡΠ΅Π΄Π½Π΅ΠΉ ΠΏΠΎΠ΄Π²Π΅ΡΠΊΠΈ. Π ΠΊΠ°ΠΆΠ΄ΠΎΠΉ ΠΏΠΎΠ»ΠΎΠ²ΠΈΠ½Π΅ ΡΠΊΠΎΠ±Ρ Π²ΡΡΠΎΡΠ΅Π½Ρ ΠΊΠΎΠ»Π΅ΡΠ½ΡΠ΅ ΡΠΈΠ»ΠΈΠ½Π΄ΡΡ Ρ Π±ΠΎΠ»ΡΡΠΈΠΌ 13 ΠΈ ΠΌΠ°Π»ΡΠΌ 12 ΠΏΠΎΡΡΠ½ΡΠΌΠΈ.
ΠΡΠΈ Π½Π°ΠΆΠ°ΡΠΈΠΈ Π½Π° ΡΠΎΡΠΌΠΎΠ·Π½ΡΡ ΠΏΠ΅Π΄Π°Π»Ρ ΠΆΠΈΠ΄ΠΊΠΎΡΡΡ ΠΈΠ· Π³Π»Π°Π²Π½ΠΎΠ³ΠΎ ΡΠΎΡΠΌΠΎΠ·Π½ΠΎΠ³ΠΎ ΡΠΈΠ»ΠΈΠ½Π΄ΡΠ° ΠΏΠ΅ΡΠ΅ΡΠ΅ΠΊΠ°Π΅Ρ ΠΏΠΎ ΡΠ»Π°Π½Π³Π°ΠΌ 2 Π² ΠΏΠΎΠ»ΠΎΡΡΠΈ ΠΊΠΎΠ»Π΅ΡΠ½ΡΡ ΡΠΈΠ»ΠΈΠ½Π΄ΡΠΎΠ² ΠΈ ΠΏΠ΅ΡΠ΅Π΄Π°Π΅Ρ Π΄Π°Π²Π»Π΅Π½ΠΈΠ΅ Π½Π° ΠΏΠΎΡΡΠ½ΠΈ, ΠΊΠΎΡΠΎΡΡΠ΅, ΠΏΠ΅ΡΠ΅ΠΌΠ΅ΡΠ°ΡΡΡ Ρ Π΄Π²ΡΡ ΡΡΠΎΡΠΎΠ½, ΠΏΡΠΈΠΆΠΈΠΌΠ°ΡΡ ΡΠΎΡΠΌΠΎΠ·Π½ΡΠ΅ ΠΊΠΎΠ»ΠΎΠ΄ΠΊΠΈ 10 ΠΊ Π΄ΠΈΡΠΊΡ 1, Π±Π»Π°Π³ΠΎΠ΄Π°ΡΡ ΡΠ΅ΠΌΡ ΠΈ ΠΏΡΠΎΠΈΡΡ ΠΎΠ΄ΠΈΡ ΡΠΎΡΠΌΠΎΠΆΠ΅Π½ΠΈΠ΅.
ΠΡΠΏΡΡΠΊΠ°Π½ΠΈΠ΅ ΠΏΠ΅Π΄Π°Π»ΠΈ Π²ΡΠ·ΡΠ²Π°Π΅Ρ ΠΏΠ°Π΄Π΅Π½ΠΈΠ΅ Π΄Π°Π²Π»Π΅Π½ΠΈΡ ΠΆΠΈΠ΄ΠΊΠΎΡΡΠΈ Π² ΠΏΡΠΈΠ²ΠΎΠ΄Π΅, ΠΏΠΎΡΡΠ½ΠΈ 13 ΠΈ 12 ΠΏΠΎΠ΄ Π΄Π΅ΠΉΡΡΠ²ΠΈΠ΅ΠΌ ΡΠΏΡΡΠ³ΠΎΡΡΠΈ ΡΠΏΠ»ΠΎΡΠ½ΠΈΡΠ΅Π»ΡΠ½ΡΡ ΠΌΠ°Π½ΠΆΠ΅Ρ ΠΈ ΠΎΡΠ΅Π²ΠΎΠ³ΠΎ Π±ΠΈΠ΅Π½ΠΈΡ Π΄ΠΈΡΠΊΠ° ΠΎΡΡ ΠΎΠ΄ΡΡ ΠΎΡ Π½Π΅Π³ΠΎ, ΠΈ ΡΠΎΡΠΌΠΎΠΆΠ΅Π½ΠΈΠ΅ ΠΏΡΠ΅ΠΊΡΠ°ΡΠ°Π΅ΡΡΡ.
ΠΡΠ΅ΠΈΠΌΡΡΠ΅ΡΡΠ²Π° Π±Π°ΡΠ°Π±Π°Π½Π½ΡΡ ΡΠΎΡΠΌΠΎΠ·ΠΎΠ²:
Β· Π½ΠΈΠ·ΠΊΠ°Ρ ΡΡΠΎΠΈΠΌΠΎΡΡΡ, ΠΏΡΠΎΡΡΠΎΡΠ° ΠΏΡΠΎΠΈΠ·Π²ΠΎΠ΄ΡΡΠ²Π°;
Β· ΠΎΠ±Π»Π°Π΄Π°ΡΡ ΡΡΡΠ΅ΠΊΡΠΎΠΌ ΠΌΠ΅Ρ Π°Π½ΠΈΡΠ΅ΡΠΊΠΎΠ³ΠΎ ΡΠ°ΠΌΠΎΡΡΠΈΠ»Π΅Π½ΠΈΡ. ΠΠ»Π°Π³ΠΎΠ΄Π°ΡΡ ΡΠΎΠΌΡ, ΡΡΠΎ Π½ΠΈΠΆΠ½ΠΈΠ΅ ΡΠ°ΡΡΠΈ ΠΊΠΎΠ»ΠΎΠ΄ΠΎΠΊ ΡΠ²ΡΠ·Π°Π½Ρ Π΄ΡΡΠ³ Ρ Π΄ΡΡΠ³ΠΎΠΌ, ΡΡΠ΅Π½ΠΈΠ΅ ΠΎ Π±Π°ΡΠ°Π±Π°Π½ ΠΏΠ΅ΡΠ΅Π΄Π½Π΅ΠΉ ΠΊΠΎΠ»ΠΎΠ΄ΠΊΠΈ ΡΡΠΈΠ»ΠΈΠ²Π°Π΅Ρ ΠΏΡΠΈΠΆΠ°ΡΠΈΠ΅ ΠΊ Π½Π΅ΠΌΡ Π·Π°Π΄Π½Π΅ΠΉ ΠΊΠΎΠ»ΠΎΠ΄ΠΊΠΈ. ΠΡΠΎΡ ΡΡΡΠ΅ΠΊΡ ΡΠΏΠΎΡΠΎΠ±ΡΡΠ²ΡΠ΅Ρ ΠΌΠ½ΠΎΠ³ΠΎΠΊΡΠ°ΡΠ½ΠΎΠΌΡ ΡΠ²Π΅Π»ΠΈΡΠ΅Π½ΠΈΡ ΡΠΎΡΠΌΠΎΠ·Π½ΠΎΠ³ΠΎ ΡΡΠΈΠ»ΠΈΡ, ΠΏΠ΅ΡΠ΅Π΄Π°Π²Π°Π΅ΠΌΠΎΠ³ΠΎ Π²ΠΎΠ΄ΠΈΡΠ΅Π»Π΅ΠΌ, ΠΈ Π±ΡΡΡΡΠΎ ΠΏΠΎΠ²ΡΡΠ°Π΅Ρ ΡΠΎΡΠΌΠΎΠ·ΡΡΠ΅Π΅ Π΄Π΅ΠΉΡΡΠ²ΠΈΠ΅ ΠΏΡΠΈ ΡΡΠΈΠ»Π΅Π½ΠΈΠΈ Π΄Π°Π²Π»Π΅Π½ΠΈΡ Π½Π° ΠΏΠ΅Π΄Π°Π»Ρ.
ΠΡΠ΅ΠΈΠΌΡΡΠ΅ΡΡΠ²Π° Π΄ΠΈΡΠΊΠΎΠ²ΡΡ ΡΠΎΡΠΌΠΎΠ·ΠΎΠ²:
— ΠΏΡΠΈ ΠΏΠΎΠ²ΡΡΠ΅Π½ΠΈΠΈ ΡΠ΅ΠΌΠΏΠ΅ΡΠ°ΡΡΡΡ Ρ Π°ΡΠ°ΠΊΡΠ΅ΡΠΈΡΡΠΈΠΊΠΈ Π΄ΠΈΡΠΊΠΎΠ²ΡΡ ΡΠΎΡΠΌΠΎΠ·ΠΎΠ² Π΄ΠΎΠ²ΠΎΠ»ΡΠ½ΠΎ ΡΡΠ°Π±ΠΈΠ»ΡΠ½Ρ, ΡΠΎΠ³Π΄Π° ΠΊΠ°ΠΊ Ρ Π±Π°ΡΠ°Π±Π°Π½Π½ΡΡ ΡΠ½ΠΈΠΆΠ°Π΅ΡΡΡ ΡΡΡΠ΅ΠΊΡΠΈΠ²Π½ΠΎΡΡΡ
— ΡΠ΅ΠΌΠΏΠ΅ΡΠ°ΡΡΡΠ½Π°Ρ ΡΡΠΎΠΉΠΊΠΎΡΡΡ Π΄ΠΈΡΠΊΠΎΠ² Π²ΡΡΠ΅, Π² ΡΠ°ΡΡΠ½ΠΎΡΡΠΈ, ΠΈΠ·-Π·Π° ΡΠΎΠ³ΠΎ, ΡΡΠΎ ΠΎΠ½ΠΈ Π»ΡΡΡΠ΅ ΠΎΡ Π»Π°ΠΆΠ΄Π°ΡΡΡΡ
— Π±ΠΎΠ»Π΅Π΅ Π²ΡΡΠΎΠΊΠ°Ρ ΡΡΡΠ΅ΠΊΡΠΈΠ²Π½ΠΎΡΡΡ ΡΠΎΡΠΌΠΎΠΆΠ΅Π½ΠΈΡ ΠΏΠΎΠ·Π²ΠΎΠ»ΡΠ΅Ρ ΡΠΌΠ΅Π½ΡΡΠΈΡΡ ΡΠΎΡΠΌΠΎΠ·Π½ΠΎΠΉ ΠΏΡΡΡ
— ΠΌΠ΅Π½ΡΡΠΈΠ΅ Π²Π΅Ρ ΠΈ ΡΠ°Π·ΠΌΠ΅ΡΡ
— ΠΏΠΎΠ²ΡΡΠ°Π΅ΡΡΡ ΡΡΠ²ΡΡΠ²ΠΈΡΠ΅Π»ΡΠ½ΠΎΡΡΡ ΡΠΎΡΠΌΠΎΠ·ΠΎΠ²
— Π²ΡΠ΅ΠΌΡ ΡΡΠ°Π±Π°ΡΡΠ²Π°Π½ΠΈΡ ΡΠΌΠ΅Π½ΡΡΠ°Π΅ΡΡΡ
— ΠΈΠ·Π½ΠΎΡΠ΅Π½Π½ΡΠ΅ ΠΊΠΎΠ»ΠΎΠ΄ΠΊΠΈ ΠΏΡΠΎΡΡΠΎ Π·Π°ΠΌΠ΅Π½ΠΈΡΡ, Π½Π° Π±Π°ΡΠ°Π±Π°Π½Π½ΡΡ ΠΏΡΠΈΡ ΠΎΠ΄ΠΈΡΡΡ ΠΏΡΠ΅Π΄ΠΏΡΠΈΠ½ΠΈΠΌΠ°ΡΡ ΡΡΠΈΠ»ΠΈΡ Π½Π° ΠΏΠΎΠ΄Π³ΠΎΠ½ΠΊΡ ΠΊΠΎΠ»ΠΎΠ΄ΠΎΠΊ ΡΡΠΎΠ±Ρ ΠΎΠ΄Π΅ΡΡ Π±Π°ΡΠ°Π±Π°Π½Ρ
— ΠΎΠΊΠΎΠ»ΠΎ 70% ΠΊΠΈΠ½Π΅ΡΠΈΡΠ΅ΡΠΊΠΎΠΉ ΡΠ½Π΅ΡΠ³ΠΈΠΈ Π°Π²ΡΠΎΠΌΠΎΠ±ΠΈΠ»Ρ Π³Π°ΡΠΈΡΡΡ ΠΏΠ΅ΡΠ΅Π΄Π½ΠΈΠΌΠΈ ΡΠΎΡΠΌΠΎΠ·Π°ΠΌΠΈ, Π·Π°Π΄Π½ΠΈΠ΅ Π΄ΠΈΡΠΊΠΎΠ²ΡΠ΅ ΡΠΎΡΠΌΠΎΠ·Π° ΠΏΠΎΠ·Π²ΠΎΠ»ΡΡΡ ΡΠ½ΠΈΠ·ΠΈΡΡ Π½Π°Π³ΡΡΠ·ΠΊΡ Π½Π° ΠΏΠ΅ΡΠ΅Π΄Π½ΠΈΠ΅ Π΄ΠΈΡΠΊΠΈ
— ΡΠ΅ΠΌΠΏΠ΅ΡΠ°ΡΡΡΠ½ΡΠ΅ ΡΠ°ΡΡΠΈΡΠ΅Π½ΠΈΡ Π½Π΅ Π²Π»ΠΈΡΡΡ Π½Π° ΠΊΠ°ΡΠ΅ΡΡΠ²ΠΎ ΠΏΡΠΈΠ»Π΅Π³Π°Π½ΠΈΡ ΡΠΎΡΠΌΠΎΠ·Π½ΡΡ ΠΏΠΎΠ²Π΅ΡΡ Π½ΠΎΡΡΠ΅ΠΉ.
Β
ΠΡΠΈΠ½ΡΠΈΠΏ ΡΠ°Π±ΠΎΡΡ ΡΠΎΡΠΌΠΎΠ·Π½ΠΎΠΉ ΡΠΈΡΡΠ΅ΠΌΡ
Β
ΠΡΠΈΠ½ΡΠΈΠΏ ΡΠ°Π±ΠΎΡΡ ΡΠΎΡΠΌΠΎΠ·Π½ΠΎΠΉ ΡΠΈΡΡΠ΅ΠΌΡ ΡΠ°ΡΡΠΌΠΎΡΡΠ΅Π½ Π½Π° ΠΏΡΠΈΠΌΠ΅ΡΠ΅ Π³ΠΈΠ΄ΡΠ°Π²Π»ΠΈΡΠ΅ΡΠΊΠΎΠΉ ΡΠ°Π±ΠΎΡΠ΅ΠΉ ΡΠΈΡΡΠ΅ΠΌΡ.
ΠΡΠΈ Π½Π°ΠΆΠ°ΡΠΈΠΈ Π½Π° ΠΏΠ΅Π΄Π°Π»Ρ ΡΠΎΡΠΌΠΎΠ·Π° Π½Π°Π³ΡΡΠ·ΠΊΠ° ΠΏΠ΅ΡΠ΅Π΄Π°Π΅ΡΡΡ ΠΊ ΡΡΠΈΠ»ΠΈΡΠ΅Π»Ρ, ΠΊΠΎΡΠΎΡΡΠΉ ΡΠΎΠ·Π΄Π°Π΅Ρ Π΄ΠΎΠΏΠΎΠ»Π½ΠΈΡΠ΅Π»ΡΠ½ΠΎΠ΅ ΡΡΠΈΠ»ΠΈΠ΅ Π½Π° Π³Π»Π°Π²Π½ΠΎΠΌ ΡΠΎΡΠΌΠΎΠ·Π½ΠΎΠΌ ΡΠΈΠ»ΠΈΠ½Π΄ΡΠ΅. ΠΠΎΡΡΠ΅Π½Ρ Π³Π»Π°Π²Π½ΠΎΠ³ΠΎ ΡΠΎΡΠΌΠΎΠ·Π½ΠΎΠ³ΠΎ ΡΠΈΠ»ΠΈΠ½Π΄ΡΠ° Π½Π°Π³Π½Π΅ΡΠ°Π΅Ρ ΠΆΠΈΠ΄ΠΊΠΎΡΡΡ ΡΠ΅ΡΠ΅Π· ΡΡΡΠ±ΠΎΠΏΡΠΎΠ²ΠΎΠ΄Ρ ΠΊ ΠΊΠΎΠ»Π΅ΡΠ½ΡΠΌ ΡΠΈΠ»ΠΈΠ½Π΄ΡΠ°ΠΌ. ΠΡΠΈ ΡΡΠΎΠΌ ΡΠ²Π΅Π»ΠΈΡΠΈΠ²Π°Π΅ΡΡΡ Π΄Π°Π²Π»Π΅Π½ΠΈΠ΅ ΠΆΠΈΠ΄ΠΊΠΎΡΡΠΈ Π² ΡΠΎΡΠΌΠΎΠ·Π½ΠΎΠΌ ΠΏΡΠΈΠ²ΠΎΠ΄Π΅. ΠΠΎΡΡΠ½ΠΈ ΠΊΠΎΠ»Π΅ΡΠ½ΡΡ ΡΠΈΠ»ΠΈΠ½Π΄ΡΠΎΠ² ΠΏΠ΅ΡΠ΅ΠΌΠ΅ΡΠ°ΡΡ ΡΠΎΡΠΌΠΎΠ·Π½ΡΠ΅ ΠΊΠΎΠ»ΠΎΠ΄ΠΊΠΈ ΠΊ Π΄ΠΈΡΠΊΠ°ΠΌ (Π±Π°ΡΠ°Π±Π°Π½Π°ΠΌ).
ΠΡΠΈ Π΄Π°Π»ΡΠ½Π΅ΠΉΡΠ΅ΠΌ Π½Π°ΠΆΠ°ΡΠΈΠΈ Π½Π° ΠΏΠ΅Π΄Π°Π»Ρ ΡΠ²Π΅Π»ΠΈΡΠΈΠ²Π°Π΅ΡΡΡ Π΄Π°Π²Π»Π΅Π½ΠΈΠ΅ ΠΆΠΈΠ΄ΠΊΠΎΡΡΠΈ ΠΈ ΠΏΡΠΎΠΈΡΡ ΠΎΠ΄ΠΈΡ ΡΡΠ°Π±Π°ΡΡΠ²Π°Π½ΠΈΠ΅ ΡΠΎΡΠΌΠΎΠ·Π½ΡΡ ΠΌΠ΅Ρ Π°Π½ΠΈΠ·ΠΌΠΎΠ², ΠΊΠΎΡΠΎΡΠΎΠ΅ ΠΏΡΠΈΠ²ΠΎΠ΄ΠΈΡ ΠΊ Π·Π°ΠΌΠ΅Π΄Π»Π΅Π½ΠΈΡ Π²ΡΠ°ΡΠ΅Π½ΠΈΡ ΠΊΠΎΠ»Π΅Ρ ΠΈ ΠΏΠΎΡΠ²Π»Π΅Π½ΠΈΡ ΡΠΎΡΠΌΠΎΠ·Π½ΡΡ ΡΠΈΠ» Π² ΡΠΎΡΠΊΠ΅ ΠΊΠΎΠ½ΡΠ°ΠΊΡΠ° ΡΠΈΠ½ Ρ Π΄ΠΎΡΠΎΠ³ΠΎΠΉ. Π§Π΅ΠΌ Π±ΠΎΠ»ΡΡΠ΅ ΠΏΡΠΈΠ»ΠΎΠΆΠ΅Π½Π° ΡΠΈΠ»Π° ΠΊ ΡΠΎΡΠΌΠΎΠ·Π½ΠΎΠΉ ΠΏΠ΅Π΄Π°Π»ΠΈ, ΡΠ΅ΠΌ Π±ΡΡΡΡΠ΅Π΅ ΠΈ ΡΡΡΠ΅ΠΊΡΠΈΠ²Π½Π΅Π΅ ΠΎΡΡΡΠ΅ΡΡΠ²Π»ΡΠ΅ΡΡΡ ΡΠΎΡΠΌΠΎΠΆΠ΅Π½ΠΈΠ΅ ΠΊΠΎΠ»Π΅Ρ. ΠΠ°Π²Π»Π΅Π½ΠΈΠ΅ ΠΆΠΈΠ΄ΠΊΠΎΡΡΠΈ ΠΏΡΠΈ ΡΠΎΡΠΌΠΎΠΆΠ΅Π½ΠΈΠΈ ΠΌΠΎΠΆΠ΅Ρ Π΄ΠΎΡΡΠΈΠ³Π°ΡΡ 10-15 ΠΠΠ°.
ΠΡΠΈ ΠΎΠΊΠΎΠ½ΡΠ°Π½ΠΈΠΈ ΡΠΎΡΠΌΠΎΠΆΠ΅Π½ΠΈΡ (ΠΎΡΠΏΡΡΠΊΠ°Π½ΠΈΠΈ ΡΠΎΡΠΌΠΎΠ·Π½ΠΎΠΉ ΠΏΠ΅Π΄Π°Π»ΠΈ), ΠΏΠ΅Π΄Π°Π»Ρ ΠΏΠΎΠ΄ Π²ΠΎΠ·Π΄Π΅ΠΉΡΡΠ²ΠΈΠ΅ΠΌ Π²ΠΎΠ·Π²ΡΠ°ΡΠ½ΠΎΠΉ ΠΏΡΡΠΆΠΈΠ½Ρ ΠΏΠ΅ΡΠ΅ΠΌΠ΅ΡΠ°Π΅ΡΡΡ Π² ΠΈΡΡ ΠΎΠ΄Π½ΠΎΠ΅ ΠΏΠΎΠ»ΠΎΠΆΠ΅Π½ΠΈΠ΅. Π ΠΈΡΡ ΠΎΠ΄Π½ΠΎΠ΅ ΠΏΠΎΠ»ΠΎΠΆΠ΅Π½ΠΈΠ΅ ΠΏΠ΅ΡΠ΅ΠΌΠ΅ΡΠ°Π΅ΡΡΡ ΠΏΠΎΡΡΠ΅Π½Ρ Π³Π»Π°Π²Π½ΠΎΠ³ΠΎ ΡΠΎΡΠΌΠΎΠ·Π½ΠΎΠ³ΠΎ ΡΠΈΠ»ΠΈΠ½Π΄ΡΠ°. ΠΡΡΠΆΠΈΠ½Π½ΡΠ΅ ΡΠ»Π΅ΠΌΠ΅Π½ΡΡ ΠΎΡΠ²ΠΎΠ΄ΡΡ ΠΊΠΎΠ»ΠΎΠ΄ΠΊΠΈ ΠΎΡ Π΄ΠΈΡΠΊΠΎΠ² (Π±Π°ΡΠ°Π±Π°Π½ΠΎΠ²). Π’ΠΎΡΠΌΠΎΠ·Π½Π°Ρ ΠΆΠΈΠ΄ΠΊΠΎΡΡΡ ΠΈΠ· ΠΊΠΎΠ»Π΅ΡΠ½ΡΡ ΡΠΈΠ»ΠΈΠ½Π΄ΡΠΎΠ² ΠΏΠΎ ΡΡΡΠ±ΠΎΠΏΡΠΎΠ²ΠΎΠ΄Π°ΠΌ Π²ΡΡΠ΅ΡΠ½ΡΠ΅ΡΡΡ Π² Π³Π»Π°Π²Π½ΡΠΉ ΡΠΎΡΠΌΠΎΠ·Π½ΠΎΠΉ ΡΠΈΠ»ΠΈΠ½Π΄Ρ. ΠΠ°Π²Π»Π΅Π½ΠΈΠ΅ Π² ΡΠΈΡΡΠ΅ΠΌΠ΅ ΠΏΠ°Π΄Π°Π΅Ρ.
