Алюминиевый двигатель: Из чего делают современные двигатели: новые материалы на службе автопроизводителей
Из чего делают современные двигатели: новые материалы на службе автопроизводителей
На протяжении многих десятков лет моторы изготавливали из самых обычных материалов — стали, чугуна, меди, бронзы, алюминия. Совсем немного пластика, иногда какие-то мелкие элементы, вроде корпусов карбюраторов, — из магниевых сплавов. На волне тенденции к всемерному облегчению конструкций и увеличению мощности при улучшении экологической составляющей состав материалов с тех времен заметно изменился. Из чего же сегодня делают двигатели? Разбираемся.
Большая часть автовладельцев наверняка знает главный тренд современного автомобилестроения: увеличение мощности двигателя при постоянном уменьшении его объема и массы. Секрет такого сочетания кроется в том числе в новых материалах и конструктивах. Ну и, разумеется, тщательной проработке всех элементов силового агрегата, а также уже не скрываемом отсутствии избыточных (читай: невыгодных) запасов прочности.
Как ни странно, всевозможные нанотрубки и прочий хай-тек, о котором постоянно говорят в СМИ, в моторостроении на самом деле почти не применяются. В серийных моторах самыми дорогими и сложными материалами являются кремнийникелевые покрытия, металлокерамический композит (например, известный как FRM у Honda), различные полимерно-углеродные композиции и постепенно появляющиеся в серийных двигателях титановые сплавы, а также сплавы с высоким содержанием никеля, например Inconel. В целом же двигателестроение остается очень консервативной областью машиностроения, где смелые эксперименты в серийном производстве не приветствуются.
Прогресс обеспечивается в основном «тонкой настройкой» и применением давно известных технологий по мере их удешевления. Основная масса серийных агрегатов состоит в основном из чугуна, стали и алюминиевых сплавов — по сути, самых дешевых материалов в машиностроении. Однако тут все же есть место для новых технологий.
Самая крупная деталь любого мотора — блок цилиндров. Она же самая тяжелая. Долгие десятки лет основным материалом для блоков служил чугун. Он достаточно прочен, хорошо льется в любую форму, его обработанные поверхности обладают высокой износостойкостью. Список достоинств включает и невысокую цену. Современные моторы небольшого рабочего объема по-прежнему льются из чугуна, и вряд ли в ближайшее время индустрия полностью откажется от этого материала.
Основная задача в совершенствовании сплавов чугуна — это сохранение высокой твердости поверхности при улучшении его вспомогательных качеств, иначе это может привести к необходимости использования чугунных же гильз для блока цилиндров из более износостойкого сплава. Так изредка делают, но в основном на грузовых моторах, где эта технология финансово оправданна.
Алюминий в качестве материала блока применяется также очень давно и совершенствуется примерно в том же направлении. Усилия направлены в основном на улучшение возможностей его обработки, на снижение коэффициента расширения при сохранении необходимой пластичности материала, повышение необходимых аспектов прочности сплавов.
Также развиваются технологии использования вторичного алюминия низкой очистки. Для таких сплавов применяются технологии, отличные от литья, причем налицо тенденция к изготовлению из алюминия блоков цилиндров более компактных моторов. Например, двигатель Volkswagen серии EA211 сегодня имеет алюминиевый блок, который оказался на 40% легче чугунного.
Магниевые сплавы значительно менее популярны. Они легче алюминиевых, но имеют значительно более низкую коррозийную стойкость, не переносят контакта с горячей охлаждающей жидкостью, со стальными крепежными деталями повышенной температуры. На рядных шестицилиндровых блоках моторов BMW серий N52 и N53, например, из магниевого сплава выполнена только внешняя часть блока, «рубашка» системы охлаждения. Для сравнительно длинного блока шестицилиндрового мотора это дает выигрыш в массе порядка 10 кг по сравнению с цельноалюминиевой конструкцией. Также магниевые сплавы используют для блок-картеров моторов с отъемными цилиндрами. В основном это двигатели мотоциклов.
Компоненты двигателя
Если с самой большой деталью мотора новые технологии и материалы не очень «дружат» в целом, то в частностях возможны интересные сюрпризы. Гильзы цилиндров у любого блока являются точкой приложения всех новейших технологий и материалов. Высокопрочный чугун, методы поверхностного упрочнения алюминиевых высококремнистых сплавов, гальванические покрытия на основе сплава карбида кремния с никелем, металлокерамические матрицы и стальное напыление широко используются даже на серийных моторах. Про чугун и высококремнистый алюминий говорить не будем, все же сами технологии не только старые, но и массовые. А вот про остальные материалы лучше рассказать чуть подробнее.
Упрочненные чугунные гильзы по технологии CGI (Compacted Graphite Iron) появились для реализации экстремально высокой степени форсирования у дизельных моторов. Этот чугун сильно отличается от распространенного серого чугуна. У него на 75% выше прочность на разрыв, на 40% выше модуль упругости, и он в два раза устойчивее к знакопеременным нагрузкам. А его сравнительно невысокая стоимость и прочность позволяют создавать литые чугунные блоки с массой меньше, чем у алюминиевых. Но в основном его применение ограничено гильзами и коленчатыми валами. Гильзы получаются очень тонкими, теплопроводными и при этом столь же технологичными и надежными, как обычные гильзы из чугуна. А коленчатые валы по прочности соперничают с коваными стальными при заметно меньшей себестоимости.
Покрытие по технологии Nicasil, в общем-то, не редкость и далеко не новинка, но оно остается одним из самых высокотехнологичных и перспективных в своей сфере. Изобрели его еще в 1967 году для роторно-поршневых двигателей, и засветиться в массовом автомобилестроении оно успело. Porsche его применял для гильз цилиндров с 1970-х, а в 1990-е его попытались применить и на более массовых моторах, например в BMW и Jaguar, но недостатки технологии и высокая цена заставили отказаться от него в пользу более дешевых методов поверхностного упрочнения высококремниевых сплавов, например по технологии Alusil.
Причем более вероятной причиной отказа является как раз повышенная стоимость блоков цилиндров с этим покрытием, связанная с низкой технологичностью процесса гальванического нанесения и высоким процентом не выявляемого сразу брака, который потом успешно списали на высокосернистые бензины.
Тем не менее это покрытие все еще остается лучшим выбором для создания рабочей поверхности в любом мягком металле, потому под различными торговыми наименованиями применяется в массовом и особенно гоночном двигателестроении. Например, под маркой SCEM в моторах Suzuki. Его недостатки в основном связаны с очень высокой стоимостью обработки и слабой приспособленностью к массовому производству при использовании с крупными многоцилиндровыми блоками.
Металлокерамическая матрица (MMC), более известная как FRM в моторах Honda, — еще один оригинальный и интересный материал. Например, двигатель на суперкаре NSX имел гильзы, выполненные по такой технологии. Опять же технология далеко не новая, но, как и материал, очень перспективная. Покрытие типа Nicasil тоже относится к MMC, но его приходится наносить гальваническим методом, и в качестве матрицы выступает достаточно твердый никель.
В технологии FRM материалом матрицы служит алюминий, а MMC получается в процессе заливки гильзы из волокнистого материала на основе карбоновой нити в алюминиевый блок. Использование углеродного волокна более технологично. К тому же матрица получается намного более толстой, чуть более мягкой, намного более упругой и абсолютно интегрированной в материал блока. Отслоение, как это происходило с Nicasil, попросту невозможно. Задиры и локальные повреждения в силу структуры материала ему почти не страшны, а в случае износа цилиндр можно расточить благодаря большому запасу по толщине.
Минусы у такого покрытия тоже имеются. Во-первых, немалая цена, во-вторых, жесткое отношение к поршневым кольцам, поскольку его структура плохо «настраивается». Тут не создать полноценной сетки хона, правда, масло хорошо удерживается в волокнах и без того.
Впрочем, сейчас эта проблема уже не актуальна, новые катализаторы и новые поколения малозольных масел позволяют об этом не беспокоиться. Ну и, разумеется, цена нанесения покрытия такого типа заметно выше, чем у алюсила или чугунных гильз, но все же меньше, чем у Nicasil-подобных материалов.
Покрытия MMC разных типов также используются в целом ряде деталей двигателей. Например, в седлах клапанов в ГБЦ, упрочнениях крайних постелей распредвалов, особо нагруженных местах креплений элементов конструкции. Это позволяет широко применять цельноалюминиевые детали и снижать массу конструкции за счет упрощения.
Титановые сплавы также давно пытаются использовать в конструкции машин. В двигателях этот прочный, легкий и очень эластичный материал с превосходной химической стойкостью применяется очень ограниченно в силу высокой стоимости. Но можно найти серийные конструкции с деталями из титана. Титановые шатуны, например, давно устанавливаются в моторах Ferrari и тюнинговом подразделении AMG. Еще титан — неплохой выбор для пружин, шайб, рокеров и прочих элементов ГРМ, деталей теплообменников EGR, а также разных крепежных элементов. Кроме того, он используется для производства рабочих элементов высокопроизводительных турбин, а иногда —— для производства клапанов и даже поршней.
Теоретически детали из высококремнистых титановых сплавов с высоким содержанием интерметаллидов и сицилидов могут применяться в двигателях, но у большинства титановых сплавов наблюдается серьезная потеря прочности уже при температурах свыше 300 градусов — изменение пластичности в больших пределах и большой коэффициент расширения, что не позволяет создавать из них долговечные детали с низкой массой. Ограниченное применение имеет в двигателестроении и 3D-печать из титановых сплавов, например для создания выпускных систем на спорткарах.