Β
ΠΡΠΈΠ²ΠΎΠ΄ ΡΠΎΡΠΌΠΎΠ·Π½ΠΎΠΉ ΡΠΈΡΡΠ΅ΠΌΡ
Β
Π’ΠΎΡΠΌΠΎΠ·Π½ΡΡ ΡΠΈΡΡΠ΅ΠΌΡ Ρ Π³ΠΈΠ΄ΡΠ°Π²Π»ΠΈΡΠ΅ΡΠΊΠΈΠΌ ΠΏΡΠΈΠ²ΠΎΠ΄ΠΎΠΌ ΡΠΎΡΠΌΠΎΠ·ΠΎΠ² ΠΏΡΠΈΠΌΠ΅Π½ΡΡΡ Π½Π° Π²ΡΠ΅Ρ Π»Π΅Π³ΠΊΠΎΠ²ΡΡ ΠΈ Π½Π΅ΠΊΠΎΡΠΎΡΡΡ Π³ΡΡΠ·ΠΎΠ²ΡΡ Π°Π²ΡΠΎΠΌΠΎΠ±ΠΈΠ»ΡΡ . ΠΠ½Π° Π²ΡΠΏΠΎΠ»Π½ΡΠ΅Ρ ΠΎΠ΄Π½ΠΎΠ²ΡΠ΅ΠΌΠ΅Π½Π½ΠΎ ΡΡΠ½ΠΊΡΠΈΠΈ ΡΠ°Π±ΠΎΡΠ΅ΠΉ, Π·Π°ΠΏΠ°ΡΠ½ΠΎΠΉ ΠΈ ΡΡΠΎΡΠ½ΠΎΡΠ½ΠΎΠΉ ΡΠΈΡΡΠ΅ΠΌ. Π§ΡΠΎΠ±Ρ ΠΏΠΎΠ²ΡΡΠΈΡΡ Π½Π°Π΄Π΅ΠΆΠ½ΠΎΡΡΡ ΡΠΎΡΠΌΠΎΠ·Π½ΠΎΠΉ ΡΠΈΡΡΠ΅ΠΌΡ Π½Π° Π»Π΅Π³ΠΊΠΎΠ²ΡΡ Π°Π²ΡΠΎΠΌΠΎΠ±ΠΈΠ»ΡΡ ΠΠΠ, ΠΠΠΠ, ΠΠΠ ΠΏΡΠΈΠΌΠ΅Π½ΡΡΡ Π΄Π²ΡΡ ΠΊΠΎΠ½ΡΡΡΠ½ΡΠΉ Π³ΠΈΠ΄ΡΠ°Π²Π»ΠΈΡΠ΅ΡΠΊΠΈΠΉ ΠΏΡΠΈΠ²ΠΎΠ΄, ΠΊΠΎΡΠΎΡΡΠΉ ΡΠΎΡΡΠΎΠΈΡ ΠΈΠ· Π΄Π²ΡΡ Π½Π΅Π·Π°Π²ΠΈΡΠΈΠΌΡΡ ΠΏΡΠΈΠ²ΠΎΠ΄ΠΎΠ², Π΄Π΅ΠΉΡΡΠ²ΡΡΡΠΈΡ ΠΎΡ ΠΎΠ΄Π½ΠΎΠ³ΠΎ Π³Π»Π°Π²Π½ΠΎΠ³ΠΎ ΡΠΎΡΠΌΠΎΠ·Π½ΠΎΠ³ΠΎ ΡΠΈΠ»ΠΈΠ½Π΄ΡΠ° Π½Π° ΡΠΎΡΠΌΠΎΠ·Π½ΡΠ΅ ΠΌΠ΅Ρ Π°Π½ΠΈΠ·ΠΌΡ ΠΎΡΠ΄Π΅Π»ΡΠ½ΠΎ ΠΏΠ΅ΡΠ΅Π΄Π½ΠΈΡ ΠΈ Π·Π°Π΄Π½ΠΈΡ ΠΊΠΎΠ»Π΅Ρ. ΠΠ° Π°Π²ΡΠΎΠΌΠΎΠ±ΠΈΠ»Π΅ ΠΠΠ-24 Ρ ΡΡΠΎΠΉ ΠΆΠ΅ ΡΠ΅Π»ΡΡ ΠΏΡΠΈΠΌΠ΅Π½ΡΡΡ Π² ΠΏΡΠΈΠ²ΠΎΠ΄Π΅ ΡΠΎΡΠΌΠΎΠ·ΠΎΠ² ΡΠ°Π·Π΄Π΅Π»ΠΈΡΠ΅Π»Ρ, ΠΏΠΎΠ·Π²ΠΎΠ»ΡΡΡΠΈΠΉ ΠΈΡΠΏΠΎΠ»ΡΠ·ΠΎΠ²Π°ΡΡ ΠΈΡΠΏΡΠ°Π²Π½ΡΡ ΡΠ°ΡΡΡ ΡΠΎΡΠΌΠΎΠ·Π½ΠΎΠΉ ΡΠΈΡΡΠ΅ΠΌΡ Π² ΠΊΠ°ΡΠ΅ΡΡΠ²Π΅ Π·Π°ΠΏΠ°ΡΠ½ΠΎΠΉ, Π΅ΡΠ»ΠΈ Π² Π΄ΡΡΠ³ΠΎΠΉ ΡΠ°ΡΡΠΈ ΡΠΎΡΠΌΠΎΠ·Π½ΠΎΠΉ ΡΠΈΡΡΠ΅ΠΌΡ ΠΏΡΠΎΠΈΠ·ΠΎΡΠ»ΠΎ Π½Π°ΡΡΡΠ΅Π½ΠΈΠ΅ Π³Π΅ΡΠΌΠ΅ΡΠΈΡΠ½ΠΎΡΡΠΈ.
ΠΠ»Π°Π²Π½ΡΠΉ ΡΠΎΡΠΌΠΎΠ·Π½ΠΎΠΉ ΡΠΈΠ»ΠΈΠ½Π΄Ρ ΠΏΡΠΈΠ²ΠΎΠ΄ΠΈΡΡΡ Π² Π΄Π΅ΠΉΡΡΠ²ΠΈΠ΅ ΠΎΡ ΡΠΎΡΠΌΠΎΠ·Π½ΠΎΠΉ ΠΏΠ΅Π΄Π°Π»ΠΈ, ΡΡΡΠ°Π½ΠΎΠ²Π»Π΅Π½Π½ΠΎΠΉ Π½Π° ΠΊΡΠΎΠ½ΡΡΠ΅ΠΉΠ½Π΅ ΠΊΡΠ·ΠΎΠ²Π°. ΠΠΎΡΠΏΡΡ 2 Π³Π»Π°Π²Π½ΠΎΠ³ΠΎ ΡΠΈΠ»ΠΈΠ½Π΄ΡΠ° Π²ΡΠΏΠΎΠ»Π½Π΅Π½ ΡΠΎΠ²ΠΌΠ΅ΡΡΠ½ΠΎ Ρ ΡΠ΅Π·Π΅ΡΠ²ΡΠ°ΡΠΎΠΌ Π΄Π»Ρ ΡΠΎΡΠΌΠΎΠ·Π½ΠΎΠΉ ΠΆΠΈΠ΄ΠΊΠΎΡΡΠΈ. ΠΠ½ΡΡΡΠΈ ΡΠΈΠ»ΠΈΠ½Π΄ΡΠ° Π½Π°Ρ ΠΎΠ΄ΠΈΡΡΡ Π°Π»ΡΠΌΠΈΠ½ΠΈΠ΅Π²ΡΠΉ ΠΏΠΎΡΡΠ΅Π½Ρ 10 Ρ ΡΠΏΠ»ΠΎΡΠ½ΠΈΡΠ΅Π»ΡΠ½ΡΠΌ ΡΠ΅Π·ΠΈΠ½ΠΎΠ²ΡΠΌ ΠΊΠΎΠ»ΡΡΠΎΠΌ. ΠΠΎΡΡΠ΅Π½Ρ ΠΌΠΎΠΆΠ΅Ρ ΠΏΠ΅ΡΠ΅ΠΌΠ΅ΡΠ°ΡΡΡΡ ΠΏΠΎΠ΄ Π΄Π΅ΠΉΡΡΠ²ΠΈΠ΅ΠΌ ΡΠΎΠ»ΠΊΠ°ΡΠ΅Π»Ρ 1, ΡΠΎΠ΅Π΄ΠΈΠ½Π΅Π½Π½ΠΎΠ³ΠΎ ΡΠ°ΡΠ½ΠΈΡΠ½ΠΎ Ρ ΠΏΠ΅Π΄Π°Π»ΡΡ.
ΠΠ»Π°Π²Π½ΡΠΉ ΡΠΎΡΠΌΠΎΠ·Π½ΠΎΠΉ ΡΠΈΠ»ΠΈΠ½Π΄Ρ
Β
ΠΠ½ΠΈΡΠ΅ ΠΏΠΎΡΡΠ½Ρ ΡΠΏΠΈΡΠ°Π΅ΡΡΡ ΡΠ΅ΡΠ΅Π· ΡΡΠ°Π»ΡΠ½ΡΡ ΡΠ°ΠΉΠ±Ρ Π² ΡΠΏΠ»ΠΎΡΠ½ΠΈΡΠ΅Π»ΡΠ½ΡΡ ΠΌΠ°Π½ΠΆΠ΅ΡΡ 9, ΠΏΡΠΈΠΆΠΈΠΌΠ°Π΅ΠΌΡΡ ΠΏΡΡΠΆΠΈΠ½ΠΎΠΉ 8. ΠΠ½Π° ΠΆΠ΅ ΠΏΡΠΈΠΆΠΈΠΌΠ°Π΅Ρ ΠΊ Π³Π½Π΅Π·Π΄Ρ Π²ΠΏΡΡΠΊΠ½ΠΎΠΉ ΠΊΠ»Π°ΠΏΠ°Π½ 7, Π²Π½ΡΡΡΠΈ ΠΊΠΎΡΠΎΡΠΎΠ³ΠΎ ΡΠ°ΡΠΏΠΎΠ»ΠΎΠΆΠ΅Π½ Π½Π°Π³Π½Π΅ΡΠ°ΡΠ΅Π»ΡΠ½ΡΠΉ ΠΊΠ»Π°ΠΏΠ°Π½ 6.
ΠΠ½ΡΡΡΠ΅Π½Π½ΡΡ ΠΏΠΎΠ»ΠΎΡΡΡ ΡΠΈΠ»ΠΈΠ½Π΄ΡΠ° ΡΠΎΠΎΠ±ΡΠ°Π΅ΡΡΡ Ρ ΡΠ΅Π·Π΅ΡΠ²ΡΠ°ΡΠΎΠΌ ΠΊΠΎΠΌΠΏΠ΅Π½ΡΠ°ΡΠΈΠΎΠ½Π½ΡΠΌ 4 ΠΈ ΠΏΠ΅ΡΠ΅ΠΏΡΡΠΊΠ½ΡΠΌ 3 ΠΎΡΠ²Π΅ΡΡΡΠΈΡΠΌΠΈ. Π ΠΊΡΡΡΠΊΠ΅ ΡΠ΅Π·Π΅ΡΠ²ΡΠ°ΡΠ° ΡΠ΄Π΅Π»Π°Π½ΠΎ ΡΠ΅Π·ΡΠ±ΠΎΠ²ΠΎΠ΅ ΠΎΡΠ²Π΅ΡΡΡΠΈΠ΅ Π΄Π»Ρ Π·Π°Π»ΠΈΠ²ΠΊΠΈ ΠΆΠΈΠ΄ΠΊΠΎΡΡΠΈ, Π·Π°ΠΊΡΡΠ²Π°Π΅ΠΌΠΎΠ΅ ΠΏΡΠΎΠ±ΠΊΠΎΠΉ 5. ΠΡΠΈ Π½Π°ΠΆΠ°ΡΠΈΠΈ Π½Π° ΡΠΎΡΠΌΠΎΠ·Π½ΡΡ ΠΏΠ΅Π΄Π°Π»Ρ ΠΏΠΎΠ΄ Π΄Π΅ΠΉΡΡΠ²ΠΈΠ΅ΠΌ ΡΠΎΠ»ΠΊΠ°ΡΠ΅Π»Ρ 1 ΠΏΠΎΡΡΠ΅Π½Ρ Ρ ΠΌΠ°Π½ΠΆΠ΅ΡΠΎΠΉ ΠΏΠ΅ΡΠ΅ΠΌΠ΅ΡΠ°Π΅ΡΡΡ ΠΈ Π·Π°ΠΊΡΡΠ²Π°Π΅Ρ ΠΎΡΠ²Π΅ΡΡΡΠΈΠ΅ 4, Π²ΡΠ»Π΅Π΄ΡΡΠ²ΠΈΠ΅ ΡΠ΅Π³ΠΎ Π΄Π°Π²Π»Π΅Π½ΠΈΠ΅ ΠΆΠΈΠ΄ΠΊΠΎΡΡΠΈ Π² ΡΠΈΠ»ΠΈΠ½Π΄ΡΠ΅ ΡΠ²Π΅Π»ΠΈΡΠΈΠ²Π°Π΅ΡΡΡ, ΠΎΡΠΊΡΡΠ²Π°Π΅ΡΡΡ Π½Π°Π³Π½Π΅ΡΠ°ΡΠ΅Π»ΡΠ½ΡΠΉ ΠΊΠ»Π°ΠΏΠ°Π½ 6 ΠΈ ΠΆΠΈΠ΄ΠΊΠΎΡΡΡ ΠΏΠΎΡΡΡΠΏΠ°Π΅Ρ ΠΊ ΡΠΎΡΠΌΠΎΠ·Π½ΡΠΌ ΠΌΠ΅Ρ Π°Π½ΠΈΠ·ΠΌΠ°ΠΌ. ΠΡΠ»ΠΈ ΠΎΡΠΏΡΡΡΠΈΡΡ ΠΏΠ΅Π΄Π°Π»Ρ, ΡΠΎ Π΄Π°Π²Π»Π΅Π½ΠΈΠ΅ ΠΆΠΈΠ΄ΠΊΠΎΡΡΠΈ Π² ΠΏΡΠΈΠ²ΠΎΠ΄Π΅ ΡΠ½ΠΈΠΆΠ°Π΅ΡΡΡ, ΠΈ ΠΎΠ½Π° ΠΏΠ΅ΡΠ΅ΡΠ΅ΠΊΠ°Π΅Ρ ΠΎΠ±ΡΠ°ΡΠ½ΠΎ Π² ΡΠΈΠ»ΠΈΠ½Π΄Ρ. ΠΡΠΈ ΡΡΠΎΠΌ ΠΈΠ·Π±ΡΡΠΎΠΊ ΠΆΠΈΠ΄ΠΊΠΎΡΡΠΈ ΡΠ΅ΡΠ΅Π· ΠΊΠΎΠΌΠΏΠ΅Π½ΡΠ°ΡΠΈΠΎΠ½Π½ΠΎΠ΅ ΠΎΡΠ²Π΅ΡΡΡΠΈΠ΅ 4 Π²ΠΎΠ·Π²ΡΠ°ΡΠ°Π΅ΡΡΡ Π² ΡΠ΅Π·Π΅ΡΠ²ΡΠ°Ρ. Π ΡΠΎ ΠΆΠ΅ Π²ΡΠ΅ΠΌΡ ΠΏΡΡΠΆΠΈΠ½Π° 8, Π΄Π΅ΠΉΡΡΠ²ΡΡ Π½Π° ΠΊΠ»Π°ΠΏΠ°Π½ 7, ΠΏΠΎΠ΄Π΄Π΅ΡΠΆΠΈΠ²Π°Π΅Ρ Π² ΡΠΈΡΡΠ΅ΠΌΠ΅ ΠΏΡΠΈΠ²ΠΎΠ΄Π° Π½Π΅Π±ΠΎΠ»ΡΡΠΎΠ΅ ΠΈΠ·Π±ΡΡΠΎΡΠ½ΠΎΠ΅ Π΄Π°Π²Π»Π΅Π½ΠΈΠ΅ ΠΏΠΎΡΠ»Π΅ ΠΏΠΎΠ»Π½ΠΎΠ³ΠΎ ΠΎΡΠΏΡΡΠΊΠ°Π½ΠΈΡ ΠΏΠ΅Π΄Π°Π»ΠΈ.
ΠΡΠΈ ΡΠ΅Π·ΠΊΠΎΠΌ ΠΎΡΠΏΡΡΠΊΠ°Π½ΠΈΠΈ ΠΏΠ΅Π΄Π°Π»ΠΈ ΠΏΠΎΡΡΠ΅Π½Ρ 10 ΠΎΡΡ ΠΎΠ΄ΠΈΡ Π² ΠΊΡΠ°ΠΉΠ½Π΅Π΅ ΠΏΠΎΠ»ΠΎΠΆΠ΅Π½ΠΈΠ΅ Π±ΡΡΡΡΠ΅Π΅, ΡΠ΅ΠΌ ΠΏΠ΅ΡΠ΅ΠΌΠ΅ΡΠ°Π΅ΡΡΡ ΠΌΠ°Π½ΠΆΠ΅ΡΠ° 9, ΠΈ ΠΆΠΈΠ΄ΠΊΠΎΡΡΡ Π½Π°ΡΠΈΠ½Π°Π΅Ρ Π·Π°ΠΏΠΎΠ»Π½ΡΡΡ ΠΎΡΠ²ΠΎΠ±ΠΎΠΆΠ΄Π°ΡΡΡΡΡΡ ΠΏΠΎΠ»ΠΎΡΡΡ ΡΠΈΠ»ΠΈΠ½Π΄ΡΠ°. ΠΠ΄Π½ΠΎΠ²ΡΠ΅ΠΌΠ΅Π½Π½ΠΎ Π² ΠΏΠΎΠ»ΠΎΡΡΠΈ Π²ΠΎΠ·Π½ΠΈΠΊΠ°Π΅Ρ ΡΠ°Π·ΡΠ΅ΠΆΠ΅Π½ΠΈΠ΅. Π§ΡΠΎΠ±Ρ ΡΡΡΡΠ°Π½ΠΈΡΡ Π΅Π³ΠΎ, Π² Π΄Π½ΠΈΡΠ΅ ΠΏΠΎΡΡΠ½Ρ ΠΈΠΌΠ΅ΡΡΡΡ ΠΎΡΠ²Π΅ΡΡΡΠΈΡ, ΡΠΎΠΎΠ±ΡΠ°ΡΡΠΈΠ΅ ΡΠ°Π±ΠΎΡΡΡ ΠΏΠΎΠ»ΠΎΡΡΡ ΡΠΈΠ»ΠΈΠ½Π΄ΡΠ° Ρ Π²Π½ΡΡΡΠ΅Π½Π½Π΅ΠΉ ΠΏΠΎΠ»ΠΎΡΡΡΡ ΠΏΠΎΡΡΠ½Ρ. Π§Π΅ΡΠ΅Π· Π½ΠΈΡ ΠΆΠΈΠ΄ΠΊΠΎΡΡΡ ΠΏΠ΅ΡΠ΅ΡΠ΅ΠΊΠ°Π΅Ρ Π² Π·ΠΎΠ½Ρ ΡΠ°Π·ΡΠ΅ΠΆΠ΅Π½ΠΈΡ, ΡΠ΅ΠΌ ΠΈ ΡΡΡΡΠ°Π½ΡΠ΅ΡΡΡ Π½Π΅ΠΆΠ΅Π»Π°ΡΠ΅Π»ΡΠ½ΡΠΉ ΠΏΠΎΠ΄ΡΠΎΡ Π²ΠΎΠ·Π΄ΡΡ Π° Π² ΡΠΈΠ»ΠΈΠ½Π΄Ρ. ΠΡΠΈ Π΄Π°Π»ΡΠ½Π΅ΠΉΡΠ΅ΠΌ ΠΏΠ΅ΡΠ΅ΠΌΠ΅ΡΠ΅Π½ΠΈΠΈ ΠΌΠ°Π½ΠΆΠ΅ΡΡ ΠΆΠΈΠ΄ΠΊΠΎΡΡΡ Π²ΡΡΠ΅ΡΠ½ΡΠ΅ΡΡΡ Π²ΠΎ Π²Π½ΡΡΡΠ΅Π½Π½ΡΡ ΠΏΠΎΠ»ΠΎΡΡΡ ΠΏΠΎΡΡΠ½Ρ ΠΈ Π΄Π°Π»Π΅Π΅ ΡΠ΅ΡΠ΅Π· ΠΏΠ΅ΡΠ΅ΠΏΡΡΠΊΠ½ΠΎΠ΅ ΠΎΡΠ²Π΅ΡΡΡΠΈΠ΅ 3 Π² ΡΠ΅Π·Π΅ΡΠ²ΡΠ°Ρ.
ΠΠΎΠ»Π΅ΡΠ½ΡΠΉ ΡΠΎΡΠΌΠΎΠ·Π½ΠΎΠΉ ΡΠΈΠ»ΠΈΠ½Π΄Ρ ΡΠΎΡΠΌΠΎΠ·Π½ΠΎΠ³ΠΎ ΠΌΠ΅Ρ Π°Π½ΠΈΠ·ΠΌΠ° Π·Π°Π΄Π½Π΅Π³ΠΎ ΠΊΠΎΠ»Π΅ΡΠ° ΡΠΎΡΡΠΎΠΈΡ ΠΈΠ· ΡΡΠ³ΡΠ½Π½ΠΎΠ³ΠΎ ΠΊΠΎΡΠΏΡΡΠ°, Π²Π½ΡΡΡΠΈ ΠΊΠΎΡΠΎΡΠΎΠ³ΠΎ ΠΏΠΎΠΌΠ΅ΡΠ΅Π½Ρ Π΄Π²Π° Π°Π»ΡΠΌΠΈΠ½ΠΈΠ΅Π²ΡΡ ΠΏΠΎΡΡΠ½Ρ Ρ ΡΠΏΠ»ΠΎΡΠ½ΠΈΡΠ΅Π»ΡΠ½ΡΠΌΠΈ ΡΠ΅Π·ΠΈΠ½ΠΎΠ²ΡΠΌΠΈ ΠΌΠ°Π½ΠΆΠ΅ΡΠ°ΠΌΠΈ. Π ΡΠΎΡΡΠΎΠ²ΡΡ ΠΏΠΎΠ²Π΅ΡΡ Π½ΠΎΡΡΡ ΠΏΠΎΡΡΠ½Π΅ΠΉ Π΄Π»Ρ ΡΠΌΠ΅Π½ΡΡΠ΅Π½ΠΈΡ ΠΈΠ·Π½Π°ΡΠΈΠ²Π°Π½ΠΈΡ Π²ΡΡΠ°Π²Π»Π΅Π½Ρ ΡΡΠ°Π»ΡΠ½ΡΠ΅ ΡΡΡ Π°ΡΠΈ. Π¦ΠΈΠ»ΠΈΠ½Π΄Ρ Ρ ΠΎΠ±Π΅ΠΈΡ ΡΡΠΎΡΠΎΠ½ Π·Π°ΠΊΡΡΡ Π·Π°ΡΠΈΡΠ½ΡΠΌΠΈ ΡΠ΅Π·ΠΈΠ½ΠΎΠ²ΡΠΌΠΈ ΡΠ΅Ρ Π»Π°ΠΌΠΈ. ΠΠΈΠ΄ΠΊΠΎΡΡΡ Π² ΠΏΠΎΠ»ΠΎΡΡΡ ΡΠΈΠ»ΠΈΠ½Π΄ΡΠ° ΠΏΠΎΡΡΡΠΏΠ°Π΅Ρ ΡΠ΅ΡΠ΅Π· ΠΎΡΠ²Π΅ΡΡΡΠΈΠ΅, Π² ΠΊΠΎΡΠΎΡΠΎΠ΅ Π²Π²Π΅ΡΠ½ΡΡ ΠΏΡΠΈΡΠΎΠ΅Π΄ΠΈΠ½ΠΈΡΠ΅Π»ΡΠ½ΡΠΉ ΡΡΡΡΠ΅Ρ. ΠΠ»Ρ Π²ΡΠΏΡΡΠΊΠ° Π²ΠΎΠ·Π΄ΡΡ Π° ΠΈΠ· ΠΏΠΎΠ»ΠΎΡΡΠΈ ΡΠΈΠ»ΠΈΠ½Π΄ΡΠ° ΠΈΡΠΏΠΎΠ»ΡΠ·ΡΠ΅ΡΡΡ ΠΊΠ»Π°ΠΏΠ°Π½ ΠΏΡΠΎΠΊΠ°ΡΠΊΠΈ, Π·Π°ΠΊΡΡΡΡΠΉ ΡΠ½Π°ΡΡΠΆΠΈ ΡΠ΅Π·ΠΈΠ½ΠΎΠ²ΡΠΌ ΠΊΠΎΠ»ΠΏΠ°ΡΠΊΠΎΠΌ. Π ΡΠΈΠ»ΠΈΠ½Π΄ΡΠ΅ ΠΈΠΌΠ΅Π΅ΡΡΡ ΡΡΡΡΠΎΠΉΡΡΠ²ΠΎ Π΄Π»Ρ ΡΠ΅Π³ΡΠ»ΠΈΡΠΎΠ²ΠΊΠΈ Π·Π°Π·ΠΎΡΠ° ΠΌΠ΅ΠΆΠ΄Ρ ΠΊΠΎΠ»ΠΎΠ΄ΠΊΠ°ΠΌΠΈ ΠΈ Π±Π°ΡΠ°Π±Π°Π½ΠΎΠΌ, ΠΏΡΠ΅Π΄ΡΡΠ°Π²Π»ΡΡΡΠ΅Π΅ ΡΠΎΠ±ΠΎΠΉ ΠΏΡΡΠΆΠΈΠ½Π½ΠΎΠ΅ ΡΠΏΠΎΡΠ½ΠΎΠ΅ ΠΊΠΎΠ»ΡΡΠΎ, Π²ΡΡΠ°Π²Π»Π΅Π½Π½ΠΎΠ΅ Ρ Π½Π°ΡΡΠ³ΠΎΠΌ Π² ΠΊΠΎΡΠΏΡΡ ΡΠΈΠ»ΠΈΠ½Π΄ΡΠ°.