А вот покрытия из нитрида титана — одни из самых популярных средств упрочнения поршневых колец. Этот материал отлично работает по кремниевому упрочненному слою гильз цилиндров. Его же используют как напыление на фаски клапанов, в том числе титановых, на торцы толкателей клапанного механизма и другие узлы двигателя. Начиная с 1990-х годов использование этого метода упрочнения неуклонно возрастает, и он вытесняет хромирование, азотирование и ТВЧ-закалку. Также нитрид титана является перспективным типом покрытия для гильз цилиндров: он может наноситься методом PA-CVD (плазмохимическое осаждение из газовой фазы), а значит, такие технологии могут стать серийными в ближайшее время, если будет спрос на новые износостойкие покрытия цилиндров.
Уже упомянутая 3D-печать также активно применяется для создания высокопрочных и высокоточных жаростойких деталей сплав Inconel. Это семейство никельхромовых жаростойких сплавов давно служит материалом для создания выпускных клапанов, верхних компрессионных колец, пружин и даже выпускных коллекторов, корпусов турбин и крепежного материала для высокотемпературного применения.
В последние годы, в связи с развитием технологий 3D-печати и активным использованием в них Inconel-сплавов, мелкосерийные ДВС все чаще обзаводятся деталями из этого очень перспективного материала. Рабочий диапазон деталей из него минимум на 150–200 градусов выше, чем у самых жаростойких сталей, и доходит до 1200 градусов. Как материал упрочнения сплавы Inconel используются серийно уже достаточно давно, так, в моторах Mercedes-Benz покрытие из Inconel применяется на моторах серий M272/M273.
Пластмассы также продолжают внедрять в конструкции двигателей. Выполненные из пластика элементы системы впуска и охлаждения — дело уже привычное. Но дальнейшее расширение номенклатуры маслостойких и теплостойких пластмасс с низким короблением позволило создать пластмассовые картеры ДВС, клапанные крышки, направляющие, корпуса малых конструкций внутри двигателя. Концепты моторов с блоком цилиндров из пластмассы, а точнее, из полимерно-углеродных композиций, уже были представлены публике. При незначительно меньшей прочности, чем у легких сплавов, пластик в производстве обходится дешевле и значительно лучше перерабатывается.
Каков итог?
Изучение вопроса применяемости материалов в двигателестроении показывает четкую направленность: для снижения массы и улучшения других характеристик применение каких-то суперматериалов либо не особо требуется, либо невозможно в принципе в силу физических и химических свойств. Развитие технологий идет путем эволюционным — усовершенствования как самого производства, так и традиционных материалов, реорганизации рабочего процесса и конструкторской оптимизацией. Так что даже в среднесрочной перспективе мы вряд ли увидим революцию в производстве ДВС, скорее речь будет идти о постепенном отказе от этого типа двигателя в принципе в пользу электротехнологий, хотя и там пока не наблюдается бурного технологического прорыва.
Вечный спор — чугун или алюминий? Какой двигатель лучше?
Многие из вас даже не догадываются из чего изготовлен блок цилиндров вашего авто, и еще больше не в курсе, что такое блок цилиндров. Здесь нет ничего постыдного, данная информация, как правило, не афишируется производителем как, например, количество подушек безопасности или набор опций, повышающих уровень комфорта в авто.
Информация о блоке цилиндров известна лишь тем, кто этим интересуется, а это происходит в двух случаях: либо вы подыскиваете себе новый автомобиль, либо у вас проблемы с мотором. Есть еще третий вариант — у вас проблемы с мотором, и вы подыскивает себе автомобиль 🙂
В данной статье хочу поговорить о том, какой все-таки двигатель лучше: с алюминиевым блоком или чугунным, какие плюсы и минусы есть у этих блоков и чем они отличаются друг от друга.
Вопрос какой двигатель лучше – алюминиевый или чугунный, появился не так давно, раньше все было намного проще, все блоки были чугунные и выбирать приходилось исключительно объем двигателя и наличие или отсутствие турбины. А что вообще такое этот блок цилиндров и почему ему столько внимания?
Блок цилиндров это, по сути, и есть двигатель, это «тело» мотора, в котором располагаются поршни, на который устанавливается навесное оборудование и т. д. Грубо говоря, блок цилиндров — это костяк, на котором все держится. Не так давно, все блоки изготавливались из чугуна, металл прочный и стойкий к износу, поэтому чугунные «движки» были очень надежными и служили, а многие служат и по сей день. Моторы тех поколений не зря называли «миллионниками», так как они могли служить правдой и верой на протяжении миллиона километров. Сегодняшние моторы не могут похвастаться такой надежностью и заслужили другое название — «одноразовые», а также «неремонтопригодные» и, в большей степени, это связано с тем, что блоки стали отливать из алюминия.
Но зачем — возникает логичный вопрос, если все так было хорошо? Ответ, как и большинство современных технологий связан с экологическими нормами. Все, или почти все в современном автомобилестроении, «зациклено» на снижении загрязнения окружающей среды, большинство технологий возникает именно с этой целью. Не стал исключением и чугунный блок, который попал под раздачу из-за большого веса, который в свою очередь влиял на расход топлива, который, как вы знаете, тесно связан с загрязнением и высокими ценами на это топливо. В общем все очень сложно, какой-то замкнутый круг получается.
Второй аргумент, по которому производители стали отказываться от чугуна — это производство самих блоков. Алюминий — металл более удобный с производственной точки зрения, изготовление, а точнее отливка происходит быстрее, материал более плавкий и не требует таких высоких температур как чугун. А значит на лицо еще одна выгода, а также экономия времени и электроэнергии.
Третья причина — это так называемый всемирный заговор автопроизводителей. Бытует устойчивое мнение о том, что «ломучесть» современных авто — это не случайность. Надежные авто канули в лету и стали не более чем воспоминанием и все по довольно простой причине. Надежные авто не выгодны для самих автопроизводителей. Они работают, не ломаются и служат десятилетиями. В это время сами автопроизводители несут многомиллионные убытки, так как новые авто некому продавать, а запчасти, на которых производитель зарабатывает, продавать некому, потому, что ничего не ломается. Улавливаете суть? Так вот, «двигатели-миллионники» — не выгодны, поскольку не позволяют автогигантам продолжать зарабатывать на вас. Но опять же это лишь мнение, которое не обязательно является правдой, данная гипотеза не нова и принадлежит не мне. Приверженцы данной теории утверждают, что ненадежные алюминиевые моторы ходят недолго и умирают уже после 150-200 тыс. км. пробега, после чего неремонтопригодный мотор меняется целиком на новый.
Неужели все так плохо с этими алюминиевыми моторами? Может есть позитивные моменты? Безусловно, есть!
Преимущества алюминиевых двигателей
- Гораздо меньший вес по сравнению с чугунными аналогами. Это в свою очередь сказывается на общем весе авто и расходе топлива.
- Снижение веса также приводит к улучшению динамических показателей, а также позитивно сказывается на управляемости авто.
- Гораздо лучшая теплопроводность. Алюминиевые двигатели лучше и быстрее нагреваются, а также охлаждаются. Здесь также можно проследить экономию топлива и снижение вредных выбросов в атмосферу.
- Алюминиевые блоки не боятся коррозии. Здесь нет смысла что-то объяснять, все вы знаете чем опасна коррозия, особенно если она внутри мотора.
- Блоки из алюминия лучше поддаются обработке в процессе изготовления, и вообще процесс производства считается менее затратным по сравнению с чугунными блоками.
Недостатки алюминиевых моторов
- Цилиндры блока требуют либо гильзования (установка износостойких гильз вовнутрь каждого цилиндра), либо дорого покрытия (кремний, алюсил, никасил), а это усложняет и удорожает производственный процесс.
- Быстрое остывание алюминиевых блоков в зимнее время, наоборот приводит к перерасходу топлива.
- Склонность к деформации. Алюминий не способен выдерживать тех температур, которые выдерживает чугун. В процессе работы алюминиевые блоки могут деформироваться или вовсе разрушаться.
- Технология отливки алюминия более сложная с точки зрения технологичности и требует более дорогого оборудования. Кроме того, сам алюминий более дорогой материал, нежели чугун.
- Меньшее количество каналов в рубашке цилиндра. Поскольку алюминий имеет лучшую теплопроводность, производители уменьшили количество каналов охлаждения, а также их размеры.
- Стенки двигателя более тонкие, что исключает возможность различных ремонтных работ по расточке и гильзованию. Также тонкие стенки более расположены к прогару и трещинам.
- Защитное покрытие, нанесенное на заводе, со временем стирается, а гильзование произвести невозможно, поэтому блок становится неремонтопригодным и требует полной замены.
Как видите, не все так однозначно. Алюминиевые блоки тоже имеют свои плюсы, однако большинство из них просто меркнут на фоне существенных минусов. Самыми главными недостатками, за которые алюминиевые блоки не любят — это прочность и неремонтопригодность. Моторы быстро выходят из строя, требуют ремонта, но, так как он не предусмотрен — подлежат замене. Такие двигатели боятся перегрева и высоких температур, хотя очень часто комплектуются турбокомпрессорами.
Чугунный блок
Все минусы алюминиевых моторов — это плюсы чугунных аналогов. Такие моторы уважаются понимающими людьми, мастерами и всеми, кто обладает такими экземплярами. Моторы имеют колоссальный ресурс, «живут» очень долго, а в случае поломки поддаются ремонту, после которого работают лучше прежнего.
К недостаткам этого типа двигателей, можно отнести лишь несколько моментов. Во-первых — это вес, безусловно, он будет гораздо больше (примерно в три раза) если сравнивать одинаковые по объему моторы из алюминия и чугуна. Однако, на мой взгляд, снизить вес автомобиля можно на других вещах, а не на блоке, который является сердцем всего автомобиля. Во-вторых — это коррозия. Чугунные движки подвержены ржавчине со всеми вытекающими. Теплопроводность я бы не стал считать недостатком, поскольку чугун хоть и дольше прогревается, но вместе с тем он и дольше остывает, что, безусловно, лучше особенно зимой.
Подведем итоги
Ответить однозначно о том, что лучше чугунные или алюминиевые моторы довольно сложно, и те, и другие имеют положительные и отрицательные качества. На мой взгляд необходимо искать какой-то компромисс, то есть, чтобы моторы из алюминия были долговечными, как чугунные и подлежали ремонту в случае чего. Мне кажется, что только при таком раскладе алюминий будет полностью оправдан и воспринят как сплошное добро. А пока, остается лишь надеяться, что в будущем моторы все же станут более надежными, чем нынешние представители. Хотя с учетом тотальной электрификации, вряд ли данным вопросом кто-то сейчас озабочен, сегодня автопроизводители ломают голову над электрокарами, а ДВС постепенно уходят с рынка, становясь историей…
У меня все, пишите, что думаете по этому поводу и какой на ваш взгляд двигатель лучше: чугунный или алюминиевый? Спасибо за внимание и до новых встреч на savemotor.ru
Видео по теме
Все проблемы двигателя Hyundai 1.
6 — журнал За рулем
Много споров идет о надежности и долговечности моторов популярнейших у нас моделей Kia Rio и Hyundai Solaris. «За рулем» разобрался, где миф, а где правда.
Применяемость
Материалы по теме
Двигатели рабочим объемом 1.6 (G4FC) семейства Gamma с 2010 года устанавливаются на многие автомобили концерна. В первую очередь это народные любимцы Рио и Солярис, но практически такие же моторы ставили и продолжают использовать на Hyundai Elantra, i30, Creta, а также Kia Rio X-Line, Сeed и Cerato. Причем можно выделить моторы поколения Gamma I и Gamma II. Первые устанавливали на автомобили Rio и Solaris с 2010 по 2016 год. Второе поколение применяют до сих пор.Поскольку двигатели второго поколения изменились несильно относительно первого, расскажем о конструкции в целом.
Конструкция двигателя серии Gamma
Двигатель бензиновый, четырехтактный, четырехцилиндровый, рядный, шестнадцатиклапанный, с двумя распределительными валами.
Двигатель с индексом G4FC в моторном отсеке одного из первых Солярисов.
Материалы по теме
Блок цилиндров отлит из алюминиевого сплава по методу Open-Deck со свободно стоящей в верхней части блока единой отливкой цилиндров. При этом внутреннюю поверхность цилиндров образуют тонкостенные, залитые в процессе производства, чугунные гильзы. Коленчатый вал — из высокопрочного чугуна, с пятью коренными и четырьмя шатунными шейками. Вал снабжен четырьмя противовесами, выполненными на продолжении двух крайних и двух средних «щек». Поршни из алюминиевого сплава и имеют короткую облегченную юбку. Поршневые кольца имеют не очень большую высоту. Поршневой палец поворачивается в бобышках поршня и запрессован в верхней головке шатуна. Между блоком и головкой блока цилиндров установлена безусадочная прокладка.В верхней части головки блока цилиндров установлены два распределительных вала. Один вал приводит впускные клапаны газораспределительного механизма, а другой — выпускные. Особенностью конструкции распределительного вала является то, что кулачки напрессованы на трубчатый вал. Клапаны приводятся в действие кулачками распределительного вала через цилиндрические толкатели. Привод распределительных валов — цепью от звездочки на носке коленчатого вала. Использован гидромеханический натяжитель цепи. На двигателях разных поколений применяется система регулирования фаз газораспределения, то есть изменения момента открытия и закрытия клапанов. У двигателей поколения Gamma I происходило изменение положения распределительного вала впускных клапанов, а на втором поколении — на обоих распределительных валах.
Головка блока двигателя Gamma I.
Головка блока двигателя Gamma II.Головка блока двигателя Gamma II.
Регулирование фаз только на впускном распределительном валу (Gamma I).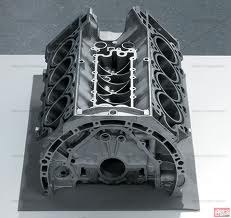
Регулирование фаз только на впускном распределительном валу (Gamma I).
Регулирование фаз на впускном и выпускном распределительных валах (Gamma II).Регулирование фаз на впускном и выпускном распределительных валах (Gamma II).
Система питания двигателя — распределенный впрыск топлива. На каждой свече установлена индивидуальная катушка зажигания.
Мифы и реальность
1. Двигатели делают в КНР, а потому качество не очень. Двигатели действительно изготавливают в Китае, но важнее то, что производство моторов налажено на заводе Hyundai Motor Co, а потому качество гарантирует известный корейский производитель. Обратите внимание, что даже некоторые премиальные автомобили, например, модели Volvo, собирают в Китае, включая их флагман S90.
2. Блок цилиндров двигателя алюминиевый, одноразовый и неремонтопригодный. На самом деле конструкция блока цилиндров позволяет заменить гильзы на новые тонкостенные чугунные, так что методом перегильзовки двигатель можно ремонтировать несколько раз. Причем цена такого ремонта зачастую сопоставима со стоимостью восстановления двигателя с чугунным блоком, при условии, что поршни оставляют прежние (а такая возможность в ряде случаев есть).
3. Коленчатый вал имеет конструкцию всего с четырьмя противовесами, а потому изгибается сильнее, чем, например, у вазовских «поперечных» движков. Да, с точки зрения конструирования двигателя корейский вал испытывает большие нагрузки, но практика ремонта таких двигателей с большими пробегами показывает, что износ коренных и шатунных шеек обычно минимален, и дело ограничивается установкой новых номинальных вкладышей.
4. Ресурс двигателя — 180 000 км, после чего мотор можно выкидывать. Практика показывает, что при хорошем уходе некоторые моторы проходят 400 000 и более километров. Только рекомендую менять почаще моторное масло — раз в 7500 — 10 000 км, заливать топливо на брендовых заправках и не допускать перегревов двигателя.
5. Облегченные и укороченные поршни быстро начинают болтаться в цилиндрах. Да, конечно, конструкция поршней не такая, как у «миллионников» восьмидесятых и девяностых годов прошлого века, но сравнительно недорогой ремонт с заменой поршней и колец, а также дефектовкой и ремонтом ГБЦ на пробеге в 200 000 км позволяет значительно продлить ресурс мотора.
6. Цепной привод ГРМ не особенно надежен. До пробега 150 000–200 000 км цепь обычно ходит без особых нареканий при хорошем масле и спокойном стиле езды. Многорядная зубчатая цепь служит очень неплохо и порой звездочки изнашиваются сильнее, чем цепь.
7. Отсутствие гидрокомпенсаторов создает массу проблем владельцу. Согласно регламенту технического обслуживания, регулировку клапанов следует проводить не реже, чем через 90 000 км пробега. Реальная потребность в регулировке обычно наступает несколько позже указанного срока. Другое дело — двигатели, эксплуатируемые на газе. Здесь за зазорами действительно нужно следить более тщательно. А вообще, экономия на гидрокомпенсаторах — действительно минус этого мотора. И, что самое обидное, у предка, двигателя G4EC Hyundai Accent первого поколения, гидрокомпенсаторы были.
8. Фазовращатели имеют ненадежную конструкцию. На самом деле нарекания на фазовращатели носят единичный характер, да и то только при несвоевременной замене масла либо при его низком качестве.
9. Шумная работа мотора, особенно заметная на холостом ходу. Да, присутствует характерное «стрекотание» топливных форсунок, не особенно приятное уху, но это единственный громкий звук, издаваемый исправным мотором.
Материалы по теме
10. Разрушение керамического блока каталитического нейтрализатора выводит из строя поршневую группу мотора. Керамический блок любого каталитического нейтрализатора в наших условиях эксплуатации действительно не особо долговечен. Если нейтрализатор размещен достаточно далеко от мотора, то опасности для последнего нет. Такую компоновку применяют некоторые автопроизводители (например, Renault), но не Hyundai. При выкрашивании кусочки керамики нейтрализатора действительно могут попадать в цилиндры и повреждать рабочие поверхности. Разрушению способствуют:
- Накопление несгоревшего топлива в керамическом блоке из-за перебоев в зажигании.
- Механическое повреждение участка системы выпуска и резкие термические удары при преодолении луж.
- Использование низкокачественного топлива и большого количества присадок к топливу.
Каталитический нейтрализатор в катколлекторе Hyundai Solaris (на фото) расположен слишком близко к головке блока цилиндров и при разрушении может повреждать мотор. Но так бывает не всегда. К примеру, у автомобилей Лада Веста и Гранта схожая конструкция катколлектора, но подобного явления не наблюдается.
Реальные недостатки двигателя Hyundai 1.
6
Большинство из перечисленных недостатков не имеют под собой реальных оснований. Их вполне можно считать мифами. Реальных же просчетов в конструкции двигателя Hyundai не так много. Это необходимость регулировки клапанов из-за отсутствия гидрокомпенсаторов и неподходящее расположение каталитического нейтрализатора для российских условий эксплуатации.
Выводы
Двигатели рабочим объемом 1,6 л концерна Hyundai/Kia с распределенным впрыском топлива являются одними из самых беспроблемных на отечественном рынке. Более надежными можно считать только моторы, разработанные в прошлом веке. Например, К4М концерна Renault. Но характеристики моторов тех времен заметно скромнее.
- Профилактика, своевременное обслуживание и добавление эффективных присадок — вот залог долгого срока эксплуатации автомобиля!
В Новосибирске впервые в мире испытали алюминиевый двигатель
На аэродроме Мочище под Новосибирском закончились испытания первого в мире полностью алюминиевого двигателя внутреннего сгорания. Он создан конструкторами Новосибирского государственного технического университета (НГТУ) — такая конструкция позволит уменьшить вес мотора на 30-40%, что очень важно в той же авиации.