ΠΠΎ Π²ΡΠ΅ΠΌΡ ΡΠΎΡΠΌΠΎΠΆΠ΅Π½ΠΈΡ Π²Π½ΡΡΡΠΈ ΡΠΈΠ»ΠΈΠ½Π΄ΡΠ° ΡΠΎΠ·Π΄Π°Π΅ΡΡΡ Π΄Π°Π²Π»Π΅Π½ΠΈΠ΅ ΠΆΠΈΠ΄ΠΊΠΎΡΡΠΈ, ΠΏΠΎΠ΄ Π΄Π΅ΠΉΡΡΠ²ΠΈΠ΅ΠΌ ΠΊΠΎΡΠΎΡΠΎΠ³ΠΎ ΠΏΠΎΡΡΠ΅Π½Ρ ΠΏΠ΅ΡΠ΅ΠΌΠ΅ΡΠ°Π΅ΡΡΡ ΠΈ ΠΎΡΠΆΠΈΠΌΠ°Π΅Ρ ΡΠΎΡΠΌΠΎΠ·Π½ΡΡ ΠΊΠΎΠ»ΠΎΠ΄ΠΊΡ. ΠΠΎ ΠΌΠ΅ΡΠ΅ ΠΈΠ·Π½Π°ΡΠΈΠ²Π°Π½ΠΈΡ ΡΡΠΈΠΊΡΠΈΠΎΠ½Π½ΠΎΠΉ Π½Π°ΠΊΠ»Π°Π΄ΠΊΠΈ Ρ ΠΎΠ΄ ΠΏΠΎΡΡΠ½Ρ ΠΏΡΠΈ ΡΠΎΡΠΌΠΎΠΆΠ΅Π½ΠΈΠΈ ΡΡΠ°Π½ΠΎΠ²ΠΈΡΡΡ Π±ΠΎΠ»ΡΡΠ΅ ΠΈ Π½Π°ΡΡΡΠΏΠ°Π΅Ρ ΠΌΠΎΠΌΠ΅Π½Ρ, ΠΊΠΎΠ³Π΄Π° ΠΎΠ½ ΡΠ²ΠΎΠΈΠΌ Π±ΡΡΡΠΈΠΊΠΎΠΌ ΠΏΠ΅ΡΠ΅Π΄Π²ΠΈΠ³Π°Π΅Ρ ΡΠΏΠΎΡΠ½ΠΎΠ΅ ΠΊΠΎΠ»ΡΡΠΎ, ΠΏΡΠ΅ΠΎΠ΄ΠΎΠ»Π΅Π²Π°Ρ ΡΡΠΈΠ»ΠΈΠ΅ Π΅Π³ΠΎ ΠΏΠΎΡΠ°Π΄ΠΊΠΈ. ΠΡΠΈ ΠΎΠ±ΡΠ°ΡΠ½ΠΎΠΌ ΠΏΠ΅ΡΠ΅ΠΌΠ΅ΡΠ΅Π½ΠΈΠΈ ΠΊΠΎΠ»ΠΎΠ΄ΠΊΠΈ ΠΏΠΎΠ΄ Π΄Π΅ΠΉΡΡΠ²ΠΈΠ΅ΠΌ ΡΡΡΠΆΠ½ΠΎΠΉ ΠΏΡΡΠΆΠΈΠ½Ρ ΡΠΏΠΎΡΠ½ΠΎΠ΅ ΠΊΠΎΠ»ΡΡΠΎ ΠΎΡΡΠ°Π΅ΡΡΡ Π² Π½ΠΎΠ²ΠΎΠΌ ΠΏΠΎΠ»ΠΎΠΆΠ΅Π½ΠΈΠΈ, ΡΠ°ΠΊ ΠΊΠ°ΠΊ ΡΡΠΈΠ»ΠΈΡ ΡΡΡΠΆΠ½ΠΎΠΉ ΠΏΡΡΠΆΠΈΠ½Ρ Π½Π΅Π΄ΠΎΡΡΠ°ΡΠΎΡΠ½ΠΎ, ΡΡΠΎΠ±Ρ ΡΠ΄Π²ΠΈΠ½ΡΡΡ Π΅Π³ΠΎ Π½Π°Π·Π°Π΄. Π’Π°ΠΊΠΈΠΌ ΠΎΠ±ΡΠ°Π·ΠΎΠΌ, Π΄ΠΎΡΡΠΈΠ³Π°Π΅ΡΡΡ ΠΊΠΎΠΌΠΏΠ΅Π½ΡΠ°ΡΠΈΡ ΠΈΠ·Π½ΠΎΡΠ° Π½Π°ΠΊΠ»Π°Π΄ΠΎΠΊ ΠΈ Π°Π²ΡΠΎΠΌΠ°ΡΠΈΡΠ΅ΡΠΊΠΈ ΡΡΡΠ°Π½Π°Π²Π»ΠΈΠ²Π°Π΅ΡΡΡ ΠΌΠΈΠ½ΠΈΠΌΠ°Π»ΡΠ½ΡΠΉ Π·Π°Π·ΠΎΡ ΠΌΠ΅ΠΆΠ΄Ρ ΠΊΠΎΠ»ΠΎΠ΄ΠΊΠ°ΠΌΠΈ ΠΈ Π±Π°ΡΠ°Π±Π°Π½ΠΎΠΌ.
ΠΠΎΠ»Π΅ΡΠ½ΡΠΉ ΡΠΈΠ»ΠΈΠ½Π΄Ρ ΡΠΎΡΠΌΠΎΠ·Π½ΠΎΠ³ΠΎ ΠΌΠ΅Ρ Π°Π½ΠΈΠ·ΠΌΠ° ΠΏΠ΅ΡΠ΅Π΄Π½Π΅Π³ΠΎ ΠΊΠΎΠ»Π΅ΡΠ° Π΄Π΅ΠΉΡΡΠ²ΡΠ΅Ρ ΡΠΎΠ»ΡΠΊΠΎ Π½Π° ΠΎΠ΄Π½Ρ ΠΊΠΎΠ»ΠΎΠ΄ΠΊΡ, ΠΏΠΎΡΡΠΎΠΌΡ ΠΎΡΠ»ΠΈΡΠ°Π΅ΡΡΡ ΠΎΡ ΠΊΠΎΠ»Π΅ΡΠ½ΠΎΠ³ΠΎ ΡΠΈΠ»ΠΈΠ½Π΄ΡΠ° Π·Π°Π΄Π½Π΅Π³ΠΎ ΠΊΠΎΠ»Π΅ΡΠ° Π²Π½Π΅ΡΠ½ΠΈΠΌΠΈ ΡΠ°Π·ΠΌΠ΅ΡΠ°ΠΌΠΈ ΠΈ ΠΊΠΎΠ»ΠΈΡΠ΅ΡΡΠ²ΠΎΠΌ ΠΏΠΎΡΡΠ½Π΅ΠΉ: Π² ΡΠΈΠ»ΠΈΠ½Π΄ΡΠ΅ Π·Π°Π΄Π½Π΅Π³ΠΎ ΠΊΠΎΠ»Π΅ΡΠ° ΡΠ°Π·ΠΌΠ΅ΡΠ΅Π½Ρ Π΄Π²Π° ΠΏΠΎΡΡΠ½Ρ, Π² ΡΠΈΠ»ΠΈΠ½Π΄ΡΠ΅ ΠΏΠ΅ΡΠ΅Π΄Π½Π΅Π³ΠΎ — ΠΎΠ΄ΠΈΠ½. ΠΡΠ΅ ΠΎΡΡΠ°Π»ΡΠ½ΡΠ΅ Π΄Π΅ΡΠ°Π»ΠΈ ΡΠΈΠ»ΠΈΠ½Π΄ΡΠΎΠ², Π·Π° ΠΈΡΠΊΠ»ΡΡΠ΅Π½ΠΈΠ΅ΠΌ ΠΊΠΎΡΠΏΡΡΠ°, ΠΎΠ΄ΠΈΠ½Π°ΠΊΠΎΠ²Ρ ΠΏΠΎ ΠΊΠΎΠ½ΡΡΡΡΠΊΡΠΈΠΈ.
Β
Β
Π£ΡΡΡΠΎΠΉΡΡΠ²ΠΎ ΠΠΠ
ΠΠ΄ΠΈΠ½ΡΡΠ²Π΅Π½Π½ΡΠΌ Π²ΠΈΠ΄ΠΈΠΌΡΠΌ ΡΠ»Π΅ΠΌΠ΅Π½ΡΠΎΠΌ Π°Π²ΡΠΎΠΌΠΎΠ±ΠΈΠ»ΡΠ½ΠΎΠΉ Π±Π°ΡΠ°ΡΠ΅ΠΈ ΡΠ²Π»ΡΠ΅ΡΡΡ ΠΊΠΎΡΠΏΡΡ, ΠΊΠΎΡΠΎΡΡΠΉ ΠΎΠ±Π΅ΡΠΏΠ΅ΡΠΈΠ²Π°Π΅Ρ ΡΠ΅Π»ΠΎΡΡΠ½ΠΎΡΡΡ ΠΈ ΠΎΠ±ΡΠ½ΠΎΡΡΡ ΠΊΠΎΠ½ΡΡΡΡΠΊΡΠΈΠΈ.
Π ΠΏΡΠΈΠ½ΡΠΈΠΏΠ΅, Π½Π°Π·Π²Π°Π½ΠΈΠ΅ Π°ΠΊΠΊΡΠΌΡΠ»ΡΡΠΎΡ Π°Π±ΡΠΎΠ»ΡΡΠ½ΠΎ Π²Π΅ΡΠ½ΠΎ ΠΏΡΠΈΠΌΠ΅Π½ΠΈΡΠ΅Π»ΡΠ½ΠΎ Π»ΠΈΡΡ ΠΊ ΠΎΠ΄Π½ΠΎΠΉ, ΠΎΡΠ΄Π΅Π»ΡΠ½ΠΎ Π²Π·ΡΡΠΎΠΉ ΡΡΠ΅ΠΉΠΊΠ΅, Π° ΠΎΠ±ΡΠ΅Π΄ΠΈΠ½Π΅Π½Π½ΡΠ΅ Π²ΠΎΠ΅Π΄ΠΈΠ½ΠΎ ΠΎΠ½ΠΈ Π΄ΠΎΠ»ΠΆΠ½Ρ ΠΈΠΌΠ΅Π½ΠΎΠ²Π°ΡΡΡΡ Π°ΠΊΠΊΡΠΌΡΠ»ΡΡΠΎΡΠ½ΠΎΠΉ Π±Π°ΡΠ°ΡΠ΅Π΅ΠΉ. Π’Π°ΠΊ, ΡΡΠ°Π½Π΄Π°ΡΡΠ½Π°Ρ 12 Π Π°ΠΊΠΊΡΠΌΡΠ»ΡΡΠΎΡΠ½Π°Ρ Π±Π°ΡΠ°ΡΠ΅Ρ Π΄Π»Ρ Π»Π΅Π³ΠΊΠΎΠ²ΠΎΠ³ΠΎ Π°Π²ΡΠΎΠΌΠΎΠ±ΠΈΠ»Ρ ΠΎΠ±ΡΠ΅Π΄ΠΈΠ½ΡΠ΅Ρ Π² ΡΠ΅Π±Π΅ ΡΠ΅ΡΡΡ ΠΎΡΠ΄Π΅Π»ΡΠ½ΡΡ Π°ΠΊΠΊΡΠΌΡΠ»ΡΡΠΎΡΠΎΠ² (Β«Π±Π°Π½ΠΎΠΊΒ»), ΠΊΠ°ΠΆΠ΄Π°Ρ ΠΈΠ· ΠΊΠΎΡΠΎΡΡΡ Π²ΡΡΠ°Π±Π°ΡΡΠ²Π°Π΅Ρ Π½Π°ΠΏΡΡΠΆΠ΅Π½ΠΈΠ΅ 2 Π.
Π ΠΊΠΎΡΠΏΡΡΡ Π±Π°ΡΠ°ΡΠ΅ΠΈ ΠΏΡΠ΅Π΄ΡΡΠ²Π»ΡΡΡ Π²Π΅ΡΡΠΌΠ° Π²ΡΡΠΎΠΊΠΈΠ΅ ΠΈ ΠΆΠ΅ΡΡΠΊΠΈΠ΅ ΡΡΠ΅Π±ΠΎΠ²Π°Π½ΠΈΡ. ΠΠ½ Π΄ΠΎΠ»ΠΆΠ΅Π½ Π±ΡΡΡ Π½Π΅Π²ΠΎΡΠΏΡΠΈΠΈΠΌΡΠΈΠ²ΡΠΌ ΠΊ Π²ΠΎΠ·Π΄Π΅ΠΉΡΡΠ²ΠΈΡ Π°Π³ΡΠ΅ΡΡΠΈΠ²Π½ΡΠΌ Ρ ΠΈΠΌΠΈΡΠ΅ΡΠΊΠΈΡ ΡΠ΅Π°Π³Π΅Π½ΡΠΎΠ², ΠΏΠ΅ΡΠ΅Π½ΠΎΡΠΈΡΡ Π·Π½Π°ΡΠΈΡΠ΅Π»ΡΠ½ΡΠ΅ ΡΠ΅ΠΌΠΏΠ΅ΡΠ°ΡΡΡΠ½ΡΠ΅ ΠΊΠΎΠ»Π΅Π±Π°Π½ΠΈΡ ΠΈ ΠΎΠ±Π»Π°Π΄Π°ΡΡ Π²ΡΡΠΎΠΊΠΎΠΉ Π²ΠΈΠ±ΡΠΎΡΡΠΎΠΉΠΊΠΎΡΡΡΡ. Π ΠΏΠΎΠ΄Π°Π²Π»ΡΡΡΠ΅ΠΌ Π±ΠΎΠ»ΡΡΠΈΠ½ΡΡΠ²Π΅ ΡΠ»ΡΡΠ°Π΅Π² ΠΊΠΎΡΠΏΡΡ ΠΈΠ·Π³ΠΎΡΠ°Π²Π»ΠΈΠ²Π°ΡΡ ΠΈΠ· ΡΠΎΠ²ΡΠ΅ΠΌΠ΅Π½Π½ΠΎΠ³ΠΎ ΡΠΈΠ½ΡΠ΅ΡΠΈΡΠ΅ΡΠΊΠΎΠ³ΠΎ ΠΌΠ°ΡΠ΅ΡΠΈΠ°Π»Π° β ΠΏΠΎΠ»ΠΈΠΏΡΠΎΠΏΠΈΠ»Π΅Π½Π°.
ΠΠΎΡΠΏΡΡ ΡΠΎΡΡΠΎΠΈΡ ΠΈΠ· Π΄Π²ΡΡ ΡΠ°ΡΡΠ΅ΠΉ: ΠΈΠ· ΠΎΡΠ½ΠΎΠ²Π½ΠΎΠΉ Π³Π»ΡΠ±ΠΎΠΊΠΎΠΉ Π΅ΠΌΠΊΠΎΡΡΠΈ, ΠΈ Π·Π°ΠΊΡΡΠ²Π°ΡΡΠ΅ΠΉ Π΅Π΅ ΠΊΡΡΡΠΊΠΈ. Π Π·Π°Π²ΠΈΡΠΈΠΌΠΎΡΡΠΈ ΠΎΡ ΡΠΈΠΏΠ° ΠΠΠ ΠΊΡΡΡΠΊΠ° ΠΌΠΎΠΆΠ΅Ρ Π±ΡΡΡ ΠΎΡΠ½Π°ΡΠ΅Π½Π° Π³ΠΎΡΠ»ΠΎΠ²ΠΈΠ½Π°ΠΌΠΈ Ρ ΠΏΡΠΎΠ±ΠΊΠ°ΠΌΠΈ, Π»ΠΈΠ±ΠΎ Π»ΠΈΡΡ Π΄ΡΠ΅Π½Π°ΠΆΠ½ΠΎΠΉ ΡΠΈΡΡΠ΅ΠΌΠΎΠΉ (ΠΊΠΎΡΠΎΡΠ°Ρ ΠΏΠΎΠΌΠΎΠ³Π°Π΅Ρ ΡΡΠ°Π±ΠΈΠ»ΠΈΠ·ΠΈΡΠΎΠ²Π°ΡΡ Π΄Π°Π²Π»Π΅Π½ΠΈΠ΅ Π²Π½ΡΡΡΠΈ Π±Π°ΡΠ°ΡΠ΅ΠΈ, ΠΈ ΠΎΡΠ²ΠΎΠ΄ΠΈΡ ΠΎΠ±ΡΠ°Π·ΡΡΡΠΈΠΉΡΡ Π³Π°Π·).
Π ΠΊΠ°ΠΆΠ΄ΡΡ ΠΈΠ· ΠΎΡΠ΄Π΅Π»ΡΠ½ΡΡ ΡΡΠ΅Π΅ΠΊ ΡΡΡΠ°Π½ΠΎΠ²Π»Π΅Π½ ΡΠΎΠ±ΡΠ°Π½Π½ΡΠΉ Π²ΠΎΠ΅Π΄ΠΈΠ½ΠΎ ΠΏΠ°ΠΊΠ΅Ρ, ΡΠΎΡΡΠΎΡΡΠΈΠΉ ΠΈΠ· ΠΌΠ½ΠΎΠΆΠ΅ΡΡΠ²Π° ΠΎΡΠ΄Π΅Π»ΡΠ½ΡΡ ΠΏΠ»Π°ΡΡΠΈΠ½, ΠΏΠΎΠ»ΡΡΠ½ΠΎΡΡΡ Π² ΠΊΠΎΡΠΎΡΡΡ ΡΠ΅ΡΠ΅Π΄ΡΠ΅ΡΡΡ. ΠΠ·Π³ΠΎΡΠΎΠ²Π»Π΅Π½Π½ΡΠ΅ ΠΈΠ· ΡΠ²ΠΈΠ½ΡΠ° ΠΏΠ»Π°ΡΡΠΈΠ½Ρ ΠΈΠΌΠ΅ΡΡ ΡΠ΅ΡΠ΅ΡΡΠ°ΡΡΡ ΡΡΡΡΠΊΡΡΡΡ ΠΈΠ· ΠΏΡΡΠΌΠΎΡΠ³ΠΎΠ»ΡΠ½ΡΡ ΡΠΎΡ. Π’Π°ΠΊΠ°Ρ ΠΊΠΎΠ½ΡΡΡΡΠΊΡΠΈΡ ΠΏΠΎΠ·Π²ΠΎΠ»ΡΠ΅Ρ Π½Π°Π½Π΅ΡΡΠΈ Π½Π° Π½ΠΈΡ ΠΎΡΠ½ΠΎΠ²Π½ΠΎΠΉ ΡΠ°Π±ΠΎΡΠΈΠΉ ΡΠ΅Π°Π³Π΅Π½Ρ β Π°ΠΊΡΠΈΠ²Π½ΡΡ ΠΌΠ°ΡΡΡ. ΠΠΎΡΠΊΠΎΠ»ΡΠΊΡ Π½Π°Π½ΠΎΡΡΡ Π΅Π΅ ΠΏΠΎΡΡΠ΅Π΄ΡΡΠ²ΠΎΠΌ Π½Π°ΠΌΠ°Π·ΡΠ²Π°Π½ΠΈΡ, ΡΠΎ Π°ΠΊΠΊΡΠΌΡΠ»ΡΡΠΎΡ ΡΠ°ΠΊ ΠΈ Π½Π°Π·ΡΠ²Π°Π΅ΡΡΡ β Ρ ΠΏΠ»Π°ΡΡΠΈΠ½Π°ΠΌΠΈ Π½Π°ΠΌΠ°Π·Π½ΠΎΠ³ΠΎ ΡΠΈΠΏΠ°.
Π‘ΡΡΠ΅ΡΡΠ²ΡΠ΅Ρ Π΅ΡΠ΅ Π΄Π²Π° ΡΠΈΠΏΠ° Π°ΠΊΠΊΡΠΌΡΠ»ΡΡΠΎΡΠΎΠ² β Π² ΠΎΠ΄Π½ΠΈΡ ΡΡΡΠ°Π½ΠΎΠ²Π»Π΅Π½Ρ ΠΏΠ»Π°ΡΡΠΈΠ½Ρ ΡΠ²Π΅Π»ΠΈΡΠ΅Π½Π½ΠΎΠΉ ΠΏΠ»ΠΎΡΠ°Π΄ΠΈ, Π° Π²ΠΎ Π²ΡΠΎΡΡΡ β ΠΈΠ· ΠΏΠ°Π½ΡΠΈΡΠ½ΠΎΠΉ ΡΠ΅ΡΠΊΠΈ. ΠΠ΄Π½Π°ΠΊΠΎ ΠΏΡΠΈ ΠΈΠ·Π³ΠΎΡΠΎΠ²Π»Π΅Π½ΠΈΠΈ Π°Π²ΡΠΎΠΌΠΎΠ±ΠΈΠ»ΡΠ½ΡΡ Π°ΠΊΠΊΡΠΌΡΠ»ΡΡΠΎΡΠΎΠ² ΠΏΡΠΈΠΌΠ΅Π½ΡΡΡ Π»ΠΈΡΡ Π½Π°ΠΌΠ°Π·Π½ΡΠ΅ ΠΏΠ»Π°ΡΡΠΈΠ½Ρ.
ΠΠΎΡΠΊΠΎΠ»ΡΠΊΡ ΠΊΠ°ΠΆΠ΄Π°Ρ ΠΈΠ· ΡΠ΅ΡΠ΅Π΄ΡΡΡΠΈΡ ΡΡ ΠΏΠ»Π°ΡΡΠΈΠ½ ΡΠ²Π»ΡΠ΅ΡΡΡ ΡΠ»Π΅ΠΊΡΡΠΎΠ΄ΠΎΠΌ Ρ ΠΏΡΠΎΡΠΈΠ²ΠΎΠΏΠΎΠ»ΠΎΠΆΠ½ΠΎΠΉ ΠΏΠΎΠ»ΡΡΠ½ΠΎΡΡΡΡ, Π½Π΅ΠΎΠ±Ρ ΠΎΠ΄ΠΈΠΌΠΎ ΠΏΡΠ΅Π΄ΠΎΡΠ²ΡΠ°ΡΠΈΡΡ Π²Π΅ΡΠΎΡΡΠ½ΠΎΡΡΡ ΠΈΡ Π·Π°ΠΌΡΠΊΠ°Π½ΠΈΡ. Π‘ ΡΡΠΎΠΉ ΡΠ΅Π»ΡΡ ΠΌΠ΅ΠΆΠ΄Ρ ΠΊΠ°ΠΆΠ΄ΠΎΠΉ ΠΏΠ°ΡΠΎΠΉ ΠΏΠ»Π°ΡΡΠΈΠ½ Π²ΡΡΠ°Π²Π»Π΅Π½ ΡΠ΅ΠΏΠ°ΡΠ°ΡΠΎΡ, ΠΈΠ·Π³ΠΎΡΠΎΠ²Π»Π΅Π½Π½ΡΠΉ ΠΈΠ· ΠΏΠΎΡΠΈΡΡΠΎΠ³ΠΎ ΠΏΠ»Π°ΡΡΠΈΠΊΠ°, Π½Π΅ ΠΏΡΠ΅ΠΏΡΡΡΡΠ²ΡΡΡΠ΅Π³ΠΎ ΡΠΈΡΠΊΡΠ»ΡΡΠΈΠΈ ΡΠ»Π΅ΠΊΡΡΠΎΠ»ΠΈΡΠ° Π²Π½ΡΡΡΠΈ ΡΡΠ΅ΠΉΠΊΠΈ. ΠΠ²ΠΈΠ΄Ρ ΡΠΎΠ³ΠΎ, ΡΡΠΎ ΠΊΠ°ΠΆΠ΄Π°Ρ ΠΏΠ»Π°ΡΡΠΈΠ½Π°, Π½Π΅ΡΡΡΠ°Ρ ΠΏΠΎΠ»ΠΎΠΆΠΈΡΠ΅Π»ΡΠ½ΡΠΉ Π·Π°ΡΡΠ΄, ΠΏΠΎΠΌΠ΅ΡΠ΅Π½Π° ΠΌΠ΅ΠΆΠ΄Ρ Π΄Π²ΡΠΌΡ Β«ΠΌΠΈΠ½ΡΡΠΎΠ²ΡΠΌΠΈΒ» (ΡΡΠΎ ΠΏΡΠ΅Π΄ΠΎΡΠ²ΡΠ°ΡΠ°Π΅Ρ ΠΊΠΎΡΠΎΠ±Π»Π΅Π½ΠΈΠ΅), ΠΎΡΡΠΈΡΠ°ΡΠ΅Π»ΡΠ½ΡΡ ΠΏΠ»Π°ΡΡΠΈΠ½ Π² ΡΡΠ΅ΠΉΠΊΠ΅ Π²ΡΠ΅Π³Π΄Π° Π½Π° ΠΎΠ΄Π½Ρ Π±ΠΎΠ»ΡΡΠ΅.