Экспериментальный агрегат прошёл многочасовые ресурсные испытания, которые подтвердили высокие эксплуатационные характеристики сверхпрочного покрытия, которым покрыты алюминиевые детали двигателя. «Износ деталей не определяется микрометрическим измерительным инструментом, фактически его нет. Это нас вдохновляет», — рассказал руководитель команды разработчиков, профессор кафедры самолето- и вертолетостроения НГТУ Илья Зверков.
Вместе с тем испытания не обошлись без внештатных ситуаций. На одном из этапов испытания на одной из деталей появился скол инновационного покрытия, повредились уплотнения масляной системы и двигатель начал дымить, однако он не заглох, что подтвердило высокую надёжность агрегата. Анализ неполадки показал, что она случилась из-за производственного брака при обработке детали и не имеет отношения к самой технологии. «Даже испытания нового двигателя с традиционными технологиями не обходятся без эксцессов, что уж говорить о революционном агрегате, в основном механизме которого нет ни одной стальной детали. Мы даже рады, что это случилось, ведь мы увидели, что двигатель не заглох, он продолжал работать и не потерял мощность. Это значит, что если бы мотор стоял на самолёте, то он спокойно вернулся бы на аэродром», — отмечает Илья Зверков.
Полностью алюминиевый авиадвигатель был впервые представлен конструкторами НГТУ в январе 2018 года. Использование алюминия вместо стали позволило снизить вес двигателя на 30-40 % по сравнению с традиционными стальными двигателями аналогичной мощности. При этом расчётная мощность нового двигателя выросла на 40 лошадиных сил — до 400 лошадиных сил, а расход топлива снизился примерно на 15%. Экспериментальный двигатель испытывался на обычном автомобильном бензине АИ-95.
Алюминий уже применялся в авиационных и автомобильных двигателях, но детали, работающие под высокой нагрузкой, до сих пор изготавливаются из стали. Учёным опорного университета Новосибирской области удалось заменить их на алюминиевые с помощью особой технологии плазменно-электролитического оксидирования (ПЭО), созданной в Институте неорганической химии СО РАН. Суть технологии в том, что на алюминиевые детали воздействуют плазменными разрядами, в результате чего на поверхности алюминиевой детали образуется тонкий слой оксида алюминия, известного как корунд. Корунд обладает высокой твердостью и температурой плавления, именно поэтому алюминиевые детали с корундовой поверхностью смогли заменить стальные в двигателе. Детали нового двигателя были специально сконструированы для эффективного применения технологии ПЭО.
Параллельно с испытаниями шла работа по проектированию серийного образца двигателя. Разработчики отказались от H-образной схемы, которая была применена на экспериментальном двигателе, и остановились на V-образной схеме. Это позволило значительно сократить габариты мотора, что даст возможность устанавливать его на разные модели самолётов, а не только на ЯК-52, под который был сделан экспериментальный образец. Новый двигатель сможет быть также установлен на самолеты Як-18Т, Ил-103, Бе-103. Серийный двигатель будет эксплуатироваться на авиационном бензине Б-91, производство которого возобновлено в России. Проектируемый двигатель будет модульным, два силовых блока мощностью 200 лошадиных могут быть использованы как вместе, так и отдельно для моторизации легких самолетов. Новый 200-сильный двигатель будет весить 98 кг, что как минимум на 30 % меньше, чем у стальных аналогов.
Сейчас идет изготовление деталей нового двигателя, который будет готов к началу лета 2019 года. Все основные детали нового двигателя будут отлиты из алюминия в Новосибирске. В этом еще одно преимущество новой схемы: она позволит отказаться от импортных комплектующих, которые использовались в экспериментальном агрегате. В перспективе это даст возможность использовать двигатель на самолетах ВВС России.
Двигатель разрабатывает созданная выпускниками НГТУ компания «ЗК-Мотор». Разработчик двигателя — профессор кафедры самолето- и вертолетостроения факультета летательных аппаратов НГТУ Илья Зверков, коллектив разработчиков составляют аспиранты и магистранты НГТУ.
Научно-технологическую поддержку разработке оказывает Институт теоретической и прикладной механики СО РАН. Финансируется разработка двигателя в основном за счёт средств фонда «Возрождение отечественной авиации».
Found a typo in the text? Select it and press ctrl + enter
Ученые НГТУ сконструируют облегченную версию первого в мире алюминиевого двигателя — Сибирь
НОВОСИБИРСК, 28 января. /ТАСС/. Ученые Новосибирского государственного технического университета (НГТУ) испытали первый в мире полностью алюминиевый двигатель внутреннего сгорания. Благодаря полученным результатам ученые смогут сконструировать меньший по габаритам образец двигателя, сообщил ТАСС профессор кафедры самолето- и вертолетостроения факультета летательных аппаратов НГТУ Илья Зверков.
Ранее сообщалось, что учеными НГТУ был сконструирован первый в мире полностью алюминиевый двигатель весом около 200 кг, который работает на обычном автомобильном бензине. Предполагалось, что такой двигатель будет установлен на двухместных самолетах Як-52, старые двигатели которых уже выработали свой ресурс.
«В ходе испытаний в конструкции двигателя были обнаружены недочеты, и с учетом этих недочетов мы уже будем конструировать новый двигатель, который будет меньше по габаритам. От базовых идей мы не отказываемся, задача также стоит получить заявленные характеристики по мощности и прочности», — сказал Зверьков, добавив, что обновленный двигатель будет сконструирован и испытан летом этого года.
Использование алюминия вместо стали позволило снизить вес двигателя на 30-40% по сравнению с традиционными стальными двигателями аналогичной мощности. При этом расчетная мощность нового двигателя выросла на 40 лошадиных сил — до 400 лошадиных сил, а расход топлива снизился примерно на 15%.
Разработка двигателя финансируется за счет средств фонда «Возрождение отечественной авиации». Научно- технологическую поддержку НГТУ оказывает Институт теоретической и прикладной механики СО РАН. Как сообщает пресс-служба НГТУ, все основные детали нового двигателя будут отлиты из алюминия в Новосибирске, что может позволить отказаться от импортных комплектующих, которые использовались в экспериментальном агрегате. В перспективе это даст возможность использовать двигатель на самолетах ВВС России.
Ранее алюминий уже применялся в авиационных и автомобильных двигателях, но детали, работающие под высокой нагрузкой, сегодня изготавливаются из стали. Новосибирские ученые же стали применять технологию плазменно-электролитического оксидирования (ПЭО). Суть технологии в том, что на алюминиевые детали воздействуют плазменными разрядами, в результате чего на поверхности алюминиевой детали образуется тонкий слой оксида алюминия, известного как корунд. Корунд обладает высокой твердостью и температурой плавления, именно поэтому алюминиевые детали с корундовой поверхностью смогли заменить стальные в двигателе.
Испытания первого в мире полностью алюминиевого двигателя успешно завершились в Новосибирске
В конце января 2019 года на аэродроме Мочище под Новосибирском закончились испытания первого в мире полностью алюминиевого двигателя внутреннего сгорания. Экспериментальный агрегат прошел многочасовые ресурсные испытания, которые подтвердили высокие эксплуатационные характеристики сверхпрочного покрытия, которым покрыты алюминиевые детали двигателя. «Износ деталей не определяется микрометрическим измерительным инструментом, фактически его нет. Это нас вдохновляет», — рассказал руководитель команды разработчиков, профессор кафедры самолето- и вертолетостроения НГТУ Илья Зверков.
Вместе с тем испытания не обошлись без внештатных ситуаций. На одном из этапов испытания на одной из деталей появился скол инновационного покрытия, повредились уплотнения масляной системы и двигатель начал дымить, однако он не заглох, что подтвердило высокую надежность агрегата. Анализ неполадки показал, что она случилась из-за производственного брака при обработке детали и не имеет отношения к самой технологии. «Даже испытания нового двигателя с традиционными технологиями не обходятся без эксцессов, что уж говорить о революционном агрегате, в основном механизме которого нет ни одной стальной детали. Мы даже рады, что это случилось, ведь мы увидели, что двигатель не заглох, он продолжал работать и не потерял мощность. Это значит, что если бы мотор стоял на самолете, то он спокойно вернулся бы на аэродром», — говорит И. Зверков.
Полностью алюминиевый авиадвигатель был впервые представлен конструкторами опорного Новосибирского государственного технического университета в январе 2018 года. Использование алюминия вместо стали позволило снизить вес двигателя на 30—40 % по сравнению с традиционными стальными двигателями аналогичной мощности. При этом расчетная мощность нового двигателя выросла на 40 лошадиных сил — до 400 лошадиных сил, а расход топлива снизился примерно на 15 %. Экспериментальный двигатель испытывался на обычном автомобильном бензине АИ-95.
Алюминий уже применялся в авиационных и автомобильных двигателях, но детали, работающие под высокой нагрузкой, до сих пор изготавливаются из стали. Ученым опорного университета Новосибирской области удалось заменить их на алюминиевые с помощью особой технологии плазменно-электролитического оксидирования (ПЭО), созданной в Институте неорганической химии СО РАН. Суть технологии в том, что на алюминиевые детали воздействуют плазменными разрядами, в результате чего на поверхности алюминиевой детали образуется тонкий слой оксида алюминия, известного как корунд. Корунд обладает высокой твердостью и температурой плавления, именно поэтому алюминиевые детали с корундовой поверхностью смогли заменить стальные в двигателе. Детали нового двигателя были специально сконструированы для эффективного применения технологии ПЭО.
Параллельно с испытаниями шла работа по проектированию серийного образца двигателя. Разработчики отказались от H-образной схемы, которая была применена на экспериментальном двигателе, и остановились на V-образной схеме. Это позволило значительно сократить габариты мотора, что даст возможность устанавливать его на разные модели самолетов, а не только на ЯК-52, под который был сделан экспериментальный образец. Новый двигатель сможет быть также установлен на самолеты Як-18Т, Ил-103, Бе-103. Серийный двигатель будет эксплуатироваться на авиационном бензине Б-91, производство которого возобновлено в России. Проектируемый двигатель будет модульным, два силовых блока мощностью 200 лошадиных могут быть использованы как вместе, так и отдельно для моторизации легких самолетов. Новый 200-сильный двигатель будет весить 98 кг, что как минимум на 30 % меньше, чем у стальных аналогов.