ΠΠ΅ΡΡ ΡΠΎΠ±ΡΠ°Π½Π½ΡΠΉ ΠΏΠ°ΠΊΠ΅Ρ Π·Π°ΡΠΈΠΊΡΠΈΡΠΎΠ²Π°Π½ ΠΎΡ Π²ΠΎΠ·ΠΌΠΎΠΆΠ½ΡΡ ΡΠΌΠ΅ΡΠ΅Π½ΠΈΠΉ ΠΈ Π΄Π΅ΡΠΎΡΠΌΠ°ΡΠΈΠΉ ΡΠΏΠ΅ΡΠΈΠ°Π»ΡΠ½ΡΠΌ Π±Π°Π½Π΄Π°ΠΆΠΎΠΌ. ΠΠ»ΡΡΠΎΠ²ΡΠ΅ ΠΈ ΠΌΠΈΠ½ΡΡΠΎΠ²ΡΠ΅ ΡΠΎΠΊΠΎΠ²ΡΠ²ΠΎΠ΄Ρ ΠΏΠ»Π°ΡΡΠΈΠ½ ΠΎΠ±ΡΠ΅Π΄ΠΈΠ½Π΅Π½Ρ ΠΏΠΎΠΏΠ°ΡΠ½ΠΎ ΠΈ ΠΏΡΠΈ ΠΏΠΎΠΌΠΎΡΠΈ ΡΠΎΠΊΠΎΡΠ±ΠΎΡΠ½ΠΈΠΊΠΎΠ² ΠΊΠΎΠ½ΡΠ΅Π½ΡΡΠΈΡΡΡΡ ΡΠ²ΠΎΡ ΡΠ½Π΅ΡΠ³ΠΈΡ Π½Π° Π²ΡΠ²ΠΎΠ΄Π½ΡΡ Π±ΠΎΡΠ½Π°Ρ Π°ΠΊΠΊΡΠΌΡΠ»ΡΡΠΎΡΠ°. Π Π½ΠΈΠΌ ΠΏΠΎΠ΄ΠΊΠ»ΡΡΠ°ΡΡ ΡΠΎΠΊΠΎΠΏΡΠΈΠ΅ΠΌΠ½ΡΠ΅ ΠΊΠ»Π΅ΠΌΠΌΡ Π°Π²ΡΠΎΠΌΠΎΠ±ΠΈΠ»Ρ.
Β
Π£ΡΡΡΠΎΠΉΡΡΠ²ΠΎ Π³Π΅Π½Π΅ΡΠ°ΡΠΎΡΠ°
Β
ΠΠ΅Π½Π΅ΡΠ°ΡΠΎΡ ΡΠΎΠΊΠ° ΠΏΡΠ΅ΠΎΠ±ΡΠ°Π·ΡΠ΅Ρ ΠΌΠ΅Ρ Π°Π½ΠΈΡΠ΅ΡΠΊΡΡ (ΠΊΠΈΠ½Π΅ΡΠΈΡΠ΅ΡΠΊΡΡ) ΡΠ½Π΅ΡΠ³ΠΈΡ Π² ΡΠ»Π΅ΠΊΡΡΠΎΡΠ½Π΅ΡΠ³ΠΈΡ. Π ΡΠ½Π΅ΡΠ³Π΅ΡΠΈΠΊΠ΅ ΠΏΠΎΠ»ΡΠ·ΡΡΡΡΡ ΡΠΎΠ»ΡΠΊΠΎ Π²ΡΠ°ΡΠ°ΡΡΠΈΠΌΠΈΡΡ ΡΠ»Π΅ΠΊΡΡΠΎΠΌΠ°ΡΠΈΠ½Π½ΡΠΌΠΈ Π³Π΅Π½Π΅ΡΠ°ΡΠΎΡΠ°ΠΌΠΈ, ΠΎΡΠ½ΠΎΠ²Π°Π½Π½ΡΠΌΠΈ Π½Π° Π²ΠΎΠ·Π½ΠΈΠΊΠ½ΠΎΠ²Π΅Π½ΠΈΠΈ ΡΠ»Π΅ΠΊΡΡΠΎΠ΄Π²ΠΈΠΆΡΡΠ΅ΠΉ ΡΠΈΠ»Ρ (ΠΠΠ‘) Π² ΠΏΡΠΎΠ²ΠΎΠ΄Π½ΠΈΠΊΠ΅, Π½Π° ΠΊΠΎΡΠΎΡΡΠΉ ΠΊΠ°ΠΊΠΈΠΌ-Π»ΠΈΠ±ΠΎ ΠΎΠ±ΡΠ°Π·ΠΎΠΌ Π΄Π΅ΠΉΡΡΠ²ΡΠ΅Ρ ΠΈΠ·ΠΌΠ΅Π½ΡΡΡΠ΅Π΅ΡΡ ΠΌΠ°Π³Π½ΠΈΡΠ½ΠΎΠ΅ ΠΏΠΎΠ»Π΅. Π’Ρ ΡΠ°ΡΡΡ Π³Π΅Π½Π΅ΡΠ°ΡΠΎΡΠ°, ΠΊΠΎΡΠΎΡΠ°Ρ ΠΏΡΠ΅Π΄Π½Π°Π·Π½Π°ΡΠ΅Π½Π° Π΄Π»Ρ ΡΠΎΠ·Π΄Π°Π½ΠΈΡ ΠΌΠ°Π³Π½ΠΈΡΠ½ΠΎΠ³ΠΎ ΠΏΠΎΠ»Ρ, Π½Π°Π·ΡΠ²Π°ΡΡ ΠΈΠ½Π΄ΡΠΊΡΠΎΡΠΎΠΌ, Π° ΡΠ°ΡΡΡ, Π² ΠΊΠΎΡΠΎΡΠΎΠΉ ΠΈΠ½Π΄ΡΡΠΈΡΡΠ΅ΡΡΡ ΠΠΠ‘ β ΡΠΊΠΎΡΠ΅ΠΌ.
ΠΡΠ°ΡΠ°ΡΡΡΡΡΡ ΡΠ°ΡΡΡ ΠΌΠ°ΡΠΈΠ½Ρ Π½Π°Π·ΡΠ²Π°ΡΡ ΡΠΎΡΠΎΡΠΎΠΌ, Π° Π½Π΅ΠΏΠΎΠ΄Π²ΠΈΠΆΠ½ΡΡ ΡΠ°ΡΡΡ β ΡΡΠ°ΡΠΎΡΠΎΠΌ. Π ΡΠΈΠ½Ρ ΡΠΎΠ½Π½ΡΡ ΠΌΠ°ΡΠΈΠ½Π°Ρ ΠΏΠ΅ΡΠ΅ΠΌΠ΅Π½Π½ΠΎΠ³ΠΎ ΡΠΎΠΊΠ° ΠΈΠ½Π΄ΡΠΊΡΠΎΡΠΎΠΌ ΠΎΠ±ΡΡΠ½ΠΎ ΡΠ²Π»ΡΠ΅ΡΡΡ ΡΠΎΡΠΎΡ, Π° Π² ΠΌΠ°ΡΠΈΠ½Π°Ρ ΠΏΠΎΡΡΠΎΡΠ½Π½ΠΎΠ³ΠΎ ΡΠΎΠΊΠ° β ΡΡΠ°ΡΠΎΡ. Π ΠΎΠ±ΠΎΠΈΡ ΡΠ»ΡΡΠ°ΡΡ ΠΈΠ½Π΄ΡΠΊΡΠΎΡ ΠΏΡΠ΅Π΄ΡΡΠ°Π²Π»ΡΠ΅Ρ ΡΠΎΠ±ΠΎΠΉ ΠΎΠ±ΡΡΠ½ΠΎ Π΄Π²ΡΡ - ΠΈΠ»ΠΈ ΠΌΠ½ΠΎΠ³ΠΎΠΏΠΎΠ»ΡΡΠ½ΡΡ ΡΠ»Π΅ΠΊΡΡΠΎΠΌΠ°Π³Π½ΠΈΡΠ½ΡΡ ΡΠΈΡΡΠ΅ΠΌΡ, ΡΠ½Π°Π±ΠΆΠ΅Π½Π½ΡΡ ΠΎΠ±ΠΌΠΎΡΠΊΠΎΠΉ Π²ΠΎΠ·Π±ΡΠΆΠ΄Π΅Π½ΠΈΡ, ΠΏΠΈΡΠ°Π΅ΠΌΠΎΠΉ ΠΏΠΎΡΡΠΎΡΠ½Π½ΡΠΌ ΡΠΎΠΊΠΎΠΌ (ΡΠΎΠΊΠΎΠΌ Π²ΠΎΠ·Π±ΡΠΆΠ΄Π΅Π½ΠΈΡ), Π½ΠΎ Π²ΡΡΡΠ΅ΡΠ°ΡΡΡΡ ΠΈ ΠΈΠ½Π΄ΡΠΊΡΠΎΡΡ, ΡΠΎΡΡΠΎΡΡΠΈΠ΅ ΠΈΠ· ΡΠΈΡΡΠ΅ΠΌΡ ΠΏΠΎΡΡΠΎΡΠ½Π½ΡΡ ΠΌΠ°Π³Π½ΠΈΡΠΎΠ². Π ΠΈΠ½Π΄ΡΠΊΡΠΈΠΎΠ½Π½ΡΡ (Π°ΡΠΈΠ½Ρ ΡΠΎΠ½Π½ΡΡ ) Π³Π΅Π½Π΅ΡΠ°ΡΠΎΡΠ°Ρ ΠΏΠ΅ΡΠ΅ΠΌΠ΅Π½Π½ΠΎΠ³ΠΎ ΡΠΎΠΊΠ° ΠΈΠ½Π΄ΡΠΊΡΠΎΡ ΠΈ ΡΠΊΠΎΡΡ Π½Π΅ ΠΌΠΎΠ³ΡΡ ΡΠ΅ΡΠΊΠΎ (ΠΊΠΎΠ½ΡΡΡΡΠΊΡΠΈΠ²Π½ΠΎ) ΡΠ°Π·Π»ΠΈΡΠ°ΡΡΡΡ Π΄ΡΡΠ³ ΠΎΡ Π΄ΡΡΠ³Π° (ΠΌΠΎΠΆΠ½ΠΎ ΡΠΊΠ°Π·Π°ΡΡ, ΡΡΠΎ ΡΡΠ°ΡΠΎΡ ΠΈ ΡΠΎΡΠΎΡ ΠΎΠ΄Π½ΠΎΠ²ΡΠ΅ΠΌΠ΅Π½Π½ΠΎ ΡΠ²Π»ΡΡΡΡΡ ΠΈ ΠΈΠ½Π΄ΡΠΊΡΠΎΡΠΎΠΌ ΠΈ ΡΠΊΠΎΡΠ΅ΠΌ).
ΠΠΎΠ»Π΅Π΅ 95 % ΡΠ»Π΅ΠΊΡΡΠΎΡΠ½Π΅ΡΠ³ΠΈΠΈ Π½Π° ΡΠ»Π΅ΠΊΡΡΠΎΡΡΠ°Π½ΡΠΈΡΡ ΠΌΠΈΡΠ° ΠΏΡΠΎΠΈΠ·Π²ΠΎΠ΄ΠΈΡΡΡ ΠΏΡΠΈ ΠΏΠΎΠΌΠΎΡΠΈ ΡΠΈΠ½Ρ ΡΠΎΠ½Π½ΡΡ Π³Π΅Π½Π΅ΡΠ°ΡΠΎΡΠΎΠ² ΠΏΠ΅ΡΠ΅ΠΌΠ΅Π½Π½ΠΎΠ³ΠΎ ΡΠΎΠΊΠ°. ΠΡΠΈ ΠΏΠΎΠΌΠΎΡΠΈ Π²ΡΠ°ΡΠ°ΡΡΠ΅Π³ΠΎΡΡ ΠΈΠ½Π΄ΡΠΊΡΠΎΡΠ° Π² ΡΡΠΈΡ Π³Π΅Π½Π΅ΡΠ°ΡΠΎΡΠ°Ρ ΡΠΎΠ·Π΄Π°Π΅ΡΡΡ Π²ΡΠ°ΡΠ°ΡΡΠ΅Π΅ΡΡ ΠΌΠ°Π³Π½ΠΈΡΠ½ΠΎΠ΅ ΠΏΠΎΠ»Π΅, Π½Π°Π²ΠΎΠ΄ΡΡΠ΅Π΅ Π² ΡΡΠ°ΡΠΎΡΠ½ΠΎΠΉ (ΠΎΠ±ΡΡΠ½ΠΎ ΡΡΠ΅Ρ ΡΠ°Π·Π½ΠΎΠΉ) ΠΎΠ±ΠΌΠΎΡΠΊΠ΅ ΠΏΠ΅ΡΠ΅ΠΌΠ΅Π½Π½ΡΡ ΠΠΠ‘, ΡΠ°ΡΡΠΎΡΠ° ΠΊΠΎΡΠΎΡΠΎΠΉ ΡΠΎΡΠ½ΠΎ ΡΠΎΠΎΡΠ²Π΅ΡΡΡΠ²ΡΠ΅Ρ ΡΠ°ΡΡΠΎΡΠ΅ Π²ΡΠ°ΡΠ΅Π½ΠΈΡ ΡΠΎΡΠΎΡΠ° (Π½Π°Ρ ΠΎΠ΄ΠΈΡΡΡ Π² ΡΠΈΠ½Ρ ΡΠΎΠ½ΠΈΠ·ΠΌΠ΅ Ρ ΡΠ°ΡΡΠΎΡΠΎΠΉ Π²ΡΠ°ΡΠ΅Π½ΠΈΡ ΠΈΠ½Π΄ΡΠΊΡΠΎΡΠ°). ΠΡΠ»ΠΈ ΠΈΠ½Π΄ΡΠΊΡΠΎΡ, Π½Π°ΠΏΡΠΈΠΌΠ΅Ρ, ΠΈΠΌΠ΅Π΅Ρ Π΄Π²Π° ΠΏΠΎΠ»ΡΡΠ° ΠΈ Π²ΡΠ°ΡΠ°Π΅ΡΡΡ Ρ ΡΠ°ΡΡΠΎΡΠΎΠΉ 3000 r/min (50 r/s), ΡΠΎ Π² ΠΊΠ°ΠΆΠ΄ΠΎΠΉ ΡΠ°Π·Π΅ ΡΡΠ°ΡΠΎΡΠ½ΠΎΠΉ ΠΎΠ±ΠΌΠΎΡΠΊΠΈ ΠΈΠ½Π΄ΡΡΠΈΡΡΠ΅ΡΡΡ ΠΏΠ΅ΡΠ΅ΠΌΠ΅Π½Π½Π°Ρ ΠΠΠ‘ ΡΠ°ΡΡΠΎΡΠΎΠΉ 50 Hz. ΠΠΎΠ½ΡΡΡΡΠΊΡΠΈΠ²Π½ΠΎΠ΅ ΠΈΡΠΏΠΎΠ»Π½Π΅Π½ΠΈΠ΅ ΡΠ°ΠΊΠΎΠ³ΠΎ Π³Π΅Π½Π΅ΡΠ°ΡΠΎΡΠ° ΡΠΏΡΠΎΡΠ΅Π½Π½ΠΎ ΠΈΠ·ΠΎΠ±ΡΠ°ΠΆΠ΅Π½ΠΎ Π½Π° ΡΠΈΡ. 1.
Π ΠΈΡ. 1. ΠΡΠΈΠ½ΡΠΈΠΏ ΡΡΡΡΠΎΠΉΡΡΠ²Π° Π΄Π²ΡΡ
ΠΏΠΎΠ»ΡΡΠ½ΠΎΠ³ΠΎ ΡΠΈΠ½Ρ
ΡΠΎΠ½Π½ΠΎΠ³ΠΎ Π³Π΅Π½Π΅ΡΠ°ΡΠΎΡΠ°. 1 ΡΡΠ°ΡΠΎΡ (ΡΠΊΠΎΡΡ), 2 ΡΠΎΡΠΎΡ (ΠΈΠ½Π΄ΡΠΊΡΠΎΡ), 3 Π²Π°Π», 4 ΠΊΠΎΡΠΏΡΡ. U-X, V-Y, W-Z β ΡΠ°Π·ΠΌΠ΅ΡΠ΅Π½Π½ΡΠ΅ Π² ΠΏΠ°Π·Π°Ρ
ΡΡΠ°ΡΠΎΡΠ° ΡΠ°ΡΡΠΈ ΠΎΠ±ΠΌΠΎΡΠΎΠΊ ΡΡΠ΅Ρ
ΡΠ°Π·
Β
ΠΠ°Π³Π½ΠΈΡΠ½Π°Ρ ΡΠΈΡΡΠ΅ΠΌΠ° ΡΡΠ°ΡΠΎΡΠ° ΠΏΡΠ΅Π΄ΡΡΠ°Π²Π»ΡΠ΅Ρ ΡΠΎΠ±ΠΎΠΉ ΡΠΏΡΠ΅ΡΡΠΎΠ²Π°Π½Π½ΡΠΉ ΠΏΠ°ΠΊΠ΅Ρ ΡΠΎΠ½ΠΊΠΈΡ ΡΡΠ°Π»ΡΠ½ΡΡ Π»ΠΈΡΡΠΎΠ², Π² ΠΏΠ°Π·Π°Ρ ΠΊΠΎΡΠΎΡΠΎΠ³ΠΎ ΡΠ°ΡΠΏΠΎΠ»Π°Π³Π°Π΅ΡΡΡ ΡΡΠ°ΡΠΎΡΠ½Π°Ρ ΠΎΠ±ΠΌΠΎΡΠΊΠ°. ΠΠ±ΠΌΠΎΡΠΊΠ° ΡΠΎΡΡΠΎΠΈΡ ΠΈΠ· ΡΡΠ΅Ρ ΡΠ°Π·, ΡΠ΄Π²ΠΈΠ½ΡΡΡΡ Π² ΡΠ»ΡΡΠ°Π΅ Π΄Π²ΡΡ ΠΏΠΎΠ»ΡΡΠ½ΠΎΠΉ ΠΌΠ°ΡΠΈΠ½Ρ Π΄ΡΡΠ³ ΠΎΡΠ½ΠΎΡΠΈΡΠ΅Π»ΡΠ½ΠΎ Π΄ΡΡΠ³Π° Π½Π° 1/3 ΠΏΠ΅ΡΠΈΠΌΠ΅ΡΡΠ° ΡΡΠ°ΡΠΎΡΠ°; Π² ΡΠ°Π·Π½ΡΡ ΠΎΠ±ΠΌΠΎΡΠΊΠ°Ρ ΠΈΠ½Π΄ΡΡΠΈΡΡΡΡΡΡ, ΡΠ»Π΅Π΄ΠΎΠ²Π°ΡΠ΅Π»ΡΠ½ΠΎ, ΠΠΠ‘, ΡΠ΄Π²ΠΈΠ½ΡΡΡΠ΅ Π΄ΡΡΠ³ ΠΎΡΠ½ΠΎΡΠΈΡΠ΅Π»ΡΠ½ΠΎ Π΄ΡΡΠ³Π° Π½Π° 120o. ΠΠ±ΠΌΠΎΡΠΊΠ° ΠΊΠ°ΠΆΠ΄ΠΎΠΉ ΡΠ°Π·Ρ, Π² ΡΠ²ΠΎΡ ΠΎΡΠ΅ΡΠ΅Π΄Ρ, ΡΠΎΡΡΠΎΠΈΡ ΠΈΠ· ΠΌΠ½ΠΎΠ³ΠΎΠ²ΠΈΡΠΊΠΎΠ²ΡΡ ΠΊΠ°ΡΡΡΠ΅ΠΊ, ΡΠΎΠ΅Π΄ΠΈΠ½Π΅Π½Π½ΡΡ ΠΌΠ΅ΠΆΠ΄Ρ ΡΠΎΠ±ΠΎΠΉ ΠΏΠΎΡΠ»Π΅Π΄ΠΎΠ²Π°ΡΠ΅Π»ΡΠ½ΠΎ ΠΈΠ»ΠΈ ΠΏΠ°ΡΠ°Π»Π»Π΅Π»ΡΠ½ΠΎ.
ΠΠΎΠ»ΡΡΠΎΠ² ΠΈΠ½Π΄ΡΠΊΡΠΎΡΠ° ΠΈ, Π² ΡΠΎΠΎΡΠ²Π΅ΡΡΡΠ²ΠΈΠΈ Ρ ΡΡΠΈΠΌ, ΠΏΠΎΠ»ΡΡΠ½ΡΡ Π΄Π΅Π»Π΅Π½ΠΈΠΉ ΡΡΠ°ΡΠΎΡΠ°, ΠΌΠΎΠΆΠ΅Ρ Π±ΡΡΡ ΠΈ Π±ΠΎΠ»ΡΡΠ΅ Π΄Π²ΡΡ . Π§Π΅ΠΌ ΠΌΠ΅Π΄Π»Π΅Π½Π½Π΅Π΅ Π²ΡΠ°ΡΠ°Π΅ΡΡΡ ΡΠΎΡΠΎΡ, ΡΠ΅ΠΌ Π±ΠΎΠ»ΡΡΠ΅ Π΄ΠΎΠ»ΠΆΠ½ΠΎ Π±ΡΡΡ ΠΏΡΠΈ Π·Π°Π΄Π°Π½Π½ΠΎΠΉ ΡΠ°ΡΡΠΎΡΠ΅ ΡΠΎΠΊΠ° ΡΠΈΡΠ»ΠΎ ΠΏΠΎΠ»ΡΡΠΎΠ². ΠΡΠ»ΠΈ, Π½Π°ΠΏΡΠΈΠΌΠ΅Ρ, ΡΠΎΡΠΎΡ Π²ΡΠ°ΡΠ°Π΅ΡΡΡ Ρ ΡΠ°ΡΡΠΎΡΠΎΠΉ 300 r/min, ΡΠΎ ΡΠΈΡΠ»ΠΎ ΠΏΠΎΠ»ΡΡΠΎΠ² Π³Π΅Π½Π΅ΡΠ°ΡΠΎΡΠ°, Π΄Π»Ρ ΠΏΠΎΠ»ΡΡΠ΅Π½ΠΈΡ ΡΠ°ΡΡΠΎΡΡ ΠΏΠ΅ΡΠ΅ΠΌΠ΅Π½Π½ΠΎΠ³ΠΎ ΡΠΎΠΊΠ° 50 Hz, Π΄ΠΎΠ»ΠΆΠ½ΠΎ Π±ΡΡΡ 20. ΠΠ°ΠΏΡΠΈΠΌΠ΅Ρ, Π½Π° ΠΎΠ΄Π½ΠΎΠΉ ΠΈΠ· ΠΊΡΡΠΏΠ½Π΅ΠΉΡΠΈΡ Π³ΠΈΠ΄ΡΠΎΡΠ»Π΅ΠΊΡΡΠΎΡΡΠ°Π½ΡΠΈΠΉ ΠΌΠΈΡΠ°, ΠΠΠ‘ ΠΡΠ°ΠΉΠΏΡ (Itaipu, ΡΠΌ. ΡΠΈΡ. 4) Π³Π΅Π½Π΅ΡΠ°ΡΠΎΡΡ, ΡΠ°Π±ΠΎΡΠ°ΡΡΠΈΠ΅ Π½Π° ΡΠ°ΡΡΠΎΡΠ΅ 50 Hz, ΠΈΡΠΏΠΎΠ»Π½Π΅Π½Ρ 66-ΠΏΠΎΠ»ΡΡΠ½ΡΠΌΠΈ, Π° Π³Π΅Π½Π΅ΡΠ°ΡΠΎΡΡ, ΡΠ°Π±ΠΎΡΠ°ΡΡΠΈΠ΅ Π½Π° ΡΠ°ΡΡΠΎΡΠ΅ 60 Hz β 78-ΠΏΠΎΠ»ΡΡΠ½ΡΠΌΠΈ.