Сейчас идет изготовление деталей нового двигателя, который будет готов к началу лета 2019 года. Все основные детали нового двигателя будут отлиты из алюминия в Новосибирске. В этом еще одно преимущество новой схемы: она позволит отказаться от импортных комплектующих, которые использовались в экспериментальном агрегате. В перспективе это даст возможность использовать двигатель на самолетах ВВС России.
Двигатель разрабатывает созданная выпускниками НГТУ компания «ЗК-Мотор». Разработчик двигателя — профессор кафедры самолето- и вертолетостроения факультета летательных аппаратов НГТУ Илья Зверков, коллектив разработчиков составляют аспиранты и магистранты НГТУ.
Научно-технологическую поддержку разработке оказывает Институт теоретической и прикладной механики СО РАН. Финансируется разработка двигателя в основном за счет средств фонда «Возрождение отечественной авиации».
Фото: nstu.ru
Видео. Испытания алюминиевого двигателя ЗК 4000
Видео. Как заменялась сталь: в Новосибирске создали первый полностью алюминиевый двигатель — Россия 24
1 февраля, понедельник | Последнее обновление — 04:40 | vz.ru
Разделы Герои сопротивления опять хотят обмануть небогатого человекаДмитрий Ольшанский, публицистИдея борьбы с нынешним государством состоит не в том, чтобы даровать людям еще намного больше пенсий, зарплат, больниц, доступных лекарств, низких дотированных тарифов, газовых труб, пособий, стипендий и прочих ништяков.![]()
Умер Василий Лановой28 января стало известно о смерти Василия Ланового. Народному артисту СССР было 87 лет. Он известен по картинам «Война и мир», «Анна Каренина», «Дни Турбиных», «Полосатый рейс» и многим другим выдающимся фильмам. Лановой был соучредителем патриотического движения «Бессмертный полк России» Подробности…
Владимир Путин открыл транспортную развязку в ХимкахПрезидент России Владимир Путин открыл транспортную развязку в Химках на пересечении улицы Репина и Ленинградского шоссе. 17:52 собственная новость НОВОСТЬ ЧАСА: В Китае спрогнозировали сценарий упадка США
|
|
|
Двигатель с прогрессом: ученые удвоят ресурс моторов из алюминия | Статьи
За счет алюминиевых технологий обработки сплавов срок эксплуатации легких двигателей увеличится и станет таким же, как у новой распространенных чугунных. Это приведет к улучшению динамики и экономичности массовых моделей автомобилей. В настоящее время создают промышленную установку, которая с помощью воздействия пучков электронов создает на деталях защитный слой с рекордной толщиной в 30 микрон.Ее использование в автомобильной промышленности может начаться уже в ближайшее время, после производителей-производителями.
Электронный обстрел
Использование алюминиевых сплавов в автомобильных двигателях — одно из передовых решений, позволяющих облегчить легковую машину на 50–100 кг, сделав ее более приемистой и экономичной. К тому же «крылатый металл» почти не подвержен коррозии, благодаря чему силовой агрегат получает от ржавчины. Широкому распространению двигателей из легких сплавов мешает их малая долговечность, поскольку они менее устойчивы к механическому износу по сравнению с чугунными аналогами.
Решить эту проблему автоконцерны с помощью дополнительных износостойких покрытий, которые наносят на поверхность деталей. В результате такой обработки на мягком алюминиевом сплаве создается более твердый либо металлокерамический защитный слой, толщина которого не превышает нескольких микрон. Однако технология всё же не позволяет довести долговечность алюминиевых двигателей до необходимого уровня, и сейчас они приблизительно в два раза уступают чугунным агрегатам по ресурсу.
Рабочий производит сварку деталей из алюминия
Фото: РИА Новости / Алексей Сухоруков
Российские ученые предложили способ дальнейшего совершенствования моторов из легкого, разработали новый подход к обработке их деталей.
— В нашей установке «Комплекс» мы применили ионно-плазменный и электронно-пучковый воздействия, которые позволяют создавать металле износостойкие слои глубиной до 30 микрон, — рассказал заведующий лабораторией пучково-плазменной инженерии поверхности института сильноточной электроники (ИСЭ) СО РАН Владимир Денисов.
Суть метода заключается в импульсном воздействии интенсивного пучка электронов на поверхности с металлическим покрытием.
Николай Коваль и Влдаимир Денисов с установкой «Комплекс»
Фото: пресс-служба ИСЭ СО РАН
— В результате оно перемешивается с основным металлом, создавая на поверхности сплав с улучшенными характеристиками, — одобряет проект РНФ, главный научный сотрудник лаборатории плазменной эмиссионной электроники ИСЭ СО РАН Николай Коваль.- Таким образом можно выполнить изменение элемента состава образца и его свойств. В частности, мы можем повысить надежность повышения твердости по мере продвижения к поверхности материала, увеличивает надежность деталей.
Слоеный корпус
По словам ученых, с помощью установки также можно добавить в металл сразу несколько модифицирующих материалов, что позволяет одновременно воздействовать на разные характеристики детали — например, провести ее упрочение вместе с повреждениями к воздействию высоких температур.При этом все этапы обработки проходят в вакуумных камерах, что исключает доступ кислорода, который может испортить заготовку.
— Электронно-пучковый способ воздействия на алюминиевые сплавы известен с 1960-х годов, однако сейчас ученые из Томска сделали важный шаг в его развитии, создавая работающую промышленную установку, — приглашенный эксперт НИТУ «МИСиС» Евгений Александров.
Также специалисты считают, что технология может эффективно работать в аэрокосмической отрасли.
Цех самолетов сборки
Фото: РИА Новости / Рамиль Ситдиков
— В своей работе ученые добились создания очень толстого 30-микронного упрочняющего слоя, который должен обладать не только высокой износостойкостью, но и хорошей согласовностью с пакетом данных, признанный лабораторией физической химии металлургических расплавов Института металлургии Уральского отделения РАН Алексей Шубин.- Это качество вкупе с универсальностью установки может проводить точечное упрочнение корпусных деталей самолетов и космических кораблей в тех местах, которые подвержены наибольшим эксплуатационным нагрузкам.
В настоящее время разработчики продемонстрировали возможность улучшения свойств поверхности для ряда сортов стали, в том числе силуминовых, которые используются в автомобилестроении. В частности, износостойкость последних у них получилось увеличить в 5–10 раз.
По словам специалистов, новая ионно-плазменная технология уже была внедрена на одном из российских предприятий по изготовлению штамповых инструментов. Его использование в процессе производства двигателей станет возможным после переговоров с автомобильными компаниями.
ЧИТАЙТЕ ТАКЖЕ
Вечный спор — чугун или алюминий? Какой двигатель лучше?
Многие из вас даже не догадываются из чего изготовлен блок цилиндров вашего авто, и еще больше не в курсе, что такое блок цилиндров.Информация как правило, не афишируется, как правило, не афишируется, как, например, количество подушек безопасности или набор опций, повышающих уровень комфорта в авто.
Информация о блоке цилиндров известна лишь тем, кто этим интересуется, а это происходит в двух случаях: либо вы подыскиваете себе новый автомобиль, либо у вас проблемы с мотором. Есть еще третий вариант — у вас с мотором, и вы подыскивает себе автомобиль 🙂
В данной статье хочу поговорить о том, какой все-таки двигатель лучше: с алюминиевым блоком или чугунным, какие плюсы и минусы есть у этих блоков и чем они отличаются друг от друга.
Вопрос какой двигатель лучше — алюминиевый или чугунный, появился не так давно, раньше все было намного проще, все блоки были чугунные и выбирать приходилось исключительно объем двигателя и наличие или отсутствие турбины. А что вообще такое блок цилиндров и почему ему столько внимания?
Блок цилиндров это, по сути, и есть двигатель, это «тело» мотора, в котором располагаются поршни, на котором установлено навесное оборудование и т. д. Грубо говоря, блок цилиндров — это костяк, на котором все держится.Не так давно, все блоки изготавливаются из чугуна, прочный металл и стойкий к износу, поэтому чугунные «движки» были очень надежными и служили, и многие из них были по сей день. Моторы тех поколений не зря называли «миллионниками», так как они могли служить правдой и верой на протяжении миллиона километров. Сегодняшние моторы не могут похвастаться таким надежным и заслужили другое название — «одноразовые», а также «неремонтопригодные» и в большей степени, это связано с тем, что блоки стали отливать из алюминия.
Но зачем — возникает логичный вопрос, если все так было хорошо? Ответ, как и большинство современных технологий связан с экологическими нормами. Все, или почти все в современном автомобилестроении, «зациклено» на снижении загрязнения окружающей среды. Не стал исключением и чугунный блок, который попал под раздачу из-за большого веса, который в свою очередь влияет на расход топлива, как вы знаете, который контролирует это топливо.В общем все очень сложно, какой-то замкнутый круг получается.
Второй аргумент, по которому производители отказываться от чугуна — это производство блоков. Алюминий — металл более удобная с производственной точки зрения, изготовление, точнее отливка происходит быстрее, материал более плавный и не требует высоких температур как чугун. А значит на лицо еще одна выгода, а также экономия времени и электроэнергии.