ΠΠ±ΠΌΠΎΡΠΊΠ° Π²ΠΎΠ·Π±ΡΠΆΠ΄Π΅Π½ΠΈΡ Π΄Π²ΡΡ - ΠΈΠ»ΠΈ ΡΠ΅ΡΡΡΠ΅Ρ ΠΏΠΎΠ»ΡΡΠ½ΠΎΠ³ΠΎ Π³Π΅Π½Π΅ΡΠ°ΡΠΎΡΠ° ΡΠ°Π·ΠΌΠ΅ΡΠ°Π΅ΡΡΡ, ΠΊΠ°ΠΊ ΠΏΠΎΠΊΠ°Π·Π°Π½ΠΎ Π½Π° ΡΠΈΡ. 1, Π² ΠΏΠ°Π·Π°Ρ ΠΌΠ°ΡΡΠΈΠ²Π½ΠΎΠ³ΠΎ ΡΡΠ°Π»ΡΠ½ΠΎΠ³ΠΎ ΡΠ΅ΡΠ΄Π΅ΡΠ½ΠΈΠΊΠ° ΡΠΎΡΠΎΡΠ°. Π’Π°ΠΊΠ°Ρ ΠΊΠΎΠ½ΡΡΡΡΠΊΡΠΈΡ ΡΠΎΡΠΎΡΠ° Π½Π΅ΠΎΠ±Ρ ΠΎΠ΄ΠΈΠΌΠ° Π² ΡΠ»ΡΡΠ°Π΅ Π±ΡΡΡΡΠΎΡ ΠΎΠ΄Π½ΡΡ Π³Π΅Π½Π΅ΡΠ°ΡΠΎΡΠΎΠ², ΡΠ°Π±ΠΎΡΠ°ΡΡΠΈΡ ΠΏΡΠΈ ΡΠ°ΡΡΠΎΡΠ΅ Π²ΡΠ°ΡΠ΅Π½ΠΈΡ Π² 3000 ΠΈΠ»ΠΈ 1500 r/min (ΠΎΡΠΎΠ±Π΅Π½Π½ΠΎ Π΄Π»Ρ ΡΡΡΠ±ΠΎΠ³Π΅Π½Π΅ΡΠ°ΡΠΎΡΠΎΠ², ΠΏΡΠ΅Π΄Π½Π°Π·Π½Π°ΡΠ΅Π½Π½ΡΡ Π΄Π»Ρ ΡΠΎΠ΅Π΄ΠΈΠ½Π΅Π½ΠΈΡ Ρ ΠΏΠ°ΡΠΎΠ²ΡΠΌΠΈ ΡΡΡΠ±ΠΈΠ½Π°ΠΌΠΈ), ΡΠ°ΠΊ ΠΊΠ°ΠΊ ΠΏΡΠΈ ΡΠ°ΠΊΠΎΠΉ ΡΠΊΠΎΡΠΎΡΡΠΈ Π½Π° ΠΎΠ±ΠΌΠΎΡΠΊΡ ΡΠΎΡΠΎΡΠ° Π΄Π΅ΠΉΡΡΠ²ΡΡΡ Π±ΠΎΠ»ΡΡΠΈΠ΅ ΡΠ΅Π½ΡΡΠΎΠ±Π΅ΠΆΠ½ΡΠ΅ ΡΠΈΠ»Ρ. ΠΡΠΈ Π±ΠΎΠ»ΡΡΠ΅ΠΌ ΡΠΈΡΠ»Π΅ ΠΏΠΎΠ»ΡΡΠΎΠ² ΠΊΠ°ΠΆΠ΄ΡΠΉ ΠΏΠΎΠ»ΡΡ ΠΈΠΌΠ΅Π΅Ρ ΠΎΡΠ΄Π΅Π»ΡΠ½ΡΡ ΠΎΠ±ΠΌΠΎΡΠΊΡ Π²ΠΎΠ·Π±ΡΠΆΠ΄Π΅Π½ΠΈΡ. Π’Π°ΠΊΠΎΠΉ ΡΠ²Π½ΠΎΠΏΠΎΠ»ΡΡΠ½ΡΠΉ ΠΏΡΠΈΠ½ΡΠΈΠΏ ΡΡΡΡΠΎΠΉΡΡΠ²Π° ΠΏΡΠΈΠΌΠ΅Π½ΡΠ΅ΡΡΡ, Π² ΡΠ°ΡΡΠ½ΠΎΡΡΠΈ, Π² ΡΠ»ΡΡΠ°Π΅ ΡΠΈΡ ΠΎΡ ΠΎΠ΄Π½ΡΡ Π³Π΅Π½Π΅ΡΠ°ΡΠΎΡΠΎΠ², ΠΏΡΠ΅Π΄Π½Π°Π·Π½Π°ΡΠ΅Π½Π½ΡΡ Π΄Π»Ρ ΡΠΎΠ΅Π΄ΠΈΠ½Π΅Π½ΠΈΡ Ρ Π³ΠΈΠ΄ΡΠΎΡΡΡΠ±ΠΈΠ½Π°ΠΌΠΈ (Π³ΠΈΠ΄ΡΠΎΠ³Π΅Π½Π΅ΡΠ°ΡΠΎΡΠΎΠ²), ΡΠ°Π±ΠΎΡΠ°ΡΡΠΈΡ ΠΎΠ±ΡΡΠ½ΠΎ ΠΏΡΠΈ ΡΠ°ΡΡΠΎΡΠ΅ Π²ΡΠ°ΡΠ΅Π½ΠΈΡ ΠΎΡ 60 r/min Π΄ΠΎ 600 r/min.
ΠΡΠ΅Π½Ρ ΡΠ°ΡΡΠΎ ΡΠ°ΠΊΠΈΠ΅ Π³Π΅Π½Π΅ΡΠ°ΡΠΎΡΡ, Π² ΡΠΎΠΎΡΠ²Π΅ΡΡΡΠ²ΠΈΠΈ Ρ ΠΊΠΎΠ½ΡΡΡΡΠΊΡΠΈΠ²Π½ΡΠΌ ΠΈΡΠΏΠΎΠ»Π½Π΅Π½ΠΈΠ΅ΠΌ ΠΌΠΎΡΠ½ΡΡ Π³ΠΈΠ΄ΡΠΎΡΡΡΠ±ΠΈΠ½, Π²ΡΠΏΠΎΠ»Π½ΡΡΡΡΡ Ρ Π²Π΅ΡΡΠΈΠΊΠ°Π»ΡΠ½ΡΠΌ Π²Π°Π»ΠΎΠΌ.
ΠΠ±ΠΌΠΎΡΠΊΡ Π²ΠΎΠ·Π±ΡΠΆΠ΄Π΅Π½ΠΈΡ ΡΠΈΠ½Ρ ΡΠΎΠ½Π½ΠΎΠ³ΠΎ Π³Π΅Π½Π΅ΡΠ°ΡΠΎΡΠ° ΠΎΠ±ΡΡΠ½ΠΎ ΠΏΠΈΡΠ°ΡΡ ΠΏΠΎΡΡΠΎΡΠ½Π½ΡΠΌ ΡΠΎΠΊΠΎΠΌ ΠΎΡ Π²Π½Π΅ΡΠ½Π΅Π³ΠΎ ΠΈΡΡΠΎΡΠ½ΠΈΠΊΠ° ΡΠ΅ΡΠ΅Π· ΠΊΠΎΠ½ΡΠ°ΠΊΡΠ½ΡΠ΅ ΠΊΠΎΠ»ΡΡΠ° Π½Π° Π²Π°Π»Ρ ΡΠΎΡΠΎΡΠ°. Π Π°Π½ΡΡΠ΅ Π΄Π»Ρ ΡΡΠΎΠ³ΠΎ ΠΏΡΠ΅Π΄ΡΡΠΌΠ°ΡΡΠΈΠ²Π°Π»ΡΡ ΡΠΏΠ΅ΡΠΈΠ°Π»ΡΠ½ΡΠΉ Π³Π΅Π½Π΅ΡΠ°ΡΠΎΡ ΠΏΠΎΡΡΠΎΡΠ½Π½ΠΎΠ³ΠΎ ΡΠΎΠΊΠ° (Π²ΠΎΠ·Π±ΡΠ΄ΠΈΡΠ΅Π»Ρ), ΠΆΠ΅ΡΡΠΊΠΎ ΡΠ²ΡΠ·Π°Π½Π½ΡΠΉ Ρ Π²Π°Π»ΠΎΠΌ Π³Π΅Π½Π΅ΡΠ°ΡΠΎΡΠ°, Π° Π² Π½Π°ΡΡΠΎΡΡΠ΅Π΅ Π²ΡΠ΅ΠΌΡ ΠΈΡΠΏΠΎΠ»ΡΠ·ΡΡΡΡΡ Π±ΠΎΠ»Π΅Π΅ ΠΏΡΠΎΡΡΡΠ΅ ΠΈ Π΄Π΅ΡΠ΅Π²ΡΠ΅ ΠΏΠΎΠ»ΡΠΏΡΠΎΠ²ΠΎΠ΄Π½ΠΈΠΊΠΎΠ²ΡΠ΅ Π²ΡΠΏΡΡΠΌΠΈΡΠ΅Π»ΠΈ. ΠΡΡΡΠ΅ΡΠ°ΡΡΡΡ ΠΈ ΡΠΈΡΡΠ΅ΠΌΡ Π²ΠΎΠ·Π±ΡΠΆΠ΄Π΅Π½ΠΈΡ, Π²ΡΡΡΠΎΠ΅Π½Π½ΡΠ΅ Π² ΡΠΎΡΠΎΡ, Π² ΠΊΠΎΡΠΎΡΡΡ ΠΠΠ‘ ΠΈΠ½Π΄ΡΡΠΈΡΡΠ΅ΡΡΡ ΡΡΠ°ΡΠΎΡΠ½ΠΎΠΉ ΠΎΠ±ΠΌΠΎΡΠΊΠΎΠΉ. ΠΡΠ»ΠΈ Π΄Π»Ρ ΡΠΎΠ·Π΄Π°Π½ΠΈΡ ΠΌΠ°Π³Π½ΠΈΡΠ½ΠΎΠ³ΠΎ ΠΏΠΎΠ»Ρ Π²ΠΌΠ΅ΡΡΠΎ ΡΠ»Π΅ΠΊΡΡΠΎΠΌΠ°Π³Π½ΠΈΡΠ½ΠΎΠΉ ΡΠΈΡΡΠ΅ΠΌΡ ΠΈΡΠΏΠΎΠ»ΡΠ·ΠΎΠ²Π°ΡΡ ΠΏΠΎΡΡΠΎΡΠ½Π½ΡΠ΅ ΠΌΠ°Π³Π½ΠΈΡΡ, ΡΠΎ ΠΈΡΡΠΎΡΠ½ΠΈΠΊ ΡΠΎΠΊΠ° Π²ΠΎΠ·Π±ΡΠΆΠ΄Π΅Π½ΠΈΡ ΠΎΡΠΏΠ°Π΄Π°Π΅Ρ ΠΈ Π³Π΅Π½Π΅ΡΠ°ΡΠΎΡ ΡΡΠ°Π½ΠΎΠ²ΠΈΡΡΡ Π·Π½Π°ΡΠΈΡΠ΅Π»ΡΠ½ΠΎ ΠΏΡΠΎΡΠ΅ ΠΈ Π½Π°Π΄Π΅ΠΆΠ½Π΅Π΅, Π½ΠΎ Π² ΡΠΎ ΠΆΠ΅ Π²ΡΠ΅ΠΌΡ ΠΈ Π΄ΠΎΡΠΎΠΆΠ΅. ΠΠΎΡΡΠΎΠΌΡ ΠΏΠΎΡΡΠΎΡΠ½Π½ΡΠ΅ ΠΌΠ°Π³Π½ΠΈΡΡ ΠΏΡΠΈΠΌΠ΅Π½ΡΡΡΡΡ ΠΎΠ±ΡΡΠ½ΠΎ Π² ΠΎΡΠ½ΠΎΡΠΈΡΠ΅Π»ΡΠ½ΠΎ ΠΌΠ°Π»ΠΎΠΌΠΎΡΠ½ΡΡ Π³Π΅Π½Π΅ΡΠ°ΡΠΎΡΠ°Ρ (ΠΌΠΎΡΠ½ΠΎΡΡΡΡ Π΄ΠΎ Π½Π΅ΡΠΊΠΎΠ»ΡΠΊΠΈΡ ΡΠΎΡΠ΅Π½ ΠΊΠΈΠ»ΠΎΠ²Π°ΡΡ).
Β
Π£ΡΡΡΠΎΠΉΡΡΠ²ΠΎ ΡΠΈΡΡΠ΅ΠΌΡ ΠΏΡΡΠΊΠ°
Β
Π‘ΠΈΡΡΠ΅ΠΌΠ° Π·Π°ΠΏΡΡΠΊΠ° Π΄Π²ΠΈΠ³Π°ΡΠ΅Π»Ρ ΠΏΡΠ΅Π΄Π½Π°Π·Π½Π°ΡΠ΅Π½Π° Π΄Π»Ρ ΡΠΎΠ·Π΄Π°Π½ΠΈΡ ΠΏΠ΅ΡΠ²ΠΈΡΠ½ΠΎΠ³ΠΎ ΠΊΡΡΡΡΡΠ΅Π³ΠΎ ΠΌΠΎΠΌΠ΅Π½ΡΠ° ΠΊΠΎΠ»Π΅Π½Π²Π°Π»Π° Π΄Π²ΠΈΠ³Π°ΡΠ΅Π»Ρ Ρ ΠΎΠ±ΠΎΡΠΎΡΠ°ΠΌΠΈ, Π½Π΅ΠΎΠ±Ρ ΠΎΠ΄ΠΈΠΌΡΠΌΠΈ Π΄Π»Ρ ΠΎΠ±ΡΠ°Π·ΠΎΠ²Π°Π½ΠΈΡ Π½ΡΠΆΠ½ΠΎΠΉ ΡΡΠ΅ΠΏΠ΅Π½ΠΈ ΡΠΆΠ°ΡΠΈΡ, Π΄Π»Ρ Π²ΠΎΡΠΏΠ»Π°ΠΌΠ΅Π½Π΅Π½ΠΈΡ Π³ΠΎΡΡΡΠ΅ΠΉ ΡΠΌΠ΅ΡΠΈ. Π£ΠΏΡΠ°Π²Π»Π΅Π½ΠΈΠ΅ ΡΠΈΡΡΠ΅ΠΌΠΎΠΉ Π·Π°ΠΏΡΡΠΊΠ° ΠΌΠΎΠΆΠ΅Ρ Π±ΡΡΡ ΡΡΡΠ½ΡΠΌ, Π°Π²ΡΠΎΠΌΠ°ΡΠΈΡΠ΅ΡΠΊΠΈΠΌ ΠΈ Π΄ΠΈΡΡΠ°Π½ΡΠΈΠΎΠ½Π½ΡΠΌ. Π‘ΠΈΡΡΠ΅ΠΌΠ° ΠΏΡΡΠΊΠ° Π΄Π²ΠΈΠ³Π°ΡΠ΅Π»Ρ ΡΠΎΡΡΠΎΠΈΡ ΠΈΠ· ΠΎΡΠ½ΠΎΠ²Π½ΡΡ ΡΡΠ½ΠΊΡΠΈΠΎΠ½Π°Π»ΡΠ½ΡΡ ΡΡΡΡΠΎΠΉΡΡΠ²:
— ΠΠΊΠΊΡΠΌΡΠ»ΡΡΠΎΡΠ½Π°Ρ Π±Π°ΡΠ°ΡΠ΅Ρ
— Π‘ΡΠ°ΡΡΠ΅Ρ
— ΠΠ΅Ρ Π°Π½ΠΈΠ·ΠΌΡ ΡΠΏΡΠ°Π²Π»Π΅Π½ΠΈΡ Π·Π°ΠΏΡΡΠΊΠ° (Π·Π°ΠΌΠΎΠΊ Π·Π°ΠΆΠΈΠ³Π°Π½ΠΈΡ, Π±Π»ΠΎΠΊ ΡΠΏΡΠ°Π²Π»Π΅Π½ΠΈΡ Π°Π²ΡΠΎΠΌΠ°ΡΠΈΡΠ΅ΡΠΊΠΈΠΌ ΠΏΡΡΠΊΠΎΠΌ, ΡΠΈΡΡΠ΅ΠΌΠ° Π΄ΠΈΡΡΠ°Π½ΡΠΈΠΎΠ½Π½ΠΎΠ³ΠΎ ΡΠΏΡΠ°Π²Π»Π΅Π½ΠΈΡ)
— Π‘ΠΎΠ΅Π΄ΠΈΠ½ΠΈΡΠ΅Π»ΡΠ½ΡΠ΅ ΠΏΡΠΎΠ²ΠΎΠ΄Π° Π±ΠΎΠ»ΡΡΠΎΠ³ΠΎ ΡΠ΅ΡΠ΅Π½ΠΈΡ (ΠΌΠ½ΠΎΠ³ΠΎΠΏΡΠΎΠ²ΠΎΠ»ΠΎΡΠ½ΡΠ΅ ΠΌΠ΅Π΄Π½ΡΠ΅).
ΠΡΠ΅Π΄ΡΡΠ²Π»ΡΠ΅ΠΌΡΠ΅ ΡΡΠ΅Π±ΠΎΠ²Π°Π½ΠΈΡ ΠΊ ΡΠΈΡΡΠ΅ΠΌΠ΅ Π·Π°ΠΏΡΡΠΊΠ°: Π½Π°Π΄Π΅ΠΆΠ½ΠΎΡΡΡ ΡΠ°Π±ΠΎΡΡ ΡΡΠ°ΡΡΠ΅ΡΠ° (ΠΎΡΡΡΡΡΡΠ²ΠΈΠ΅ ΠΏΠΎΠ»ΠΎΠΌΠΎΠΊ Π² 45-50 ΡΡΡ. ΠΊΠΌ. ΠΏΡΠΎΠ±Π΅Π³Π°) Π²ΠΎΠ·ΠΌΠΎΠΆΠ½ΠΎΡΡΡ ΡΠ²Π΅ΡΠ΅Π½Π½ΠΎΠ³ΠΎ Π·Π°ΠΏΡΡΠΊΠ° Π² ΡΡΠ»ΠΎΠ²ΠΈΡΡ ΠΏΠΎΠ½ΠΈΠΆΠ΅Π½Π½ΡΡ ΡΠ΅ΠΌΠΏΠ΅ΡΠ°ΡΡΡ ΡΠΏΠΎΡΠΎΠ±Π½ΠΎΡΡΡ ΡΠΈΡΡΠ΅ΠΌΡ ΠΊ ΠΌΠ½ΠΎΠ³ΠΎΡΠ°Π·ΠΎΠ²ΡΠΌ ΠΏΡΡΠΊΠ°ΠΌ Π² ΡΠ΅ΡΠ΅Π½ΠΈΠ΅ ΠΊΠΎΡΠΎΡΠΊΠΎΠ³ΠΎ Π²ΡΠ΅ΠΌΠ΅Π½ΠΈ.