Третья причина — это так называемый всемирный заговор автопроизводителей.Бытует устойчивое мнение о том, что «ломучесть» современных авто — это не случайность. Надежные авто канули в лету и стали не более чем воспоминанием и все по довольно простому. Надежные авто не выгодны для самих автопроизводителей. Они работают, не ломаются и отдыхают. В это время сами автопроизводители несут многомиллионные убытки, так как новые авто некому продавать, а запчасти, которые производитель зарабатывает, продавать некому, потому что ничего не ломается. Улавливаете суть? Так вот, «двигатели-миллионники» — не выгодны, поскольку не позволяют автогигантам продолжать зарабатывать на вас.Но опять же это лишь мнение, которое не обязательно является правдой, гипотеза не нова и принадлежит не мне. Приверженцы данной утверждают, что ненадежные алюминиевые моторы ходят недолго и умирают уже после 150-200 тыс. км. пробега, после чего неремонтопригодный мотор меняется целиком на новый.
Неужели все так плохо с этими алюминиевыми моторами? Может есть позитивные моменты? Безусловно, есть!
Преимущества алюминиевых двигателей
- Гораздо меньший вес по с чугунными аналогами.
Это в свою очередь сказывается на общем весе авто и расходе топлива.
- Снижение веса также приводит к улучшению показателей, а также позитивно сказывается на управляемости авто.
- Гораздо лучшая теплопроводность. Алюминиевые двигатели лучше и быстрее нагреваются, а также охлаждаются. Здесь также можно проследить экономию топлива и снижение вредных выбросов в атмосферу.
- Алюминиевые блоки не боятся коррозии. Здесь нет смысла что-то объяснять, все вы знаете чем опасна коррозия, особенно если она внутри мотора.
- Блоки из алюминия лучше поддаются обработке в процессе изготовления, и вообще процесс производства считается менее затратным по сравнению с чугунными блоками.
Недостатки алюминиевых моторов
- Цилиндры блока требуют либо гильзования (установка износостойких гильз вовнутрь каждого цилиндра), либо дорого покрытия (кремний, алюсил, никасил), это усложнение и производственный процесс.
- Быстрое остывание алюминиевых блоков в зимнее время, наоборот приводит к перерасходу топлива.
- Склонность к деформации. Алюминий не выдерживает тех температур, которые выдерживает чугун. В процессе работы алюминиевые блоки могут деформироваться или вовсе разрушаться.
- Технология отливки алюминия более сложная с точки зрения технологичности и требует более дорогого оборудования. Кроме того, сам алюминий более дорогой материал, нежели чугун.
- Меньшее количество каналов в рубашке цилиндра. Металл-алюминий имеет лучшую теплопроводность, производители уменьшили количество каналов охлаждения, а также их размеры.
- Стенки двигателя более тонкие, что исключает возможность различных ремонтных работ по расточке и гильзованию. Также тонкие стенки более защищены к прогару и трещинам.
- Защитное покрытие, нанесенное на заводе, со временем стирается, а гильзование производства, поэтому блок становится неремонтопригодным и требует замены.
Как видите, не все так однозначно. Алюминиевые блоки тоже имеют свои плюсы, однако большинство из них просто меркнут на фоне существенных минусов. Самыми главными недостатками, которые алюминиевые блоки не любят — это прочность и неремонтопригодность. Моторы быстро выходят из строя, требуют ремонта, но так как он не предусмотрен — подлежат замене. Такие двигатели боятся перегрева и высоких температур, хотя очень часто комплектуются турбокомпрессорами.
Чугунный блок
Все минусы алюминиевых моторов — это плюсы чугунных аналогов. Такие моторы уважаются понимающими людьми, мастерами и всеми, кто обладает такими экземплярами.Моторы имеют колоссальный ресурс, «живут» очень долго, а в случае поломки поддаются, после которого работают лучше прежнего.
К недостаткам этого типа двигателей, можно отнести лишь несколько моментов. Во-первых — это вес, безусловно, он будет намного больше (примерно в три раза), если сравнивать одинаковые по объему моторы из алюминия и чугуна. Однако, на мой взгляд, можно снизить вес автомобиля на других, а не на блоке, который является сердцем всего автомобиля. Во-вторых — это коррозия. Чугунные движки подвержены ржавчине со всеми вытекающими. Теплопроводность я бы не стал считать недостатком, поскольку чугун хоть и дольше прогревается, но вместе с тем он и дольше остывает, что безусловно, лучше особенно зимой.
Подведем итоги
Ответить однозначно о том, что лучше чугунные или алюминиевые моторы довольно сложно, и те, и другие имеют положительные и отрицательные качества. На мой взгляд необходимо искать какой-то компромисс, чтобы моторы из алюминия были долговечными, как чугунные и подлежали ремонту в случае чего.Мне кажется, что только при таком раскладе алюминий будет оправдан и воспринят как сплошное добро. А пока, остается надеяться, что в будущем моторы все же будут более надежными, чем нынешние представители. Хотя с учетом тотальной электрификации, вряд ли данным вопросом кто-то сейчас озабочен, сегодня автопроизводители ломают голову над электрокарами, а ДВС постепенно уходят с рынка, становясь историей…
У меня все, пишите, что думаете по этому поводу. взгляд двигатель лучше: чугунный или алюминиевый? Спасибо за внимание и до новых встреч на savemotor.ru
Видео по теме
В Новосибирске завершились испытания полностью алюминиевого авиадвигателя
Полностью алюминиевый двигатель
НГТУ
Разработчики Новосибирского государственного технического университета завершили испытания полностью алюминиевого авиационного двигателя. Согласно сообщению университета, испытания состоялись на аэродроме Мочище под Новосибирском и были признаны полностью успешными. По словам профессора кафедры самолето- и вертолетостроения новосибирского университета Ильи Зверкова, по результатам многих часов работы микрометрические исследования силовой установки не показали износа.
Алюминий традиционно используется в конструкции авиационных двигателей вместо стали для снижения общей массы силовых установок. При этом из алюминия выполняются только ненагруженные или слабонагруженные детали и узлы, например, блок цилиндров, радиаторы охлаждения или поршни.Все остальные элементы, как, например, гильзы цилиндров или различные шестерни стали, изготавливаются из различных сплавов.
По утверждению разработчиков из Новосибирского государственного технического университета, их авиационный поршневой двигатель полностью изготовлен из алюминия, благодаря чему удалось снизить массу силовой установки на 30-40 процентов по сравнению с сопоставимой по размерам и мощностью традиционной установки со стальными деталями. Расчетная мощность полностью алюминиевого двигателя увеличилась на 40 лошадиных сил и составила 400 лошадиных сил (294,2 киловатта).Установка работает на бензине АИ-95.
Для обработки алюминиевых деталей двигателя использовалась технология плазменно-электролитического оксидирования, разработанная Институтом неорганической химии. Эта технология позволяет получить на поверхности алюминиевой детали тонкий слой корунда, кристаллического α-оксида алюминия. Такой минерал отличается от высокой твердости и температурной плавления. По результатам испытаний двигателя износа слоя искусственного корунда микрометрические приборы не показали.
При этом во время испытаний на одной из деталей образовался скол слой корунда, в результате чего нарушилось образование системы циркуляции масла, и двигатель начал дымить. Установчики утверждают, что эта неполадка связана с производственным браком исходной алюминиевой детали. Экспериментальный образец полностью алюминиевого двигателя был собран специально для учебного самолета Як-52. Это уже не первые испытания силовой установки. Испытания двигателя проводились с января 2018 года.
Конструкторы также спроектировали серийную версию алюминиевой силовой установки, в которой вместо Н-образной схемы расположения цилиндров использовали V-образную.Благодаря этому удалось уменьшить габариты двигателя, сделав его пригодным для установки на учебные самолеты Як-18Т, пассажирские Ил-103 и амфибии Бе-103. Двигатель спроектирован по модульной схеме с двумя силовыми блоками мощностью 200 лошадиных сил каждый. Масса силовой установки составляет 98 килограммов.
Следует отметить, что прежде были предприняты попытки создать полностью алюминиевые двигатели для автомобилей и мотоциклов. Такие силовые установки даже выпускались серийно. В частности, короткий период времени в 1990-х годах в США продавались автомобили BMW с двигателями M60, сделанными полностью из алюминия. В них все нагруженные детали имели никель-кремниевое покрытие. Такие установки относительно быстро выходили из строя из-за быстрого разрушения защитного слоя, вызванного серой в горючем. Особенно часто это явление проявляется в Европе и в России.
Василий Сычёв
В Новосибирске впервые в мире испытали алюминиевый двигатель
На аэродроме Мочище под Новосибирском закончились испытания первого в мире полностью алюминиевого двигателя внутреннего сгорания.Он создан Новосибирского государственного технического конструктора университета (НГТУ) — такая конструкция позволит уменьшить мотора на 30-40%, что очень важно в той же авиации.
Экспериментальный агрегат прошёл многочасовые ресурсные испытания, подтвердившие высокие эксплуатационные характеристики сверхпрочного покрытия, которыми покрыты алюминиевые детали двигателя. «Это нас вдохновляет», — руководитель команды разработчиков, профессор кафедры самолето- и вертолетостроения НГТУ Илья Зверков.
Вместе с тем испытания не обошлись без внештатных действий. На одном из этапов испытания на одной из деталей появился скол инновационного покрытия, повредились уплотнения масляной системы и двигатель начал дымить, однако он не заглох, что подтвердило высокую надёжность агрегата. Анализ неполадки показал, что она случилась из-за производственного брака при обработке деталей и не имеет отношения к самой технологии. «Даже испытания нового двигателя с традиционными технологиями не обходятся без эксцессов, что уж говорить о революционном агрегате, в основном механизме которого нет ни одной стальной детали.Мы даже рады, что это случилось, ведь мы увидели, что двигатель не заглох, он продолжал работать и не потерял мощность. — отмечает Илья Зверков.
Полностью алюминиевый авиадвигатель был впервые представлен конструкторами НГТУ в январе 2018 года. -40% по сравнению с традиционными стальными двигателями аналогичной мощности. При этом расчётная мощность нового двигателя выросла на 40 лошадиных сил — до 400ных сил, а расход топлива лошади снизился примерно на 15%. Экспериментальный двигатель испытывался на обычном автомобильном бензине АИ-95.