Π£ΡΡΡΠΎΠΉΡΡΠ²ΠΎ ΡΡΠ°ΡΡΠ΅ΡΠ° Π°Π²ΡΠΎΠΌΠΎΠ±ΠΈΠ»Ρ
ΠΡΠ½ΠΎΠ²Π½ΡΠΌ ΡΠ·Π»ΠΎΠΌ ΡΠΈΡΡΠ΅ΠΌΡ Π·Π°ΠΏΡΡΠΊΠ° Π΄Π²ΠΈΠ³Π°ΡΠ΅Π»Ρ ΡΠ²Π»ΡΠ΅ΡΡΡ ΡΡΠ°ΡΡΠ΅Ρ. ΠΡΠ΅Π΄ΡΡΠ°Π²Π»ΡΠ΅Ρ ΡΠΎΠ±ΠΎΠΉ ΡΠ»Π΅ΠΊΡΡΠΎΠ΄Π²ΠΈΠ³Π°ΡΠ΅Π»Ρ ΠΏΠΎΡΡΠΎΡΠ½Π½ΠΎΠ³ΠΎ ΡΠΎΠΊΠ° Π½Π°ΠΏΡΡΠΆΠ΅Π½ΠΈΠ΅ΠΌ 12 Π²ΠΎΠ»ΡΡ ΠΈ, ΡΠ°Π·Π²ΠΈΠ²Π°ΡΡΠΈΠΉ Π½Π° Ρ ΠΎΠ»ΠΎΡΡΠΎΠΌ Ρ ΠΎΠ΄Ρ ΠΏΡΠΈΠΌΠ΅ΡΠ½ΠΎ 5000 ΠΎΠ±\ΠΌΠΈΠ½. CΡ Π΅ΠΌΠ° ΡΡΠ°ΡΡΠ΅ΡΠ° Π‘ΡΠ°ΡΡΠ΅Ρ ΡΠΎΡΡΠΎΠΈΡ ΠΈΠ· ΠΏΡΡΠΈ ΠΎΡΠ½ΠΎΠ²Π½ΡΡ ΡΠ»Π΅ΠΌΠ΅Π½ΡΠΎΠ²: ΠΠΎΡΠΏΡΡ ΡΡΠ°ΡΡΠ΅ΡΠ° Π²ΡΠΏΠΎΠ»Π½Π΅Π½ ΠΈΠ· ΡΡΠ°Π»ΠΈ, ΠΈΠΌΠ΅Π΅Ρ ΡΠΎΡΠΌΡ ΡΠΈΠ»ΠΈΠ½Π΄ΡΠ°. ΠΠ° Π²Π½ΡΡΡΠ΅Π½Π½ΡΡ ΡΡΠ΅Π½ΠΊΡ ΠΊΠΎΡΠΏΡΡΠ° ΠΊΡΠ΅ΠΏΡΡΡΡ ΠΎΠ±ΠΌΠΎΡΠΊΠΈ Π²ΠΎΠ·Π±ΡΠΆΠ΄Π΅Π½ΠΈΡ (ΠΎΠ±ΡΡΠ½ΠΎ ΡΠ΅ΡΡΡΠ΅) ΡΠΎΠ²ΠΌΠ΅ΡΡΠ½ΠΎ Ρ ΡΠ΅ΡΠ΄Π΅ΡΠ½ΠΈΠΊΠ°ΠΌΠΈ (ΠΏΠΎΠ»ΡΡΠ°ΠΌΠΈ). ΠΡΠ΅ΠΏΠ΅ΠΆ ΠΏΡΠΎΠΈΡΡ ΠΎΠ΄ΠΈΡ Π²ΠΈΠ½ΡΠΎΠ²ΡΠΌ ΡΠΎΠ΅Π΄ΠΈΠ½Π΅Π½ΠΈΠ΅ΠΌ. ΠΠΈΠ½Ρ Π·Π°ΠΊΡΡΡΠΈΠ²Π°Π΅ΡΡΡ Π² ΡΠ΅ΡΠ΄Π΅ΡΠ½ΠΈΠΊ, ΠΊΠΎΡΠΎΡΡΠΉ ΠΏΡΠΈΠΆΠΈΠΌΠ°Π΅Ρ ΠΎΠ±ΠΌΠΎΡΠΊΡ ΠΊ ΡΡΠ΅Π½ΠΊΠ΅. ΠΠΎΡΠΏΡΡ ΠΈΠΌΠ΅Π΅Ρ ΡΠ΅Π·ΡΠ±ΠΎΠ²ΡΠ΅ ΡΠ΅Ρ Π½ΠΎΠ»ΠΎΠ³ΠΈΡΠ΅ΡΠΊΠΈΠ΅ ΠΎΡΠ²Π΅ΡΡΡΠΈΡ Π΄Π»Ρ ΠΊΡΠ΅ΠΏΠ»Π΅Π½ΠΈΡ ΠΏΠ΅ΡΠ΅Π΄Π½Π΅ΠΉ ΡΠ°ΡΡΠΈ, Π² ΠΊΠΎΡΠΎΡΠΎΠΉ ΠΏΡΠΎΠΈΡΡ ΠΎΠ΄ΠΈΡ Π΄Π²ΠΈΠΆΠ΅Π½ΠΈΠ΅ ΠΎΠ±Π³ΠΎΠ½Π½ΠΎΠΉ ΠΌΡΡΡΡ. Π―ΠΊΠΎΡΡ ΡΡΠ°ΡΡΠ΅ΡΠ° ΠΏΡΠ΅Π΄ΡΡΠ°Π²Π»ΡΠ΅Ρ ΡΠΎΠ±ΠΎΠΉ ΠΎΡΡ ΠΈΠ· Π»Π΅Π³ΠΈΡΠΎΠ²Π°Π½Π½ΠΎΠΉ ΡΡΠ°Π»ΠΈ, Π½Π° ΠΊΠΎΡΠΎΡΡΡ Π·Π°ΠΏΡΠ΅ΡΡΠΎΠ²Π°Π½ ΡΠ΅ΡΠ΄Π΅ΡΠ½ΠΈΠΊ ΡΠΊΠΎΡΡ ΠΈ ΠΊΠΎΠ»Π»Π΅ΠΊΡΠΎΡΠ½ΡΠ΅ ΠΏΠ»Π°ΡΡΠΈΠ½Ρ. Π‘Π΅ΡΠ΄Π΅ΡΠ½ΠΈΠΊ ΠΈΠΌΠ΅Π΅Ρ ΠΏΠ°Π·Ρ Π΄Π»Ρ ΡΠΊΠ»Π°Π΄ΠΊΠΈ ΠΎΠ±ΠΌΠΎΡΠΎΠΊ ΡΠΊΠΎΡΡ. ΠΠΎΠ½ΡΡ ΠΎΠ±ΠΌΠΎΡΠΎΠΊ Π½Π°Π΄Π΅ΠΆΠ½ΠΎ ΠΊΡΠ΅ΠΏΡΡΡΡ ΠΊ ΠΊΠΎΠ»Π»Π΅ΠΊΡΠΎΡΠ½ΡΠΌ ΠΏΠ»Π°ΡΡΠΈΠ½Π°ΠΌ. ΠΠΎΠ»Π»Π΅ΠΊΡΠΎΡΠ½ΡΠ΅ ΠΏΠ»Π°ΡΡΠΈΠ½Ρ ΡΠ°ΡΠΏΠΎΠ»ΠΎΠΆΠ΅Π½Ρ ΠΏΠΎ ΠΊΡΡΠ³Ρ ΠΈ ΠΆΠ΅ΡΡΠΊΠΎ ΡΡΡΠ°Π½ΠΎΠ²Π»Π΅Π½Ρ Π½Π° Π΄ΠΈΡΠ»Π΅ΠΊΡΡΠΈΡΠ΅ΡΠΊΠΎΠΉ ΠΎΡΠ½ΠΎΠ²Π΅. ΠΠΈΠ°ΠΌΠ΅ΡΡ ΡΠ΅ΡΠ΄Π΅ΡΠ½ΠΈΠΊΠ° Π½Π°ΠΏΡΡΠΌΡΡ ΡΠ²ΡΠ·Π°Π½ Ρ Π²Π½ΡΡΡΠ΅Π½Π½ΠΈΠΌ Π΄ΠΈΠ°ΠΌΠ΅ΡΡΠΎΠΌ ΠΊΠΎΡΠΏΡΡΠ° (ΡΠΎΠ²ΠΌΠ΅ΡΡΠ½ΠΎ Ρ ΠΎΠ±ΠΌΠΎΡΠΊΠ°ΠΌΠΈ). Π―ΠΊΠΎΡΡ ΠΊΡΠ΅ΠΏΠΈΡΡΡ Π² ΠΏΠ΅ΡΠ΅Π΄Π½Π΅ΠΉ ΠΊΡΡΡΠΊΠ΅ ΡΡΠ°ΡΡΠ΅ΡΠ° ΠΈ Π² Π·Π°Π΄Π½Π΅ΠΉ ΠΊΡΡΡΠΊΠ΅ ΠΏΡΠΈ ΠΏΠΎΠΌΠΎΡΠΈ Π²ΡΡΠ»ΠΎΠΊ, ΠΈΠ·Π³ΠΎΡΠΎΠ²Π»Π΅Π½Π½ΡΡ ΠΈΠ· Π»Π°ΡΡΠ½ΠΈ, ΡΠ΅ΠΆΠ΅ ΠΈΠ· ΠΌΠ΅Π΄ΠΈ. ΠΡΡΠ»ΠΊΠΈ ΠΎΠ΄Π½ΠΎΠ²ΡΠ΅ΠΌΠ΅Π½Π½ΠΎ ΡΠ²Π»ΡΡΡΡΡ ΠΈ ΠΏΠΎΠ΄ΡΠΈΠΏΠ½ΠΈΠΊΠ°ΠΌΠΈ. ΠΡΡΠ³ΠΈΠ²Π°ΡΡΠ΅Π΅ ΡΠ΅Π»Π΅ ΠΈΠ»ΠΈ ΡΡΠ³ΠΎΠ²ΠΎΠ΅ ΡΠ΅Π»Π΅ ΡΡΡΠ°Π½Π°Π²Π»ΠΈΠ²Π°Π΅ΡΡΡ Π½Π° ΠΊΠΎΡΠΏΡΡ ΡΡΠ°ΡΡΠ΅ΡΠ°. Π ΠΊΠΎΡΠΏΡΡΠ΅ ΡΡΠ³ΠΎΠ²ΠΎΠ³ΠΎ ΡΠ΅Π»Π΅, Π² Π·Π°Π΄Π½Π΅ΠΉ ΡΠ°ΡΡΠΈ Π½Π°Ρ ΠΎΠ΄ΡΡΡΡ ΡΠΈΠ»ΠΎΠ²ΡΠ΅ ΠΊΠΎΠ½ΡΠ°ΠΊΡΡ β Β«ΠΏΡΡΠ°ΠΊΠΈΒ», ΠΈ ΠΏΠΎΠ΄Π²ΠΈΠΆΠ½ΡΠΉ ΠΊΠΎΠ½ΡΠ°ΠΊΡ-ΠΏΠ΅ΡΠ΅ΠΌΡΡΠΊΠ°, Π²ΡΠΏΠΎΠ»Π½Π΅Π½Π½ΡΠ΅ ΠΈΠ· ΠΌΡΠ³ΠΊΠΈΡ ΠΌΠ΅ΡΠ°Π»Π»ΠΎΠ². Β«ΠΡΡΠ°ΠΊΠΈΒ» ΠΏΡΠ΅Π΄ΡΡΠ°Π²Π»ΡΡΡ ΡΠΎΠ±ΠΎΠΉ ΠΎΠ±ΡΠΊΠ½ΠΎΠ²Π΅Π½Π½ΡΠ΅ Π±ΠΎΠ»ΡΡ, Π·Π°ΠΏΡΠ΅ΡΡΠΎΠ²Π°Π½Π½ΡΠ΅ Π² ΡΠ±ΠΎΠ½ΠΈΡΠΎΠ²ΡΡ ΠΊΡΡΡΠΊΡ ΡΡΠ³ΠΎΠ²ΠΎΠ³ΠΎ ΡΠ΅Π»Π΅. ΠΡΠΈ ΠΏΠΎΠΌΠΎΡΠΈ Π³Π°Π΅ΠΊ ΠΊ Π½ΠΈΠΌ ΠΊΡΠ΅ΠΏΡΡΡΡ ΡΠΈΠ»ΠΎΠ²ΡΠ΅ ΠΏΡΠΎΠ²ΠΎΠ΄Π° ΠΎΡ Π°ΠΊΠΊΡΠΌΡΠ»ΡΡΠΎΡΠ° ΠΈ ΠΎΡ ΠΏΠ»ΡΡΠΎΠ²ΡΡ ΡΠ΅ΡΠΎΠΊ ΡΡΠ°ΡΡΠ΅ΡΠ°. Π‘Π΅ΡΠ΄Π΅ΡΠ½ΠΈΠΊ ΡΡΠ³ΠΎΠ²ΠΎΠ³ΠΎ ΡΠ΅Π»Π΅ ΡΠΎΠ΅Π΄ΠΈΠ½ΡΠ΅ΡΡΡ, ΡΠ΅ΡΠ΅Π· ΠΏΠΎΠ΄Π²ΠΈΠΆΠ½ΠΎΠ΅ Β«ΠΊΠΎΡΠΎΠΌΡΡΠ»ΠΎΒ» Ρ ΠΎΠ±Π³ΠΎΠ½Π½ΠΎΠΉ ΠΌΡΡΡΠΎΠΉ, Π² ΠΏΡΠΎΡΡΠΎΠ½Π°ΡΠΎΠ΄ΡΠ΅ ΠΈΠΌΠ΅Π½ΡΠ΅ΠΌΠΎΠΉ Π±Π΅Π½Π΄ΠΈΠΊΡΠΎΠΌ. ΠΠ±Π³ΠΎΠ½Π½Π°Ρ ΠΌΡΡΡΠ° (Π±Π΅Π½Π΄ΠΈΠΊΡ) ΠΊΡΠ΅ΠΏΠΈΡΡΡ ΠΏΠΎΠ΄Π²ΠΈΠΆΠ½ΠΎ Π½Π° Π²Π°Π» ΡΠΊΠΎΡΡ ΠΈ ΠΏΡΠ΅Π΄ΡΡΠ°Π²Π»ΡΠ΅Ρ ΡΠΎΠ±ΠΎΠΉ ΡΠΎΠ»ΠΈΠΊΠΎΠ²ΡΠΉ ΠΌΠ΅Ρ Π°Π½ΠΈΠ·ΠΌ, ΠΊΠΎΡΠΎΡΡΠΉ ΡΠ²ΡΠ·Π°Π½ Ρ ΡΠ΅ΡΡΠ΅ΡΠ½Π΅ΠΉ Π·Π°ΡΠ΅ΠΏΠ»Π΅Π½ΠΈΡ Ρ Π²Π΅Π½ΡΠΎΠΌ ΠΌΠ°Ρ ΠΎΠ²ΠΈΠΊΠ°. ΠΠΎΠ½ΡΡΡΡΠΊΡΠΈΡ ΡΠΎΠ±ΡΠ°Π½Π° ΡΠ°ΠΊ, ΡΡΠΎ ΠΏΡΠΈ ΠΏΠΎΠ΄Π°ΡΠ΅ ΠΊΡΡΡΡΡΠ΅Π³ΠΎ ΠΌΠΎΠΌΠ΅Π½ΡΠ° Π½Π° Π±Π΅Π½Π΄ΠΈΠΊΡ Π² ΠΎΠ΄Π½Ρ ΡΡΠΎΡΠΎΠ½Ρ, ΡΠΎΠ»ΠΈΠΊΠΈ, Π½Π°Ρ ΠΎΠ΄ΡΡΠΈΠ΅ΡΡ Π² ΡΠ΅ΠΏΠ°ΡΠ°ΡΠΎΡΠ΅ Π²ΡΡ ΠΎΠ΄ΡΡ ΠΈΠ· ΠΏΠ°Π·ΠΎΠ² ΡΠ΅ΠΏΠ°ΡΠ°ΡΠΎΡΠ° ΠΈ ΠΆΠ΅ΡΡΠΊΠΎ ΡΠΈΠΊΡΠΈΡΡΡΡ ΡΠ΅ΡΡΠ΅ΡΠ½Ρ ΠΊ Π½Π°ΡΡΠΆΠ½ΠΎΠΉ ΠΎΠ±ΠΎΠΉΠΌΠ΅. ΠΡΠΈ Π²ΡΠ°ΡΠ΅Π½ΠΈΠΈ Π² ΠΏΡΠΎΡΠΈΠ²ΠΎΠΏΠΎΠ»ΠΎΠΆΠ½ΡΡ ΡΡΠΎΡΠΎΠ½Ρ ΡΠΎΠ»ΠΈΠΊΠΈ Π·Π°ΠΏΠ°Π΄Π°ΡΡ Π² ΡΠ΅ΠΏΠ°ΡΠ°ΡΠΎΡ, ΠΈ ΡΠ΅ΡΡΠ΅ΡΠ½Ρ Π²ΡΠ°ΡΠ°Π΅ΡΡΡ Π½Π΅Π·Π°Π²ΠΈΡΠΈΠΌΠΎ ΠΎΡ Π½Π°ΡΡΠΆΠ½ΠΎΠΉ ΠΎΠ±ΠΎΠΉΠΌΡ. Π©Π΅ΡΠΊΠΎΠ΄Π΅ΡΠΆΠ°ΡΠ΅Π»Ρ ΡΠ»Π΅ΠΌΠ΅Π½Ρ ΡΡΠ°ΡΡΠ΅ΡΠ°, ΡΠ΅ΡΠ΅Π· ΠΊΠΎΡΠΎΡΡΠΉ ΠΏΠΎΠ΄Π°Π΅ΡΡΡ ΡΠ°Π±ΠΎΡΠ΅Π΅ Π½Π°ΠΏΡΡΠΆΠ΅Π½ΠΈΠ΅ Π½Π° ΠΌΠ΅Π΄Π½ΠΎ-Π³ΡΠ°ΡΠΈΡΠ½ΡΠ΅ ΡΠ΅ΡΠΊΠΈ, Π° Π·Π°ΡΠ΅ΠΌ ΠΏΠ΅ΡΠ΅Π΄Π°Π΅ΡΡΡ Π½Π° ΠΊΠΎΠ»Π»Π΅ΠΊΡΠΎΡΠ½ΡΠ΅ ΠΏΠ»Π°ΡΡΠΈΠ½Ρ ΡΠΊΠΎΡΡ. ΠΡΠΏΠΎΠ»Π½Π΅Π½ ΡΠ΅ΡΠΊΠΎΠ΄Π΅ΡΠΆΠ°ΡΠ΅Π»Ρ Π² Π²ΠΈΠ΄Π΅ Π΄ΠΈΡΠ»Π΅ΠΊΡΡΠΈΡΠ΅ΡΠΊΠΎΠΉ ΠΎΠ±ΠΎΠΉΠΌΡ Ρ ΠΌΠ΅ΡΠ°Π»Π»ΠΈΡΠ΅ΡΠΊΠΈΠΌΠΈ Π²ΡΡΠ°Π²ΠΊΠ°ΠΌΠΈ, Π²Π½ΡΡΡΠΈ ΠΊΠΎΡΠΎΡΡΡ Π½Π°Ρ ΠΎΠ΄ΡΡΡΡ ΡΠ΅ΡΠΊΠΈ. ΠΠΎΠ½ΡΠ°ΠΊΡΡ ΡΠ΅ΡΠΎΠΊ (ΠΌΡΠ³ΠΊΠΈΠΉ ΠΌΠ½ΠΎΠ³ΠΎΠΆΠΈΠ»ΡΠ½ΡΠΉ ΠΏΡΠΎΠ²ΠΎΠ΄) ΠΏΡΠΈ ΠΏΠΎΠΌΠΎΡΠΈ ΡΠΎΡΠ΅ΡΠ½ΠΎΠΉ ΡΠ²Π°ΡΠΊΠΈ ΠΏΡΠΈΠ²Π°ΡΠΈΠ²Π°ΡΡΡΡ ΠΊ ΠΏΠΎΠ»ΡΡΠ½ΡΠΌ ΠΏΠ»Π°ΡΡΠΈΠ½Π°ΠΌ. ΠΠΎΠ»ΡΡΠ½ΡΠΌΠΈ ΠΏΠ»Π°ΡΡΠΈΠ½Π°ΠΌΠΈ ΠΎΠ±ΡΡΠ½ΠΎ ΡΠ²Π»ΡΡΡΡΡ Β«Ρ Π²ΠΎΡΡΡΒ» ΠΎΠ±ΠΌΠΎΡΠΎΠΊ Π²ΠΎΠ·Π±ΡΠΆΠ΄Π΅Π½ΠΈΡ.
Β
ο»Ώ
infopedia.su
Π’ΠΎΡΠΌΠΎΠ·Π½ΡΠ΅ ΠΌΠ΅Ρ Π°Π½ΠΈΠ·ΠΌΡ Π°Π²ΡΠΎΠΌΠΎΠ±ΠΈΠ»Π΅ΠΉ.
Π’ΠΎΡΠΌΠΎΠ·Π½ΡΠ΅ ΠΌΠ΅Ρ Π°Π½ΠΈΠ·ΠΌΡ
ο»ΏΠ’ΠΎΡΠΌΠΎΠ·Π½ΠΎΠΉ ΠΌΠ΅Ρ
Π°Π½ΠΈΠ·ΠΌ β ΡΡΡΡΠΎΠΉΡΡΠ²ΠΎ, Π½Π΅ΠΏΠΎΡΡΠ΅Π΄ΡΡΠ²Π΅Π½Π½ΠΎ ΠΏΡΠ΅Π΄Π½Π°Π·Π½Π°ΡΠ΅Π½Π½ΠΎΠ΅ Π΄Π»Ρ ΡΠΎΠ·Π΄Π°Π½ΠΈΡ ΠΈΠ»ΠΈ ΠΈΠ·ΠΌΠ΅Π½Π΅Π½ΠΈΡ ΠΏΡΠΈΠ½ΡΠ΄ΠΈΡΠ΅Π»ΡΠ½ΠΎΠ³ΠΎ ΡΠΎΠΏΡΠΎΡΠΈΠ²Π»Π΅Π½ΠΈΡ Π΄Π²ΠΈΠΆΠ΅Π½ΠΈΡ Π°Π²ΡΠΎΡΡΠ°Π½ΡΠΏΠΎΡΡΠ½ΠΎΠ³ΠΎ ΡΡΠ΅Π΄ΡΡΠ²Π°.
Π ΡΠΎΡΠΌΠΎΠ·Π½ΡΡ
ΡΠΈΡΡΠ΅ΠΌΠ°Ρ
Π°Π²ΡΠΎΠΌΠΎΠ±ΠΈΠ»Π΅ΠΉ Π² ΠΊΠ°ΡΠ΅ΡΡΠ²Π΅ ΡΠΎΡΠΌΠΎΠ·Π½ΡΡ
ΠΌΠ΅Ρ
Π°Π½ΠΈΠ·ΠΌΠΎΠ² Π½Π°ΠΈΠ±ΠΎΠ»Π΅Π΅ ΡΠ°ΡΡΠΎ ΠΈΡΠΏΠΎΠ»ΡΠ·ΡΡΡ ΡΡΠΈΠΊΡΠΈΠΎΠ½Π½ΡΠ΅ ΡΡΡΡΠΎΠΉΡΡΠ²Π°, Π² ΠΊΠΎΡΠΎΡΡΡ
ΠΈΡΠΊΡΡΡΡΠ²Π΅Π½Π½ΠΎΠ΅ ΡΠΎΠΏΡΠΎΡΠΈΠ²Π»Π΅Π½ΠΈΠ΅ Π΄Π²ΠΈΠΆΠ΅Π½ΠΈΡ ΡΠΎΠ·Π΄Π°Π΅ΡΡΡ Π·Π° ΡΡΠ΅Ρ ΡΠΈΠ» ΡΡΠ΅Π½ΠΈΡ ΠΌΠ΅ΠΆΠ΄Ρ Π²ΡΠ°ΡΠ°ΡΡΠΈΠΌΠΈΡΡ Π΄Π΅ΡΠ°Π»ΡΠΌΠΈ, ΡΠ²ΡΠ·Π°Π½Π½ΡΠΌΠΈ Ρ ΠΊΠΎΠ»Π΅ΡΠΎΠΌ, ΠΈ Π½Π΅ΠΏΠΎΠ΄Π²ΠΈΠΆΠ½ΡΠΌΠΈ Π΄Π΅ΡΠ°Π»ΡΠΌΠΈ, ΡΠ²ΡΠ·Π°Π½Π½ΡΠΌΠΈ Ρ Ρ
ΠΎΠ΄ΠΎΠ²ΠΎΠΉ ΡΠ°ΡΡΡΡ, Π°Π³ΡΠ΅Π³Π°ΡΠ°ΠΌΠΈ ΡΡΠ°Π½ΡΠΌΠΈΡΡΠΈΠΈ ΠΈΠ»ΠΈ Π½Π΅ΡΡΡΠ΅ΠΉ ΡΠΈΡΡΠ΅ΠΌΠΎΠΉ Π°Π²ΡΠΎΠΌΠΎΠ±ΠΈΠ»Ρ.
ΠΡΠΊΠ»ΡΡΠ΅Π½ΠΈΠ΅ ΠΌΠΎΠ³ΡΡ ΡΠΎΡΡΠ°Π²Π»ΡΡΡ Π²ΡΠΏΠΎΠΌΠΎΠ³Π°ΡΠ΅Π»ΡΠ½ΡΠ΅ ΡΠΎΡΠΌΠΎΠ·Π½ΡΠ΅ ΡΠΈΡΡΠ΅ΠΌΡ, ΠΈΡΠΏΠΎΠ»ΡΠ·ΡΡΡΠΈΠ΅ Π΄Π»Ρ ΡΠΌΠ΅Π½ΡΡΠ΅Π½ΠΈΡ ΡΠΊΠΎΡΠΎΡΡΠΈ Π°Π²ΡΠΎΠΌΠΎΠ±ΠΈΠ»Ρ Π΅ΡΡΠ΅ΡΡΠ²Π΅Π½Π½ΡΠ΅ ΡΠΈΠ»Ρ ΡΡΠ΅Π½ΠΈΡ Π² ΡΡΠ°Π½ΡΠΌΠΈΡΡΠΈΠΈ ΠΈ Π΄Π²ΠΈΠ³Π°ΡΠ΅Π»Π΅, Π° ΡΠ°ΠΊΠΆΠ΅ ΠΏΡΠΎΡΠΈΠ²ΠΎΠ΄Π°Π²Π»Π΅Π½ΠΈΠ΅ Π² Π²ΡΠΏΡΡΠΊΠ½ΠΎΠΉ ΡΠΈΡΡΠ΅ΠΌΠ΅ Π΄Π²ΠΈΠ³Π°ΡΠ΅Π»Ρ.
Π ΠΊΠ°ΡΠ΅ΡΡΠ²Π΅ ΡΠΎΡΠΌΠΎΠ·Π½ΠΎΠΉ ΡΠΈΡΡΠ΅ΠΌΡ ΡΠΏΠΎΡΡΠΈΠ²Π½ΡΡ
ΠΈ Π³ΠΎΠ½ΠΎΡΠ½ΡΡ
Π°Π²ΡΠΎΠΌΠΎΠ±ΠΈΠ»Π΅ΠΉ ΠΈΠ½ΠΎΠ³Π΄Π° ΠΏΡΠΈΠΌΠ΅Π½ΡΡΡΡΡ ΡΡΡΡΠΎΠΉΡΡΠ²Π°, ΠΈΡΠΏΠΎΠ»ΡΠ·ΡΡΡΠΈΠ΅ Π²Π½Π΅ΡΠ½ΠΈΠ΅ ΠΈΡΡΠΎΡΠ½ΠΈΠΊΠΈ ΡΠ½Π΅ΡΠ³ΠΈΠΈ, Π½Π°ΠΏΡΠΈΠΌΠ΅Ρ, ΠΏΠ°ΡΠ°ΡΡΡ. Π ΠΌΠ°ΡΡΠΎΠ²ΠΎΠΌ Π°Π²ΡΠΎΠΌΠΎΠ±ΠΈΠ»Π΅ΡΡΡΠΎΠ΅Π½ΠΈΠΈ ΡΠ°ΠΊΠΈΠ΅ ΡΠΎΡΠΌΠΎΠ·Π½ΡΠ΅ ΡΠΈΡΡΠ΅ΠΌΡ Π½Π΅ ΠΏΡΠΈΠΌΠ΅Π½ΡΡΡΡΡ.