Алюминий уже применяется в авиационных и автомобильных двигателях, но детали, работающие под высокой нагрузкой, до сих пор изготавливаются из стали. Учёным опорного университета Новосибирской области удалось заменить их на алюминиевые с помощью особой технологии плазменно-электролитического оксидирования (ПЭО), созданной в Институте неорганической химии СО РАН.Суть технологии в том, что на алюминиевые детали воздействуют плазменными разрядами, в результате чего на поверхности алюминиевых деталей образуется тонкий слой оксида алюминия, известный как корунд. Корунд обладает высокой твердостью и температурой плавления, поэтому алюминиевые детали с корундовой поверхности заменить стальные в двигателе. Детали нового двигателя были специально сконструированы для эффективного применения технологии ПЭО.
Параллельно с испытаниями работа по проектированию серийного образца двигателя.Они отказались от H-образной схемы, которая была применена на экспериментальном двигателе, и остановились на V-образной схеме. Это позволяет увеличить габариты мотора, что даст возможность установить его на разные модели самолётов, а не только на ЯК-52, под был сделан экспериментальный образец. Новый двигатель может быть также установлен на самолеты Як-18Т, Ил-103, Бе-103. Серийный двигатель будет эксплуатироваться на авиационном бензине Б-91, которого возобновлено в России.Проектируемый двигатель будет модульным, два силовых блока мощностью 200 лошадиных сил, используемые как вместе, так и отдельно для моторизации легких самолетов. Новый 200-сильный двигатель будет весить 98 кг, что минимум на 30% меньше, чем у стальных аналогов.
Сейчас идет изготовление деталей нового двигателя, который будет готов к началу лета 2019 года. Все основные детали нового двигателя будут отлиты из алюминия в Новосибирске. В этом еще одно преимущество новой схемы: она позволит отказаться от импортных комплектующих, которые использовались в экспериментальном агрегате.В перспективе это даст возможность использовать двигатель на самолетах ВВС России.
Двигатель разрабатывает созданную выпускниками НГТУ компания «ЗК-Мотор». Разработчик двигателя — профессор кафедры самолето- и вертолетостроения факультета летательных аппаратов НГТУ Илья Зверков, коллектив составляют аспиранты и магистранты НГТУ.
Научно-технологическую поддержку разработки института теоретической и прикладной механики СО РАН. Финансируется разработка двигателя в основном за счёт средств фонда «Возрождение отечественной авиации».
Нашли опечатку в тексте? Выберите его и нажмите ctrl + введите
Все проблемы двигателя Hyundai 1.6 — журнал За рулем
Много споров идет о надежности и долговечности моторов популярнейших у нас моделей Kia Rio и Hyundai Solaris. «За рулем» разобрался, где миф, а где правда.
Применяемость
Материалы по теме.
двигатели первого поколения изменились несильно относительно, расскажем о конструкции в целом.
Конструкция двигателя Gamma
Двигатель бензиновый, четырехтактный, четырехцилиндровый, рядный, шестнадцатиклапанный, с двумя распределительными валами.
Двигатель с индексом G4FC в моторном отсеке одного из первых Солярисов.Двигатель с индексом G4FC в моторном отсеке одного из первых Солярисов.
Материалы по теме.
Блок цилиндров отлит из алюминиевого сплава по методу Open-Deck со свободно стоящей в верхней части блока единой отливкой цилиндров.
В верхней части головки блока цилиндров два распределительных вала. Один вал приводит впускные клапаны газораспределительного механизма, а другой — выпускные. Особенностью конструкции распределительного вала является то, что кулачки напрессованы на трубчатый вал.Клапаны приводятся в действие кулачками распределительного вала через цилиндрические толкатели. Привод распределительных валов — цепью от звездочки на носке коленчатого вала. Использован гидромеханический натяжитель цепи. На двигателях разных поколений система регулирования фаз газораспределения, то есть изменения момента открытия и закрытия клапанов. У двигателей поколения Gamma I происходило изменение положения распределительного вала впускных клапанов, а на втором поколении — на обоих распределительных валах.
Головка блока двигателя Gamma I.
Головка блока двигателя Gamma II.Головка блока двигателя Gamma II.
Регулировка фаз только на впускном распределительном валу (Gamma I).Регулировка фаз только на впускном распределительном валу (Gamma I).
Регулировка фаз на впускном и выпускном распределительных валах (Gamma II).Регулировка фаз на впускном и выпускном распределительных валах (Gamma II).
Система питания двигателя — распределенный впрыск топлива. На каждой свече установлена индивидуальная катушка зажигания.
Мифы и реальность
1. Двигатели делают в КНР, а потому качество не очень. Двигатели действительно изготавливают в Китае, но важнее то, что производство моторов налажено на заводе Hyundai Motor Co, а потому качество известного корейского производителя. Обратите внимание, что даже некоторые премиальные автомобили, например, модели Volvo, собирают в Китае, включая их флагман S90.
2. Блок цилиндров двигателя алюминиевый, одноразовый и неремонтопригодный. На самом деле конструкция блока цилиндров позволяет заменить гильзы на новые тонкостенные чугунные, так что методом перегильзовки двигатель можно отремонтировать несколько раз. Причем цена такого ремонта двигателя сопоставима со стоимостью восстановления с чугунным блоком, при условии, что поршни оставляют прежние (такая возможность в некоторых случаях есть).
3. Коленчатый вал имеет конструкцию всего с четырьмя противовесами, поскольку изгибается сильнее, чем, например, у вазовских «поперечных» движков. Практика ремонта таких двигателей большими пробегами показывает, что износ и шатун обычно минимален, и дело ограничивается установкой новых номинальных вкладышей.
4. Ресурс двигателя — 180 000 км, после чего мотор можно выкидывать. Практика показывает, что при хорошем уходе некоторые моторы проходят 400 000 и более километров. Только рекомендую менять почаще моторное масло — раз в 7500 — 10 000 км, заливать топливо на брендовых заправках и не допускать перегревов двигателя.
5. Облегченные и укороченные поршни быстро начинают болтаться в цилиндрах. Да, конечно, конструкция поршней не такая, как у «миллионников» восьмидесятых и девяностых годов прошлого века, но сравнительно недорогой ремонт с заменой поршней и колец, а также дефектовкой и ремонтом ГБЦ на пробеге в 200 000 км позволяет значительно продлить ресурс мотора.
6. Цепной привод ГРМ не особенно надежен. До пробега 150 000–200 000 км цепь обычно ходит без особых нареканий при хорошем масле и спокойном стиле езды. Многорядная зубчатая цепь служит очень неплохо и порой звездочки изнашиваются сильнее, чем цепь.
7. Отсутствие гидрокомпенсаторов массы проблем владельцу. Согласно регламенту технического обслуживания, регулирование клапанов следует проводить не реже, чем через 90 000 км пробега. Реальная потребность в регулировке обычно наступает несколько позже срока. Другое дело — двигатели, эксплуатируемые на газе. Здесь за зазорами действительно нужно следить за более тщательно.А вообще, экономия на гидрокомпенсаторах — действительно минус этого мотора. И, что самое обидное, у предка, двигателя G4EC Hyundai Accent первого поколения, были гидрокомпенсаторы.
8. Фазовращатели имеют ненадежную конструкцию. На самом деле нарекания на фазовращатели носят единый характер, да и то только при несвоевременной замене масла либо при его низком качестве.
9. Шумная работа мотора, особенно заметная на холостом ходу. Да, присутствует характерное «стрекотание» топливных форсунок, не особенно приятное уху, но это единственный громкий звук, издаваемый исправным мотором.
Материалы по теме.
10. Разрушение керамического блока каталитического нейтрализатора вывод из строя поршневую группу мотора. Керамический блок любого каталитического нейтрализатора в наших условиях эксплуатации действительно не особо долговечен. Если нейтрализатор размещен достаточно далеко от мотора, то опасность для последнего нет. Такую компоновку применяют некоторые автопроизводители (например, Renault), но не Hyundai. При выкрашивании кусочки керамики нейтрализатора действительно могут попадать в цилиндры и повреждать рабочие поверхности.Разрушению способствуют:
- Накопление несгоревшего топлива в керамическом блоке из-за перебоев в зажигании.
- Механическое повреждение участка системы выпуска и резкие термические удары при преодолении луж.
- Использование низкокачественного топлива и большого количества присадок к топливу.
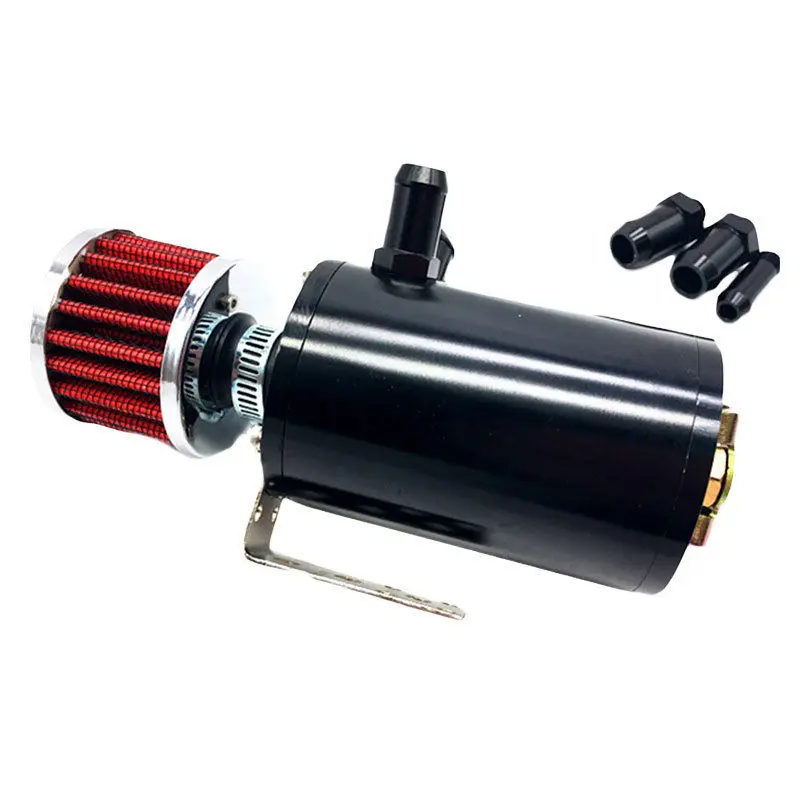
Каталитический нейтрализатор в катколлекторе Hyundai Solaris расположен слишком близко к головке блока цилиндров и при разрушении может повреждать мотор. Но так бывает не всегда. К примеру, у автомобилей Лада Веста и Гранта схожая конструкция катколлектора, но подобного явления не наблюдается.
Реальные недостатки двигателя Hyundai 1.6
Большинство из перечисленных недостатков не имеют под собой реальных оснований. Их вполне можно считать мифами. Реальных же просчетов в конструкции двигателя Hyundai не так много. Это необходимость регулировки клапанов из-за отсутствия гидрокомпенсаторов и неподходящее расположение каталитического нейтрализатора для российских условий эксплуатации.
Выводы
Двигатели рабочим объемом 1,6 л концерна Hyundai / Kia с распределенным впрыском топлива являются одними из самых беспроблемных на отечественном рынке. Более надежными можно считать только моторы, разработанные в прошлом веке. Например, К4М концерна Renault. Но характеристики моторов тех времен заметно скромнее.
- Профилактика, своевременное обслуживание и добавление эффективных присадок — вот залог долгого срока эксплуатации автомобиля!
ученых удвоят ресурс моторов из алюминия
Электронный обстрел
Использование алюминиевых сплавов в автомобильных двигателях — одно из передовых решений, позволяющее облегчить легковую машину на 50–100 кг, сделав ее более приемистой и экономичной.К тому же «крылатый металл» почти не подвержен коррозии, благодаря чему силовой агрегат получает от ржавчины. Широкому распространению двигателей из легких сплавов мешает их малая долговечность, поскольку они менее устойчивы к механическому износу по сравнению с чугунными аналогами.
Решить эту проблему автоконцерны с помощью дополнительных износостойких покрытий, которые наносят на поверхности деталей. В результате такой обработки на мягком алюминиевом сплаве создается более твердый либо металлокерамический защитный слой, толщина которого не превышает нескольких микрон.Однако технология всё же не позволяет довести долговечность алюминиевых двигателей до необходимого уровня, и сейчас они приблизительно в два раза уступают чугунным агрегатам по ресурсу.
Российские ученые предложили способ дальнейшего совершенствования моторов из легкого, разработали новый подход к обработке их деталей.
— В установке «Комплекс» мы применили ионно-плазменный и электронно-пучковый способы воздействия, которые позволяют создать в износостойкие слои глубиной до 30 микрон, — сообщил заведующий лабораторией пучково-плазменной инженерии поверхности институтта сильной электроники (ИСЭ) СО РАН Владимир Денисов.
Фото: Николай Коваль и Влдаимир Денисов с установкой «Комплекс». Источник: п ресс-служба ИСЭ СО РАН
Суть метода заключается в импульсном воздействии интенсивного пучка электронов на поверхности детали с напыленным покрытием.
— В результате оно перемешивается с использованием плазменной эмиссионной электроники ИСЭ СО РАН Николай Коваль.- Таким образом можно выполнить изменение элемента состава образца и его свойств. В частности, мы можем повысить надежность повышения твердости по мере продвижения к поверхности материала, увеличивает надежность деталей.
Слоеный корпус
По словам ученых, с помощью установки также можно добавить в металл сразу несколько модифицирующих материалов, что позволяет одновременно воздействовать на разные детали — например, провести ее упрочение вместе с высокой стойкостью к воздействию высоких температур.При этом все этапы обработки проходят в вакуумных камерах, что исключает доступ кислорода, который может испортить заготовку.
— Электронно-пучковый способ воздействия на алюминиевые сплавы известен с 1960-х годов, однако ученые из Томска сделали важный шаг в его развитии, создавая работающую промышленную установку, — отметил приглашенный эксперт НИТУ «МИСиС» Евгений Александров.
![]()
Также специалисты считают, что технология может работать в аэрокосмической отрасли.
— В своей работе ученые добились создания очень толстого 30-микронного упрочняющего слоя, который должен обладать не только высокой износостойкостью, но и хорошей согласовностью с пакетом данных, признанный лабораторией физической химии металлургических расплавов Института металлургии Уральского отделения РАН Алексей Шубин. — Это качество вкупе с универсальностью установки может проводить точечное упрочнение корпусных деталей самолетов и космических кораблей в тех местах, которые подвержены наибольшим эксплуатационным нагрузкам.
В настоящее время разработчики показывают возможность улучшения свойств поверхности для ряда сортов стали, титана и алюминиевых сплавов, включая силуминовых, которые используются в автомобилестроении. В частности, износостойкость последних у них получилось увеличить в 5–10 раз.
По словам специалистов, новая ионно-плазменная технология уже была внедрена на одном из российских предприятий по изготовлению штамповых инструментов.Его использование в процессе производства двигателей станет возможным после переговоров с автомобильными компаниями.
Испытания первого в мире полностью алюминиевого двигателя успешно завершились в Новосибирске
В конце января 2019 года на аэродроме Мочище под Новосибирском закончились испытания первого в мире алюминиевого двигателя внутреннего сгорания. Экспериментальный агрегат прошел многочасовые ресурсные испытания, подтвердившие высокие эксплуатационные характеристики сверхпрочного покрытия, покрытые алюминиевыми деталями двигателя.«Износ деталей не определяется микрометрическим измерительным инструментом, фактически его нет. Это нас вдохновляет », — рассказал руководитель команды разработчиков, профессор кафедры и вертолетостроения самолет НГТУ Илья Зверков .
Вместе с тем испытания не обошлись без внештатных действий. На одном из этапов испытания на одной из деталей появился скол инновационного покрытия, повредились уплотнения масляной системы и двигатель начал дымить, однако он не заглох, что подтвердило надежность агрегата.Анализ неполадки показал, что она случилась из-за производственного брака при обработке деталей и не имеет отношения к самой технологии. «Даже испытания нового двигателя с традиционными технологиями не обходятся без эксцессов, что уж говорить о революционном агрегате, в основном механизме которого нет ни одной стальной детали. Мы даже рады, что это случилось, ведь мы увидели, что двигатель не заглох, он продолжал работать и не потерял мощность. Это значит, что если бы мотор стоял на самолете, то он спокойно вернулся бы на аэродром », — говорит И.Зверков .
Полностью алюминиевый авиадвигатель был впервые представлен конструкторами опорного Новосибирского государственного технического университета в январе 2018 года. Использование алюминия вместо стали низкими вес двигателя на 30—40% по сравнению с традиционными ст двигателями аналогичной мощности. При этом расчетная мощность нового двигателя выросла на 40 лошадиных сил — до 400 лошадиных сил, а расход топлива лошади снизился примерно на 15%. Экспериментальный двигатель испытывался на обычном автомобильном бензине АИ-95.
Алюминий уже применяется в авиационных и автомобильных двигателях, но детали, работающие под высокой нагрузкой, до сих пор изготавливаются из стали. Ученым опорного университета Новосибирской области удалось заменить их на алюминиевые с помощью особой технологии плазменно-электролитического оксидирования (ПЭО), созданной в Институте неорганической химии СО РАН. Суть технологии в том, что на алюминиевые детали воздействуют плазменными разрядами, в результате чего на поверхности алюминиевых деталей образуется тонкий слой оксида алюминия, известный как корунд.Корунд обладает высокой твердостью и температурой плавления, поэтому алюминиевые детали с корундовой поверхности заменить стальные в двигателе. Детали нового двигателя были специально сконструированы для эффективного применения технологии ПЭО.
Параллельно с испытаниями работа по проектированию серийного образца двигателя. Они отказались от H-образной схемы, которая была применена на экспериментальном двигателе, и остановились на V-образной схеме. Это позволяет увеличить габариты мотора, что даст возможность установить его на разные модели самолетов, а не на ЯК-52, под который был сделан экспериментальный образец.Новый двигатель может быть также установлен на самолеты Як-18Т, Ил-103, Бе-103. Серийный двигатель будет эксплуатироваться на авиационном бензине Б-91, которого возобновлено в России. Проектируемый двигатель будет модульным, два силовых блока мощностью 200 лошадиных сил, используемые как вместе, так и отдельно для моторизации легких самолетов. Новый 200-сильный двигатель будет весить 98 кг, что минимум на 30% меньше, чем у стальных аналогов.
Сейчас идет изготовление деталей нового двигателя, который будет готов к началу лета 2019 года. Все основные детали нового двигателя будут отлиты из алюминия в Новосибирске. В этом еще одно преимущество новой схемы: она позволит отказаться от импортных комплектующих, которые использовались в экспериментальном агрегате. В перспективе это даст возможность использовать двигатель на самолетах ВВС России.
Двигатель разрабатывает созданную выпускниками НГТУ компания «ЗК-Мотор». Разработчик двигателя — профессор кафедры самолето- и вертолетостроения факультета летательных аппаратов НГТУ Илья Зверков , коллектив разработчиков составляют аспиранты и магистранты НГТУ.
Научно-технологическую поддержку разработки института теоретической и прикладной механики СО РАН. Финансируется разработка двигателя в основном за счет средств фонда «Возрождение отечественной авиации».
Фото: nstu.ru
Видео. Испытания алюминиевого двигателя ЗК 4000
Видео. Как заменялась сталь: в Новосибирске создали первый полностью алюминиевый двигатель — Россия 24