- ΠΏΠΎ ΡΠΎΡΠΌΠ΅ Π²ΡΠ°ΡΠ°ΡΡΠΈΡ ΡΡ Π΄Π΅ΡΠ°Π»Π΅ΠΉ ΡΠ°Π·Π»ΠΈΡΠ°ΡΡ Π±Π°ΡΠ°Π±Π°Π½Π½ΡΠ΅, Π΄ΠΈΡΠΊΠΎΠ²ΡΠ΅ ΠΈ ΡΠΊΠΈΠ²ΠΎΠ²ΡΠ΅ ΡΠΎΡΠΌΠΎΠ·Π½ΡΠ΅ ΠΌΠ΅Ρ Π°Π½ΠΈΠ·ΠΌΡ;
- ΠΏΠΎ ΡΠΎΡΠΌΠ΅ ΡΡΡΡΠΈΡ ΡΡ ΠΏΠΎΠ²Π΅ΡΡ Π½ΠΎΡΡΠ΅ΠΉ — ΠΊΠΎΠ»ΠΎΠ΄ΠΎΡΠ½ΡΠ΅ ΠΈ Π»Π΅Π½ΡΠΎΡΠ½ΡΠ΅;
- Π² Π·Π°Π²ΠΈΡΠΈΠΌΠΎΡΡΠΈ ΠΎΡ ΠΌΠ΅ΡΡΠ° ΡΡΡΠ°Π½ΠΎΠ²ΠΊΠΈ ΡΠ°Π·Π»ΠΈΡΠ°ΡΡ ΠΊΠΎΠ»Π΅ΡΠ½ΡΠ΅ ΠΈ ΡΡΠ°Π½ΡΠΌΠΈΡΡΠΈΠΎΠ½Π½ΡΠ΅ ΡΠΎΡΠΌΠΎΠ·Π½ΡΠ΅ ΠΌΠ΅Ρ Π°Π½ΠΈΠ·ΠΌΡ.
Π ΡΠ°Π±ΠΎΡΠΈΡ , ΡΡΠΎΡΠ½ΠΎΡΠ½ΡΡ ΠΈ Π·Π°ΠΏΠ°ΡΠ½ΡΡ ΡΠΎΡΠΌΠΎΠ·Π½ΡΡ ΡΠΈΡΡΠ΅ΠΌΠ°Ρ Π°Π²ΡΠΎΠΌΠΎΠ±ΠΈΠ»Π΅ΠΉ Π² ΠΏΠΎΠ΄Π°Π²Π»ΡΡΡΠ΅ΠΌ Π±ΠΎΠ»ΡΡΠΈΠ½ΡΡΠ²Π΅ ΠΏΡΠΈΠΌΠ΅Π½ΡΡΡΡΡ Π±Π°ΡΠ°Π±Π°Π½Π½ΡΠ΅ ΠΈ Π΄ΠΈΡΠΊΠΎΠ²ΡΠ΅ ΡΠΎΡΠΌΠΎΠ·Π½ΡΠ΅ ΠΌΠ΅Ρ Π°Π½ΠΈΠ·ΠΌΡ, ΠΏΠΎΡΠΊΠΎΠ»ΡΠΊΡ ΠΎΠ½ΠΈ Π½Π°ΠΈΠ±ΠΎΠ»Π΅Π΅ ΠΏΠΎΠ»Π½ΠΎ ΠΎΡΠ²Π΅ΡΠ°ΡΡ ΠΏΡΠ΅Π΄ΡΡΠ²Π»ΡΠ΅ΠΌΡΠΌ ΡΡΠ΅Π±ΠΎΠ²Π°Π½ΠΈΡΠΌ β Π½Π°Π΄Π΅ΠΆΠ½ΠΎΡΡΡ ΠΈ ΡΡΡΠ΅ΠΊΡΠΈΠ²Π½ΠΎΡΡΡ, Ρ ΠΎΡΠΎΡΠΈΠΉ ΠΎΡΠ²ΠΎΠ΄ ΡΠ΅ΠΏΠ»Π° ΠΎΡ Π΄Π΅ΡΠ°Π»Π΅ΠΉ ΠΈ ΡΠ·Π»ΠΎΠ², ΠΎΠ±Π΅ΡΠΏΠ΅ΡΠ΅Π½ΠΈΠ΅ ΠΏΠ»Π°Π²Π½ΠΎΡΡΠΈ ΡΠΎΡΠΌΠΎΠΆΠ΅Π½ΠΈΡ ΠΈ Π²ΡΡΠΎΠΊΠΈΠΉ ΠΠΠ. ΠΡΠΏΠΎΠ»ΡΠ·ΡΠ΅ΠΌΡΠ΅ Π² ΠΊΠΎΠ½ΡΡΡΡΠΊΡΠΈΡΡ ΠΌΠ½ΠΎΠ³ΠΈΡ Π΄ΠΎΡΠΎΠΆΠ½ΡΡ ΠΈ ΡΠ΅Π»ΡΡΠΊΠΎΡ ΠΎΠ·ΡΠΉΡΡΠ²Π΅Π½Π½ΡΡ ΠΌΠ°ΡΠΈΠ½ Π»Π΅Π½ΡΠΎΡΠ½ΡΠ΅ ΡΠΎΡΠΌΠΎΠ·Π½ΡΠ΅ ΠΌΠ΅Ρ Π°Π½ΠΈΠ·ΠΌΡ, ΠΈΡΠΏΠΎΠ»ΡΠ·ΡΡΡΠΈΠ΅ ΡΡΠ΅Π½ΠΈΠ΅ ΠΌΠ΅ΠΆΠ΄Ρ ΡΠΎΡΠΌΠΎΠ·Π½ΠΎΠΉ Π»Π΅Π½ΡΠΎΠΉ (ΠΈΠ»ΠΈ ΡΠ΅ΠΌΠ½Π΅ΠΌ) ΠΈ ΡΠΊΠΈΠ²ΠΎΠΌ, Π½Π° Π°Π²ΡΠΎΠΌΠΎΠ±ΠΈΠ»ΡΡ ΠΏΡΠΈΠΌΠ΅Π½Π΅Π½ΠΈΠ΅ Π½Π΅ Π½Π°ΡΠ»ΠΈ.
Π Π±Π°ΡΠ°Π±Π°Π½Π½ΡΡ ΡΠΎΡΠΌΠΎΠ·Π½ΡΡ ΠΌΠ΅Ρ Π°Π½ΠΈΠ·ΠΌΠ°Ρ (ΡΠΈΡ. 1) ΠΈΡΠΏΠΎΠ»ΡΠ·ΡΡΡΡΡ ΡΠΈΠ»Ρ ΡΡΠ΅Π½ΠΈΡ, Π²ΠΎΠ·Π½ΠΈΠΊΠ°ΡΡΠΈΠ΅ ΠΌΠ΅ΠΆΠ΄Ρ Π²Π½ΡΡΡΠ΅Π½Π½Π΅ΠΉ ΠΏΠΎΠ²Π΅ΡΡ Π½ΠΎΡΡΡΡ ΡΠΈΠ»ΠΈΠ½Π΄ΡΠΈΡΠ΅ΡΠΊΠΎΠ³ΠΎ Π±Π°ΡΠ°Π±Π°Π½Π°, Π²ΡΠ°ΡΠ°ΡΡΠ΅Π³ΠΎΡΡ Π²ΠΌΠ΅ΡΡΠ΅ Ρ ΠΊΠΎΠ»Π΅ΡΠΎΠΌ ΠΈΠ»ΠΈ ΠΏΠΎΠ΄Π²ΠΈΠΆΠ½ΡΠΌ ΡΠ»Π΅ΠΌΠ΅Π½ΡΠΎΠΌ ΡΡΠ°Π½ΡΠΌΠΈΡΡΠΈΠΈ, ΠΈ ΡΠΎΡΠΌΠΎΠ·Π½ΡΠΌΠΈ ΠΊΠΎΠ»ΠΎΠ΄ΠΊΠ°ΠΌΠΈ, ΡΠ°ΡΠ½ΠΈΡΠ½ΠΎ ΡΠΎΠ΅Π΄ΠΈΠ½ΡΠ΅ΠΌΡΠΌΠΈ Ρ Π½Π΅ΠΏΠΎΠ΄Π²ΠΈΠΆΠ½ΡΠΌΠΈ ΡΠ»Π΅ΠΌΠ΅Π½ΡΠ°ΠΌΠΈ Ρ ΠΎΠ΄ΠΎΠ²ΠΎΠΉ ΡΠ°ΡΡΠΈ, Π½Π΅ΡΡΡΠ΅ΠΉ ΡΠΈΡΡΠ΅ΠΌΡ ΠΈΠ»ΠΈ ΡΡΠ°Π½ΡΠΌΠΈΡΡΠΈΠΈ.
Π Π΄ΠΈΡΠΊΠΎΠ²ΡΡ ΡΠΎΡΠΌΠΎΠ·Π½ΡΡ ΠΌΠ΅Ρ Π°Π½ΠΈΠ·ΠΌΠ°Ρ (ΡΠΈΡ. 2) ΠΈΡΠΏΠΎΠ»ΡΠ·ΡΡΡΡΡ ΡΠΈΠ»Ρ ΡΡΠ΅Π½ΠΈΡ, Π²ΠΎΠ·Π½ΠΈΠΊΠ°ΡΡΠΈΠ΅ ΠΌΠ΅ΠΆΠ΄Ρ Π±ΠΎΠΊΠΎΠ²ΡΠΌΠΈ ΠΏΠΎΠ²Π΅ΡΡ Π½ΠΎΡΡΡΠΌΠΈ ΠΌΠ΅ΡΠ°Π»Π»ΠΈΡΠ΅ΡΠΊΠΎΠ³ΠΎ Π΄ΠΈΡΠΊΠ°, Π²ΡΠ°ΡΠ°ΡΡΠ΅Π³ΠΎΡΡ Π²ΠΌΠ΅ΡΡΠ΅ Ρ ΠΊΠΎΠ»Π΅ΡΠΎΠΌ, ΠΈ ΠΊΠΎΠ»ΠΎΠ΄ΠΊΠ°ΠΌΠΈ, ΠΊΠΎΡΠΏΡΡ ΠΊΠΎΡΠΎΡΡΡ ΠΊΡΠ΅ΠΏΠΈΡΡΡ ΠΊ Π½Π΅ΠΏΠΎΠ΄Π²ΠΈΠΆΠ½ΡΠΌ ΡΠ»Π΅ΠΌΠ΅Π½ΡΠ°ΠΌ Ρ ΠΎΠ΄ΠΎΠ²ΠΎΠΉ ΡΠ°ΡΡΠΈ. Π’ΠΎΡΠΌΠΎΠ·Π½ΠΎΠΉ ΠΏΡΠΈΠ²ΠΎΠ΄ Π² ΠΎΠ±ΠΎΠΈΡ ΠΌΠ΅Ρ Π°Π½ΠΈΠ·ΠΌΠ°Ρ Π²ΠΎΠ·Π΄Π΅ΠΉΡΡΠ²ΡΠ΅Ρ Π½Π° ΡΠΎΡΠΌΠΎΠ·Π½ΡΠ΅ ΠΊΠΎΠ»ΠΎΠ΄ΠΊΠΈ, ΠΏΡΠΈΠΆΠΈΠΌΠ°Ρ ΠΈΡ ΠΊ ΠΏΠΎΠ²Π΅ΡΡ Π½ΠΎΡΡΡΠΌ Π±Π°ΡΠ°Π±Π°Π½Π° ΠΈΠ»ΠΈ Π΄ΠΈΡΠΊΠ°, ΡΠΎΠ·Π΄Π°Π²Π°Ρ ΡΠΈΠ»Ρ ΡΡΠ΅Π½ΠΈΡ ΡΡΠ΅Π±ΡΠ΅ΠΌΠΎΠΉ ΡΡΡΠ΅ΠΊΡΠΈΠ²Π½ΠΎΡΡΠΈ.
***
ΠΠΎΡΡΠΎΠΈΠ½ΡΡΠ²Π° ΠΈ Π½Π΅Π΄ΠΎΡΡΠ°ΡΠΊΠΈ ΡΠΎΡΠΌΠΎΠ·Π½ΡΡ ΠΌΠ΅Ρ Π°Π½ΠΈΠ·ΠΌΠΎΠ²
Π Π΄ΠΎΡΡΠΎΠΈΠ½ΡΡΠ²Π°ΠΌ Π±Π°ΡΠ°Π±Π°Π½Π½ΡΡ ΡΠΎΡΠΌΠΎΠ·Π½ΡΡ ΠΌΠ΅Ρ Π°Π½ΠΈΠ·ΠΌΠΎΠ² ΡΠ»Π΅Π΄ΡΠ΅Ρ ΠΎΡΠ½Π΅ΡΡΠΈ Π±ΠΎΠ»Π΅Π΅ Π²ΡΡΠΎΠΊΡΡ ΡΡΡΠ΅ΠΊΡΠΈΠ²Π½ΠΎΡΡΡ ΠΏΡΠΈ ΠΎΠ΄ΠΈΠ½Π°ΠΊΠΎΠ²ΠΎΠΌ ΡΡΠΈΠ»ΠΈΠΈ Π½Π° ΠΈΡΠΏΠΎΠ»Π½ΠΈΡΠ΅Π»ΡΠ½ΡΠ΅ ΡΠ»Π΅ΠΌΠ΅Π½ΡΡ (ΠΊΠΎΠ»ΠΎΠ΄ΠΊΠΈ) ΠΏΠΎ ΡΡΠ°Π²Π½Π΅Π½ΠΈΡ Ρ Π΄ΠΈΡΠΊΠΎΠ²ΡΠΌ ΡΠΎΡΠΌΠΎΠ·Π½ΡΠΌ ΠΌΠ΅Ρ Π°Π½ΠΈΠ·ΠΌΠΎΠΌ ΠΏΡΠΈ ΠΏΡΠΎΡΠΈΡ ΡΠ°Π²Π½ΡΡ ΡΡΠ»ΠΎΠ²ΠΈΡΡ . ΠΡΠΎ Π΄ΠΎΡΡΠΈΠ³Π°Π΅ΡΡΡ Π²ΠΎΠ·ΠΌΠΎΠΆΠ½ΠΎΡΡΡΡ ΠΈΡΠΏΠΎΠ»ΡΠ·ΠΎΠ²Π°Π½ΠΈΡ Π±ΠΎΠ»ΡΡΠ΅ΠΉ ΠΏΠ»ΠΎΡΠ°Π΄ΠΈ ΡΡΠ΅Π½ΠΈΡ ΠΌΠ΅ΠΆΠ΄Ρ Π±Π°ΡΠ°Π±Π°Π½ΠΎΠΌ ΠΈ ΠΊΠΎΠ»ΠΎΠ΄ΠΊΠ°ΠΌΠΈ, Π° ΡΠ°ΠΊΠΆΠ΅ ΡΠΎΠ·Π΄Π°Π²Π°ΡΡ ΠΏΠΎΠ»ΡΡΠ΅Π½Π½ΠΎΠΉ ΡΠΈΠ»ΠΎΠΉ ΡΡΠ΅Π½ΠΈΡ ΠΊΡΡΡΡΡΠΈΠΉ ΠΌΠΎΠΌΠ΅Π½Ρ Ρ Π±Γ³Π»ΡΡΠΈΠΌ ΠΏΠ»Π΅ΡΠΎΠΌ, ΡΠ°Π²Π½ΡΠΌ Π²Π½ΡΡΡΠ΅Π½Π½Π΅ΠΌΡ ΡΠ°Π΄ΠΈΡΡΡ Π±Π°ΡΠ°Π±Π°Π½Π°.
ΠΠ»Π΅ΡΠΎ ΡΠΈΠ»Ρ ΡΡΠ΅Π½ΠΈΡ, ΡΠΎΠ·Π΄Π°Π²Π°Π΅ΠΌΠΎΠΉ Π΄ΠΈΡΠΊΠΎΠ²ΡΠΌ ΠΌΠ΅Ρ Π°Π½ΠΈΠ·ΠΌΠΎΠΌ, ΠΌΠ΅Π½ΡΡΠ΅ Π½Π°ΡΡΠΆΠ½ΠΎΠ³ΠΎ Π΄ΠΈΠ°ΠΌΠ΅ΡΡΠ° Π΄ΠΈΡΠΊΠ°, ΠΏΠΎΡΠΊΠΎΠ»ΡΠΊΡ ΡΡΠΌΠΌΠ°ΡΠ½Π°Ρ ΡΠΈΠ»Π° ΡΡΠ΅Π½ΠΈΡ ΠΏΡΠΈΠ»ΠΎΠΆΠ΅Π½Π° ΠΊ Π΅Π³ΠΎ Π±ΠΎΠΊΠΎΠ²ΠΎΠΉ ΠΏΠΎΠ²Π΅ΡΡ Π½ΠΎΡΡΠΈ Π½Π° Π½Π΅ΠΊΠΎΡΠΎΡΠΎΠΌ ΡΠ°ΡΡΡΠΎΡΠ½ΠΈΠΈ ΠΎΡ ΠΎΠ±ΠΎΠ΄Π°, Ρ. Π΅. ΡΠΌΠ΅ΡΠ΅Π½Π° ΠΊ ΠΎΡΠΈ ΠΊΠΎΠ»Π΅ΡΠ°. ΠΠΎ ΡΡΠΎΠΉ ΠΏΡΠΈΡΠΈΠ½Π΅, ΠΏΡΠΈ ΠΎΠ΄ΠΈΠ½Π°ΠΊΠΎΠ²ΠΎΠΉ ΡΠΈΠ»Π΅ ΡΡΠ΅Π½ΠΈΡ ΠΈ Π³Π°Π±Π°ΡΠΈΡΠ°Ρ ΡΠΎΡΠΌΠΎΠ·Π½ΠΎΠ³ΠΎ ΠΌΠ΅Ρ Π°Π½ΠΈΠ·ΠΌΠ°, Π±Π°ΡΠ°Π±Π°Π½Π½ΡΠ΅ ΡΠΎΡΠΌΠΎΠ·Π° ΡΠΎΠ·Π΄Π°ΡΡ Π±ΠΎΠ»ΡΡΠΈΠΉ ΡΠΎΡΠΌΠΎΠ·ΡΡΠΈΠΉ ΠΌΠΎΠΌΠ΅Π½Ρ, ΡΠ΅ΠΌ Π΄ΠΈΡΠΊΠΎΠ²ΡΠ΅.
Π’ΠΎΡΠΌΠΎΠ·Π½ΡΠ΅ ΠΊΠΎΠ»ΠΎΠ΄ΠΊΠΈ Π±Π°ΡΠ°Π±Π°Π½Π½ΡΡ ΠΌΠ΅Ρ Π°Π½ΠΈΠ·ΠΌΠΎΠ² ΠΈΠΌΠ΅ΡΡ Π±Γ³Π»ΡΡΡΡ ΠΏΠ»ΠΎΡΠ°Π΄Ρ ΡΡΠ΅Π½ΠΈΡ, ΡΠ΅ΠΌ ΠΊΠΎΠ»ΠΎΠ΄ΠΊΠΈ Π΄ΠΈΡΠΊΠΎΠ²ΡΡ ΡΠΎΡΠΌΠΎΠ·ΠΎΠ², ΠΏΠΎΡΡΠΎΠΌΡ ΠΎΠ½ΠΈ ΠΈΠ·Π½Π°ΡΠΈΠ²Π°ΡΡΡΡ ΠΌΠ΅Π½Π΅Π΅ ΠΈΠ½ΡΠ΅Π½ΡΠΈΠ²Π½ΠΎ. ΠΠ΅ΡΠ°Π»ΠΈ Π±Π°ΡΠ°Π±Π°Π½Π½ΠΎΠ³ΠΎ ΡΠΎΡΠΌΠΎΠ·Π½ΠΎΠ³ΠΎ ΠΌΠ΅Ρ Π°Π½ΠΈΠ·ΠΌΠ° Π»ΡΡΡΠ΅ Π·Π°ΡΠΈΡΠ΅Π½Ρ ΠΎΡ Π½Π΅Π±Π»Π°Π³ΠΎΠΏΡΠΈΡΡΠ½ΠΎΠ³ΠΎ Π²ΠΎΠ·Π΄Π΅ΠΉΡΡΠ²ΠΈΡ Π²Π½Π΅ΡΠ½Π΅ΠΉ ΡΡΠ΅Π΄Ρ, ΠΏΠΎΡΡΠΎΠΌ ΠΌΠ΅Π½ΡΡΠ΅ ΠΏΠΎΠ΄Π²Π΅ΡΠΆΠ΅Π½Ρ ΠΌΠ΅Ρ Π°Π½ΠΈΡΠ΅ΡΠΊΠΈΠΌ ΠΏΠΎΠ²ΡΠ΅ΠΆΠ΄Π΅Π½ΠΈΡΠΌ, ΠΊΠΎΡΡΠΎΠ·ΠΈΠΈ ΠΈ Π°Π±ΡΠ°Π·ΠΈΠ²Π½ΠΎΠΌΡ ΠΈΠ·Π½ΠΎΡΡ.
ο»ΏΠΡΠΎΠΌΠ΅ ΡΡΠΎΠ³ΠΎ, Π±Π°ΡΠ°Π±Π°Π½Π½ΡΠ΅ ΡΠΎΡΠΌΠΎΠ·Π½ΡΠ΅ ΠΌΠ΅Ρ Π°Π½ΠΈΠ·ΠΌΡ ΠΈΠΌΠ΅ΡΡ Π±ΠΎΠ»Π΅Π΅ ΠΆΠ΅ΡΡΠΊΡΡ ΠΊΠΎΠ½ΡΡΡΡΠΊΡΠΈΡ ΡΠΎΡΠΌΠΎΠ·ΡΡΠ΅Π³ΠΎ ΡΠ»Π΅ΠΌΠ΅Π½ΡΠ° (Π±Π°ΡΠ°Π±Π°Π½Π°), Π±Π»Π°Π³ΠΎΠ΄Π°ΡΡ ΡΠ΅ΠΌΡ ΠΎΠ½ ΠΌΠ΅Π½Π΅Π΅ ΠΏΠΎΠ΄Π²Π΅ΡΠΆΠ΅Π½ Π΄Π΅ΡΠΎΡΠΌΠ°ΡΠΈΠΈ, ΡΠ΅ΠΌ Π΄ΠΈΡΠΊ. ΠΠ΄Π½Π°ΠΊΠΎ ΠΏΡΠΎΡΡΡΠ°Π½ΡΡΠ²Π΅Π½Π½Π°Ρ ΡΠΎΡΠΌΠ° Π±Π°ΡΠ°Π±Π°Π½Π° ΡΡΠ»ΠΎΠΆΠ½ΡΠ΅Ρ Π΅Π³ΠΎ Π±Π°Π»Π°Π½ΡΠΈΡΠΎΠ²ΠΊΡ.
Π’Π°ΠΊΠΈΠ΅ ΠΊΠ°ΡΠ΅ΡΡΠ²Π°, ΠΊΠ°ΠΊ ΡΠΎΠ·Π΄Π°Π²Π°Π΅ΠΌΡΠΉ ΡΡΡΠ΅ΠΊΡΠΈΠ²Π½ΡΠΉ ΡΠΎΡΠΌΠΎΠ·Π½ΠΎΠΉ ΠΌΠΎΠΌΠ΅Π½Ρ ΠΈ ΠΏΡΠΎΡΠ½ΠΎΡΡΠ½ΡΠ΅ Π΄ΠΎΡΡΠΎΠΈΠ½ΡΡΠ²Π° Π±Π°ΡΠ°Π±Π°Π½Π° ΡΠ²Π»ΡΡΡΡΡ ΠΎΡΠ½ΠΎΠ²Π½ΠΎΠΉ ΠΏΡΠΈΡΠΈΠ½ΠΎΠΉ ΡΠΈΡΠΎΠΊΠΎΠ³ΠΎ ΠΏΡΠΈΠΌΠ΅Π½Π΅Π½ΠΈΡ Π±Π°ΡΠ°Π±Π°Π½Π½ΡΡ ΡΠΎΡΠΌΠΎΠ·Π½ΡΡ ΠΌΠ΅Ρ Π°Π½ΠΈΠ·ΠΌΠΎΠ² Π² ΡΠΈΡΡΠ΅ΠΌΠ°Ρ ΡΠΎΡΠΌΠΎΠΆΠ΅Π½ΠΈΡ Π³ΡΡΠ·ΠΎΠ²ΡΡ Π°Π²ΡΠΎΠΌΠ±ΠΈΠ»Π΅ΠΉ ΠΈ Π°Π²ΡΠΎΠ±ΡΡΠΎΠ². Π ΡΠΎΠ²ΡΠ΅ΠΌΠ΅Π½Π½ΡΡ Π»Π΅Π³ΠΊΠΎΠ²ΡΡ Π°Π²ΡΠΎΠΌΠΎΠ±ΠΈΠ»ΡΡ ΠΈΡ ΠΏΡΠΈΠΌΠ΅Π½Π΅Π½ΠΈΠ΅ ΠΎΠ³ΡΠ°Π½ΠΈΡΠ΅Π½ΠΎ ΠΈΠ·-Π·Π° ΡΡΠ°Π²Π½ΠΈΡΠ΅Π»ΡΠ½ΠΎ Π±ΠΎΠ»ΡΡΠΎΠΉ ΠΌΠ°ΡΡΡ ΠΈ Π³Π°Π±Π°ΡΠΈΡΠΎΠ².
Π Π΄ΠΎΡΡΠΎΠΈΠ½ΡΡΠ²Π°ΠΌ Π΄ΠΈΡΠΊΠΎΠ²ΡΡ
ΡΠΎΡΠΌΠΎΠ·Π½ΡΡ
ΠΌΠ΅Ρ
Π°Π½ΠΈΠ·ΠΌΠΎΠ² ΠΌΠΎΠΆΠ½ΠΎ ΠΎΡΠ½Π΅ΡΡΠΈ ΠΌΠ°Π»ΡΠ΅ Π³Π°Π±Π°ΡΠΈΡΡ ΠΈ ΠΌΠ°ΡΡΡ, ΡΡΡΠ΅ΠΊΡΠΈΠ²Π½ΠΎΠ΅ ΠΎΡ
Π»Π°ΠΆΠ΄Π΅Π½ΠΈΠ΅ Π΄Π΅ΡΠ°Π»Π΅ΠΉ ΠΌΠ΅Ρ
Π°Π½ΠΈΠ·ΠΌΠ° ΠΈΠ·-Π·Π° Π±ΠΎΠ»ΡΡΠΎΠΉ ΠΏΠ»ΠΎΡΠ°Π΄ΠΈ ΠΎΡ
Π»Π°ΠΆΠ΄Π΅Π½ΠΈΡ ΠΈ Π²ΠΎΠ·ΠΌΠΎΠΆΠ½ΠΎΡΡΠΈ Π²Π΅Π½ΡΠΈΠ»ΠΈΡΠΎΠ²Π°Π½ΠΈΡ, Π½Π΅Π·Π°Π²ΠΈΡΠΈΠΌΠΎΡΡΡ Π΄Π΅ΠΉΡΡΠ²ΠΈΡ ΡΠΎΡΠΌΠΎΠ·ΠΎΠ² ΠΎΡ ΠΈΠ·Π½ΠΎΡΠ° Π½Π°ΠΊΠ»Π°Π΄ΠΎΠΊ ΠΈ Π²ΠΎΠ·ΠΌΠΎΠΆΠ½ΠΎΡΡΡ ΡΠ°Π±ΠΎΡΡ Ρ ΠΌΠ°Π»ΡΠΌΠΈ Π·Π°Π·ΠΎΡΠ°ΠΌΠΈ, Π±ΠΎΠ»Π΅Π΅ ΡΠ°Π²Π½ΠΎΠΌΠ΅ΡΠ½ΠΎΠ΅ ΡΠ°ΡΠΏΡΠ΅Π΄Π΅Π»Π΅Π½ΠΈΠ΅ Π΄Π°Π²Π»Π΅Π½ΠΈΠΉ ΠΈ Π²ΡΡΠΎΠΊΡΡ ΡΡΠ°Π±ΠΈΠ»ΡΠ½ΠΎΡΡΡ ΡΠ°Π±ΠΎΡΡ.
ΠΠΈΡΠΊΠΎΠ²ΡΠ΅ ΡΠΎΡΠΌΠΎΠ·Π½ΡΠ΅ ΠΌΠ΅Ρ
Π°Π½ΠΈΠ·ΠΌΡ ΠΏΡΠΎΡΠ΅ ΠΎΠ±ΡΠ»ΡΠΆΠΈΠ²Π°ΡΡ. Π’Π°ΠΊ, Π½Π°ΠΏΡΠΈΠΌΠ΅Ρ, Π·Π°ΠΌΠ΅Π½Π° ΡΠΎΡΠΌΠΎΠ·Π½ΡΡ
ΠΊΠΎΠ»ΠΎΠ΄ΠΎΠΊ Π΄ΠΈΡΠΊΠΎΠ²ΡΡ
ΡΠΎΡΠΌΠΎΠ·ΠΎΠ² Π·Π°Π½ΠΈΠΌΠ°Π΅Ρ Π·Π½Π°ΡΠΈΡΠ΅Π»ΡΠ½ΠΎ ΠΌΠ΅Π½ΡΡΠ΅ Π²ΡΠ΅ΠΌΠ΅Π½ΠΈ, ΡΠ΅ΠΌ Π² Π±Π°ΡΠ°Π±Π°Π½Π½ΡΡ
ΡΠΎΡΠΌΠΎΠ·Π½ΡΡ
ΠΌΠ΅Ρ
Π°Π½ΠΈΠ·ΠΌΠ°Ρ
.
Π£ Π΄ΠΈΡΠΊΠΎΠ²ΡΡ ΡΠΎΡΠΌΠΎΠ·ΠΎΠ² Π·Π°Π²ΠΈΡΠΈΠΌΠΎΡΡΡ ΠΊΠΎΡΡΡΠΈΡΠΈΠ΅Π½ΡΠ° ΡΡΡΠ΅ΠΊΡΠΈΠ²Π½ΠΎΡΡΠΈ ΠΎΡ ΠΊΠΎΡΡΡΠΈΡΠΈΠ΅Π½ΡΠ° ΡΡΠ΅Π½ΠΈΡ ΠΈΠΌΠ΅Π΅Ρ Π±ΠΎΠ»Π΅Π΅ Π±Π»Π°Π³ΠΎΠΏΡΠΈΡΡΠ½ΡΠΉ (Π»ΠΈΠ½Π΅ΠΉΠ½ΡΠΉ) Ρ Π°ΡΠ°ΠΊΡΠ΅Ρ, ΡΠ΅ΠΌ Ρ Π±Π°ΡΠ°Π±Π°Π½Π½ΡΡ .
ΠΠ»Π°Π³ΠΎΠ΄Π°ΡΡ ΠΏΠ΅ΡΠ΅ΡΠΈΡΠ»Π΅Π½Π½ΡΠΌ Π΄ΠΎΡΡΠΎΠΈΠ½ΡΡΠ²Π°ΠΌ Π΄ΠΈΡΠΊΠΎΠ²ΡΠ΅ ΡΠΎΡΠΌΠΎΠ·Π½ΡΠ΅ ΠΌΠ΅Ρ Π°Π½ΠΈΠ·ΠΌΡ Π² ΠΏΠΎΡΠ»Π΅Π΄Π½ΠΈΠ΅ Π³ΠΎΠ΄Ρ ΠΏΡΠ°ΠΊΡΠΈΡΠ΅ΡΠΊΠΈ Π²ΡΡΠ΅ΡΠ½ΠΈΠ»ΠΈ Π±Π°ΡΠ°Π±Π°Π½Π½ΡΠ΅ ΠΌΠ΅Ρ Π°Π½ΠΈΠ·ΠΌΡ Π² ΠΊΠΎΠ½ΡΡΡΡΠΊΡΠΈΡΡ ΡΠΎΡΠΌΠΎΠ·Π½ΡΡ ΡΠΈΡΡΠ΅ΠΌ Π»Π΅Π³ΠΊΠΎΠ²ΡΡ Π°Π²ΡΠΎΠΌΠΎΠ±ΠΈΠ»Π΅ΠΉ, ΠΈ Π²ΡΠ΅ ΡΠ°ΡΠ΅ ΠΏΡΠΈΠΌΠ΅Π½ΡΡΡΡΡ Π½Π° Π³ΡΡΠ·ΠΎΠ²ΡΡ Π°Π²ΡΠΎΠΌΠΎΠ±ΠΈΠ»ΡΡ .
Π’Π΅ΠΌ Π½Π΅ ΠΌΠ΅Π½Π΅Π΅, ΠΈ ΡΠΎΡ ΠΈ Π΄ΡΡΠ³ΠΎΠΉ ΡΠΈΠΏ ΡΠΎΡΠΌΠΎΠ·Π½ΡΡ
ΠΌΠ΅Ρ
Π°Π½ΠΈΠ·ΠΌΠΎΠ² ΠΌΠΎΠΆΠ΅Ρ ΠΈΡΠΏΠΎΠ»ΡΠ·ΠΎΠ²Π°ΡΡΡΡ Π² ΠΊΠΎΠ½ΡΡΡΡΠΊΡΠΈΠΈ Π²ΡΠ΅Ρ
ΡΠΈΠΏΠΎΠ² Π°Π²ΡΠΎΠΌΠΎΠ±ΠΈΠ»Π΅ΠΉ, ΠΏΡΠΈ ΡΡΠΎΠΌ Π±Π°ΡΠ°Π±Π°Π½Π½ΡΠ΅ ΡΠΎΡΠΌΠΎΠ·Π½ΡΠ΅ ΠΌΠ΅Ρ
Π°Π½ΠΈΠ·ΠΌΡ ΡΠ°ΡΠ΅ ΠΏΡΠΈΠΌΠ΅Π½ΡΡΡΡΡ Π² ΡΠΎΡΠΌΠΎΠ·Π½ΡΡ
ΡΠΈΡΡΠ΅ΠΌΠ°Ρ
Π³ΡΡΠ·ΠΎΠ²ΡΡ
Π°Π²ΡΠΎΠΌΠΎΠ±ΠΈΠ»Π΅ΠΉ, Π΄ΠΈΡΠΊΠΎΠ²ΡΠ΅ β Π² ΡΠΎΡΠΌΠΎΠ·Π½ΡΡ
ΡΠΈΡΡΠ΅ΠΌΠ°Ρ
Π»Π΅Π³ΠΊΠΎΠ²ΡΡ
Π°Π²ΡΠΎΠΌΠΎΠ±ΠΈΠ»Π΅ΠΉ.
ΠΡΡΡΠ΅ΡΠ°ΡΡΡΡ ΠΈ ΠΊΠΎΠΌΠ±ΠΈΠ½Π°ΡΠΈΠΈ ΡΠ°ΠΊΠΈΡ
ΠΌΠ΅Ρ
Π°Π½ΠΈΠ·ΠΌΠΎΠ² Π½Π° ΠΎΠ΄Π½ΠΎΠΌ Π°Π²ΡΠΎΠΌΠΎΠ±ΠΈΠ»Π΅, Π½Π°ΠΏΡΠΈΠΌΠ΅Ρ, ΡΠΎΡΠΌΠΎΠ·Π½ΡΠ΅ ΠΌΠ΅Ρ
Π°Π½ΠΈΠ·ΠΌΡ Π·Π°Π΄Π½ΠΈΡ
ΠΊΠΎΠ»Π΅Ρ Π»Π΅Π³ΠΊΠΎΠ²ΠΎΠ³ΠΎ Π°Π²ΡΠΎΠΌΠΎΠ±ΠΈΠ»Ρ ΠΌΠΎΠ³ΡΡ Π±ΡΡΡ Π±Π°ΡΠ°Π±Π°Π½Π½ΡΠΌΠΈ, ΠΏΠ΅ΡΠ΅Π΄Π½ΠΈΡ
ΠΊΠΎΠ»Π΅Ρ β Π΄ΠΈΡΠΊΠΎΠ²ΡΠΌΠΈ.
ΠΠ°ΡΠ°Π±Π°Π½Π½ΡΠ΅ ΡΠΎΡΠΌΠΎΠ·Π½ΡΠ΅ ΠΌΠ΅Ρ Π°Π½ΠΈΠ·ΠΌΡ, ΡΠ°Π·ΠΌΠ΅ΡΠ΅Π½Π½ΡΠ΅ Π½Π° ΡΠ»Π΅ΠΌΠ΅Π½ΡΠ°Ρ ΡΡΠ°Π½ΡΠΌΠΈΡΡΠΈΠΈ, Π½Π΅ΡΠ΅Π΄ΠΊΠΎ ΠΈΡΠΏΠΎΠ»ΡΠ·ΡΡΡΡΡ Π² ΡΡΠΎΡΠ½ΠΎΡΠ½ΡΡ ΡΠΎΡΠΌΠΎΠ·Π½ΡΡ ΡΠΈΡΡΠ΅ΠΌΠ°Ρ Π³ΡΡΠ·ΠΎΠ²ΡΡ Π°Π²ΡΠΎΠΌΠΎΠ±ΠΈΠ»Π΅ΠΉ ΠΌΠ°Π»ΠΎΠΉ ΠΈ ΡΡΠ΅Π΄Π½Π΅ΠΉ Π³ΡΡΠ·ΠΎΠΏΠΎΠ΄ΡΠ΅ΠΌΠ½ΠΎΡΡΠΈ.
***
ΠΠ»Π΅ΠΌΠ΅Π½ΡΡ ΡΠΎΡΠΌΠΎΠ·Π½ΡΡ ΠΌΠ΅Ρ Π°Π½ΠΈΠ·ΠΌΠΎΠ²
Π’ΠΎΡΠΌΠΎΠ·Π½ΡΠ΅ Π±Π°ΡΠ°Π±Π°Π½Ρ ΠΌΠΎΠ³ΡΡ Π±ΡΡΡ Π»ΠΈΡΡΠ΅, ΡΡΠ°ΠΌΠΏΠΎΠ²Π°Π½Π½ΡΠ΅ ΠΈ ΠΊΠΎΠΌΠ±ΠΈΠ½ΠΈΡΠΎΠ²Π°Π½Π½ΡΠ΅. ΠΡ ΠΎΡΠ»ΠΈΠ²Π°ΡΡ ΠΈΠ· ΡΡΠ³ΡΠ½Π° Ρ ΠΏΡΠΈΠΌΠ΅ΡΡΡ ΠΌΠ΅Π΄ΠΈ, ΠΌΠΎΠ»ΠΈΠ±Π΄Π΅Π½Π°, Π½ΠΈΠΊΠ΅Π»Ρ ΠΈ ΡΠΈΡΠ°Π½Π°, Π° ΡΠ°ΠΊΠΆΠ΅ ΠΈΠ· Π°Π»ΡΠΌΠΈΠ½ΠΈΠ΅Π²ΡΡ ΡΠΏΠ»Π°Π²ΠΎΠ². Π¨ΡΠ°ΠΌΠΏΠΎΠ²Π°Π½Π½ΡΠ΅ Π±Π°ΡΠ°Π±Π°Π½Ρ ΠΎΠ±ΡΡΠ½ΠΎ Π²ΡΠΏΠΎΠ»Π½ΡΡΡΡΡ ΠΈΠ· Π»ΠΈΡΡΠΎΠ²ΠΎΠΉ ΡΡΠ°Π»ΠΈ, ΠΏΡΠΈ ΡΡΠΎΠΌ ΠΈΠΌΠ΅ΡΡ Π²Π½ΡΡΡΠ΅Π½Π½ΠΈΠΉ ΡΠ»ΠΎΠΉ ΠΈΠ· Π»Π΅Π³ΠΈΡΠΎΠ²Π°Π½Π½ΠΎΠ³ΠΎ ΡΡΠ³ΡΠ½Π°.
Π’ΠΎΡΠΌΠΎΠ·Π½ΡΠ΅ Π΄ΠΈΡΠΊΠΈ ΠΈΠ·Π³ΠΎΡΠΎΠ²Π»ΡΡΡ, ΠΊΠ°ΠΊ ΠΏΡΠ°Π²ΠΈΠ»ΠΎ, ΠΈΠ· ΡΡΠ³ΡΠ½Π°. ΠΡΠΈΠΌΠ΅Π½ΡΡΡ ΡΠ°ΠΊΠΆΠ΅ Π±ΠΈΠΌΠ΅ΡΠ°Π»Π»ΠΈΡΠ΅ΡΠΊΠΈΠ΅ Π΄ΠΈΡΠΊΠΈ, ΠΊΠΎΡΠΎΡΡΠ΅ Π²ΡΠΏΠΎΠ»Π½ΡΡΡ Ρ ΡΡΠΈΠΊΡΠΈΠΎΠ½Π½ΡΠΌ ΡΠ»ΠΎΠ΅ΠΌ ΠΈΠ· ΡΠ΅ΡΠΎΠ³ΠΎ ΡΡΠ³ΡΠ½Π°, ΡΠ°Π·ΠΌΠ΅ΡΠ°Π΅ΠΌΠΎΠ³ΠΎ Π½Π° Π°Π»ΡΠΌΠΈΠ½ΠΈΠ΅Π²ΠΎΠΌ ΠΈΠ»ΠΈ ΠΌΠ΅Π΄Π½ΠΎΠΌ ΠΎΡΠ½ΠΎΠ²Π°Π½ΠΈΠΈ.
ΠΠΎΠ»ΠΎΠ΄ΠΊΠΈ ΡΠΎΡΠΌΠΎΠ·Π½ΡΡ ΠΌΠ΅Ρ Π°Π½ΠΈΠ·ΠΌΠΎΠ² Π²ΡΠΏΠΎΠ»Π½ΡΡΡ ΡΠ°ΡΠ΅ Π²ΡΠ΅Π³ΠΎ Π»ΠΈΡΡΠΌΠΈ ΠΈΠ· ΡΡΠ³ΡΠ½Π° ΠΈΠ»ΠΈ Π»Π΅Π³ΠΊΠΈΡ ΡΠΏΠ»Π°Π²ΠΎΠ², Π° ΡΠ°ΠΊΠΆΠ΅ ΡΡΠ°ΠΌΠΏΠΎΠ²Π°Π½Π½ΡΠΌΠΈ ΠΈΠ»ΠΈ ΡΠ²Π°ΡΠ½ΡΠΌΠΈ. Π Π½ΠΈΠΌ Ρ ΠΏΠΎΠΌΠΎΡΡΡ Π·Π°ΠΊΠ»Π΅ΠΏΠΎΠΊ ΠΈΠ»ΠΈ ΠΊΠ»Π΅Ρ ΠΊΡΠ΅ΠΏΡΡ ΡΠΎΡΠΌΠΎΠ·Π½ΡΠ΅ Π½Π°ΠΊΠ»Π°Π΄ΠΊΠΈ. ΠΠΎΠ»ΠΎΠ΄ΠΊΠΈ ΡΡΡΠΆΠ½ΡΠΌΠΈ ΠΏΡΡΠΆΠΈΠ½Π°ΠΌΠΈ ΠΏΠΎΡΡΠΎΡΠ½Π½ΠΎ ΠΏΡΠΈΠΆΠ°ΡΡ ΠΊ ΡΠ°Π·ΠΆΠΈΠΌΠ½ΠΎΠΌΡ ΡΡΡΡΠΎΠΉΡΡΠ²Ρ.
Π’ΠΎΡΠΌΠΎΠ·Π½ΡΠ΅ Π½Π°ΠΊΠ»Π°Π΄ΠΊΠΈ ΠΌΠΎΠ³ΡΡ Π±ΡΡΡ ΠΏΡΠ΅ΡΡΠΎΠ²Π°Π½Π½ΡΠ΅ ΠΈΠ»ΠΈ ΡΠΎΡΠΌΠΎΠ²Π°Π½Π½ΡΠ΅ ΠΈΠ»ΠΈ ΠΏΠ»Π΅ΡΠ΅Π½Π½ΡΠ΅. ΠΠ»Ρ Π½Π°ΠΊΠ»Π°Π΄ΠΎΠΊ ΠΈΡΠΏΠΎΠ»ΡΠ·ΡΡΡ ΡΠΎΡΠΌΠΎΠ²Π°Π½Π½ΡΠ΅ ΠΈ ΠΏΡΠ΅ΡΡΠΎΠ²Π°Π½Π½ΡΠ΅ ΠΌΠ°ΡΠ΅ΡΠΈΠ°Π»Ρ Π½Π° Π°ΡΠ±ΠΎΠΊΠ°ΡΡΡΠΊΠΎΠ²ΠΎΠΉ ΠΎΡΠ½ΠΎΠ²Π΅ (ΠΊΠΎΡΠΎΡΠΊΠΎΠ²ΠΎΠ»ΠΎΠΊΠ½ΠΈΡΡΡΠΉ Π°ΡΠ±Π΅ΡΡ, Π½Π°ΠΏΠΎΠ»Π½ΠΈΡΠ΅Π»ΠΈ ΠΈ ΡΠ²ΡΠ·ΡΡΡΠΈΠ΅ ΠΌΠ°ΡΠ΅ΡΠΈΠ°Π»Ρ — ΡΠ°ΡΠ΅ Π±Π°ΠΊΠ΅Π»ΠΈΡΠΎ-ΡΠΎΡΠΌΠ°Π»ΡΠ΄Π΅Π³ΠΈΠ΄Π½ΡΠ΅ ΡΠΌΠΎΠ»Ρ), Π° ΡΠ°ΠΊΠΆΠ΅ ΠΌΠ΅ΡΠ°Π»Π»ΠΎΠΊΠ΅ΡΠ°ΠΌΠΈΠΊΡ.
***
Π£ΡΡΡΠΎΠΉΡΡΠ²ΠΎ ΡΠΎΡΠΌΠΎΠ·Π½ΡΡ ΠΌΠ΅Ρ Π°Π½ΠΈΠ·ΠΌΠΎΠ² ΡΠ°Π·Π»ΠΈΡΠ½ΡΡ ΠΌΠ°ΡΠΎΠΊ ΠΎΡΠ΅ΡΠ΅ΡΡΠ²Π΅Π½Π½ΡΡ Π°Π²ΡΠΎΠΌΠΎΠ±ΠΈΠ»Π΅ΠΉ ΠΌΠΎΠΆΠ½ΠΎ ΠΈΠ·ΡΡΠΈΡΡ, ΠΏΡΠΎΠΉΠ΄Ρ ΠΏΠΎ ΠΏΡΠΈΠ²Π΅Π΄Π΅Π½Π½ΡΠΌ Π½ΠΈΠΆΠ΅ ΡΡΡΠ»ΠΊΠ°ΠΌ (ΡΡ Π΅ΠΌΡ ΠΎΡΠΊΡΠΎΡΡΡΡ Π² ΠΎΡΠ΄Π΅Π»ΡΠ½ΠΎΠΌ ΠΎΠΊΠ½Π΅ Π±ΡΠ°ΡΠ·Π΅ΡΠ°):
Β Β Β Β Π’ΠΎΡΠΌΠΎΠ·Π½ΡΠ΅ ΠΌΠ΅Ρ
Π°Π½ΠΈΠ·ΠΌΡ Π°Π²ΡΠΎΠΌΠΎΠ±ΠΈΠ»Π΅ΠΉ Β«ΠΠΠΒ» ΠΈ Β«ΠΠΠΒ»
Β Β Β Β Β Β Β Β Π’ΠΎΡΠΌΠΎΠ·Π½ΡΠ΅ ΠΌΠ΅Ρ
Π°Π½ΠΈΠ·ΠΌΡ Π°Π²ΡΠΎΠΌΠΎΠ±ΠΈΠ»Π΅ΠΉ Β«ΠΠ°ΠΌΠΠΒ» ΠΈ Β«ΠΠΠΒ»
Β Β Β Β Β Β Β Β Β Β Β Β ΠΠΈΡΠΊΠΎΠ²ΡΠ΅ ΡΠΎΡΠΌΠΎΠ·Π½ΡΠ΅ ΠΌΠ΅Ρ
Π°Π½ΠΈΠ·ΠΌΡ Π°Π²ΡΠΎΠΌΠΎΠ±ΠΈΠ»Π΅ΠΉ Β«ΠΠΎΠ»Π³Π°Β», Β«ΠΠΎΡΠΊΠ²ΠΈΡΒ»
Β Β Β Β Β Β Β Β Β Β Β Β Β Β Β Β ΠΠΈΡΠΊΠΎΠ²ΡΠΉ ΡΠΎΡΠΌΠΎΠ·Π½ΠΎΠΉ ΠΌΠ΅Ρ
Π°Π½ΠΈΠ·ΠΌ Π°Π²ΡΠΎΠΌΠΎΠ±ΠΈΠ»Π΅ΠΉ Β«ΠΠΠΒ»
***
ΠΠ°Π·Π½Π°ΡΠ΅Π½ΠΈΠ΅ ΠΈ ΠΎΠ±ΡΠ΅Π΅ ΡΡΡΡΠΎΠΉΡΡΠ²ΠΎ ΡΡΠ»Π΅Π²ΠΎΠ³ΠΎ ΡΠΏΡΠ°Π²Π»Π΅Π½ΠΈΡ
ο»Ώk-a-t.ru